Delve into the world of metal joining as we uncover the art and science of resistance spot welding. A favored method in the automotive, aerospace, and manufacturing industries, resistance spot welding is a process that fuses metals through the application of heat and pressure. Uniting precision with efficiency, this technique yields durable and high-strength welds, making it an indispensable asset across various sectors.
As metal fabrication continually seeks innovation, understanding the nuances of resistance welding becomes increasingly pertinent. Whether you are a seasoned professional or an enthusiast delving into the realm of welding, this comprehensive guide will equip you with insights into the principles, applications, and advancements within the realm of resistance spot welding.
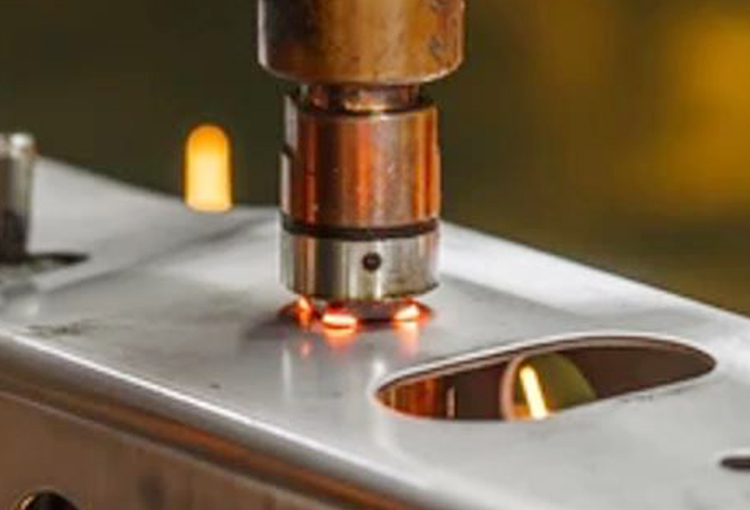
Image : Shutterstock
Stay tuned as we demystify the intricacies of this versatile welding technique, shedding light on its role in shaping the modern industrial landscape. Whether you seek to broaden your knowledge or enhance proficiency, embarking on this exploration will reveal the dynamic fusion of technology and craftsmanship in the world of resistance spot welding.
Understanding the Process of Resistance Spot Welding
Resistance spot welding, also known as resistance welding, is a process that involves the joining of metal sheets through the application of heat and pressure. This technique relies on the concept of electrical resistance to generate heat at the interface of the metal sheets, leading to their fusion. By concentrating the heat and pressure at specific points, resistance spot welding creates strong and durable bonds, making it an ideal choice for applications that require high structural integrity.
The process of resistance spot welding involves the use of specialized equipment, including welding electrodes and a power supply. The electrodes apply pressure to the metal sheets while passing a high electrical current through them, generating heat at the contact points. As the metal reaches its melting point, the electrodes exert pressure, causing the molten metal to fuse, ultimately forming a solid weld nugget. This seamless fusion results in welds with excellent mechanical properties, making resistance spot welding a preferred choice in industries that demand reliable and high-strength joints.
Resistance spot welding offers several advantages, such as high production rates, minimal need for filler materials, and the ability to weld various metals, including steel, aluminum, and stainless steel. However, it also presents some limitations, including restricted accessibility for complex joint geometries and the potential for electrode wear. Understanding these pros and cons is crucial for evaluating the suitability of resistance spot welding for specific applications.
Advantages and Disadvantages of Resistance Spot Welding
Resistance welding offers numerous advantages, making it a popular choice for joining metal components in various industries. One of its primary benefits is the high production rates it enables, making it an efficient method for mass production. Resistance spot welding eliminates the need for filler materials, reducing material costs and minimizing post-weld cleanup.
Another advantage of resistance spot welding is its versatility in welding different metals, including steel, aluminum, and stainless steel. This flexibility makes it a valuable technique for applications that involve dissimilar metal joining. Moreover, resistance spot welding produces welds with excellent mechanical properties, including high strength and structural integrity, making it suitable for critical structural components.
However, resistance welding also has its limitations. One of the challenges associated with this technique is the restricted accessibility for complex joint geometries. In cases where the welding electrodes cannot reach the desired welding points, alternative welding methods may be necessary. Additionally, resistance welding can lead to electrode wear over time, requiring regular maintenance and replacement.
Understanding the advantages and disadvantages of resistance welding is essential for making informed decisions regarding its applicability in specific manufacturing processes and product designs.
Applications of Resistance Spot Welding
Resistance spot welding finds widespread applications across various industries, ranging from automotive and aerospace to consumer electronics and appliance manufacturing. In the automotive sector, resistance spot welding is extensively used to assemble car bodies, joining metal panels and components with precision and durability. This process plays a crucial role in enhancing the structural integrity of vehicles, contributing to their safety and performance.
In the aerospace industry, resistance spot welding is employed for fabricating aircraft structures and components, where high-strength and reliable welds are essential for ensuring the safety and longevity of aircraft. The versatility of resistance spot welding also extends to the consumer electronics and appliance manufacturing sectors, where it is utilized for joining metal enclosures, frames, and components with efficiency and consistency.
Resistance welding is favored in the production of industrial equipment, machinery, and metal furniture, where the demand for sturdy and durable welds is paramount. The widespread adoption of resistance spot welding across diverse industries underscores its significance as a versatile and reliable metal joining technique.
How Resistance Welding Spot Works
The process of resistance welding involves several key steps that contribute to the successful fusion of metal sheets. It begins with the preparation of the metal surfaces to be welded, ensuring that they are clean and free from contaminants that could affect the quality of the weld. Once the surfaces are prepared, the metal sheets are positioned between the welding electrodes, which apply pressure to hold them in place during the welding process.
The next step involves the application of a high electrical current through the welding electrodes, creating resistance heating at the contact points of the metal sheets. As the metal reaches its melting point, the electrodes exert pressure, causing the molten metal to fuse, forming a solid weld nugget. The duration of the current flow and pressure application is carefully controlled to achieve the desired weld quality, ensuring that the resulting joint exhibits the required strength and integrity.
The success of resistance welding hinges on precise control of the welding parameters, including current magnitude, welding time, and electrode force. These parameters are tailored to the specific material properties and thickness of the metal sheets being welded, as well as the design of the joint. By optimizing these parameters, manufacturers can achieve consistent and reliable welds, meeting the stringent quality standards demanded by various industries.
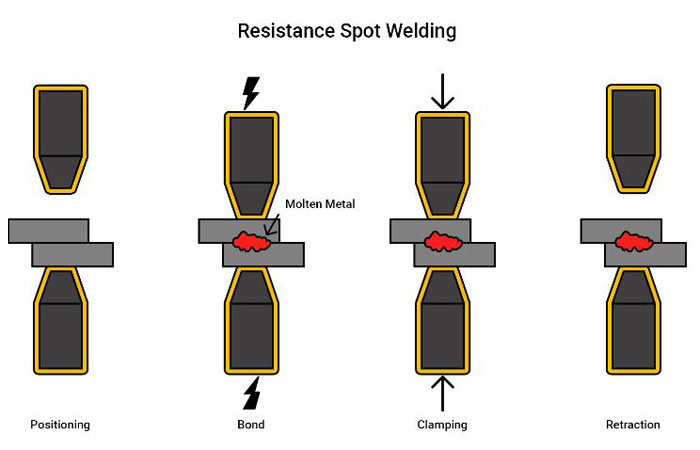
Image by punchlistzero.com
Factors Affecting Welding Quality
The quality of resistance welding is influenced by several factors that must be carefully managed to ensure the integrity and performance of the welded joints. One of the critical factors is the material properties of the metals being welded, including their conductivity, thickness, and surface condition. Metals with different conductivities and thicknesses require adjustments to the welding parameters to achieve optimal heat generation and fusion.
The design of the weld joint and the electrode configuration play a significant role in determining the quality of welding. Proper electrode alignment, size, and shape are essential for ensuring uniform pressure distribution and heat transfer during the welding process. Additionally, the cleanliness of the metal surfaces and the electrode condition are crucial factors that can impact the weld quality, as contaminants and electrode wear can compromise the integrity of the weld.
Furthermore, environmental factors, such as ambient temperature and humidity, can affect the performance of resistance spot welding equipment and the properties of the welded joints. It is essential to consider these variables and implement suitable measures to mitigate their influence on the welding process, ensuring consistent and reliable weld quality.
Equipment and Materials Used in Resistance Spot Welding
Resistance spot welding requires specialized equipment and materials to facilitate the precise and efficient joining of metal components. The primary components of a resistance spot welding system include welding electrodes, a power supply, and a control unit. The welding electrodes, typically made of copper alloys, apply pressure to the metal sheets and conduct the electrical current necessary for generating heat at the welding points.
The power supply delivers the high electrical current required for resistance welding, with the ability to control the magnitude and duration of the current flow. This control is essential for achieving the optimal heat input and fusion of the metal sheets, ensuring the formation of strong and durable welds. The control unit enables operators to set and monitor the welding parameters, including current, time, and pressure, allowing for precise adjustments to accommodate variations in material thickness and joint design.
In addition to the primary components, resistance welding also involves the use of consumables, such as electrode caps and tip dressers, which contribute to maintaining the condition and performance of the welding electrodes. These consumables are integral to the longevity and effectiveness of the welding system, as they help mitigate electrode wear and ensure consistent weld quality over extended periods of operation.
The selection of welding materials, including the metal sheets and any required filler materials, is a critical consideration in resistance spot welding. The compatibility of the materials, their conductivity, and mechanical properties must align with the welding parameters and requirements to achieve the desired weld quality and performance.
Safety Precautions in Resistance Spot Welding
As with any welding process, resistance spot welding necessitates adherence to strict safety protocols to mitigate potential hazards and ensure the well-being of operators and personnel in the vicinity. One of the primary safety considerations in resistance welding is the risk of electrical hazards, given the high current levels involved in the process. Operators must be adequately trained in electrical safety practices and equipped with appropriate personal protective equipment, including insulated gloves and footwear, to minimize the risk of electrical shock.
Additionally, the generation of heat during resistance welding poses a risk of thermal hazards, particularly in the form of radiant heat and sparks. Operators should wear protective clothing, such as flame-resistant jackets and goggles, to shield themselves from heat and potential splattering of molten metal. Adequate ventilation and fire safety measures should also be in place to prevent the accumulation of fumes and the occurrence of fire hazards.
The handling and maintenance of resistance spot welding equipment require careful attention to prevent injuries and accidents. Operators should be trained in safe operating procedures, including the proper handling of welding electrodes, the adjustment of welding parameters, and the inspection and replacement of consumables. Regular equipment inspections and maintenance, coupled with comprehensive training programs, are essential for promoting a safe working environment and preventing potential mishaps.
Common Challenges in Resistance Spot Welding
Resistance spot welding presents several challenges that can impact the quality and efficiency of the welding process. One common challenge is the occurrence of weld defects, such as insufficient fusion, excessive spatter, or electrode sticking. These defects can compromise the integrity of the welded joints, necessitating corrective actions, including adjustments to the welding parameters, electrode maintenance, or rework of the affected welds.
Moreover, the accessibility of welding points in complex joint geometries can pose challenges, particularly in applications involving intricate or irregularly shaped components. In such cases, specialized welding fixtures or alternative welding methods may be required to ensure proper fusion and structural integrity. Additionally, the presence of surface contaminants, such as oil, rust, or coatings, can impede the welding process, leading to inferior weld quality and the need for thorough surface preparation.
Another challenge in resistance welding is the management of electrode wear, which can affect the consistency and longevity of the welding process. Regular monitoring of electrode condition and timely replacement of worn components are essential for maintaining optimal weld quality and equipment performance. Addressing these challenges through proactive measures and continuous improvement initiatives is vital for ensuring the reliability and effectiveness of resistance spot welding in diverse applications.
Training and Certification
Proficiency in resistance welding is contingent upon comprehensive training and certification programs that equip operators with the knowledge and skills necessary to execute the welding process effectively and safely. Training in resistance spot welding encompasses theoretical and practical instruction on welding principles, equipment operation, welding parameters, and quality control measures.
Additionally, training programs focus on safety protocols, including hazard awareness, personal protective equipment usage, and emergency response procedures, ensuring that operators are well-prepared to navigate the potential risks associated with resistance spot welding. Certification programs validate the competency of individuals in performing resistance spot welding, verifying their ability to adhere to industry standards and best practices.
Certified resistance spot welding professionals demonstrate proficiency in executing the welding process, identifying and addressing weld defects, and maintaining the integrity of welding equipment. They play a pivotal role in upholding the quality and reliability of resistance spot welding across various industries, contributing to the production of structurally sound and durable welded components.
Continuous education and skill development are essential for individuals engaged in resistance spot welding, enabling them to stay abreast of technological advancements, industry trends, and evolving best practices. By pursuing ongoing training and certification opportunities, welding professionals can enhance their expertise and contribute to the continued advancement of resistance spot welding as a cornerstone of modern metal fabrication.
Conclusion
Resistance spot welding stands as a cornerstone of modern metal joining, offering a potent combination of precision, efficiency, and durability. Its widespread applications across automotive, aerospace, manufacturing, and other industries underscore its significance as a versatile and reliable welding technique. By understanding the principles, advantages, challenges, and safety considerations associated with resistance welding, professionals and enthusiasts alike can embrace its potential as a transformative force in the realm of metal fabrication.
As the industrial landscape continues to evolve, resistance spot welding remains a steadfast ally, shaping the production of high-quality, structurally resilient components. By delving into the intricacies of resistance welding and embracing ongoing training and certification, welding professionals can harness the full potential of this dynamic welding technique, contributing to the creation of robust and enduring products that drive innovation and progress across diverse sectors.