Plug welding aluminum involves joining two metal pieces by creating a hole in one piece and welding through it. This technique is essential in various industries for its strength and precision.
Aluminum plug welding is a common method used in industries such as automotive, aerospace, and construction. This process ensures strong, durable joints and is particularly useful where high strength and reliability are required. Aluminum’s lightweight and corrosion-resistant properties make it an ideal material for plug welding.
Mastering this technique requires understanding aluminum’s unique characteristics, such as its high thermal conductivity and oxide layer. Proper preparation, including thorough cleaning and precise drilling, is crucial. Using the correct welding equipment and techniques ensures optimal results. Overall, plug welding aluminum is a valuable skill for creating robust metal structures.
Introduction To Plug Welding Aluminum
Plug welding aluminum is a unique technique. It involves joining two pieces of aluminum. This method ensures strong and durable connections. Aluminum is lightweight yet sturdy. It is widely used in various industries. Understanding plug welding can help you create solid joints.
Importance Of Strong Joints
Strong joints are essential in any construction. They ensure the structure’s stability and longevity. Weak joints can lead to failures. This can cause safety hazards. Plug welding aluminum guarantees robust joints. This technique is reliable and efficient.
Advantages of Strong Joints |
---|
Increased Durability |
Enhanced Safety |
Better Load Distribution |
Applications In Various Industries
Many industries use plug welding aluminum. Here are some key areas:
- Automotive Industry: Used in car frames and panels.
- Aerospace Industry: Critical for aircraft components.
- Construction Industry: Utilized in building frameworks.
- Marine Industry: Essential for shipbuilding and repairs.
Each industry benefits from strong aluminum joints. These ensure safety and reliability. Plug welding aluminum is a valuable skill. It is crucial for creating durable structures.
Tools And Equipment
Plug welding aluminum requires the right tools and equipment. Using the correct gear ensures a strong weld. Let’s explore the essential tools and safety gear needed.
Essential Welding Tools
- MIG Welder: A MIG welder is ideal for aluminum welding. It provides a strong and clean weld.
- TIG Welder: A TIG welder offers precision. It is perfect for detailed aluminum work.
- Welding Torch: A welding torch helps control the heat. This is crucial for aluminum welding.
- Aluminum Welding Wire: Use aluminum-specific wire. It ensures compatibility and strength.
- Wire Brush: A wire brush cleans the aluminum surface. Clean surfaces create better welds.
- Clamps: Clamps hold the metal pieces. They keep the pieces steady during welding.
Safety Gear And Precautions
Safety Gear | Importance |
---|---|
Welding Helmet | Protects eyes and face from sparks and UV rays. |
Welding Gloves | Protects hands from heat and sparks. |
Fire-Resistant Jacket | Prevents burns from hot metal and sparks. |
Safety Glasses | Shields eyes from flying debris. |
Ear Protection | Guards against loud noises and flying debris. |
Always follow these precautions:
- Work in a well-ventilated area. This reduces exposure to fumes.
- Keep a fire extinguisher nearby. Welding can cause fires.
- Inspect all equipment before use. Ensure everything is in good condition.
Material Preparation
Proper material preparation is crucial in plug welding aluminum. Ensuring the materials are clean and securely clamped helps achieve high-quality welds. Let’s dive into the steps you need for effective material preparation.
Cleaning And Degreasing
Clean and degrease the aluminum before welding. Use a wire brush or dedicated aluminum cleaner. Remove all dirt, oil, and oxidation. A clean surface ensures better weld penetration and strength.
- Use a stainless steel brush for cleaning.
- Wipe with acetone to remove grease.
- Ensure the surface is dry before welding.
Proper Clamping Techniques
Proper clamping holds the materials steady during welding. A secure fit prevents movement and ensures accurate welds.
- Use clamps to hold the aluminum pieces in place.
- Ensure there are no gaps between the pieces.
- Check the alignment before starting the weld.
With the right clamping techniques, you can achieve precise and strong welds.
Step | Action | Purpose |
---|---|---|
1 | Clean surface | Remove contaminants |
2 | Degrease with acetone | Remove oils and grease |
3 | Clamp pieces securely | Prevent movement during welding |

Credit: www.researchgate.net
Choosing The Right Filler Material
Plug welding aluminum requires the perfect filler material. The filler material ensures strong and durable welds. Choosing the right filler material is key to achieving high-quality results. Below, we explore various types of filler metals and how to match them to the base metal.
Types Of Filler Metals
Various filler metals are available for aluminum welding. Here is a list of common types:
- 4043: Suitable for general-purpose welding. It offers good weldability and corrosion resistance.
- 5356: Ideal for higher strength and better ductility. It is commonly used in marine applications.
- 4047: Contains more silicon, providing better fluidity and less shrinkage.
Filler Metal | Characteristics | Common Uses |
---|---|---|
4043 | Good weldability, corrosion resistance | General-purpose welding |
5356 | Higher strength, better ductility | Marine applications |
4047 | Better fluidity, less shrinkage | Specific applications needing higher silicon |
Matching Filler To Base Metal
The base metal type affects the choice of filler metal. The following guidelines help in selecting the right filler:
- For 3003 aluminum, use 4043 filler for optimal results.
- For 6061 aluminum, either 4043 or 5356 can be used.
- For 5xxx series aluminum, 5356 filler metal works best.
Correctly matching the filler to the base metal ensures stronger, more reliable welds. This approach avoids issues such as cracking or poor adhesion. Always refer to manufacturer recommendations for precise matches.
Welding Techniques
Plug welding aluminum requires specific techniques to ensure strong bonds. Mastering these techniques can help you achieve successful welds. Below are some key methods and procedures to follow.
Heat Control Methods
Aluminum has high thermal conductivity, making heat control crucial. Proper heat management prevents warping and ensures a strong weld.
Method | Description |
---|---|
Preheating | Preheat the aluminum to reduce thermal shock. |
Pulse Welding | Use pulse welding to control heat input. |
Water Cooling | Employ water cooling to manage heat. |
Proper Plug Welding Procedures
Follow these steps for effective plug welding aluminum:
- Clean the surfaces to remove any oxides or contaminants.
- Drill holes for the plug welds at the designated spots.
- Align the pieces to ensure proper fit.
- Preheat the aluminum if necessary.
- Begin welding using a consistent, controlled technique.
- Allow the weld to cool naturally to avoid cracking.
Keeping these techniques and procedures in mind will help you achieve strong, reliable aluminum welds.
Avoiding Common Mistakes
Plug welding aluminum can be tricky. Avoiding common mistakes ensures strong and clean welds. Let’s discuss how to prevent frequent issues.
Preventing Cracks And Porosity
Cracks and porosity are common problems in aluminum welding. Cracks weaken the weld and can lead to failure. Porosity causes tiny holes in the weld, making it less robust.
- Use a clean work area. Dirt and oil cause porosity.
- Ensure proper preheat temperature. Cold aluminum cracks easily.
- Use correct filler material. Mismatched materials cause cracks.
- Maintain steady welding speed. Inconsistent speed leads to porosity.
Follow these steps to minimize these issues:
- Clean the aluminum surface thoroughly.
- Preheat the material to the recommended temperature.
- Select the appropriate filler rod.
- Maintain a consistent speed while welding.
Managing Heat Distortion
Managing heat distortion is crucial in plug welding aluminum. Excessive heat causes the material to warp, affecting the weld quality.
Tip | Action |
---|---|
Use Heat Sinks | Place heat sinks near the weld area to absorb excess heat. |
Control Heat Input | Adjust welding parameters to manage the heat input. |
Weld in Short Bursts | Short bursts reduce the amount of heat applied at one time. |
By following these tips, you can minimize heat distortion:
- Apply heat sinks to absorb excess heat.
- Adjust settings to control heat input.
- Weld in short, controlled bursts.
These strategies help in maintaining weld integrity and quality.
Post-welding Processes
After the plug welding process on aluminum, several crucial steps follow to ensure the weld’s integrity and quality. These steps ensure the final product meets the desired standards. Below are the key post-welding processes to consider.
Inspection And Testing
Inspection and testing are vital post-welding processes. They help identify any defects or irregularities. Here are some common methods used:
- Visual Inspection: This is the first step. Inspect the weld for visible defects such as cracks, porosity, or incomplete fusion.
- Ultrasonic Testing: This method uses sound waves to detect internal flaws. It is non-destructive and provides detailed information about the weld.
- Radiographic Testing: Also known as X-ray inspection. It reveals internal and surface defects by capturing images of the weld.
- Destructive Testing: Involves physically breaking the weld to evaluate its strength and quality. It includes tensile, bend, and fatigue tests.
Inspection Method | Purpose |
---|---|
Visual Inspection | Detects visible defects |
Ultrasonic Testing | Identifies internal flaws |
Radiographic Testing | Reveals both internal and surface defects |
Destructive Testing | Evaluates weld strength |
Finishing And Polishing
Finishing and polishing enhance the weld’s appearance and functionality. Proper finishing ensures the weld is smooth and free of imperfections. Key steps include:
- Grinding: Removes excess weld material. It smoothens rough edges.
- Filing: Further refines the weld surface. It ensures a smooth transition between the welded and base material.
- Buffing: Polishes the weld to a high sheen. It enhances the overall appearance.
In some cases, additional treatments may be required:
- Anodizing: Adds a protective oxide layer. It improves corrosion resistance.
- Painting: Provides an aesthetic finish. It also offers additional protection.
These processes ensure the weld is not only strong but also visually appealing.
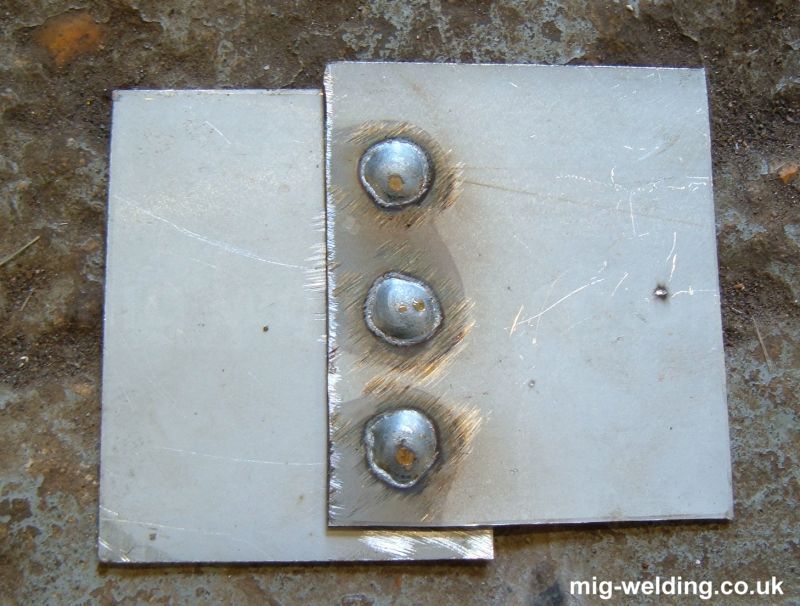
Credit: www.mig-welding.co.uk
Tips From Experts
Plug welding aluminum can be challenging. Experts share their best tips to make your welds strong and clean. Follow these guidelines to improve your welding skills and achieve professional results.
Proven Practices
Experts recommend several proven practices for effective plug welding aluminum:
- Clean the Surface: Remove any dirt, grease, or oxidation.
- Use Proper Filler: Select the correct filler material for the job.
- Control Heat: Aluminum conducts heat quickly. Adjust your settings.
- Practice Patience: Take your time. Rushing can cause mistakes.
Advanced Techniques
For those looking to master plug welding aluminum, consider these advanced techniques:
- Pulsed Welding: Use pulsed welding to control heat input and avoid burn-through.
- Back Purging: Employ back purging to protect the weld from contamination.
- Preheating: Preheat thick sections to ensure proper fusion.
- Use of Helium: Add helium to the shielding gas to increase heat input and improve weld penetration.
Following these expert tips can significantly enhance your plug welding results. Practice these techniques to achieve clean, strong welds every time.

Credit: www.sciencedirect.com
Frequently Asked Questions
What Is Plug Welding Aluminum?
Plug welding aluminum is a technique used to join two aluminum pieces. It involves creating a hole in one piece and welding through it to another piece.
Can You Plug Weld Aluminum?
Yes, you can plug weld aluminum. This method is effective for creating strong, durable joints in aluminum structures.
What Tools Are Needed For Plug Welding Aluminum?
To plug weld aluminum, you’ll need a welder, aluminum filler rod, and appropriate safety gear. A hole punch or drill is also necessary.
How To Prepare Aluminum For Plug Welding?
Clean the aluminum surfaces to remove any contaminants. Drill or punch a hole in the top piece. Ensure everything aligns correctly.
Conclusion
Mastering plug welding aluminum requires practice and attention to detail. Follow the steps outlined for successful outcomes. Ensure proper preparation, use the right tools, and maintain safety measures. With dedication, you can achieve strong, durable welds. Keep experimenting and refining your skills for the best results in your welding projects.