When it comes to plastic welding, mastering the tips and tricks can make all the difference in creating strong and seamless bonds. Whether you’re a DIY enthusiast or a professional welder, understanding the nuances of plastic welding is essential for achieving top-notch results. From choosing the right welding technique to troubleshooting common issues, this guide is your go-to resource for mastering the art of plastic welding.
Throughout this article, we will delve into expert insights and practical advice to elevate your plastic welding tips and skills. Whether you are tackling small repairs or large-scale projects, these tips will empower you to navigate the challenges of plastic welding with confidence. Prepare to unlock a treasure trove of insider tips and tricks that will revolutionize the way you approach plastic welding. Get ready to take your craftsmanship to new heights and achieve flawless welds every time.
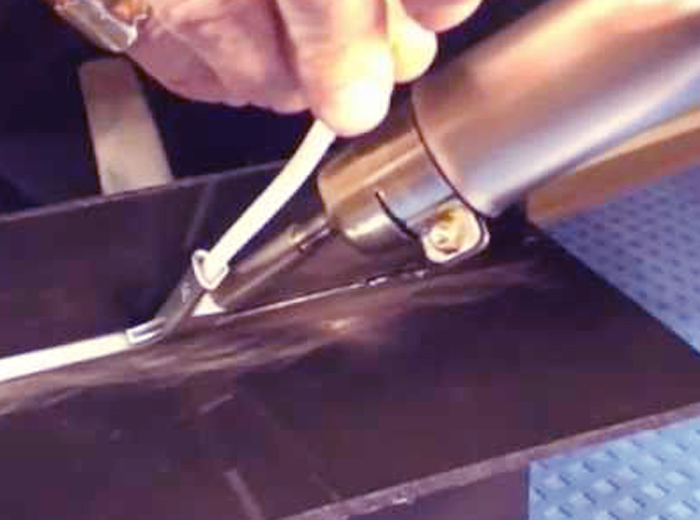
Photo by TECHSPANONLINE
About Plastic Welding
Plastic welding is a process that involves joining two pieces of plastic together using heat, pressure, or both. Unlike traditional welding, which is typically associated with metals, plastic welding requires specialized techniques due to the unique properties of plastic materials. The behavior of different types of plastics is crucial for achieving successful welds. Whether it’s polyethylene, polypropylene, PVC, or ABS, each type of plastic demands specific considerations when it comes to welding.
Plastic welding can be utilized in a wide range of applications, including automotive repairs, plumbing, fabrication of plastic tanks, and even artistic projects. The ability to create strong and durable bonds between plastic components makes plastic welding an indispensable skill for professionals and hobbyists alike. With the right knowledge and techniques, you can harness the potential of plastic welding to bring your creative visions to life.
Advantages of Plastic Welding
One of the key advantages of plastic welding is its ability to produce seamless and structurally sound joints. Unlike adhesives or mechanical fasteners, plastic welding creates a molecular bond between the joined surfaces, resulting in a bond that is often as strong as the original material. This superior bond strength makes plastic welding ideal for applications where durability and longevity are paramount.
Additionally, plastic welding offers the advantage of maintaining the integrity of the plastic material. When executed properly, plastic welding minimizes the risk of weakening the plastic or altering its properties, ensuring that the joined components retain their original strength and characteristics. This preservation of material integrity is crucial in applications where the performance and appearance of the plastic are critical.
Furthermore, plastic welding is a versatile process that can be used to join a wide variety of plastic materials, including thermoplastics and even certain types of thermoset plastics. This versatility makes plastic welding a valuable skill for professionals working across diverse industries, from manufacturing to construction and beyond.
Types of Plastic Welding Methods
Plastic welding encompasses several distinct techniques, each tailored to specific types of plastic materials and applications. The most common plastic welding techniques include hot gas welding, extrusion welding, high-frequency welding, and ultrasonic welding. Each technique has its unique advantages and considerations, making it essential for welders to familiarize themselves with the principles and best practices associated with each method.
Hot air welding, for instance, utilizes a stream of heated gas to soften the plastic surfaces, which are then fused together using pressure. This technique is particularly effective for welding thermoplastics such as PVC and polyethylene. Extrusion welding, on the other hand, involves melting a thermoplastic welding rod with a hot air gun and depositing the molten material into the joint to create a strong bond.
High-frequency welding, also known as radio frequency welding, relies on electromagnetic energy to generate heat within the plastic material, allowing for precise and rapid welding of thermoplastic components. Ultrasonic welding, meanwhile, uses high-frequency ultrasonic vibrations to create frictional heat at the joint interface, resulting in a quick and clean weld.
Essential Tools and Equipment for Plastic Welding
To execute successful plastic welds, it is essential to have the right tools and equipment at your disposal. The specific tools required for plastic welding vary depending on the chosen welding technique and the type of plastic being welded. However, some fundamental tools and equipment are universally essential for plastic welding applications.
A reliable heat source, such as a hot air gun or a welding torch, is a cornerstone of plastic welding. The heat source should be capable of delivering precise and controlled heat to soften the plastic material without causing degradation. In addition to the heat source, welding rods made from compatible plastic materials are essential for reinforcing the weld joint and ensuring a strong bond.
Clamping and fixturing tools play a crucial role in holding the plastic components in the correct position during the welding process. These tools help to maintain alignment and pressure, facilitating the formation of a uniform and secure weld. Safety equipment, including protective goggles, gloves, and respiratory protection, is also paramount to safeguard the welder from potential hazards associated with plastic welding.
Plastic Welding Safety Precautions
While plastic welding offers numerous benefits, it is essential to prioritize safety throughout the welding process. The heat generated during plastic welding can release fumes and vapors, which may pose health risks if inhaled. As such, proper ventilation and the use of personal protective equipment are imperative to mitigate the potential hazards associated with plastic welding.
Additionally, the heat source used for plastic welding can reach high temperatures, presenting the risk of burns and fire hazards. It is essential to operate the heat source with caution and adhere to recommended temperature settings to prevent overheating and material degradation. Ensuring that the work area is free from flammable materials and maintaining fire safety precautions is vital for a safe welding environment.
Proper handling and storage of plastic welding materials, such as welding rods and adhesives, are essential to prevent exposure to moisture and contaminants that could compromise the quality of the weld. By adhering to safety protocols and best practices, welders can create a secure and healthy working environment conducive to successful plastic welding.
Successful Plastic Welding Tips
To achieve successful plastic welds, it is essential to adhere to best practices and leverage expert tips that can enhance the quality and integrity of the weld joints. One crucial tip is to thoroughly prepare the surfaces to be welded by removing any contaminants, such as dirt, grease, or oxidation, which can impede the bonding process. Proper surface preparation sets the stage for a clean and robust weld.
Additionally, selecting the appropriate welding technique and matching it with the specific plastic material being welded is paramount for achieving optimal results. Different plastics require different welding methods and parameters, and understanding these nuances is key to producing high-quality welds. Maintaining consistent heat and pressure during the welding process is essential to ensure uniform melting and bonding of the plastic surfaces.
Furthermore, practicing proper weld bead formation and controlling the cooling process after welding are critical factors that contribute to the strength and aesthetics of the weld joint. By paying attention to these details and honing your technique, you can elevate the quality and precision of your plastic welds.
Common Mistakes to Avoid in Plastic Welding
Despite the benefits of plastic welding, there are common mistakes that can compromise the integrity of the weld and the overall success of the welding process. One prevalent mistake is neglecting to adjust the welding parameters to suit the specific type and thickness of the plastic material being welded. Inadequate heat, pressure, or welding speed can result in weak or incomplete welds.
Another common mistake is overlooking proper joint design and preparation. Inadequate joint geometry, such as insufficient overlap or improper joint angles, can weaken the weld and compromise its strength. Additionally, failing to maintain cleanliness and contamination control during the welding process can lead to inferior weld quality and reduced bond strength.
Furthermore, inadequate training and lack of familiarity with the nuances of plastic welding techniques can contribute to subpar welds. It is crucial for welders to undergo comprehensive training and stay abreast of the latest advancements in plastic welding technology and best practices to avoid common pitfalls and achieve superior results.
Applications of Plastic Welding in Different Industries
Plastic welding finds widespread application across various industries, where it serves as a versatile and reliable method for joining plastic components. In the automotive industry, plastic welding is utilized for repairing plastic body panels, bumpers, and interior components. The ability to seamlessly weld plastic parts enables automotive technicians to restore damaged components to their original condition with precision and durability.
In the field of construction, plastic welding is employed for fabricating and repairing plastic pipes, tanks, and other structural components. The watertight and durable bonds produced through plastic welding make it an indispensable technique for ensuring the integrity and longevity of plumbing and fluid containment systems.
The medical industry leverages plastic welding for manufacturing medical devices, disposable medical components, and specialized plastic enclosures. The ability to create sterile and robust welds is essential for meeting the stringent quality and safety standards of the healthcare sector.
The versatility of plastic welding extends to the realm of consumer products, where it is used for assembling plastic furniture, toys, and electronic enclosures. By harnessing the capabilities of plastic welding, manufacturers can produce high-quality products with seamless and reliable assembly.
Training and Courses for Plastic Welding
For individuals looking to enhance their plastic welding skills and expand their knowledge of plastic welding techniques, there are numerous training programs and courses available. These programs cover a wide range of topics, including plastic welding fundamentals, advanced welding techniques, material selection, and safety practices. Whether you’re a novice looking to enter the world of plastic welding or a seasoned professional seeking to refine your expertise, there are training options tailored to your specific needs.
Many training programs offer hands-on experience with various plastic welding equipment and techniques, allowing participants to gain practical skills and confidence in executing successful plastic welds. Additionally, these programs often provide insights into industry best practices, emerging technologies, and the latest developments in the field of plastic welding.
By investing in comprehensive training and education, individuals can position themselves as proficient and knowledgeable plastic welders, equipped to tackle diverse welding challenges and deliver exceptional results across different industries.
Conclusion and Final Thoughts
Mastering the art of plastic welding involves a blend of technical knowledge, practical skills, and a commitment to continuous learning. By understanding the nuances of plastic welding techniques, leveraging the right tools and equipment, and prioritizing safety and best practices, welders can achieve flawless and durable weld joints with confidence. The versatility of plastic welding extends across a spectrum of industries, offering solutions for automotive repairs, construction projects, medical device manufacturing, and consumer product assembly. With the right training and expertise, individuals can unlock the potential of plastic welding and contribute to the creation of robust and reliable plastic components.
As you embark on your plastic welding journey, remember that each successful weld is a testament to your craftsmanship and dedication to excellence. By implementing the tips and tricks outlined in this guide, you can elevate your plastic welding skills and overcome the challenges of plastic welding with finesse and precision. As you apply these insights and techniques in your welding endeavors, you’ll witness firsthand the transformative impact of mastering the art of plastic welding. Embrace the opportunities that plastic welding presents, and let your passion for precision and quality guide you toward achieving exceptional welds that stand the test of time.