Plastic welding polyethylene involves using heat to fuse two pieces of polyethylene together. This technique ensures a strong, durable bond.
Polyethylene is a widely used thermoplastic found in various applications, from packaging to industrial components. Plastic welding is crucial for repairing or fabricating polyethylene items. The process involves heating the material until it becomes pliable, then pressing the pieces together until they cool and solidify.
Proper technique and equipment are essential for a successful weld, ensuring the bond is as strong as the original material. Popular methods include hot gas welding, extrusion welding, and butt welding. Each method has specific uses depending on the thickness and type of polyethylene being welded.

Credit: www.amazon.com
Introduction To Plastic Welding
Plastic welding is a process that joins plastic materials. It involves heating, melting, and fusing parts together. This technique creates strong and durable bonds. One common material used is polyethylene. It is versatile and widely used in various industries.
Importance Of Plastic Welding
Plastic welding ensures strong and reliable connections. It is essential for creating leak-proof joints. This is crucial in piping systems and containers. Plastic welding also maintains the integrity of the material. It reduces the risk of cracks and breaks.
Plastic welding is cost-effective. It minimizes the need for additional materials like adhesives. This process is environmentally friendly. It often uses recyclable materials, reducing waste.
Applications In Various Industries
Plastic welding is used in many industries. It is vital in the automotive industry. It is used to join parts like bumpers and fuel tanks. The construction industry relies on plastic welding for pipes and fittings.
In the medical field, plastic welding creates sterile equipment. It is used to make items like blood bags and tubing. The packaging industry uses plastic welding for creating strong seals. This ensures the safety and freshness of products.
Industry | Applications |
---|---|
Automotive | Bumpers, fuel tanks |
Construction | Pipes, fittings |
Medical | Blood bags, tubing |
Packaging | Seals, containers |
Understanding Polyethylene
Polyethylene is one of the most common plastics. It is used in various applications, including plastic welding. This material is lightweight, durable, and versatile. Learning about its properties and types helps in effective welding.
Properties Of Polyethylene
Polyethylene has several unique properties. These properties make it suitable for plastic welding.
Property | Description |
---|---|
Lightweight | Polyethylene is very light. It has a density of 0.91-0.96 g/cm³. |
Durable | It is resistant to impact. It does not break easily. |
Flexible | Polyethylene can bend without breaking. This makes it versatile. |
Water-resistant | It does not absorb water. This is ideal for water-related applications. |
Chemical-resistant | Polyethylene resists many chemicals. This ensures durability in harsh environments. |
Common Types Used In Welding
Several types of polyethylene are used in plastic welding. Each type has its advantages.
- High-Density Polyethylene (HDPE)
- HDPE is strong and rigid.
- It is used for heavy-duty applications.
- Low-Density Polyethylene (LDPE)
- LDPE is flexible and soft.
- It is used for films and packaging.
- Linear Low-Density Polyethylene (LLDPE)
- LLDPE combines strength with flexibility.
- It is used in stretch films and flexible tubing.
Preparation For Welding
Proper preparation is vital for effective plastic welding polyethylene. It ensures strong and durable bonds. This section focuses on essential steps to prepare for welding.
Surface Cleaning Techniques
Cleaning the surface is the first step. It removes dirt, grease, and contaminants.
Use these techniques to clean polyethylene surfaces:
- Soap and Water: Wash the surface with warm soapy water. Rinse thoroughly.
- Isopropyl Alcohol: Apply isopropyl alcohol using a clean cloth. Wipe the surface.
- Abrasion: Lightly sand the surface with fine-grit sandpaper. Remove dust with a dry cloth.
Material Compatibility
Ensure the materials are compatible for welding. Check the polyethylene type. Both pieces should be of the same or similar grade.
Here is a simple guide for material compatibility:
Polyethylene Type | Compatible Materials |
---|---|
HDPE (High-Density Polyethylene) | HDPE, LDPE |
LDPE (Low-Density Polyethylene) | LDPE, HDPE |

Credit: www.amazon.com
Welding Methods
Polyethylene plastic welding involves joining pieces of polyethylene material. This process requires heat and pressure. There are different methods to achieve this. Each has its own applications and benefits. Let’s explore the most common welding methods.
Hot Gas Welding
Hot gas welding, also known as hot air welding, uses heated gas. This method melts the plastic surfaces to be joined. The heated gas is usually air or nitrogen.
Here are the steps involved in hot gas welding:
- Clean the surfaces.
- Heat the surfaces with a hot air gun.
- Apply pressure to join the melted surfaces.
- Allow the joint to cool.
Hot gas welding is ideal for small repair jobs. It’s also suitable for fabricating small items.
Extrusion Welding
Extrusion welding is another popular method. It uses an extruder to melt plastic filler material. This molten filler is then applied to the joint area.
Here are the steps involved in extrusion welding:
- Prepare the surfaces by cleaning and preheating.
- Feed the filler material into the extruder.
- Apply the molten filler to the joint.
- Smooth the joint with a roller or paddle.
- Allow the joint to cool.
Extrusion welding is great for large-scale projects. It’s used in tank fabrication and pipe joining.
Both methods require skilled operators. Proper technique ensures strong and durable joints. Choose the method that best fits your project needs.
Essential Tools And Equipment
Plastic welding polyethylene requires specific tools and equipment. Using the right tools ensures strong and durable welds. Below, we discuss the essential tools and equipment for this process.
Welding Guns And Nozzles
A welding gun is the primary tool for plastic welding polyethylene. The gun heats the plastic to its melting point. For polyethylene, a hot air welding gun is ideal. This gun allows precise control of the temperature.
Nozzles are attached to the welding gun. They direct the hot air onto the plastic. Different nozzles serve various purposes. Standard nozzles are good for general welding tasks. Specialized nozzles help with intricate or difficult welds.
Type of Nozzle | Use Case |
---|---|
Standard Nozzle | General welding tasks |
Speed Welding Nozzle | Faster welding with consistent results |
Round Nozzle | Precision welding of small areas |
Safety Gear
Safety gear is crucial when welding polyethylene. Always wear protective gloves. They protect your hands from burns. Heat-resistant gloves are the best choice.
Safety goggles are also essential. They protect your eyes from flying debris and bright light. Choose goggles with a good fit and clear visibility.
An apron or protective clothing shields your body from heat and sparks. Use a heavy-duty apron for better protection.
- Protective gloves
- Safety goggles
- Protective clothing or apron
In addition, ensure proper ventilation in your workspace. This keeps you safe from harmful fumes.
Welding Process
Plastic welding polyethylene involves fusing two pieces of plastic together. This method is effective for creating strong, durable bonds. Understanding the welding process ensures better results and fewer issues.
Step-by-step Guide
- Preparation: Clean the surfaces to remove any dirt or grease. Use isopropyl alcohol for best results.
- Alignment: Secure the pieces in place using clamps or fixtures.
- Heating: Use a plastic welding gun to heat the joint area. The temperature should be around 220°C.
- Welding Rod: Insert the polyethylene welding rod into the heated joint.
- Pressure: Apply gentle pressure to ensure the rod melts into the joint.
- Cooling: Allow the joint to cool naturally. Avoid moving the pieces during cooling.
- Inspection: Check the weld for any gaps or weak spots. Reheat and fill if necessary.
Common Mistakes To Avoid
- Improper Cleaning: Failing to clean surfaces can weaken the weld.
- Wrong Temperature: Using the incorrect temperature can damage the plastic.
- Uneven Pressure: Applying uneven pressure results in weak joints.
- Rushing the Cooling: Moving the pieces before cooling leads to poor welds.
- Ignoring Safety: Always wear safety gear to protect yourself from burns and fumes.
Ensuring Strong Bonds
Achieving robust and durable bonds in plastic welding polyethylene is crucial. Ensuring strong bonds guarantees the longevity and reliability of your welded products. Various techniques and testing methods can help in securing these solid connections. Let’s explore how to test weld strength and troubleshoot weak joints effectively.
Testing Weld Strength
Testing the strength of your welds is essential. It helps verify the quality and durability of the bonds. There are several methods available for testing weld strength, including:
- Tensile Testing: This involves stretching the welded piece until it breaks. It measures the force required to pull the joint apart.
- Bend Testing: This method bends the welded part to see if it holds without cracking.
- Peel Testing: This involves peeling the welded layers to check the bond’s integrity.
Using these methods, you can ensure your welds meet the required standards. Regular testing helps maintain high-quality welds.
Troubleshooting Weak Joints
Identifying and troubleshooting weak joints is vital for maintaining strong bonds. Several factors can cause weak joints, such as:
- Insufficient Heat: Ensure the welding temperature is appropriate for polyethylene.
- Improper Alignment: Align the pieces correctly before welding.
- Contamination: Clean the surfaces thoroughly to remove dirt and grease.
Addressing these issues can significantly enhance weld strength. Regular inspection and maintenance are key to avoiding weak joints.
Maintenance And Repair
Maintaining and repairing polyethylene products extends their lifespan. Proper care ensures your items stay in top shape. Let’s explore some effective methods.
Repair Techniques For Polyethylene
Polyethylene is durable but can suffer damage. Effective repair techniques can restore its integrity.
- Plastic Welding: Use a hot air welder. Melt the edges of the crack and fuse them together.
- Epoxy Resin: Use polyethylene-specific epoxy. Apply it to the damaged area and let it cure.
- Heat Gun: Heat the damaged area. Press it back into shape using a wooden block.
Always clean the damaged area before repairing. This ensures proper adhesion.
Long-term Maintenance Tips
Maintaining polyethylene products prevents frequent repairs. Follow these tips for long-term care.
- Regular Cleaning: Wash with mild soap and water. Avoid harsh chemicals.
- Inspect for Damage: Check for cracks or wear regularly. Early detection prevents bigger issues.
- Store Properly: Keep polyethylene items in a cool, dry place. Avoid direct sunlight.
- Use Protective Coatings: Apply UV-resistant coatings. This prevents sun damage.
Consistent maintenance keeps your polyethylene products in excellent condition. Follow these tips to extend their life.
Expert Tips And Best Practices
Plastic welding polyethylene can be tricky. Following expert tips and best practices ensures a strong and reliable weld. This guide will help you achieve the best results.
Advice From Professionals
Professionals recommend these essential tips for successful polyethylene welding:
- Prepare the Surface: Clean the surfaces before welding. Remove any dirt, grease, or contaminants.
- Use the Right Tools: Ensure you have the correct welding equipment. Use a welding rod compatible with polyethylene.
- Practice Proper Technique: Maintain consistent pressure and speed. Avoid overheating the material.
Following these tips helps achieve a cleaner and stronger weld.
Innovative Techniques
Innovative techniques can improve polyethylene welding. Consider these advanced methods:
- Hot Gas Welding: This method uses a hot air gun. It is ideal for welding thin polyethylene sheets.
- Extrusion Welding: This technique involves an extruder. It is suitable for thicker materials and provides a robust weld.
- Laser Welding: Laser technology offers precision. It is perfect for intricate and detailed welding tasks.
Employing these techniques can enhance the welding process and yield superior results.
Technique | Best For | Key Benefit |
---|---|---|
Hot Gas Welding | Thin Sheets | Easy to Handle |
Extrusion Welding | Thicker Materials | Strong Weld |
Laser Welding | Detailed Work | High Precision |
By adopting these expert tips and innovative techniques, you can achieve excellent results in plastic welding polyethylene.
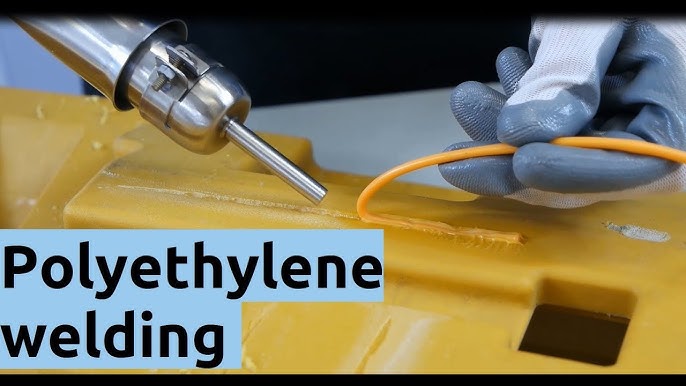
Credit: m.youtube.com
Future Of Plastic Welding
The future of plastic welding polyethylene is bright. New technologies and sustainable methods are changing the industry. This section explores the exciting advancements and environmental considerations.
Technological Advancements
Technological advancements are revolutionizing plastic welding. Laser welding and ultrasonic welding are leading the way. They offer precision and speed.
- Laser welding: Highly accurate and efficient.
- Ultrasonic welding: Fast and reliable for thin materials.
New automation tools are emerging. They reduce human error and increase productivity. Robotics and AI are also playing a crucial role. They bring consistency and quality to plastic welding.
Sustainability Considerations
Sustainability is a major focus in plastic welding. Eco-friendly materials are gaining popularity. They reduce environmental impact and are recyclable.
Energy-efficient methods are also important. They save energy and reduce costs. Solar-powered welding machines are a great example. They use renewable energy and lower carbon footprint.
Businesses are adopting sustainable practices. They aim to reduce waste and promote recycling. This aligns with global efforts to combat climate change.
The future of plastic welding polyethylene is not just about technology. It is also about creating a greener planet. By embracing advancements and sustainability, the industry can thrive and protect the environment.
Frequently Asked Questions
What Is Plastic Welding?
Plastic welding is a process that joins plastic parts using heat. It’s commonly used for materials like polyethylene. This method ensures a strong, durable bond.
Can You Weld Polyethylene?
Yes, you can weld polyethylene using specialized equipment. The process involves heating the plastic parts. This creates a strong and lasting bond.
What Tools Are Needed For Plastic Welding?
Basic tools include a plastic welding gun and filler rods. Additional equipment may include a heat gun and protective gear. These tools ensure precise and safe welding.
Is Plastic Welding Durable?
Plastic welding is highly durable when done correctly. The welded joints are strong and long-lasting. This makes it ideal for various applications.
Conclusion
Mastering plastic welding for polyethylene opens up numerous opportunities. It ensures durable and reliable bonds for various applications. By following proper techniques, you can achieve professional results. Remember to prioritize safety and invest in quality tools. This will make your plastic welding projects successful and efficient.
Happy welding!