Mig weld not penetrating into the base metal are a common problem that can be challenging to fix. There are several reasons for this, including inaccurate setup procedures, incomplete penetration of the weld, and worn out equipment. If left unsolved, this issue can lead to root cause analysis failure. There are some simple fixes you can implement right now to help resolve the issue and prevent it from reoccurring in the future. Let’s take a look at how you can fix a mig weld not penetrating.
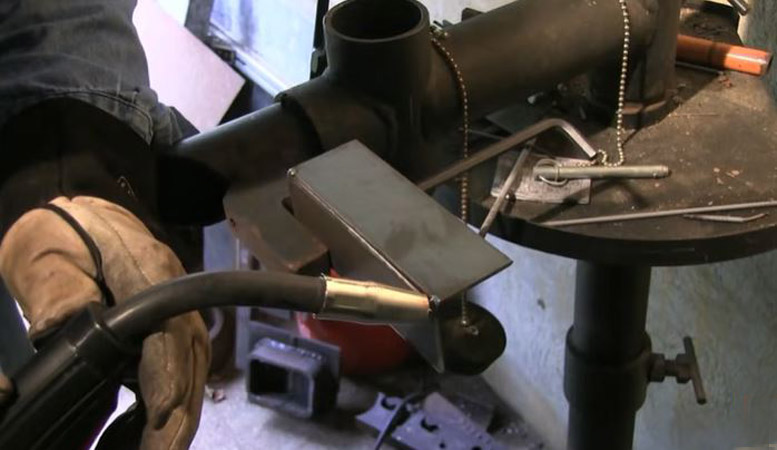
Photo by weldingtipsandtricks
Set up your mig welding correctly
Mig welds not penetrating can often be traced back to improper setup of the welding process and also use a certified good quality welder. During this phase, welders need to ensure that the amount of current, wire speed, and distance from the torch to the workpiece are correct. If anyone of these factors is off, the weld will not penetrate the base metal. While it’s important to follow the correct procedure for setting up your mig weld, this doesn’t always solve the issue of a weld not penetrating.
The root cause of a weld not penetrating is often an issue with the weld itself. So, before you change anything else, make sure your setup procedure is correct. Once that’s taken care of, you can start to troubleshoot the weld penetration issue.
Inspect for penetration issues
When you are welding a thicker material, you are going to run into issues with a mig weld not penetrating. If you are welding thinner materials, you are probably going to have issues with mig welds not penetrating. So, you will want to inspect your welds and make sure you are getting the penetration you want. If you are not getting the depth of penetration you want, you will want to check your setup procedure and make sure you are not missing something. Welds can be easily inspected with a mig welder, so you can easily inspect your welds and make sure you are getting the depth of penetration you want.
Change your process or equipment if necessary
If you are welding a thicker material and still running into issues with your mig welds penetrating, it’s possible that you are operating the equipment in the wrong setup. This could mean that you are using the incorrect thickness gauge or setting up the equipment incorrectly. The base material thickness could be too thin.
Welding thicker materials like steel or aluminum is a bit different than welding thinner materials like sheet metal. Welding thicker materials, like steel, has a much higher melting point. This means that the weld has to maintain a higher temperature. To do this, it has to be hotter and produce more heat than the base metal. This, in turn, means that you need a thicker gauge to be able to produce enough current for the welding process.
There are a few things you can do to change your process or equipment if necessary to address this penetration issue. You can use a thicker gauge, change the thickness of the base material, or change the thickness of the power source. Whatever you decide on, make sure you’re operating in the correct setup.
Maintain Equipment and Proper Welding Procedures
Once you have changed your setup or equipment, you will want to make sure you are maintaining it and following proper welding procedures. Poor welding procedures are often the root cause of the penetration issues you face. If the welding procedure is incorrect, you are not going to be able to penetrate the weld. To maintain proper welding procedures, you will want to make sure you are using the right size wire, welding at the right voltage, and using the welder with proper amperage. Keep in mind that improper wire size is often the culprit behind a mig weld not penetrating.
When welding thinner materials, you will almost always be using a smaller wire size than you would when welding thicker materials. You will want to make sure you are welding at the correct voltage, too. Many times, mig welders will weld with a higher voltage than they should. This is usually because the welding equipment is producing a higher voltage than it should be producing.
Check the quality of your welds
You will want to inspect the quality of your welds. When you are welding thicker materials, you will always want to inspect the penetration of your welds. When you are welding thinner materials, you will need to inspect other aspects as well. You will want to make sure you are getting a good bead on your welds and that the weld quality is acceptable. If you are getting a good bead on your welds, you are probably not having any issues with penetration. As far as the weld quality is concerned, you will want to inspect for incomplete penetration. If the weld is not penetrating enough, you will want to inspect for other issues.
The Final Step- Root Cause Analysis
At this point, you have taken care of the basic issues with a mig weld not penetrating. However, you may still have some issues with penetration that you need to take care of. If this is the case, you will want to finish the root cause analysis. During a root cause analysis, you will want to inspect the weld and the base material while looking for other issues that could be causing a weld not to penetrate.
At the same time, you will also want to look at each factor that could be causing the problem. After you have finished your root cause analysis, you should be able to determine the exact factor causing the problem. If necessary, you can change the setup, equipment, or procedure to solve the issue.