Plasma cutting is an essential skill for metalworkers, and mastering it can take time and practice. Whether you are a beginner or an experienced professional, there are always ways to improve your techniques and achieve better results in every cut you make. In this comprehensive guide, we will share some of the best plasma cutting tips and tricks for improving your precision, efficiency, and overall performance.
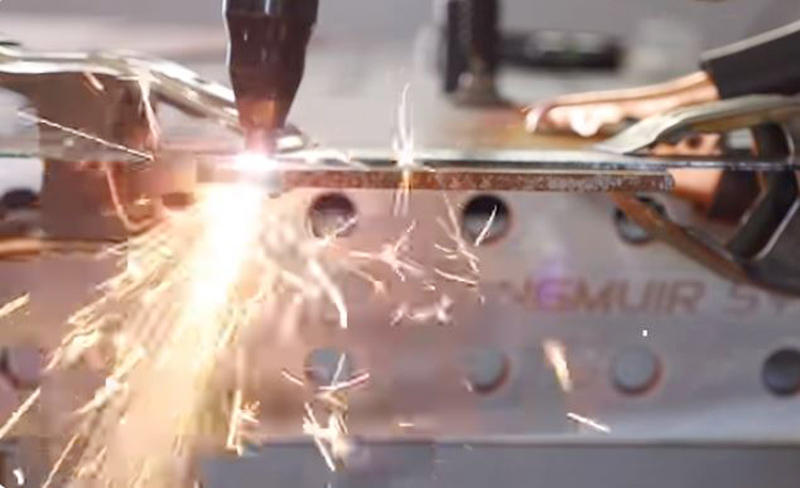
Plasma Cutting Techniques
If you want to achieve optimal results in plasma cutting, it’s essential to understand the various techniques available and their applications. Here, we will explore the most common plasma cutting techniques used by metalworkers, along with some advanced techniques to take your skills to the next level.
Types of Plasma Cutting Techniques
Standard or Conventional Plasma Cutting
This is the most common plasma cutting technique used by hobbyists and professionals alike. It involves a single gas (usually air) being ionized to create plasma at the nozzle, which then cuts through metal. Standard plasma cutting is ideal for cutting through materials of average thickness (up to 1 inch).
High-Definition Plasma Cutting
This technique is used for cutting materials of high precision and thickness. It uses a nozzle that is capable of focusing the plasma arc into a smaller area, resulting in a finer and more accurate cut.
Water Injection Plasma Cutting
Water injection plasma cutting is used for cutting non-ferrous metals, such as aluminum. The technique involves injecting water into the plasma stream to reduce the heat of the cutting process. This technique results in a smoother edge and less warping of the material.
Plasma Cutting Techniques
Dual-Gas Plasma Cutting
This technique involves using a mixture of gases, such as argon and hydrogen, to create a plasma stream with high energy and heat. Dual-gas plasma cutting is ideal for metals with high thermal conductivity.
Controlled Plasmas Cutting
This technique uses computer-controlled equipment to create the plasma stream. It allows for precise control over the cutting speed, angle, and depth, resulting in highly detailed cuts on a variety of metal materials.
Using these advanced techniques can take your plasma cutting skills to the next level, allowing you to achieve even greater accuracy and consistency in every cut.
plasma Cutter Settings
Setting up your plasma cutter correctly is crucial to achieving clean and accurate cuts. Here are some expert plasma cutting advice to ensure a successful setup:
Choosing the right amperage
Selecting the correct amperage setting for your plasma cutter is essential for achieving the best results. Generally, the thicker the material you are cutting, the higher the amperage setting you will need. Most plasma cutters have a recommended amperage chart in the user manual. Follow this chart or consult with an expert to ensure you are using the right amperage for your material.
Regulating gas pressure
Proper gas pressure plays a key role in plasma cutting. A good rule of thumb is to set your gas pressure to 70 psi for handheld torches and 80 psi for mechanized cutting. Be sure to check your user manual for the recommended gas pressure for your specific plasma cutter.
Using the right consumables
The correct consumables can make all the difference in the precision of your cuts. It’s essential to use manufacturer-recommended consumables for your plasma cutter. Using the wrong consumables may cause uneven cuts and damage to your equipment.
Following these effective plasma cutting strategies will help you set up your plasma cutter for success. Take your time and make sure everything is set up correctly before making any cuts. A well-set-up plasma cutter will save you time and money in the long run.
Maintaining and Troubleshooting for Plasma Cutter
Proper maintenance of your plasma cutter is critical to ensure its longevity and peak performance. Here are some expert plasma cutting advice to help you keep your machine running smoothly:
Read the manual
It may seem simple, but many people do not read the manual that comes with their plasma cutter. The manual provides essential information on maintenance schedules, replacement parts, and troubleshooting tips. This valuable resource should be your first point of reference.
Clean the machine
Keeping your plasma cutter clean is essential to prevent dust and debris buildup that can cause damage over time. Use a clean cloth to wipe down the exterior of the machine and blow compressed air into the vents to remove any debris.
Monitor consumables
The consumables of a plasma cutter, such as the electrode and nozzle, wear out over time and need periodic replacement. Keep track of consumable usage and replace them according to the manufacturer’s recommendations to ensure consistent cutting quality.
Check for leaks
Gas leaks in the plasma cutter can cause poor cutting quality and, in extreme cases, pose a safety risk. Regularly check gas hoses and connections for any signs of wear and tighten them as needed.
Troubleshoot common issues
If you encounter issues with your plasma cutter, such as poor cutting quality or a loss of power, refer to the troubleshooting section of your manual. Some common issues and solutions include cleaning the machine, replacing consumables, and adjusting the gas pressure.
“Proper maintenance and troubleshooting of your plasma cutter are essential to ensure consistent cutting quality and prolong the life of your machine. Regular cleaning, monitoring of consumables, and checking for leaks are some key steps to keep in mind.”
Enhancing Precision with Cutting Techniques
When it comes to plasma cutting, precision is key. Regardless of the project, you want your cuts to be accurate and clean. Here are some advanced plasma cutting techniques and essential tips to help you achieve precision.
Drag Cutting
Drag cutting is a technique where you drag the plasma torch along the metal surface, making the cut. This technique is useful for making long, straight cuts, and when you need to keep the torch steady. To ensure smooth and precise drag cutting, keep the torch perpendicular to the metal surface and move it at a consistent speed.
Bevel Cutting
Bevel cutting involves cutting at an angle to create a beveled edge. This technique is useful for welding and creating joints. When bevel cutting, use a guide or angle marker to ensure the correct angle. You can also use the drag technique while bevel cutting, which allows for more control over the cut.
Pierce Cutting
Pierce cutting is a technique where you make a hole in the metal with the torch and then continue the cut from that point. This technique is commonly used for creating intricate shapes or for cutting thicker metals. To make a precise hole, mark the center point and use a center punch to create a small indentation. Then, use the plasma cutter to pierce through the metal.
Using a Straight Edge Guide
Using a straight edge guide can provide stability and accuracy when making cuts. The guide is placed on the metal surface, and the plasma torch is run along it to create the cut. This technique is useful for making long, straight cuts or when you’re cutting a large piece of metal.
Using a Circle Cutting Guide
A circle cutting guide can be used to create precise circles and curves. The guide is attached to the plasma torch and is adjustable, allowing you to create circles of varying sizes. This technique is useful for creating rounded edges or for cutting holes in metal.
By incorporating these advanced plasma cutting techniques and essential tips, you can improve your precision and take your metalwork to the next level. Experiment with different techniques and keep practicing to master the craft of plasma cutting.
Increasing Efficiency in Plasma Cutting
Plasma cutting is a versatile and efficient method of metalworking that can save you time and resources. Here are some top plasma cutting hacks and effective strategies to help you increase efficiency in your projects:
Maximize consumable life
Make sure you’re using the right consumables for your plasma cutter and that they are properly installed and maintained. This will ensure you get the most out of each consumable and avoid unnecessary downtime.
Choose the right amperage
Using the correct amperage for your project is essential for achieving clean and accurate cuts. Make sure to follow the manufacturer’s recommendations for your specific cutter and material.
Optimize gas pressure
Proper gas pressure is crucial for quality plasma cuts. Too much or too little gas can affect the cut quality and shorten consumable life. Follow the manufacturer’s recommendations and test the gas pressure regularly to ensure optimal performance.
Use cutting guides
Cutting guides can help you achieve straight, precise cuts and save time in the process. Many plasma cutters come with built-in cutting guides, but you can also purchase or make your own.
Invest in a quality air compressor
A quality air compressor can improve the performance of your plasma cutter and help extend the life of your consumables. Make sure to choose an air compressor that can deliver the necessary CFM (cubic feet per minute) for your cutter.
Practice good housekeeping
Keeping your workspace clean and organized can save you time and make the plasma cutting process smoother. Make sure to clean up any debris and keep your consumables and other tools organized and easily accessible.
By implementing these top plasma cutting hacks and effective strategies, you can increase efficiency in your projects, save time, and achieve the best results possible.
Keep on honing your craft
Mastery of plasma cutting requires knowledge, skill, and practice. Don’t be discouraged if you don’t see immediate results; keep honing your craft, and you will soon be able to produce high-quality metalwork. By implementing the top hacks and strategies shared in this guide, you can increase your productivity and make the most of each cut.
Conclusion Thoughts
Plasma cutting is a demanding craft, but with the right tips and tricks, you can master it. We hope this comprehensive guide has been helpful in improving your precision and efficiency in every cut you make. By understanding the different plasma cutting techniques, setting up your plasma cutter correctly, maintaining and troubleshooting your equipment, and enhancing precision with cutting techniques, you can achieve the desired results for your metalwork projects.
FAQ’s
What are some essential plasma cutting tips for beginners?
Some essential plasma cutting tips for beginners include ensuring proper grounding of the workpiece, maintaining the correct distance between the torch tip and the material, and using the appropriate amperage and gas pressure for the thickness of the metal being cut.
How can I improve precision in plasma cutting?
To improve precision in plasma cutting, it’s important to practice steady hand movement, use a guide or template when necessary, and choose the appropriate cutting techniques such as drag cutting or bevel cutting.
What are some common issues I may encounter while plasma cutting?
Some common issues you may encounter while plasma cutting include dross buildup, warping of the material, and erratic arcs. These issues can often be resolved by adjusting the cutting speed, gas pressure, or replacing worn consumables.
How do I maintain my plasma cutter?
To maintain your plasma cutter, it’s important to regularly clean or replace consumables, perform routine inspections for any signs of wear or damage, and follow the manufacturer’s guidelines for lubrication and maintenance.
What are some advanced plasma cutting techniques?
Some advanced plasma cutting techniques include precision piercing, multi-pass cutting, and hole cutting. These techniques can be used to achieve intricate designs or precise cuts in various types of metal.
How can I increase efficiency in plasma cutting?
To increase efficiency in plasma cutting, you can optimize your cutting speed, adjust the amperage and gas pressure for the specific material, and utilize cutting techniques that minimize wasted material or reduce the need for secondary operations.