When it comes to joining metal pieces in manufacturing and automotive industries, the debate between plug welds and spot welds is one of precision and strength. Both methods have their merits, but understanding the nuances can make a significant difference in the structural integrity and longevity of the finished product.
In the automotive world, the battle between plug weld vs spot weld has been ongoing, with advocates on both sides touting the merits of their preferred method. So which is truly superior? And in which scenarios should each technique be used?
In this comprehensive guide, we’ll delve into the nitty-gritty details of both plug welds and spot welds. We’ll explore their differences, applications, and comparative advantages, providing you with the knowledge to make an informed decision for your specific needs. Whether you are a seasoned professional or a newcomer to metalworking, understanding the nuances of plug weld vs spot weld is fundamental to achieving optimal results and durability in your projects.
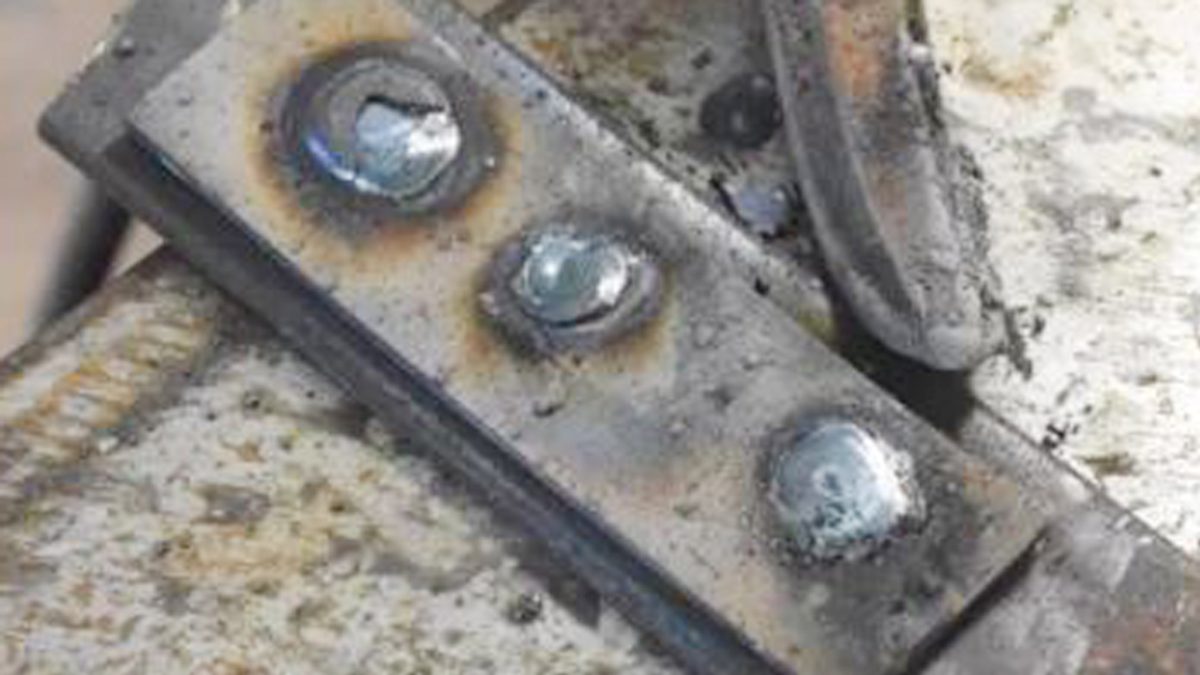
Image by iamwelder
Understanding the Plug Welding and Spot Welding
Plug welding and spot welding are two distinct methods used to join metal pieces together. While both techniques involve the fusion of metals, they differ in their application and execution.
Plug Welding
Plug welding, also known as hole welding, involves joining two metal pieces by filling a hole in the top piece with weld material, which then fuses with the bottom piece. This method creates a strong, durable bond and is commonly used in automotive and manufacturing applications.
Spot Welding
Spot welding, on the other hand, involves applying pressure and heat to a specific spot on the metal pieces, causing them to fuse together without the need for additional materials. This method is widely used in the automotive industry for joining thin metal sheets.
Both plug welding vs spot welding have their unique advantages and disadvantages, and understanding these nuances is crucial for making informed decisions in metalworking projects.
Differences Between Plug Weld vs Spot Weld
Technique and Equipment
One of the primary differences between plug weld vs spot weld lies in the technique and equipment used. Plug welding requires drilling a hole in the top metal piece, while spot welding involves the use of specialized equipment to apply pressure and heat to a specific spot.
Material and Strength
In terms of material usage and strength, plug welding often requires additional weld material to fill the hole, resulting in a potentially stronger bond compared to spot welding, which relies solely on the fusion of the metal pieces.
Versatility and Application
While spot welding is well-suited for joining thin metal sheets, plug welding offers greater versatility in joining metal pieces of varying thicknesses, making it a preferred choice for a wider range of applications.
Understanding the differences between plug welding vs spot welding sets the stage for evaluating their respective advantages and disadvantages in specific metalworking scenarios.
Advantages and Disadvantages of Plug Welding
Advantages of Plug Welding
- Superior strength and durability due to the additional weld material.
- Versatility in joining metal pieces of varying thicknesses.
- Reduced risk of burn-through in thicker metal pieces compared to spot welding.
Disadvantages of Plug Welding
- Requires additional drilling for the hole, adding an extra step to the welding process.
- Potential for weld spatter and slag formation during the welding process.
- Higher skill level and precision needed to ensure proper filling and fusion of the hole.
While plug welding offers notable advantages in terms of strength and versatility, it also comes with its own set of challenges that need to be carefully considered in metalworking projects.
Advantages and Disadvantages of Spot Welding
Advantages of Spot Welding
- Efficient and time-saving, especially for mass production in the automotive industry.
- Minimal material usage, as spot welding does not require additional weld material.
- Lower skill level required compared to plug welding, making it accessible for a wider range of workers.
Disadvantages of Spot Welding
- Limited to joining thin metal sheets effectively.
- Potential for reduced strength in the weld due to the absence of additional material.
- Risk of burn-through in thicker metal pieces, requiring careful adjustment of welding parameters.
Despite its efficiency and accessibility, spot welding’s limitations in terms of material thickness and strength must be carefully weighed against its advantages in specific metalworking applications.
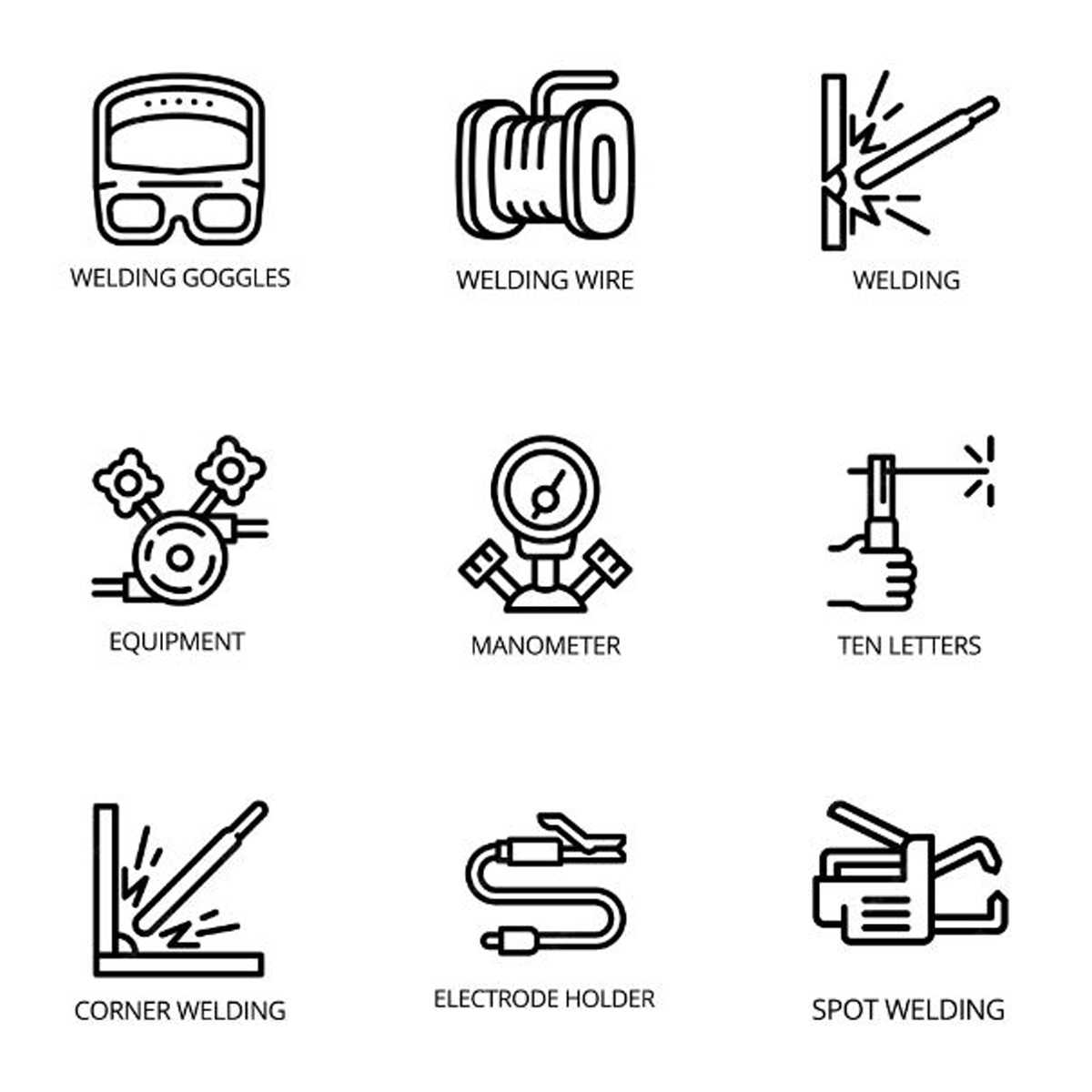
Applications of Plug Welding
Automotive Industry
In the automotive industry, plug welding finds extensive use in joining structural components, frame rails, and other critical areas where strength and durability are paramount. The ability to join metal pieces of varying thicknesses makes plug welding a versatile choice for diverse automotive welding needs.
Manufacturing and Fabrication
Beyond the automotive sector, plug welding is also widely employed in manufacturing and fabrication processes, particularly in the assembly of heavy machinery, metal structures, and structural components that require robust joint integrity.
Repair and Restoration
For repair and restoration projects involving metal components, plug welding serves as a reliable method for replacing damaged sections and reinforcing weakened areas, ensuring structural stability and longevity.
Understanding the specific applications of plug welding highlights its significance in various industries and underscores its role in ensuring the integrity of metal structures and components.
Applications of Spot Welding
Automotive Manufacturing
Spot welding is a cornerstone of automotive manufacturing, particularly for joining thin metal sheets in vehicle bodies, panels, and components. Its efficiency and speed make it an ideal choice for mass production lines.
Sheet Metal Fabrication
In sheet metal fabrication, spot welding is often utilized for creating seams, joints, and connections in various products, ranging from household appliances to industrial equipment, where precision and speed are crucial.
Electronics and Consumer Goods
The electronics and consumer goods industries also leverage spot welding for assembling metal components in devices, appliances, and products where seamless, reliable connections are essential for functionality and durability.
The widespread applications of spot welding across multiple industries underscore its significance in meeting the demand for efficient, reliable metal joining solutions.
How to Perform Plug Welding
Preparation and Setup
Before initiating the plug welding process, ensure that the metal pieces are clean, free of contaminants, and properly positioned for welding. Secure the pieces in place to maintain precise alignment during the welding process.
Drilling the Hole
Using the appropriate drill size, carefully create a hole in the top metal piece at the designated welding location. The size of the hole should be in accordance with the welding requirements and the thickness of the metal pieces.
Welding Process
With the hole prepared, initiate the welding process by filling the hole with weld material, ensuring complete and uniform coverage for a strong, reliable bond. Pay close attention to welding parameters and techniques to achieve optimal results.
Understanding the step-by-step process of plug welding is crucial for executing this technique with precision and ensuring the integrity of the welded joint.
How to Perform Spot Welding
Preparation and Alignment
Prior to spot welding, carefully align the metal pieces to ensure proper contact at the welding spot. Clean the surfaces to be welded to remove any contaminants that may interfere with the welding process.
Spot Welding Equipment
Utilize specialized spot welding equipment, such as spot welders or resistance welders, to apply the necessary pressure and heat to the welding spot. Adjust the welding parameters based on the metal thickness and material properties.
Welding Process
Initiate the spot welding process, ensuring consistent pressure and heat application to create a strong fusion between the metal pieces. Monitor the welding spot for proper formation and integrity of the weld. Mastering the intricacies of spot welding equipment and techniques is essential for achieving precise, reliable welds in various metalworking applications.
Factors to Consider When Choosing Between Plug Weld vs Spot Weld
Material Thickness and Type
Consider the thickness and type of the metal pieces to be welded, as this can influence the suitability of plug welding or spot welding for achieving the desired strength and joint integrity.
Structural Requirements
Evaluate the structural demands of the project, including load-bearing capabilities, impact resistance, and environmental factors, to determine which welding method aligns with the specific performance needs.
Production Volume and Efficiency
For mass production scenarios, weigh the efficiency and speed of spot welding against the potential strength advantages of plug welding, factoring in the overall production requirements and timelines.
Skill Level and Expertise
Assess the skill levels of the welding personnel and the availability of specialized equipment, as these factors can impact the feasibility and success of plug welding or spot welding in a given setting. By carefully considering these factors, you can make informed decisions when choosing between plug welding and spot welding, ensuring optimal results and durability in your metalworking projects.
Conclusion
In the realm of metalworking, the choice between plug weld vs spot weld hinges on a multitude of factors, including material thickness, strength requirements, production efficiency, and skill levels. While plug welding offers superior strength and versatility, spot welding excels in efficiency and accessibility for joining thin metal sheets.
Understanding the nuances of both methods, their applications, advantages, and disadvantages is essential for making informed decisions in metalworking projects. By leveraging this comprehensive guide, you can navigate the complexities of plug weld vs spot weld with confidence, ensuring the structural integrity and longevity of your welded joints in diverse industrial and automotive applications.