Mig welding sheet metal requires precision and control to prevent warping or burn-through. A thin wire and low heat settings are essential.
Mig welding, also known as Gas Metal Arc Welding (GMAW), is a popular method for welding sheet metal due to its speed and versatility. It uses a continuous solid wire electrode heated and fed into the weld pool from a welding gun.
Shielding gas, typically a mix of argon and carbon dioxide, protects the weld from contamination. Proper technique is crucial to avoid common issues like warping or burn-through. Using the right settings and tools, such as a thin wire and appropriate heat levels, ensures strong, clean welds. Mig welding is ideal for automotive, construction, and various DIY projects involving sheet metal.
Introduction To Mig Welding
MIG welding stands for Metal Inert Gas welding. It is a type of welding that uses a continuous wire feed. This makes it easier to weld thin sheet metal. MIG welding is popular for its simplicity and speed. It is also known as Gas Metal Arc Welding (GMAW).
Basics Of Mig Welding
The MIG welding process involves feeding a wire electrode through a welding gun. This wire melts and joins the metal pieces together. The welding gun also releases a shielding gas. This gas protects the weld from contaminants in the air.
- Power source: Provides the electric current.
- Wire feeder: Feeds the wire to the welding gun.
- Welding gun: Directs the wire and gas to the weld area.
- Shielding gas: Protects the weld from oxidation and contamination.
Advantages Of Mig Welding
MIG welding offers many benefits, especially for sheet metal work. Here are some key advantages:
Advantage | Description |
---|---|
Ease of Use | MIG welding is easy to learn, even for beginners. |
Speed | It is faster than many other welding techniques. |
Clean Welds | The shielding gas creates cleaner and stronger welds. |
Versatility | Suitable for welding different types of metals. |
MIG welding is ideal for both professional and hobbyist welders. It provides a combination of strength, speed, and ease of use.
Essential Tools And Equipment
Before starting with MIG welding sheet metal, gather the right tools and equipment. This ensures safety and effectiveness. Below, we outline the essential items needed for MIG welding sheet metal.
Welding Machine Selection
Choosing the right welding machine is crucial for successful MIG welding. Consider the following factors:
- Power Output: Ensure the machine has adjustable power settings.
- Wire Feed Speed: Look for machines with variable wire feed speed controls.
- Portability: A lightweight and portable machine can be beneficial.
- Brand Reputation: Opt for reputable brands known for reliability.
Machine Feature | Description |
---|---|
Power Output | Adjustable power settings for different metal thicknesses. |
Wire Feed Speed | Variable speed controls for precise welding. |
Portability | Lightweight and easy to move around. |
Brand Reputation | Choose brands known for their reliability. |
Protective Gear
Safety is paramount in MIG welding. Always wear the right protective gear:
- Welding Helmet: Protects your eyes and face from sparks and UV rays.
- Welding Gloves: Shields your hands from heat and splatter.
- Fire-Resistant Clothing: Wear long sleeves and pants made of fire-resistant materials.
- Safety Glasses: Wear under the helmet for added eye protection.
- Respirator Mask: Prevent inhalation of harmful fumes.
Ensuring you have the correct gear will keep you safe while welding.
Preparing The Sheet Metal
Proper preparation is crucial for successful MIG welding of sheet metal. This stage ensures a clean, precise, and strong weld. Follow these steps to make sure your sheet metal is ready for welding.
Cleaning The Surface
Before welding, the surface must be free of dirt, oil, and rust. Use a wire brush or grinder to clean the metal. Clean metal leads to better welds. Wipe the surface with acetone or a similar solvent. This removes any remaining contaminants.
For stubborn rust, consider using a chemical rust remover. Always wear protective gloves and work in a well-ventilated area. A clean surface prevents weld contamination and ensures a stronger bond.
Cutting And Shaping
Once the surface is clean, the next step is to cut and shape the metal. Use a plasma cutter, tin snips, or a metal saw. Ensure precise cuts for a better fit and cleaner welds.
Tool | Best For | Safety Tips |
---|---|---|
Plasma Cutter | Thick Metal | Wear gloves and eye protection. |
Tin Snips | Thin Metal | Use a firm grip and cut slowly. |
Metal Saw | Large Sheets | Secure metal before cutting. |
Once cut, use a file or grinder to smooth the edges. This will prevent injuries and ensure a better weld. Accurate shaping is key for a seamless welding process.
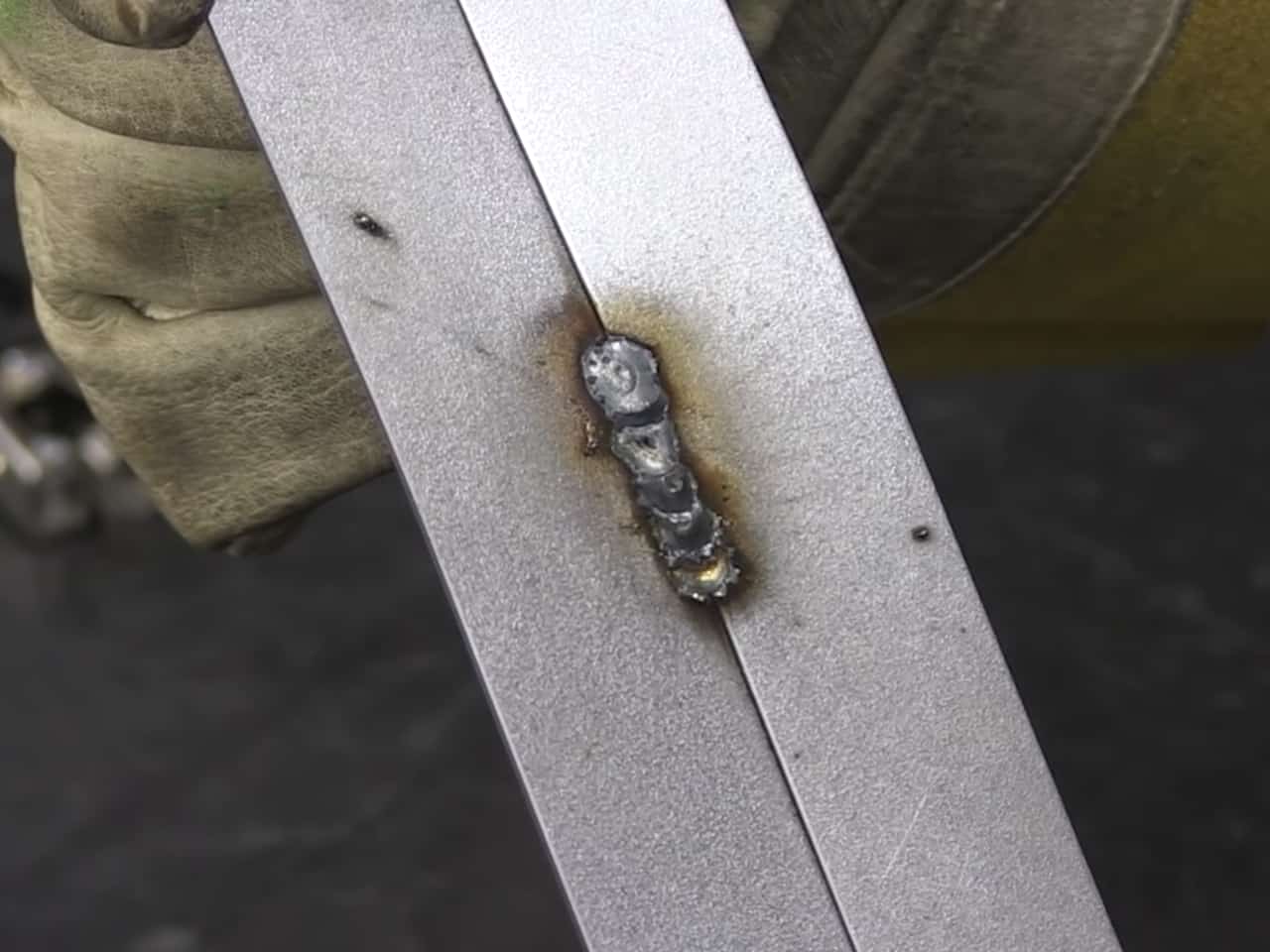
Credit: weldguru.com
Setting Up Your Welding Machine
Setting up your welding machine is a crucial step in MIG welding sheet metal. Proper setup ensures clean and strong welds. Follow these steps to get your machine ready for welding.
Adjusting Voltage And Amperage
Adjusting the voltage and amperage is essential for a successful weld. Voltage controls the arc length, while amperage affects the heat input.
- Set the voltage according to the thickness of the sheet metal.
- Thicker metals require higher voltage.
- Adjust amperage to control the weld penetration.
- Check the machine’s manual for recommended settings.
For example:
Metal Thickness (inches) | Voltage (V) | Amperage (A) |
---|---|---|
0.025 | 14-16 | 30-50 |
0.125 | 18-20 | 100-130 |
Choosing The Right Wire Feed Speed
The wire feed speed is another critical setting. It controls the rate at which the wire is fed into the weld pool.
- Set the wire feed speed based on the metal thickness.
- Thicker metals require a higher wire feed speed.
- Ensure the speed matches the voltage and amperage settings.
Here is a guide:
Metal Thickness (inches) | Wire Feed Speed (ipm) |
---|---|
0.025 | 200-300 |
0.125 | 400-500 |
Remember to adjust settings as needed. Proper setup ensures a clean, strong weld on sheet metal. Happy welding!
Techniques For Perfect Welds
MIG welding sheet metal requires skill and precision. Mastering these techniques ensures strong and clean welds. This section covers key methods to achieve perfection.
Maintaining Proper Distance
Keep the welding gun at a consistent distance. The ideal distance is about 1/4 inch from the workpiece. This allows for proper penetration and stable arc.
Too close, and the weld pool becomes unstable. Too far, and the arc loses focus, causing weak welds.
Distance | Effect |
---|---|
Too Close | Unstable weld pool |
Too Far | Weak welds |
Optimal (1/4 inch) | Strong, clean welds |
Using The Right Angle
The angle of the welding gun impacts the weld quality. Aim for a 90-degree angle to the workpiece. This ensures even penetration and a flat weld bead.
For fillet welds, use a 45-degree angle between the two pieces. This creates a strong joint with good fusion.
Key Angles:
- 90 degrees: Flat welds on sheet metal
- 45 degrees: Strong fillet welds
Consistent angles prevent common welding issues. Practice maintaining these angles for the best results.
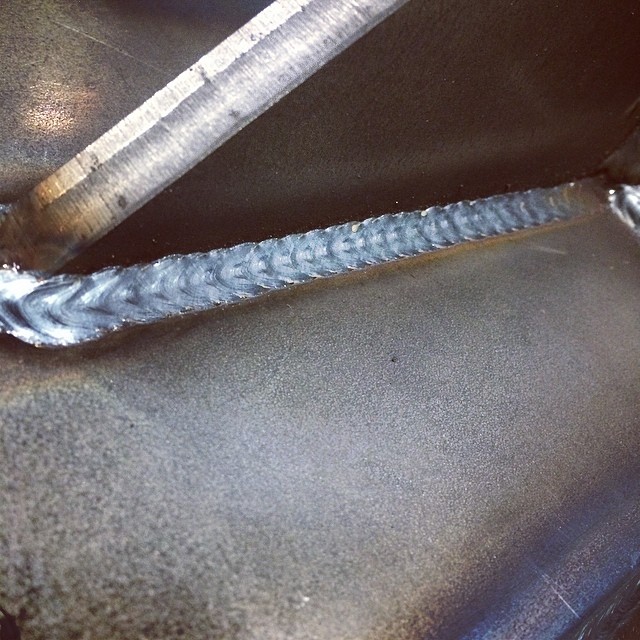
Credit: garage.grumpysperformance.com
Avoiding Common Mistakes
Mig Welding Sheet Metal can be tricky. Many welders make common mistakes. These mistakes can lead to poor results and wasted materials. In this section, we will explore how to avoid two common errors: warping and burn-through.
Preventing Warping
Warping is a frequent issue in Mig welding. It occurs when the metal heats unevenly. This can cause the metal to bend or twist.
Tip | Description |
---|---|
Use Short Welds | Short welds reduce heat buildup. |
Alternate Welds | Weld on opposite sides. This balances the heat. |
Clamps and Fixtures | Secure the metal in place. This prevents movement. |
Following these tips can help prevent warping and ensure a smooth weld.
Avoiding Burn-through
Burn-through happens when the metal becomes too hot. This can create holes in the sheet metal.
- Lower the Voltage: High voltage increases heat.
- Use a Faster Travel Speed: Move quickly to reduce heat concentration.
- Thicker Sheet Metal: Thicker metal is less prone to burn-through.
By following these steps, you can avoid burn-through and achieve a clean weld.
Finishing The Weld
Finishing the weld is a critical step in MIG welding sheet metal. It ensures durability and a professional appearance. This involves a few key processes: grinding and polishing, and inspecting the weld. Let’s dive into these steps in detail.
Grinding And Polishing
Grinding removes excess material from the weld. Use an angle grinder for this task.
- Wear safety goggles and gloves.
- Hold the grinder at a 20-degree angle.
- Move the grinder along the weld seam.
- Check your progress regularly.
Next, polishing smoothens the weld. It gives a shiny finish.
- Switch to a finer grit disc.
- Polish in circular motions.
- Wipe the surface clean with a cloth.
Inspecting The Weld
Inspecting the weld ensures its strength and quality. Start with a visual check.
- Look for cracks or holes.
- Ensure the weld is even.
- Check for discoloration.
Next, perform a structural inspection. This confirms the weld’s integrity.
- Tap the weld with a hammer.
- Listen for any unusual sounds.
- Check for any loose sections.
If you notice any issues, re-weld the affected areas. Always ensure your welds are solid and smooth.

Credit: www.minifaber.com
Safety Tips For Mig Welding
MIG welding sheet metal requires precision and attention. Safety is a crucial aspect that cannot be overlooked. Whether you’re a beginner or an experienced welder, following the right safety tips ensures a smooth and safe welding experience. Below are some essential safety tips for MIG welding.
Fire Prevention
Fire prevention is a critical part of MIG welding. Sparks and heat are always present. Here’s how to prevent fire hazards:
- Keep the work area clean and free of flammable materials.
- Use a fire extinguisher nearby for emergency situations.
- Wear flame-resistant clothing to protect yourself from sparks.
- Inspect the welding area for any combustible items before starting.
Proper Ventilation
Proper ventilation ensures that harmful fumes do not accumulate. This is crucial for your health and safety.
- Work in a well-ventilated area to avoid inhaling toxic fumes.
- Use exhaust fans to direct fumes away from your breathing zone.
- Wear a respirator if you’re working in confined spaces.
- Check the ventilation system regularly to ensure it’s functioning well.
Frequently Asked Questions
What Is Mig Welding?
MIG welding is a process using a wire electrode fed through a welding gun. It creates a strong, clean weld. It is ideal for sheet metal.
How To Set Up Mig Welder?
Set up involves connecting the gas supply and adjusting voltage and wire speed. Ensure all safety precautions are followed.
What Gas Is Used For Mig Welding?
Common gases include argon, CO2, or a mix. The choice depends on the material being welded.
Why Is Sheet Metal Welding Challenging?
Sheet metal welding is challenging due to its thinness. It requires precise control to avoid warping or burning through.
Conclusion
Mastering MIG welding for sheet metal can enhance your project quality and efficiency. Remember to prioritize safety and practice consistently. With the right techniques, you can achieve professional results. Keep honing your skills and stay updated with the latest welding tips.
This will ensure your projects are always top-notch.