Are you exploring the world of resistance welding aluminum? If so, you’ve come to the right place. In this article, we will delve into the ins and outs of resistance welding and how it applies specifically to aluminum materials. Resistance welding is a popular method for joining metals together. It involves applying pressure and passing an electric current through two pieces of metal, causing them to heat up and fuse together. Aluminum, with its unique properties and challenges, requires some special considerations when it comes to resistance welding.
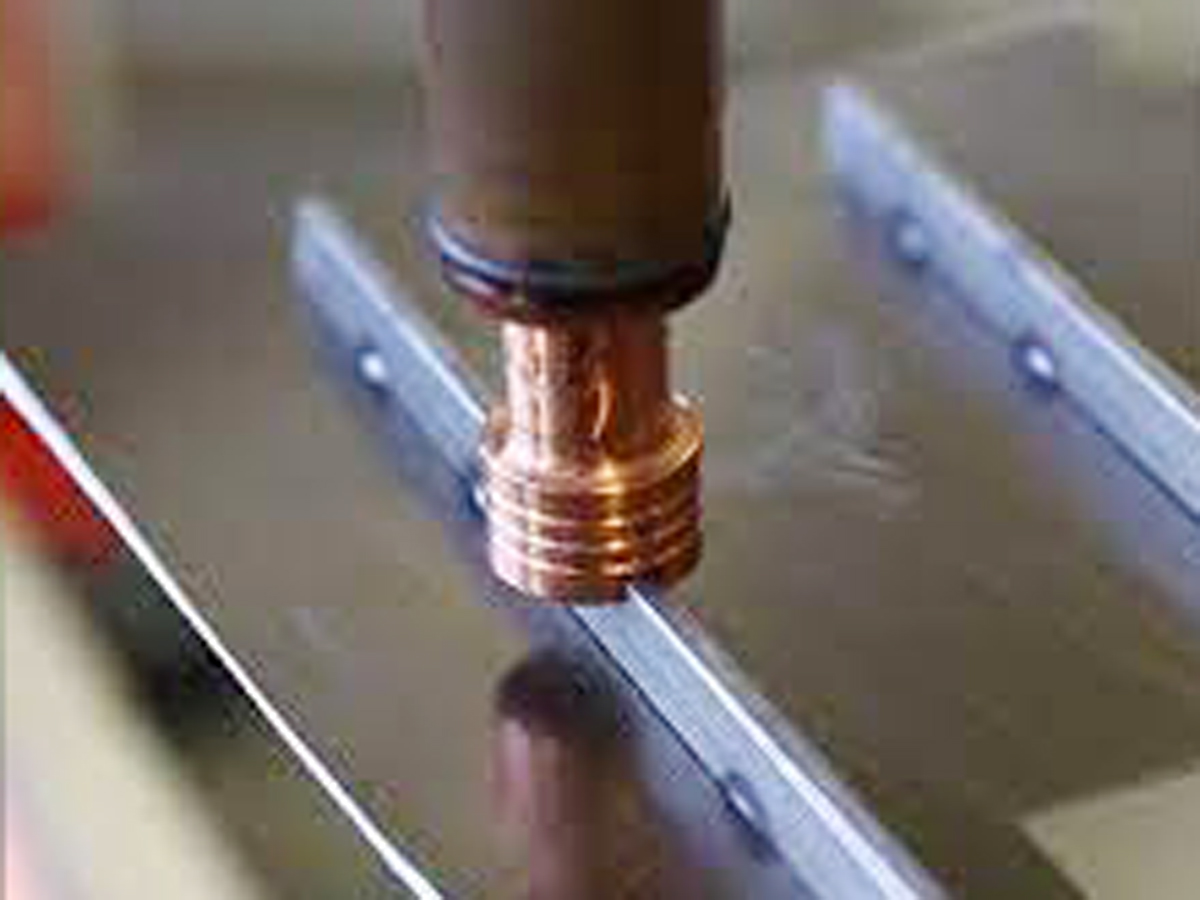
Photos by froniuswelding
Advantages of Resistance Welding Aluminum
Aluminum has gained popularity in various industries due to its lightweight, high strength-to-weight ratio, and excellent corrosion resistance. Resistance welding aluminum offers several advantages that make it a preferred choice in many applications. Firstly, resistance welding aluminum is a fast and efficient process. The heat generated by the electric current is concentrated in a small area, resulting in rapid heating and cooling times. This allows for high production rates and increased efficiency.
Secondly, resistance welding aluminum creates strong and durable joints. The process produces a solid metallurgical bond between the two aluminum pieces, ensuring the integrity and strength of the weld. This is crucial in applications where structural integrity is paramount. Additionally, resistance welding aluminum is a cost-effective solution. The equipment required for resistance welding is relatively inexpensive compared to other welding methods, making it an attractive option for manufacturers and fabricators.
Challenges of Resistance Welding Aluminum
While resistance welding aluminum offers numerous advantages, it also presents some challenges. Understanding these challenges is essential to ensure successful welds and quality results. One of the main challenges in resistance welding aluminum is its high thermal conductivity. Aluminum conducts heat at a much higher rate than other metals, making it more difficult to achieve the desired heat concentration for welding. This can result in inconsistent welds and insufficient fusion.
Another challenge is the formation of surface oxides on the aluminum during welding. These oxides act as insulators and can interfere with the welding process. Proper surface preparation, such as cleaning and removing oxides, is crucial to ensure good electrical contact and efficient heat transfer.
Additionally, aluminum is more prone to distortion and warping during the welding process. Its low melting point and high thermal expansion coefficient make it susceptible to heat-related deformations. Proper fixturing and control of heat input are essential to minimize distortion and maintain the desired shape of the welded components.
Types of Resistance Welding Methods for Aluminum
There are several resistance welding methods commonly used for joining aluminum materials. Each method has its advantages and considerations, depending on the specific application requirements.
- Spot Welding: Spot welding is the most common type of resistance welding used for aluminum. It involves applying pressure and passing an electric current through two overlapping aluminum sheets to create a weld at a localized spot. Spot welding is suitable for thin to medium thickness aluminum sheets and is widely used in automotive, aerospace, and electronics industries.
- Projection Welding: Projection welding is similar to spot welding, but with the addition of raised projections on one or both aluminum sheets. These projections concentrate the electric current and create localized heat, resulting in stronger and more consistent welds. Projection welding is commonly used for joining aluminum components with irregular shapes or varying thicknesses.
- Seam Welding: Seam welding is used for joining overlapping aluminum sheets along a continuous seam. It involves passing an electric current through two rotating copper wheels that press the aluminum sheets together, creating a continuous weld along the seam. Seam welding is ideal for applications that require leak-proof and hermetic seals, such as fuel tanks and pressure vessels.
Factors to Consider Before Resistance Welding Aluminum
Before embarking on the resistance welding process for aluminum, several factors need to be considered to ensure optimal results.
Aluminum Alloy Selection: Different aluminum alloys have varying properties, including electrical conductivity, thermal conductivity, and melting temperature. It is important to select the appropriate alloy that suits the application requirements and is compatible with the resistance welding process.
Electrode Material Selection: The choice of electrode material plays a crucial role in resistance welding aluminum. Copper alloys, such as Class 2 and Class 3 copper, are commonly used due to their high electrical and thermal conductivity. The electrode material should also have good wear resistance to withstand the high temperatures and forces involved in the welding process.
Welding Parameters: The welding parameters, including current, voltage, welding time, and electrode force, must be carefully controlled to achieve consistent and high-quality welds. Optimal welding parameters depend on factors such as the aluminum alloy, thickness, joint design, and desired weld strength.
Surface Preparation: Proper surface preparation is essential to ensure good electrical contact and efficient heat transfer during resistance welding. The aluminum surfaces should be clean, free from contaminants, and oxide-free. Mechanical cleaning methods, such as wire brushing or abrasive cleaning, are commonly used to remove oxides and ensure a clean welding surface.
Tips for Successful Resistance Welding Aluminum
To achieve successful resistance welding of aluminum, consider the following tips:
Optimize Welding Parameters: Experiment with different welding parameters to find the optimal settings for your specific application. Adjustments in current, voltage, welding time, and electrode force can significantly impact the quality and strength of the weld.
Use Proper Electrode Dressing: Regularly check and maintain the condition of the electrodes. Proper electrode dressing helps to ensure consistent electrical contact and heat transfer. Replace worn-out electrodes to maintain optimal welding performance.
Implement Proper Fixturing: Use suitable fixtures and clamping techniques to minimize distortion and maintain the desired alignment during the welding process. Proper fixturing ensures consistent joint quality and prevents misalignment issues.
Consider Preheating: Preheating the aluminum material before welding can help reduce thermal stresses and minimize distortion. However, preheating may not be necessary for all applications, so carefully evaluate the need based on the specific aluminum alloy and joint design.
Common Issues and Troubleshooting in Resistance Welding Aluminum
While resistance welding aluminum can yield high-quality welds, several common issues may arise during the process. Understanding these issues and their potential causes can help troubleshoot and rectify the problems.
Insufficient Fusion: Insufficient fusion occurs when the aluminum pieces do not fully melt and fuse together. This can be caused by inadequate heat input, low electrode force, or surface contamination. Increasing the welding current, increasing the electrode force, or improving surface cleaning can help achieve better fusion.
Burn-Through: Burn-through happens when excessive heat input causes the aluminum material to melt through or create holes. This can be caused by excessive welding current, prolonged welding time, or insufficient electrode force. Adjusting the welding parameters and ensuring proper electrode contact can prevent burn-through.
Electrode Sticking: Electrode sticking occurs when the electrode becomes welded to the aluminum surface, making it difficult to separate. This can be caused by inadequate electrode material selection, improper electrode dressing, or insufficient lubrication. Using appropriate electrode materials, regular electrode maintenance, and applying suitable lubricants can prevent electrode sticking.
Safety Precautions for Resistance Welding Aluminum
When resistance welding aluminum, it is crucial to prioritize safety to protect yourself and ensure a safe working environment. Here are some essential safety precautions to follow:
- Personal Protective Equipment (PPE): Wear appropriate PPE, including safety glasses, welding gloves, and flame-resistant clothing, to protect against potential hazards such as sparks, UV radiation, and heat.
- Ventilation: Ensure proper ventilation in the welding area to remove fumes and gases generated during the welding process. Use local exhaust ventilation or work in a well-ventilated space to minimize exposure to hazardous fumes.
- Machine Maintenance: Regularly inspect and maintain the resistance welding equipment to ensure its safe and optimal operation. Follow the manufacturer’s guidelines for maintenance tasks and schedule.
- Training and Certification: Ensure that operators and personnel involved in resistance welding aluminum receive proper training and certification. This includes understanding the equipment, safety procedures, and welding techniques.
Case Studies and Examples of Resistance Welding Aluminum Applications
Resistance welding aluminum finds applications in various industries, thanks to its numerous advantages and capabilities. Here are some case studies and examples that highlight the versatility of resistance welding aluminum:
Automotive Industry: Resistance welding aluminum is extensively used in the automotive industry for joining aluminum body panels, such as hoods, doors, and fenders. The lightweight properties of aluminum contribute to fuel efficiency while maintaining structural integrity and crash performance.
Aerospace Industry: The aerospace industry utilizes resistance welding aluminum for manufacturing aircraft components, such as fuel tanks, wing panels, and landing gear. The high strength and corrosion resistance of aluminum make it an ideal choice for aircraft construction.
Electronics Industry: Resistance welding is commonly employed in the electronics industry to join aluminum heat sinks, connectors, and circuit board components. The efficient and precise nature of resistance welding allows for the production of reliable and high-performing electronic devices.
The Future of Resistance Welding Aluminum
Resistance welding aluminum offers numerous advantages and presents some unique challenges. With proper understanding, preparation, and optimization of welding parameters, successful welds can be achieved, resulting in strong and durable joints. As technology continues to advance, the future of resistance welding aluminum looks promising. Innovations in electrode materials, welding equipment, and process control are constantly improving the efficiency and quality of resistance welding aluminum.
Whether you are a professional in the industry or simply curious about the world of resistance welding, this article has equipped you with the knowledge needed to navigate the complexities of resistance welding aluminum. Embrace the possibilities and explore the fascinating world of resistance welding aluminum.