When it comes to MIG welding, the mig gun liner plays a crucial role in ensuring smooth and consistent wire feeding. This small, yet vital component is essentially a consumable part that guides the welding wire from the wire feeder, through the gun, and up to the contact tip. Understanding the construction and function of the mig gun liner is fundamental to appreciating its significance in the welding process. A typical mig gun liner consists of a flexible inner core made of materials such as Teflon or stainless steel, encased within a protective outer layer.
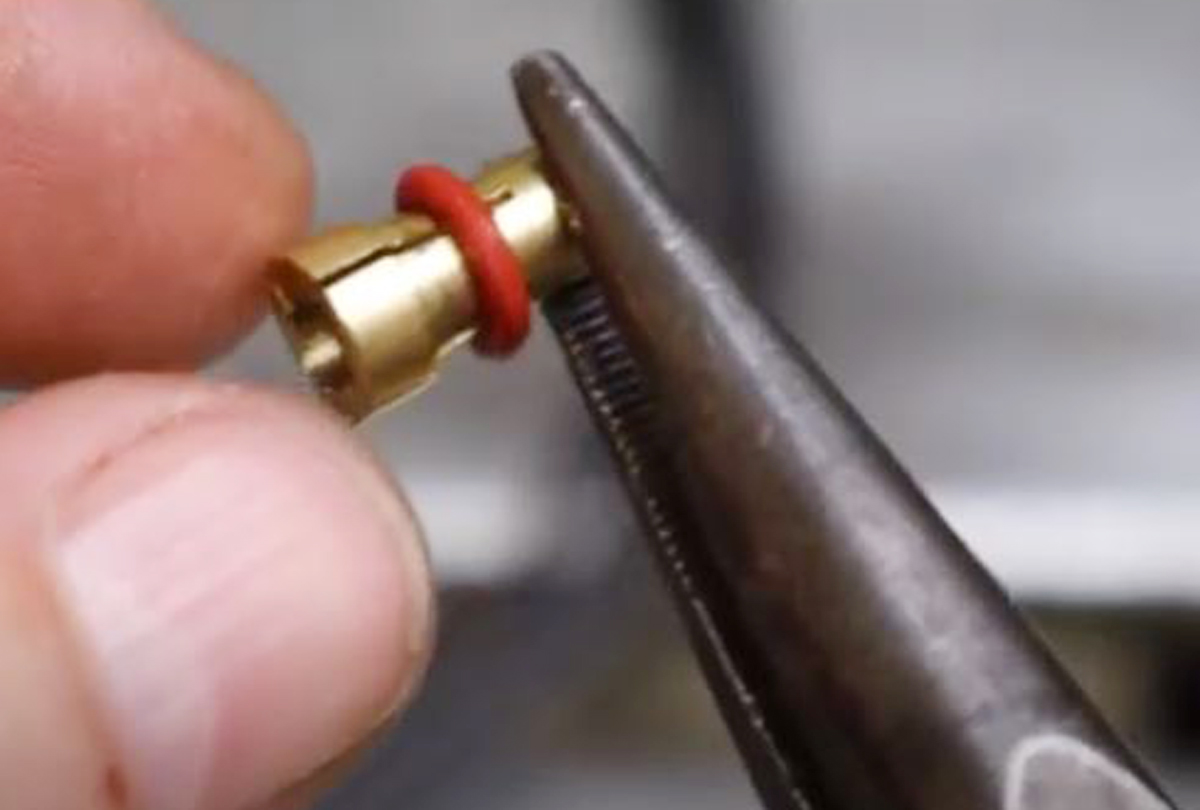
Image by DIYHomesteadProjectsDIYHP10 on YT
The inner core’s primary function is to provide a smooth, low-friction path for the welding wire to pass through, preventing kinks and snags that could impede the wire feeding process. The outer layer, often made of durable materials like nylon or polyethylene, shields the inner core from abrasion and wear caused by the constant movement of the welding wire. Together, these components ensure the seamless delivery of welding wire from the feeder to the contact tip, ultimately impacting the quality and efficiency of the welding process.
Understanding the mig gun liner’s construction and purpose sets the stage for recognizing the importance of timely replacement and maintenance to uphold optimal welding performance and longevity of the equipment.
Signs that the Mig Gun Liner Needs Replacement
Recognizing the signs indicating that a mig gun liner requires replacement is essential for maintaining peak welding performance. Some common indicators include erratic wire feeding, increased wire drag, excessive wire kinking, and visible wear or damage to the liner. Erratic wire feeding can manifest as inconsistent arc stability and weld quality, leading to frustration and compromised workmanship.
Increased wire drag, often felt as resistance when feeding the wire through the gun, is a clear sign of liner deterioration, hindering the smooth flow of the welding wire. Excessive wire kinking within the liner can obstruct the wire’s movement, causing interruptions in the welding process and potentially damaging the wire itself. Visible wear or damage to the liner, such as flattened or deformed sections, is a clear indication that replacement is necessary to restore optimal wire feeding performance.
By being attuned to these signs, welders can proactively address liner issues, ensuring uninterrupted workflow and consistent weld quality.
Steps to Replace the Mig Gun Liner
Replacing the mig gun liner is a straightforward process that can significantly enhance welding efficiency. Begin by disconnecting the MIG gun from the power source and removing the nozzle and contact tip. Next, carefully remove the existing liner from the gun, ensuring that any retaining clips or screws are safely detached. Once the old liner is removed, inspect the gun for any debris or obstructions that may have accumulated.
With the gun and liner clear of any debris, prepare the new mig gun liner by trimming it to the appropriate length, ensuring it matches the specifications of the original liner. Carefully insert the new liner into the gun, ensuring it follows the correct path and is securely fastened as per the manufacturer’s guidelines. Once the new liner is in place, reattach the contact tip, nozzle, and any other components that were removed, ensuring a snug fit.
Finally, reconnect the MIG gun to the power source, feed the welding wire through the new liner, and perform a test run to ensure smooth and consistent wire feeding. Following these steps will ensure a seamless mig gun liner replacement, optimizing the welding setup for enhanced performance.
Choosing the Right Mig Gun Liner
Selecting the appropriate mig gun liner is crucial for maintaining optimal welding performance. Factors to consider when choosing a replacement liner include the wire diameter compatibility, liner material, and overall quality. It is imperative to match the diameter of the welding wire with the corresponding liner size to facilitate smooth wire feeding and minimize friction.
Selecting a high-quality liner material, such as stainless steel or Teflon, can significantly impact the liner’s longevity and resistance to wear. Considering the welding application environment, such as the presence of abrasive particles or high temperatures, is essential in choosing a liner material that can withstand these conditions. Investing in a durable, high-quality mig gun liner ensures consistent wire feeding and prolonged equipment lifespan, ultimately contributing to superior welding outcomes.
Consulting with welding equipment experts and adhering to manufacturer recommendations can provide valuable guidance in selecting the most suitable mig gun liner for specific welding requirements.
Maintaining the Mig Gun Liner for Longevity
To prolong the lifespan and optimize the performance of the mig gun liner, regular maintenance and care are essential. Periodically inspecting the liner for signs of wear, kinks, or damage allows for timely replacement, preventing potential disruptions during welding operations. Keeping the gun and liner free of debris, spatter, and contaminants helps maintain smooth wire feeding and prevents premature wear.
Applying a small amount of high-quality liner lubricant or conditioner can further reduce friction and prolong the life of the mig gun liner. Proper storage of spare liners in a clean, dry environment protects them from environmental degradation and ensures their readiness for replacement when needed. By incorporating these maintenance practices into the welding routine, welders can optimize the longevity and reliability of their mig gun liners, ultimately enhancing overall welding productivity.
Common Mistakes to Avoid When Replacing Mig Gun Liner
When performing a mig gun liner replacement, avoiding common pitfalls is crucial to achieving successful outcomes. One common mistake is neglecting to thoroughly clean the gun and inspect it for debris or obstructions before installing the new liner. Failing to do so can lead to premature wear and interference with wire feeding, undermining the purpose of the replacement.
Additionally, overlooking the proper trimming of the new liner to match the original length can lead to feeding irregularities and liner damage. It is imperative to follow the manufacturer’s guidelines for trimming and installation to ensure optimal performance. Another mistake to avoid is using a worn or damaged liner, as this can compromise wire feeding and potentially damage the welding wire, impacting the quality of the welds.
Mig Gun Liner Replacement Tools and Equipment
Equipping oneself with the necessary tools and equipment for mig gun liner replacement is essential for a smooth and efficient process. Some essential tools include a set of precision wire cutters for trimming the new liner to the correct length, a liner reaming tool for deburring the liner’s edges, and a wire brush for cleaning the gun and components.
Having a supply of high-quality replacement mig gun liners, compatible with the specific welding wire diameter and application, ensures readiness for timely replacements. It is also beneficial to have a small amount of recommended liner lubricant or conditioner on hand to reduce friction and prolong the life of the new liner. By having these tools and equipment readily available, welders can streamline the mig gun liner replacement process and uphold optimal welding performance.
Mig Gun Liner Replacement FAQs
How often should the mig gun liner be replaced?
The frequency of mig gun liner replacement depends on factors such as the volume of welding, the type of welding wire used, and the operating conditions. Regular inspection and proactive replacement as needed are key to maintaining optimal performance.
Can I use any type of liner for my MIG gun?
It is crucial to select a mig gun liner that is compatible with the specific welding wire diameter, material, and application requirements. Using an unsuitable liner can lead to feeding issues and premature wear.
What are the benefits of using a high-quality mig gun liner?
High-quality mig gun liners offer smoother wire feeding, reduced friction, and increased resistance to wear, ultimately contributing to consistent welding performance and prolonged equipment lifespan.
Are there any maintenance tips for extending the life of the mig gun liner?
Regular inspection for wear, cleaning the gun and components, and applying recommended liner lubricant or conditioner can help prolong the life of the mig gun liner and optimize its performance.
Mig Gun Liner Replacement Troubleshooting
In the event of encountering issues after replacing the mig gun liner, troubleshooting can help identify and address potential problems. If experiencing erratic wire feeding or resistance, it is essential to inspect the liner for improper installation, kinks, or obstructions that may be impeding the wire’s movement. Additionally, ensuring that the welding wire is compatible with the liner size and material is crucial for smooth feeding.
If encountering feeding irregularities, such as bird nesting or wire slipping, adjusting the tension settings on the wire feeder and ensuring proper alignment of the components can alleviate these issues. Furthermore, consulting the equipment manual and reaching out to welding equipment specialists can provide valuable insights and solutions for troubleshooting mig gun liner replacement challenges, ensuring optimal welding performance.
Conclusion and Final Tips
In conclusion, the mig gun liner replacement is a fundamental maintenance task that significantly impacts welding efficiency and quality. Understanding the construction and function of the mig gun liner, recognizing the signs that indicate replacement, and following the proper steps for replacement are essential for maintaining optimal welding performance. Selecting the right mig gun liner, implementing maintenance practices, and avoiding common mistakes contribute to prolonged equipment lifespan and superior welding outcomes.
By equipping oneself with the necessary tools, knowledge, and maintenance practices, welders can ensure seamless mig gun liner replacement and uphold peak welding performance. Proactive inspection, timely replacement, and meticulous care of the mig gun liner are integral to achieving consistent and high-quality welds. Incorporating these best practices into the welding routine sets the foundation for an enhanced welding experience, ultimately leading to precise and professional results.