The no gas MIG welder, also known as a flux-cored welder, is a type of welding equipment that allows beginners to dive into the world of welding without the need for gas cylinders. Unlike traditional MIG welders that require a shielding gas to protect the weld pool from atmospheric contamination, the no gas MIG welder uses a flux-cored wire to create a protective shield. This wire contains a flux compound that releases a gas when heated, creating a shielding effect.
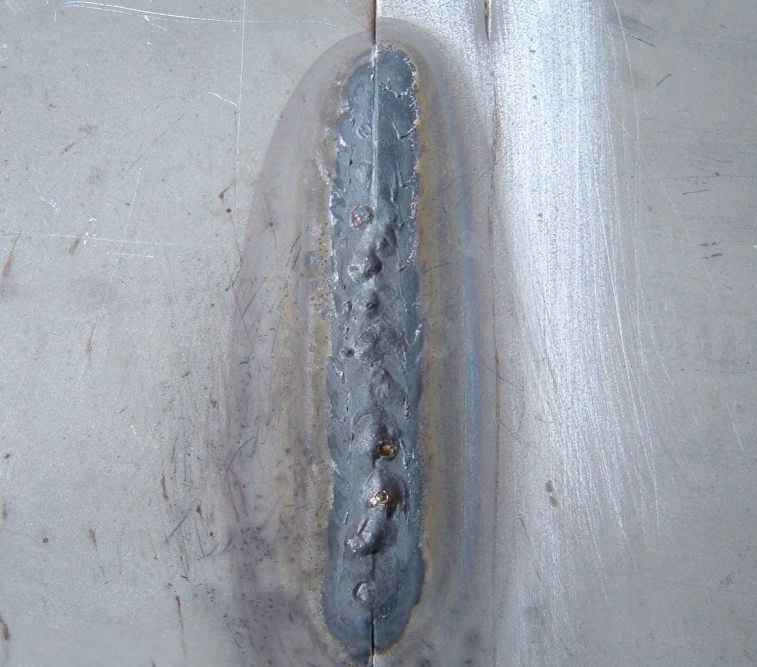
The no gas MIG welder is a versatile and portable tool that offers a range of benefits for beginners. It’s perfect for small repairs, hobby projects, and light fabrication work. With its compact size and user-friendly design, this welder is easy to handle, making it ideal for those just starting out on their welding journey.
Using a no gas MIG welder is relatively straightforward. The wire is fed through the welder’s torch, and when the trigger is pulled, an electric arc is created between the wire and the workpiece. As the wire melts, it forms a weld pool that fuses the pieces together. The flux compound in the wire creates a protective gas shield that prevents contamination and produces clean, strong welds.
Advantages of using a no gas MIG welder
There are several advantages to using a no gas MIG welder, especially for beginners. Let’s explore some of the key benefits:
Cost-effectiveness
One of the biggest advantages of the no gas MIG welder is its cost-effectiveness. By eliminating the need for gas cylinders, this welder helps you save money on consumables. The flux-cored wire used in this type of welder is more affordable compared to purchasing gas cylinders, making it an excellent investment for those on a budget.
Portability
The no gas MIG welder is typically compact and lightweight, making it highly portable. You can easily transport it to different locations or move it around your workshop. This portability is especially beneficial for beginners who may not have a dedicated welding space and need to work in different areas.
Versatility
The no gas MIG welder offers versatility in terms of the types of projects you can tackle. It can be used for various welding applications, including repairs, fabrication, and DIY projects. Whether you’re working with mild steel, stainless steel, or aluminum, the no gas MIG welder can handle a wide range of materials.
Ease of use
For beginners, ease of use is crucial. The no gas MIG welder is designed with user-friendliness in mind. It typically features simple controls and settings, making it easier for beginners to learn and operate. With a bit of practice and guidance, you can quickly master the basics of welding using this type of welder.
Quality welds
Despite its simplicity, the no gas MIG welder is capable of producing high-quality welds. The flux-cored wire provides excellent penetration and fusion, resulting in strong and durable welds. With proper technique and practice, you can achieve professional-looking welds even as a beginner.
Types of no gas MIG welders
When it comes to no gas MIG welders, there are a few different types to choose from. Let’s take a closer look at each type:
Self-shielded flux-cored welders
These welders use a flux-cored wire that contains a self-shielding flux compound. The flux releases a gas when heated, creating a protective shield around the weld pool. Self-shielded flux-cored welders are popular among beginners due to their simplicity and ease of use.
Gas-shielded flux-cored welders
Unlike self-shielded flux-cored welders, gas-shielded flux-cored welders require the use of an external shielding gas. The gas is typically a mixture of carbon dioxide and argon, which provides better control over the welding process. Gas-shielded flux-cored welders are known for producing cleaner and more precise welds.
Dual-purpose welders
Some welders on the market offer the option to switch between no gas (flux-cored) and gas (MIG) welding. These dual-purpose welders provide versatility and allow you to choose the welding method that best suits your needs. They are a good option if you anticipate working on a variety of projects that may require different welding techniques.
When choosing a no gas MIG welder, consider factors such as your budget, the types of projects you plan to tackle, and your skill level. It’s important to select a welder that aligns with your specific requirements and goals.
Features to consider when buying a no gas MIG welder
Before purchasing a no gas MIG welder, it’s essential to consider a few key features. These features can greatly impact your welding experience and the quality of your welds. Here are some features to keep in mind:
Power output
The power output of a welder determines its welding capabilities. Higher power output allows for welding thicker materials and achieving deeper penetration. Consider the thickness of the materials you plan to work with and choose a welder with a suitable power output.
Wire feed speed control
Wire feed speed control allows you to adjust the rate at which the wire is fed through the welder. This control is crucial for achieving optimal weld bead size and penetration. Look for a welder that offers precise wire feed speed control to ensure consistent and controlled welding.
Voltage control
Some no gas MIG welders come with voltage control, which allows you to adjust the welding voltage. Voltage control provides flexibility and helps you achieve the desired weld characteristics. This feature is particularly useful when working with different materials and thicknesses.
Duty cycle
The duty cycle refers to the amount of time a welder can operate continuously before needing to cool down. A higher duty cycle means the welder can work for longer periods without overheating. Consider the duration of your welding sessions and choose a welder with an appropriate duty cycle to avoid interruptions.
Portability
If you anticipate moving your welder frequently or working in different locations, portability is an important factor to consider. Look for a welder that is lightweight and easy to transport. Some welders also come with handles or wheels for added convenience.
Safety features
Welding can be hazardous, so it’s crucial to prioritize safety. Look for welders that offer safety features such as thermal overload protection, voltage overload protection, and short circuit protection. These features can help prevent accidents and protect both you and your equipment.
Taking the time to research and compare different welders based on these features will ensure that you find the right no gas MIG welder for your needs.
Setting up a no gas MIG welder
Setting up a no gas MIG welder is a relatively simple process. Here’s a step-by-step guide to get you started:
Choose the right location: Find a well-ventilated area with sufficient space for your welding activities. Ensure that there are no flammable materials nearby and that you have a clear workspace.
Prepare your workpiece: Clean and prepare the surfaces you plan to weld. Remove any rust, paint, or debris that may interfere with the welding process. Proper preparation ensures better weld quality and improves the overall strength of the weld.
Select the appropriate wire: Depending on the type of material you’re working with, choose the appropriate flux-cored wire. Different wires are designed for specific materials, so make sure you have the right one for your project.
Load the wire: Open the wire feed compartment on your welder and load the wire spool. Follow the manufacturer’s instructions for proper loading. Make sure the wire is properly seated and secured.
Set the wire feed speed: Adjust the wire feed speed according to the welding parameters recommended for your specific wire and material. The proper wire feed speed ensures smooth and controlled welding.
Connect the ground clamp: Attach the ground clamp to your workpiece. This provides a safe electrical connection and helps ground the welding circuit.
Put on safety gear: Before starting the welding process, put on your safety gear, including a welding helmet, gloves, and protective clothing. Safety should always be a top priority when welding.
Test the welder: Run a test weld on a scrap piece of material to ensure that the welder is functioning correctly and that the settings are appropriate for your project. Make any necessary adjustments before proceeding.
Once you have completed these steps, you’re ready to start welding with your no gas MIG welder. Remember to always follow safety guidelines and practice proper welding techniques for optimal results.
Safety precautions when using a no gas MIG welder
Welding can be a hazardous activity if proper safety precautions are not taken. Here are some essential safety precautions to keep in mind when using a no gas MIG welder:
Protective gear
Always wear appropriate protective gear, including a welding helmet with a proper shade, gloves, long-sleeved clothing, and closed-toe shoes. Welding produces intense heat, sparks, and UV radiation, so protecting your eyes, skin, and hands is crucial.
Ventilation
Ensure that your workspace is well-ventilated to prevent the accumulation of harmful fumes and gases. If working indoors, use exhaust fans or open windows to allow fresh air circulation. If ventilation is insufficient, consider using a fume extraction system.
Fire safety
Welding involves the use of heat and sparks, which can ignite flammable materials. Clear the area of any combustible materials and have a fire extinguisher readily accessible. Take extra precautions when working near flammable substances or in confined spaces.
Grounding
Proper grounding is essential for electrical safety. Ensure that the workpiece and the welder are properly grounded to avoid electrical shocks and potential damage to the equipment.
Avoid welding in confined spaces
Welding in confined spaces can increase the risk of exposure to harmful fumes and gases. If welding in a confined space is necessary, ensure proper ventilation and use respiratory protection to minimize the risk.
Inspect your equipment
Regularly inspect your welder and welding accessories for any signs of damage or wear. Faulty equipment can result in accidents, so it’s important to address any issues promptly.
Training and knowledge
Proper training and knowledge are essential for safe welding. Take the time to educate yourself on welding techniques, safety procedures, and equipment operation. Consider taking a welding course or seeking guidance from experienced welders.
By following these safety precautions, you can minimize the risks associated with welding and ensure a safe working environment.
Basic techniques for welding with a no gas MIG welder
Mastering the basic techniques of welding is vital for achieving clean, strong, and durable welds. Here are some fundamental techniques to practice when using a no gas MIG welder:
- Positioning: Position yourself comfortably and maintain a stable stance while welding. Use both hands to support the torch and control the movement.
- Arc length: Maintain a consistent arc length between the tip of the wire and the workpiece. The optimal arc length is typically around 1/4 inch. Too short of an arc can cause the wire to stick, while too long of an arc can result in poor penetration.
- Travel speed: Control your travel speed to ensure proper heat input and fusion. Moving too slowly can cause excessive heat buildup, while moving too quickly may result in insufficient penetration. Practice maintaining a steady travel speed for consistent welds.
- Angle and direction: Hold the torch at a slight angle, typically around 15-45 degrees, depending on the joint and welding position. The direction of travel should be towards the unwelded portion of the joint. Experiment with different angles and directions to find what works best for your project.
- Weld bead size: Achieving the desired weld bead size requires proper wire feed speed and travel speed control. Practice adjusting these settings to achieve the desired bead appearance and size.
- Overlap technique: When welding joints, use a slight overlap technique to ensure proper fusion. Overlapping the weld bead onto the previous weld creates a strong and continuous bond.
- Pause and restart: If you need to pause during welding, keep the torch in position but release the trigger to stop the wire feed. When restarting, briefly pause to establish the arc before continuing the weld.
- Practice and consistency: Welding is a skill that requires practice to master. Consistency in technique, such as maintaining a consistent arc length and travel speed, is key to achieving consistent and high-quality welds.
Common mistakes to avoid when using a no gas MIG welder
As a beginner using a no gas MIG welder, it’s common to make mistakes. Here are some common mistakes to avoid to ensure better welding results:
Improper wire feed speed
Incorrect wire feed speed can lead to inconsistent and poor-quality welds. Take the time to experiment and find the optimal wire feed speed for your specific project. Refer to the manufacturer’s recommendations as a starting point.
Incorrect voltage setting
Setting the voltage too high or too low can result in improper penetration, excessive spatter, or weak welds. Adjust the voltage according to the material thickness and welding parameters recommended for your specific welder.
Inadequate preparation
Failing to clean and prepare the workpiece properly can lead to weak welds and contamination. Remove any rust, paint, or debris from the surfaces you plan to weld to ensure proper fusion.
Lack of proper technique
Welding requires proper technique and control. Avoid moving too quickly or too slowly, and ensure a consistent arc length and travel speed. Practice and focus on maintaining proper technique to achieve better weld results.
Insufficient heat input
Insufficient heat input can result in poor penetration and weak welds. Ensure that the weld puddle is adequately heated by adjusting the wire feed speed, voltage, and travel speed as needed.
Ignoring safety precautions
Welding can be hazardous, so always prioritize safety. Failure to wear appropriate protective gear
Remember, practice makes perfect, so don’t be discouraged if your initial welds don’t meet your expectations. With time and practice, you will improve your welding skills and produce better results.
Conclusion
The no gas MIG welder, also known as a flux-cored welder, is a cost-effective and versatile tool that is perfect for beginners. By eliminating the need for gas cylinders, it offers a more budget-friendly option for welding. Its portability and ease of use make it ideal for those starting out on their welding journey. Despite its simplicity, this welder is capable of producing high-quality welds on a variety of materials. When choosing a no gas MIG welder, it’s important to consider factors such as power output, wire feed speed control, voltage control, and duty cycle. Overall, the no gas MIG welder provides beginners with an accessible and efficient way to explore the world of welding.