Are you frustrated with the challenges of MIG welding? If so, you’re not alone. MIG welding, while incredibly versatile, can encounter its fair share of problems. From issues with wire feed to weld defects and irregularities, these obstacles can be a headache for both experienced and novice welders. But fear not, because in this article, we’ll be exploring some common MIG welding problems and their solutions.
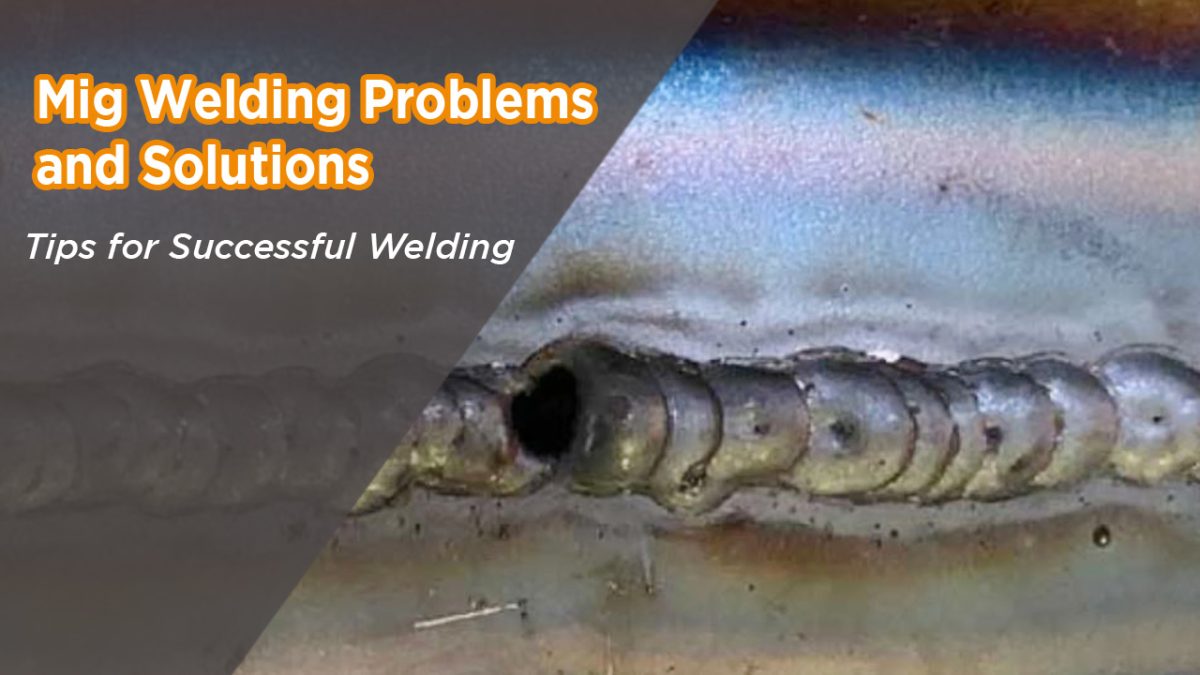
Image by basicwelding
Common MIG Welding Problems
Welding Wire Feed Issues
One of the most common problems encountered in MIG welding is related to wire feed. A steady and consistent wire feed is crucial for achieving high-quality welds. However, issues such as wire tangling, birdnesting, or erratic wire feed can occur, leading to poor welds and frustration for the welder.
There are several factors that can contribute to wire feed issues. One common culprit is improper wire tension. If the tension is too loose or too tight, it can cause problems with the wire feed. Another factor to consider is the type and condition of the welding wire being used. Low-quality or rusty wires can lead to feeding problems. Additionally, the welding gun and its components should be inspected regularly for any signs of wear or damage that could affect the wire feed.
To address wire feed issues, it’s important to ensure proper wire tension by following the manufacturer’s recommendations. Cleaning the wire before feeding it into the welder can also help prevent feeding problems. Regular maintenance of the welding gun and its components, such as replacing worn or damaged parts, can help maintain a smooth wire feed.
Poor Weld Penetration and Fusion
Achieving proper weld penetration and fusion is essential for weld strength and integrity. However, poor penetration can be a common issue in MIG welding, especially when working with thicker materials or improper welding techniques.
Several factors can contribute to poor weld penetration. Inadequate heat input, improper shielding gas flow, incorrect welding parameters, or improper joint preparation can all affect the penetration depth of the weld. Insufficient weld penetration can result in weak and brittle welds that are prone to failure.
To address poor weld penetration, it’s important to ensure proper heat input by adjusting the welding parameters according to the material thickness. Adequate shielding gas flow is crucial to protect the weld pool from atmospheric contamination and ensure proper fusion. Proper joint preparation, including cleaning and beveling, can also improve weld penetration. Additionally, using the correct welding technique, such as maintaining the right travel speed and angle, can help achieve adequate penetration.
Excessive Spatter During Welding
Excessive spatter, the small molten metal particles that can splatter onto the workpiece during welding, is another common problem in MIG welding. Spatter can not only create a messy work environment but can also lead to poor weld appearance and reduced weld quality.
Several factors can contribute to excessive spatter. Improper shielding gas flow or composition, incorrect wire stick-out, and high welding current are some of the common culprits. Inadequate cleaning of the workpiece, such as the presence of rust, oil, or paint, can also increase the likelihood of spatter.
To reduce excessive spatter, it’s important to ensure proper shielding gas flow and composition. Adjusting the wire stick-out, which is the distance between the contact tip of the welding gun and the workpiece, can also help minimize spatter. Controlling the welding current within the recommended range and properly cleaning the workpiece before welding can further reduce spatter. Additionally, using an anti-spatter spray or gel on the workpiece can help prevent spatter from sticking.
Inconsistent Weld Bead Appearance
Achieving a consistent and aesthetically pleasing weld bead appearance is important for both visual appeal and weld quality. Inconsistencies in the weld bead, such as uneven width, height, or shape, can occur in MIG welding.
Several factors can contribute to inconsistent weld bead appearance. Inconsistent travel speed, improper wire feed speed, and incorrect welding parameters, such as voltage and amperage, can all affect the appearance of the weld bead. Improper technique, such as erratic gun movement or improper gun angle, can also result in inconsistent bead appearance.
To achieve a consistent weld bead appearance, it’s important to maintain a steady and consistent travel speed throughout the welding process. Adjusting the wire feed speed to match the welding parameters and material thickness can help achieve a uniform weld bead. Ensuring proper technique, such as maintaining a steady gun movement and the correct gun angle, can also improve the bead appearance. Regularly inspecting and cleaning the contact tip of the welding gun can further prevent any inconsistencies.
Welding Defects and Imperfections
Despite the best efforts, welding defects and imperfections can still occur in MIG welding. These can include weld discontinuities such as porosity, undercutting, lack of fusion, or weld cracks. These defects not only compromise the structural integrity of the weld but can also lead to potential failures in the future.
Several factors can contribute to welding defects and imperfections. Inadequate shielding gas coverage, incorrect welding parameters, improper joint preparation, or contamination of the weld area are some common causes. Insufficient cleaning of the workpiece, such as the presence of oil, grease, or dirt, can also lead to welding defects.
To prevent welding defects, it’s important to ensure proper shielding gas coverage by correctly setting the flow rate and using the appropriate gas mix for the material being welded. Adjusting the welding parameters, such as voltage, amperage, and travel speed, according to the material thickness can also help minimize defects. Proper joint preparation, including cleaning and beveling, can improve weld quality and reduce the risk of defects. Thoroughly cleaning the workpiece before welding and protecting the weld area from contamination are also crucial steps in preventing welding defects.
Solutions to MIG Welding Problems
Troubleshooting MIG Welding Issues
When faced with MIG welding problems, troubleshooting is an essential skill that can help identify the root causes and find effective solutions. Some common troubleshooting techniques include:
Inspecting Equipment: Regularly inspecting the welding machine, welding gun, and their components can help identify any potential issues that may be affecting the weld quality. Look out for signs of wear, damage, or loose connections that may need to be addressed.
Checking Welding Parameters: Ensure that the welding parameters, such as voltage, amperage, wire feed speed, and gas flow, are correctly set according to the material thickness and welding technique being used. Adjustments may be needed to achieve optimal weld quality.
Reviewing Technique: Evaluate your welding technique, including gun angle, travel speed, and gun movement. Make adjustments as necessary to ensure a consistent and proper weld.
Inspecting Welds: Regularly inspect the finished welds for any signs of defects or imperfections. This can help identify any ongoing issues that may need to be addressed.
By following these troubleshooting techniques and addressing any underlying issues, you can overcome common MIG welding problems and achieve high-quality, flawless welds. Remember, practice and experience are key to improving your welding skills, so don’t get discouraged if you encounter challenges along the way. With the right knowledge and perseverance, you can become a proficient MIG welder.
Conclusion
MIG welding can be a rewarding and versatile welding process, but it’s not without its challenges. From wire feed issues to poor weld penetration, excessive spatter, inconsistent weld bead appearance, and welding defects, there are several common problems that welders may encounter. However, armed with the knowledge of the root causes and troubleshooting techniques, you can effectively address these issues and achieve high-quality welds.
Remember to maintain proper wire tension, adjust welding parameters, ensure adequate shielding gas flow, and practice good welding technique. Regularly inspect and clean your equipment, and don’t forget to prepare your workpiece properly. By following these tips and techniques, you can overcome MIG welding problems and take your welding skills to the next level. So, don’t let the challenges deter you. Embrace them as opportunities for growth and improvement.