Navigating the depths of the ocean, underwater welders possess a unique set of skills that allow them to perform complex tasks in an extraordinary environment. This high-risk profession comes with a set of dangers that require a deep understanding of safety measures and protocols. “Dangers of Underwater Welding” delves into the perilous realities of this occupation, shedding light on the potential hazards and risks faced by these skilled craftsmen beneath the waves.
From extreme water pressure to the threat of electric shock, this article uncovers the critical aspects that demand attention and precaution in underwater welding. Join us as we explore the intricacies of this challenging profession and gain insight into the crucial safety practices that can safeguard the lives of those who dare to work in this unconventional and hazardous setting.
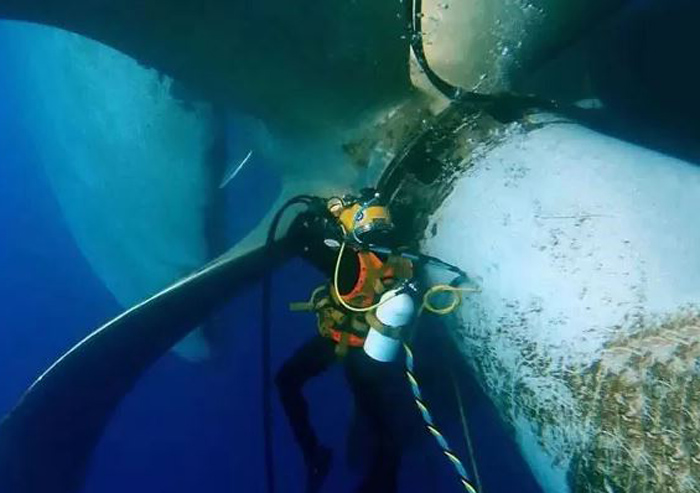
Photos: inboxq.com
Risks of Underwater Welding
Underwater welding presents a unique set of risks and dangers that are distinct from those encountered in traditional welding environments. One of the primary hazards is the extreme water pressure that can affect the human body and equipment. The diver-welders are exposed to immense pressure as they descend deeper into the ocean, which can lead to physical discomfort and, in severe cases, decompression sickness.
The presence of underwater creatures and unpredictable currents adds an element of unpredictability, making the working conditions even more hazardous. Despite the advancements in technology and safety protocols, the inherent dangers of working in an underwater environment cannot be overlooked.
The threat of electric shock is another critical risk associated with underwater welding. The combination of electricity, water, and metal structures creates a potentially lethal situation for welders. Without proper insulation and electrical safety measures, the risk of electric shock increases significantly. The limited visibility in underwater conditions adds an extra layer of complexity, making it challenging for welders to detect potential electrical hazards. Mitigating the risk of electric shock requires strict adherence to safety guidelines and continuous monitoring of equipment and environmental conditions.
The exposure to hazardous materials such as toxic gases and chemicals during underwater welding poses health risks to the divers. The confined spaces and lack of adequate ventilation can exacerbate the effects of these substances, potentially leading to respiratory issues and long-term health complications. It is imperative for underwater welders to be equipped with proper respiratory protection and undergo thorough training on the handling of hazardous materials to minimize the associated risks.
Underwater Welding Techniques and Safety Measures
In order to mitigate the risks and dangers inherent in underwater welding, specialized techniques and safety measures are employed to ensure the safety of the diver-welders and the integrity of the welding operations. One of the primary techniques used in underwater welding is known as hyperbaric welding, which involves welding in a chamber filled with a high-pressure gas mixture to simulate the underwater conditions. This method allows for controlled welding environments, reducing the exposure to external hazards and providing a safer alternative to traditional underwater welding.
Safety measures such as thorough equipment inspections, pre-dive checks, and continuous monitoring of environmental conditions play a crucial role in minimizing the risks associated with underwater welding. Diver-welders undergo comprehensive training to familiarize themselves with emergency procedures, safety protocols, and the use of specialized equipment designed for underwater operations. The implementation of strict operational guidelines and the presence of experienced dive supervisors further enhance the safety measures during underwater welding projects.
The utilization of advanced diving suits and equipment, including helmet-mounted cameras and communication systems, enables diver-welders to maintain better situational awareness and receive real-time assistance from support teams on the surface. These technological advancements not only contribute to the safety of the divers but also improve the overall efficiency and precision of underwater welding operations. By integrating cutting-edge technology with stringent safety practices, the risks associated with underwater welding can be effectively managed, ensuring the well-being of the divers and the successful completion of welding projects.
Underwater Welding Accidents and Case Studies
Despite the implementation of safety measures and advancements in technology, underwater welding accidents can still occur, highlighting the inherent dangers of working in this challenging environment. Case studies of underwater welding incidents provide valuable insights into the causes of accidents and the lessons learned to prevent similar occurrences in the future. Understanding the root causes of accidents is crucial for continuously improving safety protocols and minimizing the risks associated with underwater welding.
One notable case involved a diver-welder who experienced decompression sickness due to rapid ascent from the depths, emphasizing the importance of adhering to proper decompression procedures. Another incident highlighted the risk of equipment failure, leading to a loss of electrical insulation and subsequent electric shock to the diver-welder. These real-life scenarios underscore the critical need for stringent safety measures, thorough equipment maintenance, and continuous training to mitigate the potential dangers of underwater welding.
By analyzing past accidents and identifying the contributing factors, industry professionals and regulatory bodies can implement targeted improvements in safety standards, equipment design, and emergency response protocols. These proactive measures are essential for enhancing the overall safety culture within the underwater welding industry and safeguarding the well-being of diver-welders who brave the challenges of working in underwater environments.
Training and Certification for Underwater Welding
The specialized nature of underwater welding requires extensive training and certification to ensure the competency and safety of diver-welders. Comprehensive training programs encompass theoretical knowledge, practical skills, and hands-on experience in simulated underwater conditions. Diver-welders undergo rigorous training in diving techniques, welding procedures, equipment maintenance, emergency response, and safety protocols specific to underwater environments.
Obtaining certification from recognized organizations and regulatory bodies is essential for validating the proficiency and competence of underwater welders. Certification processes typically involve assessments of theoretical understanding, practical skills demonstration, and adherence to safety standards. These certifications serve as a testament to the diver-welders’ ability to perform underwater welding tasks safely and effectively, instilling confidence in employers and project stakeholders regarding their capabilities.
Continuous professional development and refresher training are integral components of maintaining certification for underwater welding. As technology and safety practices evolve, diver-welders are required to stay abreast of the latest industry standards and advancements through ongoing training and skills enhancement programs. By prioritizing training and certification, the underwater welding industry upholds a commitment to excellence and safety, setting a high bar for skill proficiency and adherence to best practices.
The Importance of Proper Equipment and Maintenance
The reliability and functionality of equipment used in underwater welding operations are paramount to the safety and success of the diver-welders. Regular maintenance, inspection, and testing of diving and welding equipment are essential to identify potential issues and prevent equipment failure during underwater operations. Any compromise in equipment integrity can significantly elevate the risks associated with underwater welding, emphasizing the critical role of thorough equipment maintenance.
Specialized tools and apparatus designed for underwater welding undergo stringent quality checks and must meet industry-specific standards to ensure optimal performance and safety. From welding electrodes to diving suits and breathing apparatus, every piece of equipment plays a vital role in safeguarding the diver-welders and facilitating efficient welding operations in challenging underwater conditions. The proper storage and handling of equipment, both onshore and offshore, are integral aspects of equipment management for underwater welding projects.
The proactive replacement of worn-out components, adherence to manufacturer recommendations, and adherence to scheduled maintenance routines contribute to the overall reliability of the equipment used in underwater welding. A comprehensive understanding of equipment functionality and the implementation of preventive maintenance measures are essential for mitigating potential risks and upholding the safety standards essential for underwater welding operations.
Regulations and Standards for Underwater Welding
The underwater welding industry is subject to stringent regulations and standards aimed at ensuring the safety of diver-welders, the protection of the environment, and the quality of welding work performed in underwater settings. Regulatory bodies and industry organizations establish and enforce guidelines related to diving operations, welding procedures, equipment specifications, and environmental impact assessments. Compliance with these regulations is fundamental to the responsible and ethical conduct of underwater welding projects.
Regulations governing underwater welding encompass a wide range of aspects, including diver qualifications, equipment certification, emergency response protocols, environmental protection measures, and project documentation requirements. Adherence to these regulations not only mitigates the risks associated with underwater welding but also fosters a culture of accountability and professionalism within the industry. Furthermore, regulatory oversight ensures that underwater welding projects adhere to ethical and legal standards, safeguarding the interests of all stakeholders involved.
Industry standards for underwater welding continually evolve to incorporate the latest technological advancements, safety best practices, and environmental considerations. The collaborative efforts of regulatory bodies, industry professionals, and research institutions contribute to the ongoing refinement of standards, reflecting a commitment to continuous improvement and the highest levels of safety and quality in underwater welding operations.
Advancements in Underwater Welding Technology
The field of underwater welding has witnessed remarkable advancements in technology, leading to innovative solutions that enhance the safety, efficiency, and precision of welding operations in underwater environments. From the development of specialized welding equipment to the integration of robotics and automation, technological progress has significantly transformed the landscape of underwater welding, opening new possibilities and raising the standards for safety and performance.
The introduction of remote-operated vehicles (ROVs) equipped with welding capabilities has revolutionized underwater welding by enabling precise and controlled operations without the direct physical presence of diver-welders. ROVs offer enhanced maneuverability, real-time monitoring, and the ability to access confined spaces, thereby reducing the exposure of human divers to hazardous conditions. Additionally, advancements in welding consumables, such as improved electrode formulations and shielding gases, have contributed to higher weld quality and increased productivity in underwater welding applications.
Underwater welding technology continues to evolve with the integration of advanced imaging systems, non-destructive testing methods, and underwater welding simulators that provide realistic training environments for diver-welders. These technological innovations not only elevate the safety standards for underwater welding but also expand the capabilities and versatility of underwater welding operations, paving the way for enhanced performance and reliability in challenging underwater environments.
Career Opportunities and Outlook for Underwater Welders
Despite the inherent risks and challenges, the field of underwater welding offers unique career opportunities for individuals with a passion for adventure, technical expertise, and a commitment to safety. Diver-welders play a crucial role in supporting various industries, including offshore construction, marine infrastructure maintenance, ship repair, and underwater salvage operations. The demand for skilled underwater welders remains strong, driven by ongoing developments in marine engineering, offshore energy exploration, and underwater construction projects.
The outlook for underwater welders is influenced by the growing global emphasis on sustainable development, renewable energy initiatives, and the maintenance of critical underwater structures and assets. As infrastructure projects expand into marine environments and offshore territories, the need for proficient diver-welders capable of executing complex welding tasks in challenging underwater conditions continues to rise. Furthermore, the integration of innovative technologies and the evolution of safety standards present promising avenues for career advancement and specialization within the field of underwater welding.
Career pathways for diver-welders encompass diverse roles, including welding inspectors, underwater construction supervisors, equipment technicians, and specialized welding consultants. With the right combination of training, experience, and dedication to safety, underwater welders can forge rewarding careers that offer both professional fulfillment and the opportunity to contribute to vital projects that impact the marine and offshore industries.
Conclusion and Key Takeaways
“Dangers of Underwater Welding” has shed light on the critical aspects of this high-risk profession, emphasizing the inherent dangers, safety measures, technological advancements, and career prospects associated with underwater welding. The risks of extreme water pressure, electric shock, and exposure to hazardous materials underscore the need for stringent safety protocols, advanced equipment, and continuous training for diver-welders.
By prioritizing safety, embracing technological innovations, and adhering to industry regulations, the underwater welding industry can mitigate risks and ensure the well-being of those who undertake the challenges of working in unconventional and hazardous underwater environments.
As the demand for underwater welding expertise continues to grow, aspiring diver-welders are encouraged to pursue comprehensive training, obtain recognized certifications, and stay informed about the latest advancements in underwater welding technology. Moreover, industry professionals and regulatory bodies must collaborate to enhance safety standards, promote ethical practices, and support the career development of underwater welders.
Through a concerted effort to prioritize safety, foster innovation, and create rewarding career pathways, the field of underwater welding can thrive while maintaining a steadfast commitment to the well-being and success of diver-welders around the world.
Final Thoughts
This comprehensive blog article provides a thorough exploration of the dangers associated with underwater welding, offering valuable insights into the risks, safety measures, technological advancements, and career opportunities within this extraordinary profession. By shedding light on the complexities and challenges of underwater welding, this article aims to raise awareness about the critical aspects that demand attention and precaution in this high-risk occupation. Through a dedicated focus on safety, innovation, and industry collaboration, the underwater welding community can navigate the dangers and pave the way for continued excellence in underwater welding operations.