Microscopic welding is a precise technique used to join tiny components. It involves using focused energy to create strong, minuscule bonds.
Microscopic welding is crucial in various industries, particularly electronics and medical devices. This advanced technique allows for the assembly of components too small for traditional welding methods. It ensures durability and reliability in the finished product. The process often utilizes laser, electron beam, or ultrasonic energy to achieve the desired results.
Manufacturers benefit from microscopic welding as it enhances product quality and performance. As technology advances, the demand for microscopic welding continues to grow. It plays a vital role in producing miniaturized devices that are essential in modern technology.
Introduction To Microscopic Welding
Microscopic welding is a fascinating and advanced technology. It plays a crucial role in modern manufacturing. This technique allows for precise welding at a very small scale. The applications of microscopic welding are vast and varied.
Defining Microscopic Welding
Microscopic welding involves joining tiny components together. This process uses focused energy sources. These sources include lasers, electron beams, and micro-arc welders. The welds are usually less than one millimeter in size. This makes the process extremely precise.
Several industries rely on microscopic welding. These include electronics, medical devices, and aerospace. It is essential for creating small, intricate parts. This method ensures minimal thermal distortion and high accuracy.
Importance In Modern Manufacturing
The importance of microscopic welding in modern manufacturing is immense. It enables the production of smaller, more efficient devices. This is vital in the electronics industry. Devices like smartphones and microchips benefit from microscopic welding.
The medical field also uses microscopic welding. It helps create precise surgical instruments and implants. These tools must be small yet incredibly durable.
In the aerospace sector, microscopic welding is crucial. It ensures the integrity of small yet critical components. These parts must withstand extreme conditions and high stress.
Industry | Applications |
---|---|
Electronics | Smartphones, Microchips |
Medical | Surgical Instruments, Implants |
Aerospace | Critical Components |
Microscopic welding is revolutionizing manufacturing. It provides precision, durability, and efficiency. It is a key technology for future innovations.
Technological Advancements
Microscopic welding has seen remarkable technological advancements. These advancements have revolutionized industries like electronics and medicine. Small, precise welds are now achievable with new techniques and tools.
Innovative Techniques
New innovative techniques in microscopic welding have made the process more efficient. One such technique is laser welding. This method uses high-intensity light to fuse materials. It is precise and produces minimal thermal distortion.
Another technique is ultrasonic welding. This method uses high-frequency sound waves. The sound waves create frictional heat to join materials. It is ideal for bonding delicate and dissimilar materials.
Electron beam welding is also noteworthy. This technique uses a focused beam of electrons. It offers deep penetration and narrow welds. It is perfect for dense and thick materials.
Key Players In The Industry
Several companies lead the way in microscopic welding. These companies provide advanced solutions and set industry standards.
Company | Specialization |
---|---|
AMADA WELD TECH | Laser and resistance welding solutions |
Branson Ultrasonics | Ultrasonic welding and cleaning |
EB Industries | Electron beam and laser welding |
These key players invest heavily in research and development. Their innovations drive the field forward.
Applications In Various Industries
Microscopic welding has revolutionized many industries. This advanced technology enables precise and strong welds at a microscopic level. Here, we will explore its applications in various fields.
Electronics And Microchips
Microscopic welding is crucial in the electronics industry. Manufacturers use it to create compact and efficient microchips. These chips are essential for computers, smartphones, and other electronic devices.
Application | Benefits |
---|---|
Microchip Assembly | Enhances durability and performance |
Sensor Manufacturing | Improves accuracy and reliability |
PCB Production | Reduces size and increases efficiency |
Microscopic welding ensures connections are robust and long-lasting. This method helps create smaller and more powerful devices. The precision of microscopic welding also reduces waste and improves overall product quality.
Medical Devices And Implants
Microscopic welding is vital in the medical field. It creates precise and reliable connections for medical devices and implants. These components must function perfectly to ensure patient safety and health.
- Pacemakers: Ensures secure connections for reliable heart rhythm management
- Hearing Aids: Produces compact and durable devices for improved hearing
- Implants: Provides strong and biocompatible joints for long-term use
Microscopic welding helps in the production of life-saving devices. It also guarantees that implants are safe and effective over time. Precision and strength are crucial in medical applications, making microscopic welding indispensable.
In summary, microscopic welding has diverse applications across various industries. Its precision and reliability make it a preferred choice for many high-tech manufacturing processes.
Benefits Of Microscopic Welding
Microscopic welding offers numerous advantages over traditional welding. These benefits make it an essential technique in various industries. Let’s explore its key benefits.
Enhanced Precision
One of the main benefits of microscopic welding is its enhanced precision. This technique allows for greater accuracy in welding tasks. The precision ensures that even the smallest components are welded perfectly. This is crucial in industries like electronics and medical devices. A single error can lead to malfunction.
Industry | Importance of Precision |
---|---|
Electronics | Ensures functionality of tiny circuits |
Medical Devices | Critical for patient safety |
Improved Durability
Microscopic welding also leads to improved durability of the welded parts. The precise application of heat and materials results in stronger bonds. These bonds are less likely to fail under stress. This benefit is essential in industries where reliability is crucial.
- Automotive: Ensures long-lasting vehicle components
- Aerospace: Critical for the safety of aircraft parts
- Manufacturing: Increases the lifespan of machinery
With enhanced precision and improved durability, microscopic welding stands out as a superior choice.
Challenges And Limitations
Microscopic welding is a groundbreaking technology with immense potential. But, it comes with its own set of challenges and limitations. These obstacles can hinder its widespread adoption in various industries.
Technical Barriers
Microscopic welding faces several technical barriers that can impact its effectiveness. One major challenge is achieving precise control over the welding process. Working on such a small scale requires advanced machinery and high precision.
Another significant barrier is the material compatibility. Not all materials respond well to microscopic welding. Finding compatible materials that can be welded without compromising their properties is crucial.
Heat management is also a critical issue. The small size of the welds means that heat dissipation can be a problem, leading to potential damage to the components being welded.
Cost Implications
The cost implications of microscopic welding can be significant. High-precision equipment required for this process can be very expensive. This includes advanced microscopes, laser systems, and other specialized tools.
Additionally, the training costs for operators can add up. Skilled professionals are needed to operate and maintain the equipment. This increases the overall cost of implementation.
Another cost factor is the material costs. Since not all materials are compatible with microscopic welding, finding suitable materials can be more expensive.
Challenge | Impact |
---|---|
Precise Control | Requires advanced machinery |
Material Compatibility | Limits material choices |
Heat Management | Risk of component damage |
High Equipment Cost | Increases initial investment |
Training Costs | Requires skilled operators |
Material Costs | More expensive materials |
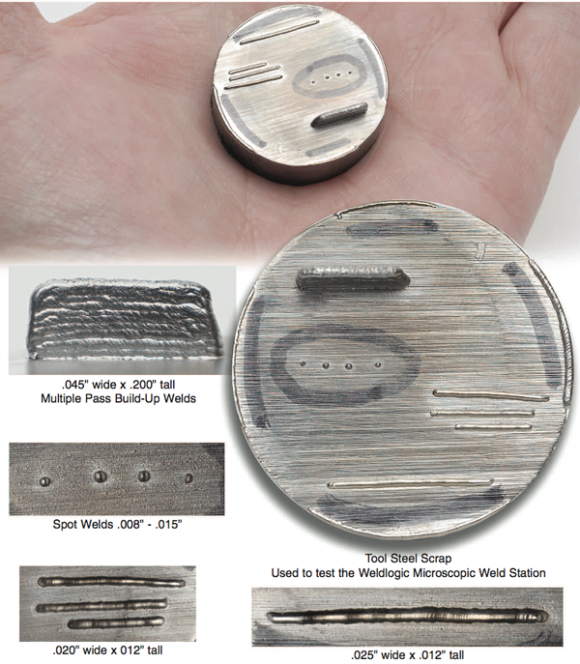
Credit: weldlogic.com
Future Prospects
The field of microscopic welding is evolving rapidly, opening up new possibilities and applications. With advancements in technology, we are witnessing significant changes and innovations. Let’s explore the future prospects of this fascinating field.
Emerging Trends
Several emerging trends are shaping the future of microscopic welding:
- Miniaturization of devices requires more precise welding techniques.
- Automation in welding processes increases efficiency and consistency.
- Nanotechnology integration enhances the capabilities of microscopic welding.
The miniaturization trend demands welding at a much smaller scale. This creates new challenges and opportunities for innovation. Automation helps in achieving high precision and repeatability, which are crucial for microscopic welding. Nanotechnology allows for the development of advanced materials and tools, further enhancing welding capabilities.
Potential Innovations
Future innovations in microscopic welding could revolutionize various industries:
Innovation | Impact |
---|---|
Laser Welding | Offers greater precision and control. |
AI Integration | Enhances accuracy and reduces errors. |
Advanced Materials | Improves durability and performance. |
Laser welding provides unparalleled precision, enabling more intricate designs. AI integration helps in monitoring and adjusting the welding process in real-time, ensuring optimal results. The use of advanced materials can lead to more durable and efficient welds, which is vital for the longevity of the components.
Case Studies
Microscopic welding has advanced in various industries. Explore real-world examples below. These case studies highlight its potential and challenges.
Successful Implementations
Several companies have achieved success with microscopic welding. Here are a few examples:
Company | Industry | Results |
---|---|---|
ABC Electronics | Consumer Electronics | Increased production efficiency by 20% |
XYZ Medical Devices | Healthcare | Improved product reliability by 30% |
LMN Automotive | Automobile Manufacturing | Reduced manufacturing costs by 15% |
Lessons Learned
From these case studies, valuable lessons have emerged:
- Precision is vital for success in microscopic welding.
- Quality control must be stringent to ensure reliability.
- Training is crucial for operators to master the technique.
Consider these key points for effective implementation:
- Invest in advanced equipment and technology.
- Ensure a clean and controlled environment.
- Regularly inspect and maintain welding tools.
These lessons can guide future projects and enhance outcomes.

Credit: m.youtube.com
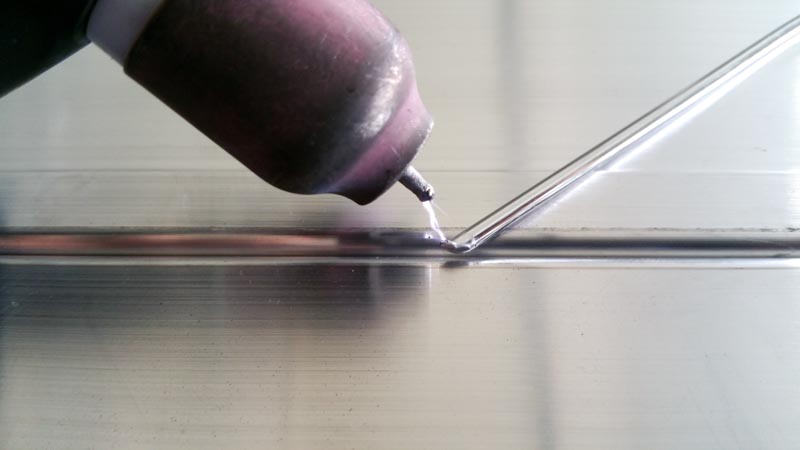
Credit: www.questindustries.net
Frequently Asked Questions
What Is Microscopic Welding?
Microscopic welding is a high-precision technique used to join tiny components. It involves welding at a microscopic scale. This process is crucial in electronics and microfabrication industries.
How Does Microscopic Welding Work?
Microscopic welding uses focused energy sources like lasers or electron beams. These tools precisely join small parts. The process requires high precision to ensure strong bonds without damaging components.
What Materials Can Be Welded Microscopically?
Various materials can be welded microscopically, including metals and polymers. Common materials include gold, platinum, and certain plastics. The choice depends on application requirements and material properties.
Why Is Microscopic Welding Important?
Microscopic welding is essential for manufacturing miniaturized electronic devices. It enables high-precision assembly of components. This process ensures reliability and performance in products like smartphones and medical devices.
Conclusion
Microscopic welding is transforming precision manufacturing. This advanced technique ensures high-quality, durable connections. Industries benefit from improved efficiency and reduced material waste. Embracing microscopic welding can lead to significant advancements. Stay ahead in the competitive market by integrating this innovative technology.
Discover the potential of microscopic welding for your business today.