As pipes wind their way through diverse terrains, the integrity of their welds is paramount to sustaining the smooth flow of vital resources. This is where pipeline welding rigs step in as the unsung heroes of the energy and infrastructure sectors. These specialized rigs form the cornerstone of seamless pipeline construction, ensuring precise welds that endure the test of time.
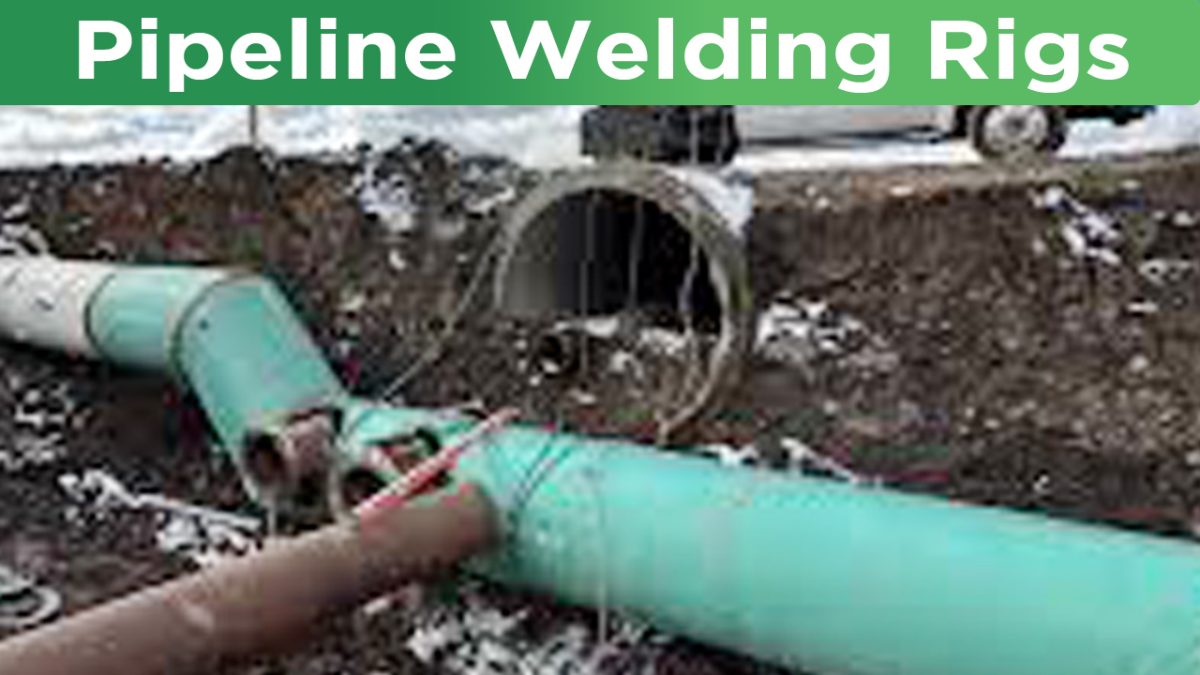
Importance of High-Quality Pipeline Welding Rigs
High-quality pipeline welding rigs are indispensable for ensuring the longevity and reliability of pipelines. The ability of these rigs to produce consistent, high-strength welds is critical for the safe and efficient transportation of liquids and gases. Moreover, the durability of these welds is essential for withstanding environmental stresses and maintaining the structural integrity of the pipelines over time.
Pipeline welding rigs are designed to withstand rugged terrains, extreme weather conditions, and challenging working environments. Their robust construction and advanced features enable them to meet the stringent demands of pipeline projects, making them a vital asset in the construction and maintenance of pipeline networks.
Efficient pipeline welding rigs contribute to the reduction of potential leaks and failures, thereby enhancing the overall safety and reliability of the pipeline infrastructure. By ensuring the integrity of the welds, these rigs play a pivotal role in preventing costly and hazardous incidents, making them an indispensable component of the pipeline construction process.
Key Components of Pipeline Welding Rigs
Pipeline welding rigs consist of several key components that collectively contribute to their effectiveness and reliability. The welding power source, welding head, control system, and support equipment are integral elements that work in unison to achieve precise and durable welds.
The welding power source provides the necessary energy for the welding process, typically utilizing advanced technologies to ensure stable and consistent power output. The welding head is responsible for positioning and manipulating the welding torch, enabling it to accurately fuse the pipe sections. The control system governs the parameters of the welding process, including the speed, heat, and pressure, to maintain optimal weld quality. Additionally, support equipment such as pipe handling systems and alignment tools facilitate the proper positioning and alignment of the pipes during the welding operation.
Each component plays a critical role in the seamless functioning of pipeline welding rigs, ensuring that the welding process meets the highest standards of precision and durability. The integration and synchronization of these components are essential for achieving reliable and long-lasting welds in pipeline construction.
Types of Pipeline Welding Rigs
Pipeline welding rigs are available in various configurations to cater to the diverse requirements of pipeline construction projects. One of the primary distinctions lies in the mobility and setup of the rigs, with options ranging from stationary rigs to self-propelled and track-mounted rigs.
Stationary pipeline welding rigs are designed for fixed-site operations, offering stability and enhanced control over the welding process. These rigs are suitable for projects where the pipeline sections are brought to the welding site for assembly. On the other hand, self-propelled and track-mounted rigs are equipped with mobility features that enable them to traverse challenging terrains and access remote locations, making them well-suited for large-scale pipeline projects that span expansive geographical areas.
Another classification of pipeline welding rigs pertains to the welding method employed. The two primary welding methods utilized in pipeline construction are shielded metal arc welding (SMAW) and automatic welding processes such as gas metal arc welding (GMAW) and flux-cored arc welding (FCAW). Each welding method has its unique advantages and applications, and the selection of the appropriate rig depends on the specific requirements of the project.
The diversity of pipeline welding rig types allows for flexibility in addressing the distinct needs of various pipeline construction projects, ensuring that the welding process is tailored to the specific characteristics of the pipelines and the surrounding environment.
Choosing the Right Pipeline Welding Rig for Your Project
Selecting the optimal pipeline welding rig for a project involves a comprehensive assessment of the project’s scope, environmental conditions, and technical specifications. Factors such as the pipe diameter, material composition, welding method, and accessibility of the construction site are essential considerations in determining the most suitable rig for the job.
For projects involving large-diameter pipelines or those requiring extensive mobility, self-propelled or track-mounted welding rigs equipped with automatic welding processes are preferred. These rigs offer the versatility and maneuverability necessary for addressing the challenges posed by expansive pipeline installations and rugged terrains. Conversely, stationary welding rigs are well-suited for projects with smaller pipe diameters and fixed-site operations, providing precise control over the welding process.
The material compatibility of the welding rig, particularly in relation to the type of pipes being welded, is a critical factor in ensuring the quality and integrity of the welds. Different welding processes and rig configurations may be better suited for specific pipe materials, necessitating a thorough evaluation of the welding rig’s compatibility with the project’s material requirements.
Furthermore, considerations related to safety features, operator ergonomics, and maintenance requirements play a vital role in the selection process, ensuring that the chosen welding rig aligns with the project’s operational and safety standards.
Maintenance and Safety Tips for Pipeline Welding Rigs
The maintenance and safe operation of pipeline welding rigs are paramount to their performance and the well-being of the operators. Regular maintenance routines, including inspections, lubrication, and component replacements, are essential for preserving the functionality and longevity of the rigs. Adhering to the manufacturer’s maintenance guidelines and scheduling routine servicing are imperative in mitigating the risk of equipment malfunctions and ensuring the continued reliability of the rigs.
Safety protocols and training programs are fundamental aspects of operating pipeline welding rigs, safeguarding the operators against potential hazards and accidents. Rigorous training in welding techniques, equipment operation, and safety procedures equips the operators with the knowledge and skills necessary to execute the welding tasks competently and securely.
Implementing comprehensive safety measures, such as the use of personal protective equipment (PPE), adherence to established welding procedures, and adherence to industry standards, fosters a secure working environment and minimizes the likelihood of occupational incidents.
Innovations and Advancements in Pipeline Welding Rigs
The realm of pipeline welding rigs has witnessed significant advancements driven by technological innovations aimed at enhancing efficiency, precision, and safety. The integration of automation and robotics in welding processes has revolutionized the industry, enabling the development of sophisticated rigs equipped with advanced control systems and real-time monitoring capabilities.
Remote welding systems, augmented reality interfaces, and sensor-based technologies have emerged as cutting-edge features that optimize the welding process and provide valuable insights into weld quality and performance. These innovations not only elevate the accuracy and consistency of welds but also contribute to the reduction of operational downtime and the enhancement of overall productivity.
In addition to technological advancements, environmental sustainability and energy efficiency have become focal points in the evolution of pipeline welding rigs. The integration of eco-friendly practices, such as energy-efficient welding power sources and recyclable components, aligns with the industry’s commitment to minimizing environmental impact and promoting sustainable construction practices.
The convergence of technological innovations and sustainability initiatives has propelled the development of next-generation pipeline welding rigs, setting new benchmarks for precision, reliability, and environmental responsibility in pipeline construction.
Top Manufacturers of Pipeline Welding Rigs
Several renowned manufacturers specialize in producing high-quality pipeline welding rigs, offering a diverse range of rigs tailored to specific project requirements. Companies such as Lincoln Electric, Miller Electric Mfg. LLC, ESAB, and Red-D-Arc Welderentals are esteemed for their expertise in manufacturing cutting-edge welding equipment and providing comprehensive solutions for pipeline construction.
These manufacturers leverage advanced engineering techniques and state-of-the-art technologies to design and fabricate pipeline welding rigs that meet the exacting demands of the industry. Their commitment to innovation, quality, and customer satisfaction has solidified their positions as leaders in the realm of pipeline welding equipment, earning the trust and confidence of pipeline contractors and operators worldwide.
The reputation and track record of these manufacturers underscore the reliability and performance of their pipeline welding rigs, making them preferred choices for contractors seeking top-tier equipment for their pipeline projects.
Training and Certification for Pipeline Welding Rig Operators
Proficient operation of pipeline welding rigs necessitates comprehensive training and certification to ensure the competence and safety of the operators. Specialized training programs, often provided by welding equipment manufacturers or accredited training institutions, equip operators with the requisite skills in rig operation, welding techniques, and safety protocols.
Attainment of industry-recognized certifications, such as the American Welding Society (AWS) certification, validates the proficiency of operators in handling pipeline welding rigs and executing welding tasks in compliance with industry standards. Certification programs encompass theoretical knowledge, practical skills assessment, and adherence to safety regulations, establishing a benchmark for the professional competence of pipeline welding rig operators.
Continual professional development and refresher training further enhance the proficiency and awareness of operators, ensuring that they remain abreast of the latest technological advancements and industry best practices in pipeline welding.
Conclusion
Pipeline welding rigs stand as indispensable assets in the construction and maintenance of robust, interconnected pipeline networks. Their role in ensuring the precision, durability, and safety of pipeline welds is paramount to the reliability and efficiency of the entire pipeline infrastructure. As technological advancements continue to drive the evolution of pipeline welding rigs, the industry is poised to witness further innovations that elevate the standards of pipeline construction, cementing the pivotal position of pipeline welding rigs as the backbone of seamless pipeline welding.
The future of pipeline construction hinges on the continued advancement of pipeline welding rigs, encompassing enhanced efficiency, sustainability, and safety. With the collaboration of skilled operators, leading manufacturers, and progressive technologies, pipeline welding rigs will continue to play a vital role in shaping the interconnected network of pipelines that sustains the flow of essential resources across diverse landscapes and regions.
By embracing the capabilities and potential of pipeline welding rigs, the industry charts a course toward a future characterized by resilient, high-performance pipeline systems that meet the evolving needs of society and the environment.