Mig welding is a great way to join metal parts but it can also be a nightmare. Feeding wire into the spool or clamp is one of the common problems of using a mig welder, and it doesn’t get any easier as you progress in your welding career. With so many variables involved, from feed rate to wire diameter, running a perfect mig welding setup can be challenging. Fortunately, there are some tricks to help a mig welder keeps feeding wire and avoid common issues when running a small (or big) machine shop. Follow these tips and keep your mig welder humming smoothly all day long.
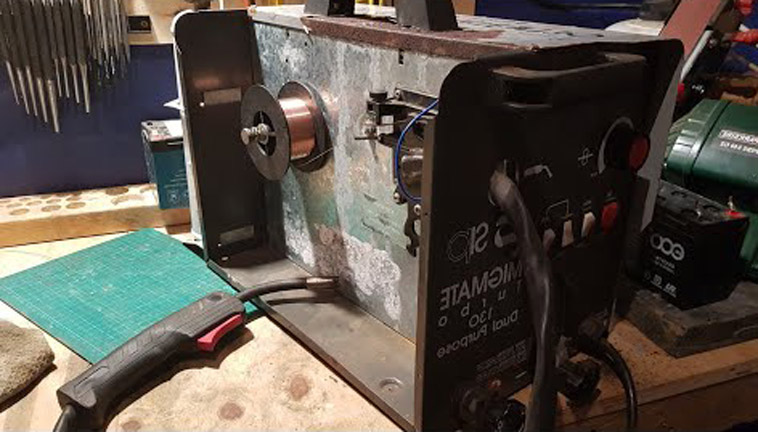
Set up your mig weffer properly
The most important step in running your mig welder is setting up the machine properly. Since you won’t be able to precisely control the welds, it’s imperative that your machine is setup correctly. Whether you are using a Fusion welder or a stick welder, the setup process is similar.
First, adjust the welding parameters to suit your needs and the material you plan to weld. This means adjusting your welding current and speed settings, as well as your weld bead size. Be mindful of the material’s characteristics when setting these parameters. For example, stainless steel’s resistance to welding is different from that of mild steel. You may also want to adjust your shielding gas parameters, if needed.
Next, you need to position your torch properly. You can either use a separate table specifically built for welding, or you can use a wooden workbench. Remember that when welding, the torch is on a constant flame. You may therefore want to create a barrier between the welding table and the rest of your workshop. This can be done by placing a few boxes or an old piece of wood.
Use the right shielding gas for mig welder keeps feeding wire
Gases used in mig welding can have a huge impact on the quality of your welds. When you are just starting out, a lower-cost argon (Ar) shielding gas is usually suitable. However, as you progress in your welding career, you are likely to want to experiment with other gases.
There are a number of factors to consider when choosing a shielding gas for mig welding, including cost, availability, weldability and toxicity. For example, argon gas is cost-effective, widely available and has low toxicity. It’s not very weldable, so you may want to consider switching to a more versatile gas such as helium or CO2.
Shielding gases are available in a range of grades, with the most common being 80% argon and 20% CO2. If you want to experiment with more exotic gases, you can purchase a welder kit that contains a mixing rig. These kits are designed to make it easy to change gas grades on the fly, as well as ensure consistent mixing between gases.
Keep torch on a constant flame
Mig welding torches are equipped with a gas valve. Most of the time, this valve is set to emit a constant flow of gas. This is important when you are welding, but it’s even more important when you are welding with a torch. One of the biggest causes of mig welding problems is when the flame goes out. This may happen if you turn off the welding torch or if the gas valve gets clogged with dust.
Whatever the cause of your flame going out, it’s important to quickly re-ignite the torch. To quickly re-ignite the flame, pull the trigger and quickly let go. This will reopen the gas valve and allow the torch to burn hot enough to weld. The torch flame should be hot enough to create a red-hot weld, although if it’s too cool, you can simply add a few puffs of air.
Check loose connections regularly for mig welder keeps feeding wire smoothly
One of the key principles of welding is that joined metal parts should be electrically isolated from the welder. Most mig welders come with a pair of fuse wires. These wires are used to prevent your welder’s electrical components from being exposed to the weld puddle. What most people don’t realise is that the fuse wires should be checked regularly. This is because they may break and cause loose sparks. If you don’t check these wires, they could lead to arcing and damaged components.
In some cases, the fuse wires may break completely, causing your mig welder to shut down completely. If this happens, it’s important to quickly diagnose the problem. A possible cause is when the welding cable breaks or comes disconnected from the welding apparatus. Another possible cause is when the shielding gas is leaking, which could be due to a faulty valve. If you find that the shielding gas is leaking, you should replace the gas valve immediately.
Check for clogged wires periodically
Since mig welders are generally used for small-scale welding, it’s important to periodically clean the wires in your mig welder. This is especially important if you have been welding for a long time or you’re welding complicated parts. You should clean the wires after welding when the torch flame has gone out, as well as before you start a new job for Mig welder keeps feeding wire. Begin by removing any wire clogs from the wires using a wire spooling brush.
Next, use a professional wire cleaning solution to flush the wires. You can also use vinegar and water to clean the wires. Do not use wire cleaners that contain acids. If you notice that the wire cleaning solution isn’t cleaning the wires properly, you may need to clean the wires with a wire brush. If this is the case, you should re-clean the wires with a wire brush before re-using the wire cleaning solution.
Final Words
Mig welding is a useful skill to have, especially if you are interested in working with metal. You should be prepared for the challenges that come with using this type of welding. If you approach your mig welding with these tips in mind, you will be well on your way to run a successful and efficient shop.