In the world of medical device manufacturing, precision and reliability are paramount. That’s where medical welding comes into the picture. Welding medical devices is a critical process that demands the utmost expertise to ensure the safety and efficacy of medical tools and equipment. From surgical instruments to implantable devices, the seamless fusion of components is crucial for their performance and, ultimately, for patient well-being. Within this intricate realm, the welding techniques, regulations, and innovations are continuously evolving to meet the highest standards of quality and safety.
In this article, we delve into the intricacies of medical device welding, exploring the latest advancements and the pivotal role it plays in the healthcare landscape. Whether you are a professional in the medical manufacturing industry or simply curious about the vital cogs in the healthcare machinery, join us as we unravel the precision and artistry behind medical device welding.
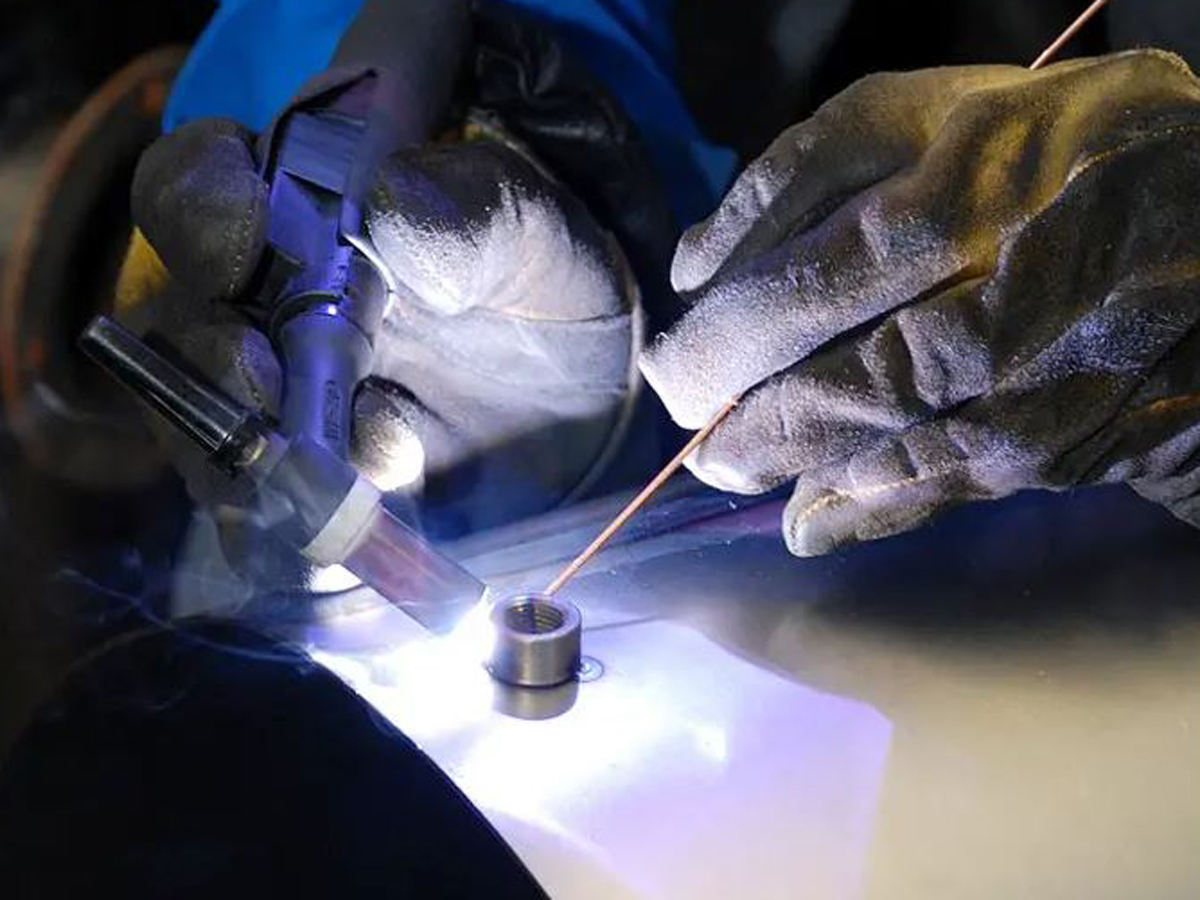
Photo by marsjo
Importance of Precision in Medical Device Welding
Precision in medical device welding is non-negotiable. The seamless fusion of components is vital for the functionality and safety of medical devices. Any imperfection in the welding process can compromise the structural integrity of the device, leading to potential risks for patients. The precision in welding ensures that the devices can withstand the rigors of medical procedures and maintain their performance over time. It also plays a crucial role in minimizing the risk of contamination and infection, particularly in devices that come into direct contact with bodily tissues and fluids. The precision of medical device welding directly correlates with patient safety and the overall efficacy of medical treatments and procedures.
The precision in medical device welding is achieved through the use of advanced technologies and highly skilled professionals. Laser welding, for example, allows for microscopic precision, enabling the welding of tiny components with exceptional accuracy. Additionally, the use of robotic welding systems ensures consistent and precise welds, eliminating the margin for human error. Furthermore, stringent quality control measures are implemented to verify the precision of each weld, ensuring that the finished medical devices meet the highest standards of safety and reliability.
The pursuit of precision in medical device welding also extends to the selection of materials. The compatibility of materials with the human body, along with their ability to withstand sterilization processes and environmental factors, is critical in ensuring the overall precision and longevity of the welded components. As technology continues to advance, the pursuit of precision in medical device welding remains a driving force in the evolution of medical device manufacturing.
Types of Welding Techniques for Medical Devices
Medical device welding encompasses a variety of techniques, each tailored to meet specific requirements and challenges in the manufacturing process. Among the most prevalent techniques is laser welding, renowned for its precision and versatility. Laser welding allows for pinpoint accuracy, making it ideal for joining delicate components in medical devices. Its non-contact nature also minimizes the risk of contamination, a crucial factor in medical applications.
Another commonly used technique in medical device welding is resistance spot welding. This method utilizes electrical resistance to join metal components, offering a rapid and cost-effective solution for high-volume production. While it may not provide the same level of precision as laser welding, resistance spot welding is well-suited for certain medical devices that do not require microscopic weld seams.
Ultrasonic welding is also prominent in the medical device manufacturing industry, particularly for thermoplastic materials. This method employs high-frequency ultrasonic vibrations to create strong molecular bonds between components, making it suitable for applications where heat-sensitive materials are involved. The versatility of ultrasonic welding enables the assembly of a wide range of medical devices, from disposable medical tools to complex surgical instruments.
In addition to these techniques, arc welding and electron beam welding find their niche in specific medical device manufacturing processes, catering to the welding of larger and more robust components. The diversity of welding techniques available for medical devices reflects the industry’s commitment to finding the most suitable method for each unique application, balancing factors such as precision, efficiency, and material compatibility.
Materials Used in Medical Device Welding
The materials utilized in medical device welding play a pivotal role in determining the functionality, safety, and longevity of the finished products. Stainless steel, known for its corrosion resistance and biocompatibility, is a prevalent choice in the manufacturing of surgical instruments, orthopedic implants, and medical tool casings. Its strength and durability make it an ideal material for components subjected to demanding mechanical stresses and sterilization processes.
Titanium and its alloys are also highly favored in medical device welding, particularly in the production of implants and prosthetics. The biocompatibility of titanium, along with its exceptional strength-to-weight ratio, renders it an excellent choice for load-bearing implants and devices intended for long-term implantation within the human body. The weldability of titanium further enhances its appeal, allowing for the creation of intricate and durable medical components.
In the realm of disposable medical devices, thermoplastic materials such as polycarbonate, polyethylene, and polypropylene are commonly employed. These materials offer a balance of strength, flexibility, and ease of manufacturing, making them suitable for applications ranging from fluid delivery systems to diagnostic tools. The welding of thermoplastics demands specialized techniques and expertise to achieve reliable and robust bonds, ensuring the integrity of the final products.
The advancement of biodegradable materials has introduced new possibilities in medical device welding, particularly for temporary implants and drug delivery systems. Biodegradable polymers, such as polylactic acid (PLA) and polyglycolic acid (PGA), are gaining traction for their ability to gradually degrade within the body, eliminating the need for surgical removal after fulfilling their intended purpose. The welding of biodegradable materials presents unique challenges due to their degradation properties, necessitating precise control over the welding process to maintain structural integrity until the end of the device’s lifespan.
The selection of materials for medical device welding involves a meticulous consideration of factors such as biocompatibility, mechanical properties, sterilization compatibility, and manufacturability. Each material brings its own set of advantages and challenges, influencing the welding techniques and processes employed to achieve optimal results in medical device manufacturing.
Quality Control in Medical Device Welding
The quality control measures implemented in medical device welding are paramount in ensuring the reliability and safety of the finished products. From the initial stages of material inspection to the final validation of welded components, rigorous quality control protocols are integrated into every facet of the manufacturing process. Visual inspection, non-destructive testing, and mechanical testing are among the techniques employed to verify the integrity of welds and the overall quality of medical devices.
Visual inspection serves as the first line of defense in quality control, allowing for the identification of surface imperfections, discontinuities, or deviations from the prescribed welding parameters. This initial assessment is complemented by non-destructive testing methods, such as radiographic testing, ultrasonic testing, and dye penetrant inspection, which delve beneath the surface to detect internal flaws that may compromise the structural integrity of welded components.
The utilization of advanced imaging technologies, such as computed tomography (CT) scanning, further enhances the capacity to scrutinize complex weld geometries and intricate assemblies, providing a comprehensive evaluation of the weld quality. These non-destructive testing methods enable manufacturers to identify and rectify potential defects before the completed medical devices undergo clinical implementation, mitigating the risk of product failure and ensuring the well-being of patients.
Mechanical testing, encompassing tensile testing, bend testing, and fatigue testing, is instrumental in assessing the strength and durability of welded components. These tests subject the welds to simulated mechanical stresses, gauging their performance under conditions that mirror real-world usage. By subjecting the welded components to rigorous mechanical evaluations, manufacturers can ascertain their ability to withstand the demands of medical applications, offering a level of assurance in the quality and longevity of the devices.
Furthermore, traceability and documentation play a crucial role in quality control, allowing for the comprehensive recording of welding parameters, material specifications, and inspection results. This meticulous documentation facilitates the traceability of each component throughout its lifecycle, enabling manufacturers to uphold accountability and transparency in the production of medical devices. The culmination of these quality control measures instills confidence in the reliability and safety of medical devices, underscoring the significance of stringent quality management in medical device welding.
Regulatory Standards for Medical Device Welding
The manufacturing of medical devices, including the welding processes involved, is subject to stringent regulatory oversight to ensure the utmost safety and efficacy for patients and healthcare professionals. Regulatory bodies, such as the U.S. Food and Drug Administration (FDA) and the European Medicines Agency (EMA), impose comprehensive guidelines and standards that dictate the requirements for medical device manufacturing, encompassing design, materials, production processes, and post-market surveillance.
The International Organization for Standardization (ISO) also plays a pivotal role in establishing international standards for medical device manufacturing, harmonizing practices on a global scale. ISO 13485, in particular, outlines the requirements for a quality management system specific to the medical device industry, encompassing the design, development, production, installation, and servicing of medical devices. Compliance with ISO 13485 demonstrates a manufacturer’s commitment to meeting the highest standards of quality and regulatory conformity in medical device welding.
The regulatory landscape for medical device welding extends beyond general manufacturing standards to address the specific considerations associated with welding processes. For instance, the FDA’s guidance document on laser welding of thermoplastics outlines the agency’s expectations regarding the validation of laser welding processes, material compatibility assessments, and the documentation of welding parameters. Similarly, the European Committee for Standardization (CEN) provides standards such as EN ISO 13918, which delineates the requirements for the stud welding of metallic materials, including those used in medical devices.
Compliance with regulatory standards is not only a legal requirement but also a fundamental aspect of ensuring patient safety and product effectiveness. Manufacturers and welding professionals must navigate the intricate web of regulations, staying abreast of updates and revisions to standards while upholding a steadfast commitment to adherence. The convergence of regulatory compliance and technical proficiency is essential in safeguarding the integrity of medical devices and fostering trust within the healthcare community.
Future Trends in Medical Device Welding
The landscape of medical device welding is continually evolving, driven by technological advancements, material innovations, and the ever-changing demands of the healthcare industry. One of the prominent trends shaping the future of medical device welding is the integration of additive manufacturing, commonly known as 3D printing. Additive manufacturing techniques offer unparalleled design freedom, enabling the creation of intricately structured components that were previously unattainable through traditional manufacturing methods.
The marriage of additive manufacturing with welding processes opens new frontiers in the production of customized implants, patient-specific medical devices, and complex geometries that cater to individual anatomies. This convergence presents both opportunities and challenges, prompting the refinement of welding techniques tailored to the unique characteristics of additively manufactured components, ensuring the integrity and performance of the final products.
The advent of smart materials and nanotechnology also holds promise for the future of medical device welding. Smart materials, imbued with responsive and adaptive properties, offer the potential for self-healing mechanisms, drug delivery functionalities, and real-time monitoring capabilities within medical devices. The welding of smart materials necessitates advanced methodologies that preserve their inherent properties while facilitating seamless integration into multifunctional medical devices.
Furthermore, nanotechnology presents opportunities for the development of nanostructured materials and coatings that enhance the biocompatibility, antimicrobial properties, and wear resistance of medical devices. The welding of nanoengineered components demands precision at the nanoscale, requiring novel approaches and expertise to harness the benefits of nanotechnology while ensuring the reliability and safety of the welded assemblies.
The convergence of digitalization and welding processes is also poised to revolutionize the landscape of medical device manufacturing. Digital twin technology, which entails the virtual representation of physical devices and processes, offers the potential for real-time monitoring, predictive maintenance, and optimization of welding parameters. This digital integration empowers manufacturers to refine their welding practices, minimize variability, and maximize the consistency and quality of medical device production.
As the healthcare industry continues to embrace personalized medicine and advanced therapies, the demand for innovative medical devices will drive the evolution of welding techniques and materials. The future of medical device welding lies at the intersection of precision engineering, material science, and regulatory compliance, charting a course toward the creation of safer, more effective, and technologically sophisticated medical devices.
Training and Certification for Medical Device Welding
The proficiency and expertise required for medical device welding necessitate comprehensive training and certification programs to equip professionals with the requisite knowledge and skills. Welding operators, engineers, and quality assurance personnel involved in medical device manufacturing undergo specialized training to comprehend the nuances of welding processes specific to the healthcare industry. These training programs encompass theoretical instruction, hands-on practical exercises, and assessments to ensure competence and adherence to regulatory standards.
Certification plays a pivotal role in validating the proficiency of welding professionals, providing assurance to employers and regulatory authorities that individuals possess the requisite competencies to execute medical device welding tasks effectively and safely. Certifying bodies, such as the American Welding Society (AWS) and the International Institute of Welding (IIW), offer certifications tailored to medical device welding, encompassing various welding techniques, materials, and quality control practices.
The training and certification of welding professionals extend beyond technical skills to encompass an understanding of regulatory compliance, quality management systems, and the ethical considerations inherent in medical device manufacturing. Welding personnel are trained to interpret and implement welding procedures, comprehend material specifications, and navigate the documentation and traceability requirements essential for regulatory conformity. Additionally, an awareness of the impact of welding on the performance and safety of medical devices is instilled, emphasizing the critical responsibility entrusted to welding professionals in the healthcare ecosystem.
Ongoing professional development is also integral in the realm of medical device welding, as it allows welding professionals to stay abreast of technological advancements, regulatory updates, and best practices. Continuous learning and skill enhancement ensure that welding personnel remain at the forefront of industry developments, upholding the highest standards of quality and safety in medical device manufacturing. The investment in training and certification for medical device welding serves as a cornerstone in fostering a proficient and ethical workforce dedicated to the well-being of patients.
Choosing a Medical Device Welding Partner
Selecting a proficient and reliable partner for medical device welding is a consequential decision that profoundly impacts the quality, safety, and success of medical devices. When evaluating potential welding partners, several key considerations come to the forefront, guiding manufacturers and stakeholders in their quest for a collaborative and capable welding specialist.
Final Thoughts
Medical Device Welding is one of the most common welding processes in the field of medical and surgery. This process is used for joining metals by melting the base material. In order for the process to be successful, proper materials need to be purchased and transported. When performing welding on different types of metals, the welding process must be adjusted accordingly. During welding a single layer of metal is melted and then fused together. This process is often called stick welding because the weld is hot enough to make a simple stick of the interlocked materials. The type of medical device welding used depends on what is being welded.