MIG welding is a versatile and popular welding technique used in various industries. But can you MIG weld galvanized steel? This question often arises due to the unique characteristics of galvanized steel. In this article, we will explore this topic and provide you with all the information you need to know.
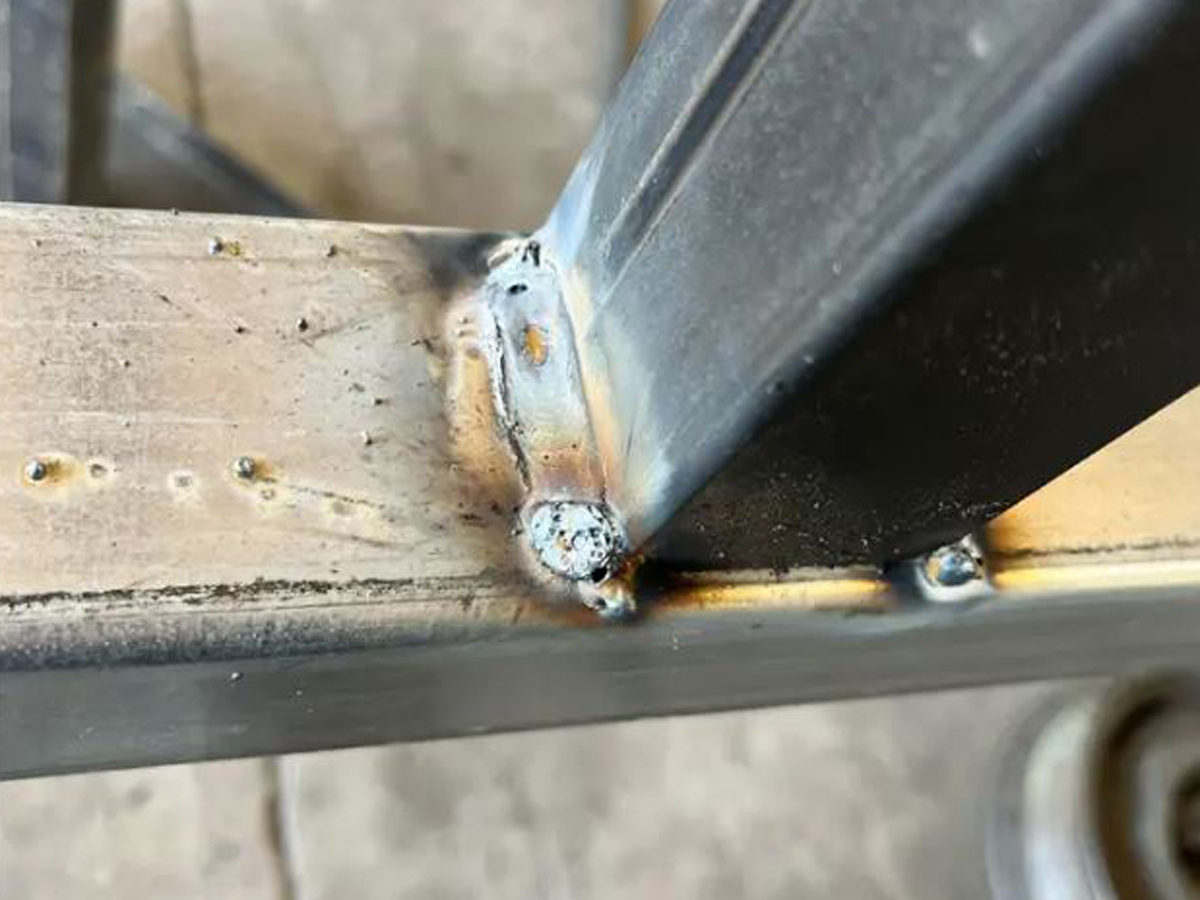
Image: reddit/Welding
What is galvanized steel?
Galvanized steel is steel that has been coated with a layer of zinc to protect it from corrosion. This process involves immersing the steel in a bath of molten zinc or by electroplating it with a thin layer of zinc. The zinc coating acts as a sacrificial layer, offering protection to the underlying steel substrate. Galvanized steel is commonly used in outdoor applications, such as fences, roofing, and structural components, where corrosion resistance is essential.
Challenges of welding galvanized steel
Welding galvanized steel presents several challenges that need to be addressed to ensure a successful weld. One of the main challenges is the release of toxic fumes when the zinc coating is heated. These fumes can cause health hazards, such as metal fume fever, which is characterized by flu-like symptoms. Additionally, the zinc coating can interfere with the welding process, resulting in a weaker and less durable weld. Therefore, it is crucial to take proper precautions and follow specific welding techniques when working with galvanized steel.
Can you MIG weld galvanized steel?
Yes, you can MIG weld galvanized steel, but it requires some additional steps and precautions. The primary concern when welding galvanized steel is the release of zinc fumes, which can be harmful if inhaled. To ensure your safety, it is essential to work in a well-ventilated area or use local exhaust ventilation to remove the fumes from the welding zone. Proper respiratory protection, such as a respirator with an appropriate filter, should also be worn to prevent inhalation of the fumes.
Preparing galvanized steel for MIG welding
Before you start MIG welding galvanized steel, it is crucial to properly prepare the material. The first step is to remove the zinc coating from the area to be welded. This can be done using a wire brush or grinding wheel, making sure to remove any residue or contaminants. Cleaning the surface of the galvanized steel is essential to ensure good weld quality. It is also recommended to pre-heat the material before welding to minimize the cooling effect of the zinc coating.
Safety precautions when MIG welding galvanized steel
Safety should always be your top priority when working with any welding process, including MIG welding galvanized steel. In addition to proper ventilation and respiratory protection, here are some additional safety precautions to consider:
- Use eye protection: Welding produces intense light and UV radiation, so wearing a welding helmet or goggles with the appropriate shade is essential to protect your eyes.
- Wear protective clothing: Cover exposed skin with flame-resistant clothing to protect against sparks, splatter, and UV radiation.
- Use welding gloves and boots: Protect your hands and feet from burns and sparks by wearing appropriate gloves and boots.
- Keep a fire extinguisher nearby: In case of a fire, having a fire extinguisher within reach can help prevent further damage and injuries.
- Follow proper electrical safety measures: Make sure your welding equipment is properly grounded, and follow all electrical safety guidelines to avoid electrical shocks.
MIG welding techniques for galvanized steel
When MIG welding galvanized steel, there are a few techniques that can help you achieve better results:
- Use the right shielding gas: Carbon dioxide (CO2) or a mix of CO2 and argon is commonly used as the shielding gas for MIG welding galvanized steel. This gas combination helps reduce spatter and produce a cleaner weld.
- Adjust the voltage and wire feed speed: Galvanized steel requires higher voltage and wire feed speed settings compared to uncoated steel. Experimentation and practice are key to finding the optimal settings for your specific welding setup.
- Use a shorter arc length: A shorter arc length helps reduce heat input and minimizes the chances of burning through the thin zinc coating.
- Employ proper technique: Maintain a steady travel speed, use a push technique, and ensure good joint fit-up to achieve a strong and consistent weld.
Common issues and troubleshooting when MIG welding galvanized steel
Despite taking all the necessary precautions, you may encounter some common issues when MIG welding galvanized steel. Here are a few problems you might face and some troubleshooting tips:
- Excessive spatter: Excessive spatter can occur when welding galvanized steel due to the presence of the zinc coating. To minimize spatter, reduce the wire feed speed or adjust the voltage settings. Using an anti-spatter spray can also help.
- Porosity: Porosity, or the presence of small holes or voids in the weld, can be caused by trapped moisture or contaminants. Ensure that the galvanized steel is properly cleaned and dried before welding.
- Brittle welds: Brittle welds can occur when the zinc coating is not adequately removed, resulting in poor fusion between the base metal and the weld. Make sure to remove the zinc coating thoroughly and use appropriate welding techniques to achieve a strong and durable weld.
Alternatives to MIG welding for galvanized steel
While MIG welding is commonly used for galvanized steel, there are alternative welding processes that can be used, depending on the specific application and requirements. Some alternatives include:
- Flux-cored arc welding (FCAW): FCAW is a welding process that uses a hollow wire electrode with flux inside. This process can provide higher deposition rates and deeper penetration compared to MIG welding, making it suitable for thicker galvanized steel.
- Stick welding (SMAW): Stick welding is a versatile welding process that can be used for welding galvanized steel. It requires a flux-coated electrode that provides shielding and helps remove the zinc coating during the welding process.
- TIG welding (GTAW): TIG welding can also be used for welding galvanized steel, especially for intricate and precise welds. This process uses a non-consumable tungsten electrode and requires the use of a shielding gas.
Tips for successful MIG welding on galvanized steel
To achieve successful MIG welding on galvanized steel, here are some additional tips to keep in mind:
- Practice on scrap material: Before welding on your actual project, practice on scrap galvanized steel to familiarize yourself with the welding process and optimize your technique.
- Use the right consumables: Select welding consumables, such as electrodes and filler wires, specifically designed for welding galvanized steel. These consumables are formulated to provide better adhesion and minimize the effects of the zinc coating.
- Monitor the zinc coating thickness: The thickness of the zinc coating can vary, so it is essential to monitor it and adjust your welding parameters accordingly.
- Perform post-weld cleaning: After welding, it is crucial to remove any slag, spatter, or other contaminants from the weld. This can be done using a wire brush or grinding wheel.
- Inspect the weld: After completing the weld, thoroughly inspect it for any defects or imperfections. This includes checking for proper fusion, absence of porosity, and overall weld quality.
Conclusion
MIG welding galvanized steel is possible, but it requires additional precautions and techniques due to the unique characteristics of galvanized steel. Proper ventilation, cleaning, and selection of suitable consumables are crucial to achieve a strong and durable weld. By following the safety precautions and welding techniques outlined in this article, you can successfully MIG weld galvanized steel and ensure both your safety and the quality of your weld. Remember to always prioritize safety and take the necessary steps to protect yourself and those around you when working with galvanized steel.