Laser welding provides high precision and minimal distortion, making it ideal for thin materials. MIG welding is more versatile and cost-effective for thicker materials and general applications.
Laser welding uses a concentrated light beam to join materials, resulting in precise and clean welds. It is suitable for high-speed and automated processes, often used in industries like aerospace and automotive manufacturing. MIG welding, short for Metal Inert Gas welding, involves feeding a continuous wire electrode through a welding gun.
This method is widely used in construction, automotive repair, and fabrication due to its versatility and ease of use. Each welding technique has distinct advantages, making them suitable for different applications and material thicknesses.
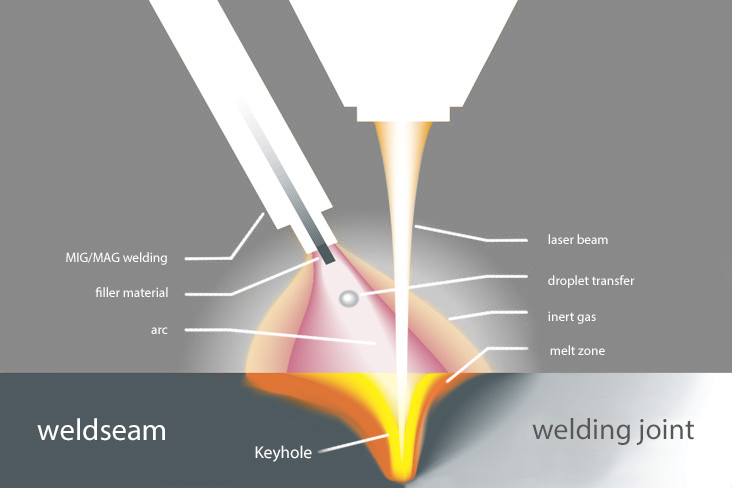
Credit: safe-welding.com
Basics Of Laser Welding
Laser welding is a process that uses a laser beam to join materials. This method ensures a precise and strong weld. It is widely used in various industries due to its accuracy and efficiency. Laser welding can join both similar and dissimilar materials. It is particularly useful for thin materials and delicate components.
How Laser Welding Works
Laser welding works by focusing a laser beam on the materials to be joined. The high energy of the laser melts the material at the point of contact. As the material cools, it solidifies to form a strong bond.
This process can be performed in two main modes:
- Conduction Mode: The laser heats the material to create a weld pool.
- Keyhole Mode: The laser creates a small keyhole in the material, which then fills with molten metal.
Laser welding is often performed using automated systems. This ensures consistent and high-quality welds. It is ideal for applications requiring precision and minimal heat distortion.
Types Of Laser Welding
There are several types of laser welding, each suited for different applications:
Type | Description | Applications |
---|---|---|
CW (Continuous Wave) Laser Welding | The laser emits a continuous beam. | Used for deep welds and high-speed applications. |
Pulsed Laser Welding | The laser emits short, high-energy pulses. | Ideal for welding thin materials and delicate components. |
Fiber Laser Welding | Uses optical fibers to deliver the laser beam. | Popular in automotive and aerospace industries. |
CO2 Laser Welding | Uses a gas mixture to generate the laser. | Common in medical device manufacturing. |
Each type of laser welding offers unique advantages. The choice of type depends on the material, thickness, and application requirements. Laser welding is a versatile technique that provides high precision and control.

Credit: www.youtube.com
Basics Of Mig Welding
MIG welding, or Metal Inert Gas welding, is a popular welding method. It uses a continuous wire electrode. This method is known for its simplicity and speed. Beginners and professionals alike use MIG welding extensively. It is often used in automotive repair, construction, and manufacturing industries.
How Mig Welding Works
MIG welding involves feeding a wire through a welding gun. The wire serves as both the electrode and the filler material. An electric arc forms between the wire and the base metal. This arc melts the wire, creating a molten pool. This pool then cools, forming a strong bond.
The process uses a shielding gas. This gas protects the weld from atmospheric contamination. Common gases used include argon, carbon dioxide, or a mix of both. The type of gas affects the weld quality and properties.
Types Of Mig Welding
There are several types of MIG welding. Each type is suitable for different applications and materials. Here is a brief overview:
Type | Description |
---|---|
Short Circuit Transfer | Ideal for thin materials. The wire touches the metal, creating a short circuit. This results in a small, controlled arc. |
Globular Transfer | Uses a higher voltage. Creates larger droplets that transfer to the weld pool. Suitable for thicker materials. |
Spray Transfer | Produces a fine spray of molten metal. Ideal for welding thick materials and high-speed welding. |
Pulsed MIG | Alternates between high and low current. Reduces heat input. Suitable for thin materials and out-of-position welding. |
Each type offers unique benefits. Choose the type based on your project requirements. Understanding these basics can help you achieve better welding results.
Comparing Efficiency
When comparing efficiency, laser welding and MIG welding both have unique strengths. Understanding these differences can help you choose the best method for your project. Let’s delve into the key aspects of efficiency with a focus on speed, precision, and material suitability.
Speed And Precision
Laser welding is renowned for its speed. It delivers quick, high-quality welds. The laser beam is highly concentrated, allowing for fast, precise work. This method is ideal for projects requiring detailed and intricate welds.
On the other hand, MIG welding is also efficient but in a different way. It is easier for beginners and can be faster for larger, less detailed tasks. MIG welding provides a consistent weld, suitable for various applications.
Aspect | Laser Welding | MIG Welding |
---|---|---|
Speed | High | Moderate |
Precision | Very High | Moderate |
Material Suitability
Laser welding excels with thin materials and non-ferrous metals. It is perfect for aluminum and titanium. This technique also minimizes heat distortion, preserving material integrity.
MIG welding, conversely, is more versatile with thicker materials. It works well with steel and other ferrous metals. It is excellent for heavy-duty tasks and robust structures.
- Laser Welding:
- Thin materials
- Non-ferrous metals
- Aluminum and titanium
- MIG Welding:
- Thicker materials
- Ferrous metals
- Steel
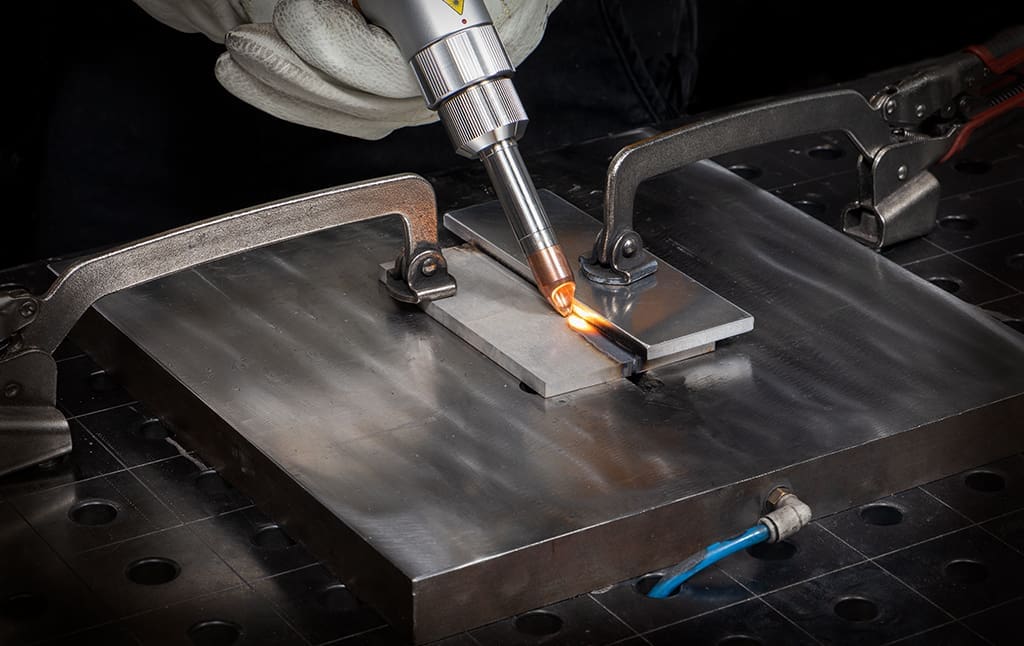
Credit: selmach.com
Cost Considerations
When comparing Laser Welding and MIG Welding, cost considerations play a crucial role. Understanding the financial aspects can help you make a more informed decision.
Equipment Costs
The initial investment in welding equipment varies significantly between Laser Welding and MIG Welding. Laser welding machines are generally more expensive due to advanced technology and precision. These machines can cost anywhere from $50,000 to over $1 million, depending on the specifications and capabilities.
In contrast, MIG welding equipment is more affordable. A basic MIG welder can start as low as $200, with industrial-grade models reaching up to $10,000. This makes MIG welding a more accessible option for smaller operations or individuals.
Welding Type | Equipment Cost Range |
---|---|
Laser Welding | $50,000 – $1,000,000+ |
MIG Welding | $200 – $10,000 |
Operational Costs
Operational costs also differ between the two welding methods. Laser Welding typically requires less maintenance and fewer consumables. However, the cost of power consumption can be higher due to the high-energy lasers used.
On the other hand, MIG Welding involves ongoing expenses for consumables like gas and wire. Maintenance costs can also add up over time, especially if the equipment is used extensively.
- Laser Welding:
- Lower maintenance costs
- Higher power consumption
- MIG Welding:
- Higher consumable costs
- Frequent maintenance required
In summary, Laser Welding has higher upfront costs but may save money in the long run. MIG Welding is cheaper to start with, but operational costs can add up.
Quality And Strength
Laser welding and MIG welding are popular techniques. They are used for joining metals. Each method has its strengths and weaknesses. This section focuses on their weld quality and durability.
Weld Quality
Laser welding produces precise and clean welds. It uses a concentrated beam of light. This results in minimal distortion. The welds have a smooth appearance. They often require less finishing work.
MIG welding, on the other hand, uses a wire electrode. It produces thicker welds. The process is faster but can result in more spatter. The welds may need additional cleaning.
Here’s a comparison table for quick reference:
Aspect | Laser Welding | MIG Welding |
---|---|---|
Precision | High | Moderate |
Appearance | Clean | Spatter-prone |
Finishing | Less Required | More Required |
Durability Of Welds
Laser welds are strong and durable. The heat-affected zone (HAZ) is smaller. This means less material stress. The joints are often more resistant to fatigue and wear.
MIG welds are also durable. They are thicker and can handle more load. But the larger HAZ can introduce weaknesses. Proper technique and material choice are crucial.
In summary, both methods offer strong welds. The choice depends on the specific application and requirements.
Safety Aspects
Understanding the safety aspects of welding methods is crucial. Welding involves risks, and each method has different safety concerns. Let’s explore the safety aspects of Laser Welding and MIG Welding.
Laser Welding Safety
Laser welding uses high-energy laser beams. This method has unique safety requirements. Here are some key safety aspects to consider:
- Eye Protection: Laser beams can damage eyes. Use appropriate laser safety goggles.
- Skin Protection: Lasers can burn skin. Wear protective clothing.
- Fume Extraction: Laser welding produces fumes. Ensure proper ventilation.
- Fire Safety: High-energy lasers can ignite materials. Keep fire extinguishers nearby.
- Machine Safety: Maintain laser welding machines regularly. Check for any malfunctions.
Mig Welding Safety
MIG welding uses an electric arc. It also involves specific safety measures. Here are the essential safety points:
- Eye Protection: Wear a welding helmet. Protects against arc rays and sparks.
- Respiratory Safety: Use a respirator. Prevents inhalation of harmful fumes.
- Skin Protection: Wear flame-resistant clothing and gloves. Protects against burns.
- Electrical Safety: Ensure proper grounding. Prevents electrical shocks.
- Fire Safety: Keep the work area free of flammable materials. Have fire extinguishers ready.
Both welding methods have their own safety concerns. Always follow safety guidelines. Protect yourself and others.
Applications In Industry
Laser welding and MIG welding have diverse applications in various industries. Their unique features make them suitable for specific tasks. Below, we explore their use in two major industries: automotive and aerospace.
Automotive Industry
Laser welding is widely used in the automotive industry. It provides high precision and clean welds. This method is perfect for intricate components. It ensures minimal heat distortion, which is essential for car body panels.
MIG welding is also popular in the automotive sector. It’s used for thicker materials and structural parts. This method is faster and more cost-effective for large-scale production. MIG welding is ideal for chassis and frame constructions.
Welding Method | Applications | Advantages |
---|---|---|
Laser Welding | Car body panels, intricate components | High precision, minimal heat distortion |
MIG Welding | Chassis, frame constructions | Faster, cost-effective |
Aerospace Industry
Laser welding plays a crucial role in the aerospace industry. It offers precise control and high-strength welds. This method is essential for critical components like turbine blades and fuel tanks.
MIG welding is also used in aerospace. It’s suitable for larger structures and repairs. MIG welding provides strong bonds and is effective on various metals. This method is used for assembling aircraft fuselages and wings.
- Laser Welding: Turbine blades, fuel tanks, high-strength welds
- MIG Welding: Aircraft fuselages, wings, strong bonds
Future Trends
The future of welding technology holds many exciting possibilities. Both laser welding and MIG welding are evolving rapidly. These advancements will shape the manufacturing industry for years to come. Let’s dive into the latest innovations and advancements.
Innovations In Laser Welding
Laser welding is becoming more precise and efficient. New technologies are pushing the boundaries of what is possible.
- Fiber lasers are now more powerful and reliable.
- Automation is making laser welding faster and safer.
- Real-time monitoring improves weld quality.
- 3D laser welding allows for complex shapes.
These innovations make laser welding suitable for high-volume production. Industries like automotive and aerospace benefit greatly.
Advancements In Mig Welding
MIG welding is also seeing significant advancements. These changes enhance performance and user experience.
- Pulsed MIG welding reduces spatter and improves control.
- Inverter technology offers better arc stability.
- Advanced welding helmets provide better visibility and safety.
- Improved wire feeders ensure consistent welds.
These advancements make MIG welding more accessible and efficient. This technique is ideal for construction and fabrication.
Feature | Laser Welding | MIG Welding |
---|---|---|
Precision | High | Moderate |
Automation | Advanced | Developing |
Material Versatility | High | Medium |
Speed | Fast | Moderate |
Frequently Asked Questions
What Is Laser Welding?
Laser welding is a technique that uses a laser to join materials. It provides precision and high-quality welds. It’s ideal for intricate and delicate tasks.
What Is Mig Welding?
MIG welding uses a continuous solid wire electrode. It is fed through a welding gun into the weld pool. It’s suitable for thicker materials and offers good productivity.
Which Welding Is More Precise?
Laser welding is more precise than MIG welding. It allows for detailed and intricate welding. This makes it ideal for small and complex components.
Which Welding Method Is Faster?
Laser welding is generally faster than MIG welding. It delivers quicker welds with high precision. This reduces production time significantly.
Conclusion
Choosing between laser welding and MIG welding depends on your specific needs. Laser welding offers precision and speed, while MIG welding provides versatility and cost-effectiveness. Evaluate your project requirements, budget, and desired outcomes. Both methods have their unique advantages, ensuring you achieve the best results for your welding tasks.