When it comes to welding, there are various methods to choose from, each with its own unique advantages and disadvantages. MIG welding vs stick welding are two popular options that are widely used in the industry. Understanding the differences between these two techniques is crucial for welding experts to determine the most suitable method for their specific projects. This comprehensive comparison will delve into the intricacies of MIG welding vs stick welding, exploring factors such as versatility, ease of use, speed, and quality of welds. Whether you are a seasoned professional or a welding enthusiast looking to expand your knowledge, read on to discover which welding technique reigns supreme.
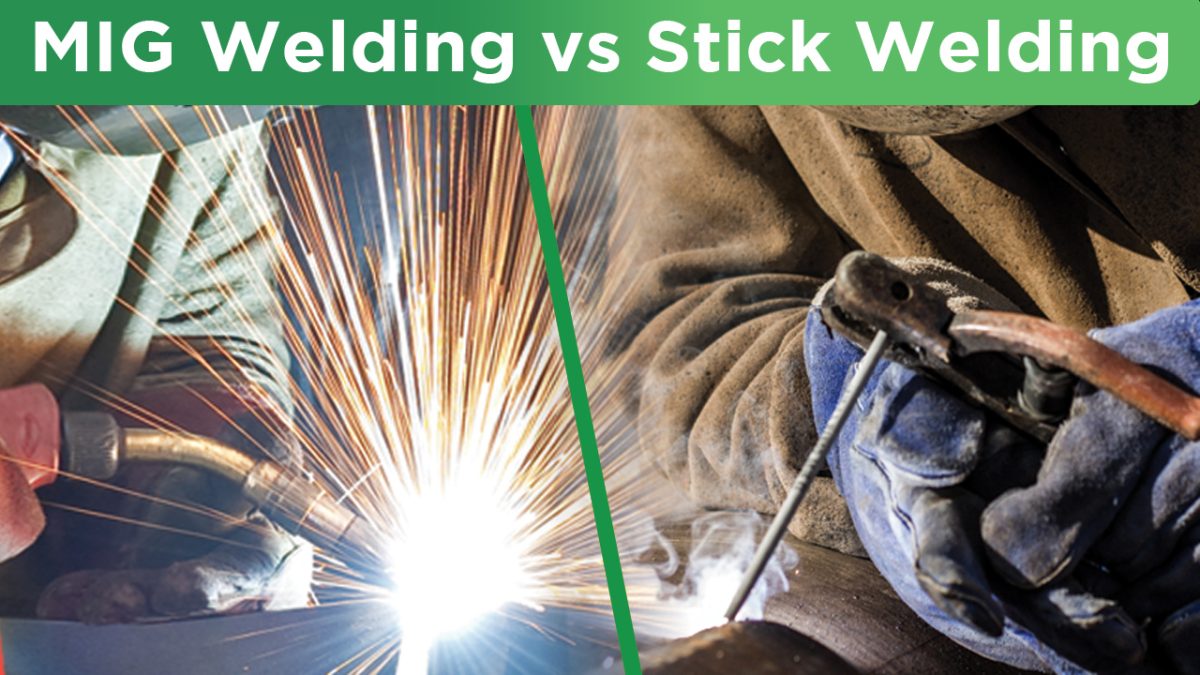
Advantages and disadvantages of MIG welding
MIG welding, also known as Gas Metal Arc Welding (GMAW), is renowned for its versatility and ease of use. It involves using a wire electrode that is continuously fed through a welding gun, along with a shielding gas to protect the weld from oxidation and other contaminants.
One of the main advantages of MIG welding is its ability to produce high-quality welds. The process allows for better control over parameters such as heat input, weld penetration, and bead appearance. This makes it ideal for applications that require strong, clean welds, such as automotive manufacturing and structural fabrication.
MIG welding offers faster welding speed compared to stick welding. The continuous wire feed eliminates the need to stop and change electrodes, resulting in increased productivity.
However, MIG welding does have some drawbacks. The equipment for MIG welding can be quite expensive, and the process may require a constant supply of shielding gas. MIG welding tends to be less forgiving when it comes to welding dirty or rusty materials.
Advantages and disadvantages of stick welding
Stick welding, also known as Shielded Metal Arc Welding (SMAW), is a widely used welding technique that has been in existence for decades. It involves using a consumable electrode coated in flux that melts to form a protective gas shield around the weld. This process is known for its simplicity and versatility.
One of the main advantages of stick welding is its portability. The equipment is lightweight and requires minimal power, making it suitable for remote locations and outdoor projects. Its versatility allows it to be used on various materials, including steel, stainless steel, cast iron, and even non-ferrous metals.
Another advantage of stick welding is its ability to penetrate thick materials. The deep weld penetration capability makes it an excellent choice for heavy-duty applications such as construction, shipbuilding, and pipeline welding.
However, stick welding does have its limitations. The welding process produces a lot of smoke, fumes, and slag, which can make it potentially hazardous if proper ventilation is not provided. Additionally, it requires a significant amount of skill and experience to achieve high-quality welds consistently.
The key factors to consider when choosing between MIG welding vs stick welding
When deciding between MIG welding vs stick welding, there are several key factors to consider. These factors will help you make an informed decision based on your specific needs and budget.
Firstly, let’s talk about cost. MIG welding equipment tends to be more expensive upfront compared to stick welding equipment. The cost of MIG welders, gas cylinders, and other accessories can add up quickly. On the other hand, stick welding equipment is generally more affordable and accessible, making it a budget-friendly option.
Secondly, equipment requirements should be taken into account. MIG welding requires a constant voltage power source, a shielding gas, and a wire feeder. This means you will need to have access to electricity and gas supply, which may not always be possible in remote locations. Stick welding, on the other hand, only requires a power source and the stick electrodes, making it more versatile and suitable for outdoor projects.
Skillset required for each welding technique
Another important aspect to consider when comparing MIG welding vs stick welding is the skillset required for each technique. While both techniques require practice and experience to master, there are some key differences in the skills needed.
MIG welding, also known as Gas Metal Arc Welding (GMAW), is generally considered easier to learn for beginners. With the automatic wire feed and continuous welding process, it offers a more forgiving and user-friendly experience. This makes it an ideal choice for those who are new to welding or looking for a more efficient and faster welding method.
On the other hand, stick welding, also known as Shielded Metal Arc Welding (SMAW), requires a higher level of skill and technique. It involves manually striking an electrode against the workpiece, creating an arc that melts the electrode and fuses the metals together. This process requires precise control of the electrode angle, arc length, and movement speed. While it can be more challenging to master, stick welding offers a greater level of control over the welding process, allowing for more customization and adaptability in various welding situations.
Ultimately, the skillset required for each welding technique depends on your level of experience, the complexity of the project, and your personal preferences. Whether you lean towards the simplicity of MIG welding or enjoy the artistry of stick welding, both techniques offer unique learning opportunities for welding enthusiasts.
Cost comparison of MIG welding vs stick welding
When it comes to welding, cost is an important factor to consider. Understanding the cost implications of MIG welding and stick welding can help you make an informed decision for your projects.
MIG welding typically requires more initial investment compared to stick welding. MIG welding machines are generally more expensive due to the additional components required, such as the wire feeder and shielding gas system. The cost of the consumables, such as the wire and shielding gas, also adds up over time.
On the other hand, stick welding has a lower initial investment cost. The welding machines for stick welding are usually more affordable, and the electrodes used are relatively inexpensive. This makes stick welding a more budget-friendly option, especially for hobbyists or those on a tight budget.
However, it is important to note that the overall cost of welding goes beyond the initial investment. Factors such as efficiency, productivity, and long-term durability should also be considered. MIG welding, with its faster and continuous welding process, can result in higher productivity and lower labor costs in certain situations. Stick welding, on the other hand, may require more time to complete a weld, resulting in higher labor costs for large-scale projects.
Ultimately, the cost comparison between MIG welding and stick welding depends on the specific requirements of your projects and your long-term goals. Analyzing your budget, the scale of your projects, and the anticipated productivity can help you determine which welding technique offers the best value for your needs.
Applications best suited for MIG welding
MIG welding, also known as Gas Metal Arc Welding (GMAW), is widely regarded as the preferred method for a variety of applications. One of the key advantages of MIG welding is its versatility across different materials and thicknesses.
MIG welding is highly suitable for light to medium thickness materials, making it ideal for projects involving automotive, sheet metal fabrication, and general metal repairs. The precise and controlled heat input of MIG welding allows for clean and aesthetically pleasing welds, making it a popular choice for cosmetic applications.
Additionally, MIG welding offers excellent control over the welding process, enabling welders to easily adjust the heat input and wire feed speed. This control allows for better weld penetration, ensuring stronger and more durable welds.
MIG welding is also well-suited for creating quick and efficient welds, making it ideal for high-volume production environments. The continuous wire feed and high welding speeds of MIG welding contribute to its efficiency, resulting in higher productivity for large-scale projects.
Applications best suited for stick welding
While MIG welding offers versatility and precise control, stick welding, also known as Shielded Metal Arc Welding (SMAW), has its own advantages that make it the preferred method for certain projects. Stick welding is commonly used in heavy-duty applications that involve thick materials such as structural steel, pipelines, and industrial fabrication. Its ability to handle thick and dirty materials, including rust and paint, makes it an excellent choice for outdoor and on-site welding.
Moreover, stick welding is known for its durability and reliability. It can withstand harsh weather conditions and extreme environments, making it suitable for welding in remote and challenging locations where other methods may not be feasible. Another benefit of stick welding is its portability. With no need for a shielding gas, stick welding equipment is more compact and portable, allowing welders to work in tight spaces or in areas with limited accessibility.
Choosing the right welding technique for your specific needs
Both MIG welding and stick welding have their own advantages and are suited for different applications. While MIG welding offers versatility and precise control, stick welding excels in heavy-duty applications involving thick and dirty materials. It is durable, reliable, and can withstand extreme environments, making it ideal for welding in challenging locations.
When choosing the Proper welding technique for your specific needs, it is important to consider factors such as the material thickness, environmental conditions, and portability requirements. Assessing these factors will help you determine which method is best suited for your project.