Are you seeking a seamless solution for welding polyethylene? Look no further. Welding polyethylene, an art form in itself, demands precision and expertise. Whether you are dealing with high-density or low-density polyethylene, the process requires a delicate touch and the right tools. Our comprehensive guide on welding polyethylene delves into the intricacies of the welding process, offering insights into the most effective techniques and the latest advancements in plastic welding technology. From butt welding to socket fusion and electrofusion, we cover it all.
Our expertise in plastic welding polyethylene ensures that you will find the best practices, tips, and tricks for a successful welding operation. Whether you are a seasoned professional or a novice in the field, this guide is designed to equip you with the knowledge and skills necessary to tackle any welding project involving polyethylene. So, gear up to master the art of welding polyethylene as we unravel the secrets to achieving durable and high-strength polyethylene welds.
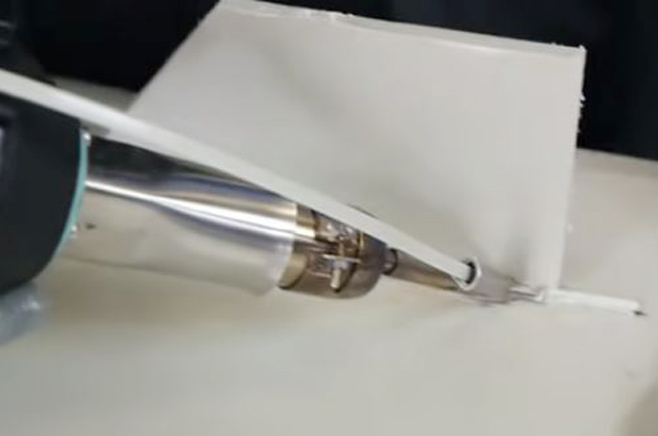
Image by Ataszekinternational on YT
Understanding the Process of Polyethylene Welding
When it comes to welding polyethylene, it’s essential to understand the properties of the material. Polyethylene is known for its high strength, durability, and chemical resistance, making it a popular choice for various applications. However, welding polyethylene requires careful consideration of its molecular structure and the potential challenges associated with fusing this thermoplastic material. Unlike metals, polyethylene undergoes a different fusion process, involving the softening and melting of the material to form a strong bond. Understanding the behavior of polyethylene during the welding process is crucial for achieving reliable and long-lasting welds.
Polyethylene welding involves several techniques, each tailored to specific applications and project requirements. The choice of welding technique depends on factors such as the thickness of the material, the intended use of the welded product, and environmental considerations. By familiarizing yourself with the different welding methods, you can select the most suitable approach for your polyethylene welding projects, ensuring optimal results and performance.
The art of welding polyethylene extends beyond the technical aspects of the process. It also encompasses the ability to adapt to varying welding conditions, troubleshoot potential issues, and consistently produce high-quality welds. By gaining a comprehensive of polyethylene welding, you can enhance your proficiency in working with this versatile thermoplastic material, opening up new possibilities for fabrication and construction projects.
Types of Plastic Welding Polyethylene Techniques
Polyethylene welding encompasses a diverse range of techniques, each tailored to specific applications and project requirements. The most common welding methods for polyethylene include butt welding, socket fusion, and electrofusion. Butt welding involves the fusion of two ends of polyethylene pipes or sheets, creating a seamless joint with uniform strength across the weld. This technique is widely used in the construction of pipelines, water distribution systems, and industrial storage tanks.
Socket fusion, on the other hand, utilizes a specialized fusion tool to join polyethylene pipes and fittings, offering a reliable and leak-proof connection. Electrofusion, a modern welding method, employs electric current to heat and fuse polyethylene components, ensuring precise and efficient welds for various applications.
Each welding technique has its unique advantages and considerations, making it essential to select the most suitable method based on the specific requirements of the welding project. The intricacies of each welding technique, you can harness the full potential of polyethylene welding, achieving seamless joints and robust connections that meet the highest standards of quality and performance.
Advantages of Plastic Welding Polyethylene
Welding polyethylene offers a wide array of advantages, making it a preferred choice for fabricators, engineers, and construction professionals. One of the primary benefits of polyethylene welding is its ability to create strong and durable joints that can withstand challenging environmental conditions, chemical exposure, and mechanical stress. The seamless fusion of polyethylene components ensures leak-proof connections, making it ideal for applications in water management, sewage systems, and industrial fluid transport. Additionally, polyethylene welding enables the fabrication of custom components, such as tanks, containers, and specialized fittings, providing flexibility and customization options for diverse projects.
Plastic welding polyethylene contributes to the longevity and reliability of welded structures, reducing the risk of maintenance issues and costly repairs over time. The lightweight nature of polyethylene, coupled with its corrosion resistance, makes it a versatile material for welding applications in various industries, including agriculture, infrastructure development, and manufacturing. By harnessing the advantages of welding polyethylene, professionals can optimize their fabrication processes, streamline installation procedures, and deliver high-performance solutions that exceed client expectations.
Applications of Plastic Welding Polyethylene
The applications of plastic welding in polyethylene span a wide spectrum of industries and sectors, showcasing the versatility and adaptability of this welding process. In the field of infrastructure development, polyethylene welding plays a vital role in the construction of water supply networks, irrigation systems, and gas distribution pipelines. The ability to create seamless connections and joints using polyethylene welding ensures the integrity and efficiency of these essential infrastructure components, contributing to the sustainable development of communities and urban areas.
Plastic welding in polyethylene finds extensive use in the manufacturing of chemical storage tanks, industrial containers, and specialized equipment for handling corrosive substances. The chemical resistance and durability of polyethylene make it an ideal material for fabricating components that require reliable and long-lasting performance in demanding industrial environments.
The versatility of polyethylene welding extends to the agricultural sector, where it is employed in the construction of irrigation systems, greenhouse structures, and livestock containment facilities, offering cost-effective and resilient solutions for agricultural operations.
The applications of plastic welding in polyethylene are not limited to traditional industries but also extend to innovative sectors such as 3D printing, where polyethylene serves as a viable material for additive manufacturing processes. The ability to weld polyethylene opens up opportunities for creating complex geometries and customized parts using advanced fabrication techniques, contributing to the evolution of additive manufacturing technologies. With its diverse applications across various industries, plastic welding in polyethylene continues to drive innovation and efficiency in the fabrication and construction sectors, showcasing its adaptability and reliability in meeting the evolving needs of modern manufacturing and infrastructure development.
Welding Polyethylene Safety Measures
Safety is paramount in any welding operation, and polyethylene welding is no exception. Prioritizing safety measures not only safeguards the well-being of welding professionals but also ensures the integrity of the welded components and the surrounding environment. When working with polyethylene welding, it is crucial to adhere to established safety protocols, including the use of personal protective equipment (PPE), proper ventilation in welding areas, and adherence to industry regulations and standards. Additionally, the identification and mitigation of potential hazards associated with polyethylene welding, such as exposure to fumes and airborne particles, are essential for creating a safe and healthy work environment.
The safe handling and storage of polyethylene welding equipment, including fusion machines, heating elements, and fusion fittings, contribute to minimizing the risk of accidents and equipment damage. Proper training and certification for polyethylene welding ensure that welding professionals are equipped with the knowledge and skills necessary to execute welding operations safely and efficiently. By instilling a culture of safety awareness and compliance, organizations can mitigate risks, protect their workforce, and uphold the highest standards of occupational health and safety in polyethylene welding activities.
In addition to personal safety measures, environmental considerations play a significant role in polyethylene welding. Proper disposal of waste materials, adherence to environmental regulations, and the implementation of sustainable practices contribute to minimizing the ecological footprint of polyethylene welding processes. By integrating safety measures and environmental stewardship into polyethylene welding operations, professionals can uphold ethical standards and contribute to the sustainable development of the welding industry.
Tools and Equipment for Plastic Welding Polyethylene
The success of a plastic welding polyethylene operation hinges on the utilization of the right tools and equipment, tailored to the specific requirements of the welding project. Essential tools for plastic welding polyethylene include fusion machines, heating elements, cutting tools, and specialized fixtures for holding and aligning polyethylene components during the welding process. Fusion machines play a crucial role in achieving precise and uniform heating of polyethylene components, facilitating seamless fusion and the creation of strong, leak-proof joints. The selection of fusion machines should align with the size and specifications of the polyethylene components being welded, ensuring compatibility and optimal performance.
Heating elements, such as heaters and hot plates, are integral to the polyethylene welding process, providing controlled heat application for softening and fusing the material. The proper calibration and maintenance of heating elements contribute to consistent and reliable welds, reducing the likelihood of defects and inconsistencies in the welded joints.
Additionally, cutting tools designed for polyethylene enable precise trimming and preparation of welding surfaces, ensuring clean and uniform mating surfaces for the fusion process. The use of specialized fixtures and clamps enhances the alignment and stability of polyethylene components during welding, minimizing misalignments and distortions in the final welded joints.
The selection of fusion fittings, such as couplings, elbows, and tees, plays a critical role in creating leak-proof connections and transitions in polyethylene piping systems. By utilizing high-quality fusion fittings that comply with industry standards and material specifications, welding professionals can ensure the integrity and performance of welded polyethylene assemblies. The proper maintenance and calibration of tools and equipment for welding polyethylene are essential for achieving consistent and high-quality welds, underscoring the importance of investing in reliable and well-maintained welding resources.
Techniques for Plastic Welding Polyethylene
The successful welding of polyethylene hinges on the mastery of techniques that encompass the preparation, heating, and fusion of the material to create robust and enduring joints. Proper surface preparation is a fundamental aspect of plastic welding polyethylene, involving the cleaning and machining of mating surfaces to remove contaminants, burrs, and irregularities that can compromise the quality of the weld. The use of appropriate cleaning solvents and mechanical tools ensures the establishment of clean and uniform welding surfaces, laying the foundation for successful fusion and bonding of polyethylene components.
Heating plays a pivotal role in plastic welding polyethylene, requiring controlled and uniform application of heat to soften the material without causing degradation or overheating. The selection of heating elements and fusion machines that deliver precise temperature control and heat distribution is essential for achieving consistent and reliable welds. Maintaining the heating parameters within the recommended ranges for plastic welding polyethylene contributes to the formation of strong and durable joints, minimizing the risk of defects and weak points in the welded assembly.
The fusion phase of polyethylene welding demands attentiveness to the heating and cooling cycles, ensuring that the material reaches the optimal fusion temperature and exhibits proper flow characteristics for creating a seamless bond. Proper fusion pressure and heating time, coupled with meticulous monitoring of the fusion process, are essential for achieving uniform and reliable welds.
Post-fusion cooling and consolidation of the welded joint contribute to the development of a robust molecular bond, enhancing the strength and integrity of the polyethylene weld. By mastering the techniques of plastic welding polyethylene, professionals can elevate the quality and performance of welded components, meeting the stringent demands of diverse applications and industries.
Common Mistakes in Plastic Polyethylene Welding
Despite the precision and expertise required for plastic welding polyethylene, several common mistakes can compromise the quality and integrity of the welded joints. Inadequate surface preparation, characterized by the presence of contaminants, moisture, or inadequate cleaning, can lead to weak adhesion and reduced bond strength in polyethylene welds.
Insufficient heating or overheating during the fusion process can result in incomplete fusion, cold fusion, or material degradation, leading to compromised weld integrity and performance. Improper fusion pressure and cooling cycles can also contribute to defects in polyethylene welds, such as voids, delamination, and brittleness, undermining the reliability of the welded components.
Furthermore, the use of substandard or incompatible fusion fittings, heating elements, and welding tools can introduce inconsistencies and weaknesses in polyethylene welds, jeopardizing their structural integrity and leak resistance. Inadequate training and lack of certification in polyethylene welding techniques can lead to errors in process control, fusion parameters, and weld inspection, diminishing the quality and reliability of the welded joints.
By identifying and addressing these common mistakes in plastic welding polyethylene, professionals can elevate their welding practices, reduce rework and repair costs, and deliver superior quality welds that meet the highest standards of performance and durability.
Training and Certification for Plastic Welding Polyethylene
The acquisition of specialized training and certification in welding polyethylene is essential for professionals seeking to excel in this specialized field. Training programs that encompass theoretical knowledge, hands-on practical experience, and industry best practices equip welding professionals with the skills and competencies necessary to execute polyethylene welding operations with precision and expertise. Comprehensive training in polyethylene welding covers topics such as material properties, welding techniques, safety protocols, and quality assurance measures, providing a holistic understanding of the intricacies of working with polyethylene.
Certification in polyethylene welding validates the proficiency and qualifications of welding professionals, affirming their ability to adhere to industry standards, regulatory requirements, and best practices in polyethylene welding. Certified welders demonstrate their commitment to upholding the highest standards of quality, safety, and performance in polyethylene welding activities, instilling confidence in clients and employers regarding their capabilities.
Additionally, ongoing professional development and recertification in polyethylene welding enable welding professionals to stay abreast of the latest advancements in welding technology, material science, and industry trends, enhancing their expertise and adaptability in the ever-evolving field of polyethylene welding.
By investing in training and certification for polyethylene welding, professionals elevate their professional credentials, expand their career opportunities, and contribute to the overall advancement and standardization of polyethylene welding practices. The pursuit of excellence through continuous learning and certification underscores the dedication of welding professionals to mastering the art of polyethylene welding and delivering exceptional results in various welding applications and industries.
Conclusion
Plastic welding polyethylene encompasses a diverse array of techniques, considerations, and best practices that converge to create durable and high-strength polyethylene welds. From understanding the properties of polyethylene to mastering the intricacies of welding techniques, the art of welding polyethylene demands expertise, precision, and a commitment to quality. By embracing the advantages of plastic welding polyethylene, professionals can unlock new possibilities for fabricating, constructing, and innovating across a spectrum of industries and applications. The applications of plastic welding in polyethylene reflect its adaptability and reliability in addressing the evolving needs of modern manufacturing and infrastructure development.
Moreover, safety measures, proper tools and equipment, and the mastery of welding techniques are essential pillars of successful polyethylene welding operations, ensuring the integrity, performance, and longevity of welded components. By addressing common mistakes in polyethylene welding and prioritizing training and certification, welding professionals can elevate their skills, reduce rework, and deliver superior quality welds that meet the highest standards of performance and durability.