In today’s rapidly evolving industrial landscape, the demand for advanced materials capable of withstanding extreme conditions is higher than ever. Titanium, renowned for its exceptional strength, corrosion resistance, and biocompatibility, has emerged as a material of choice across diverse sectors, from aerospace and automotive to medical device manufacturing. However, the inherent challenges of welding titanium have historically limited its widespread application. Traditional welding methods often result in compromised structural integrity and undesirable heat-affected zones, undermining the material’s inherent properties.
Enter laser welding – a cutting-edge technique that has revolutionized the fabrication of titanium components, offering precision, efficiency, and quality that were previously unattainable. In this comprehensive exploration, we delve into the transformative potential of laser welding for titanium applications, shedding light on its unparalleled precision, advantages, challenges, best practices, quality control, and future trends.
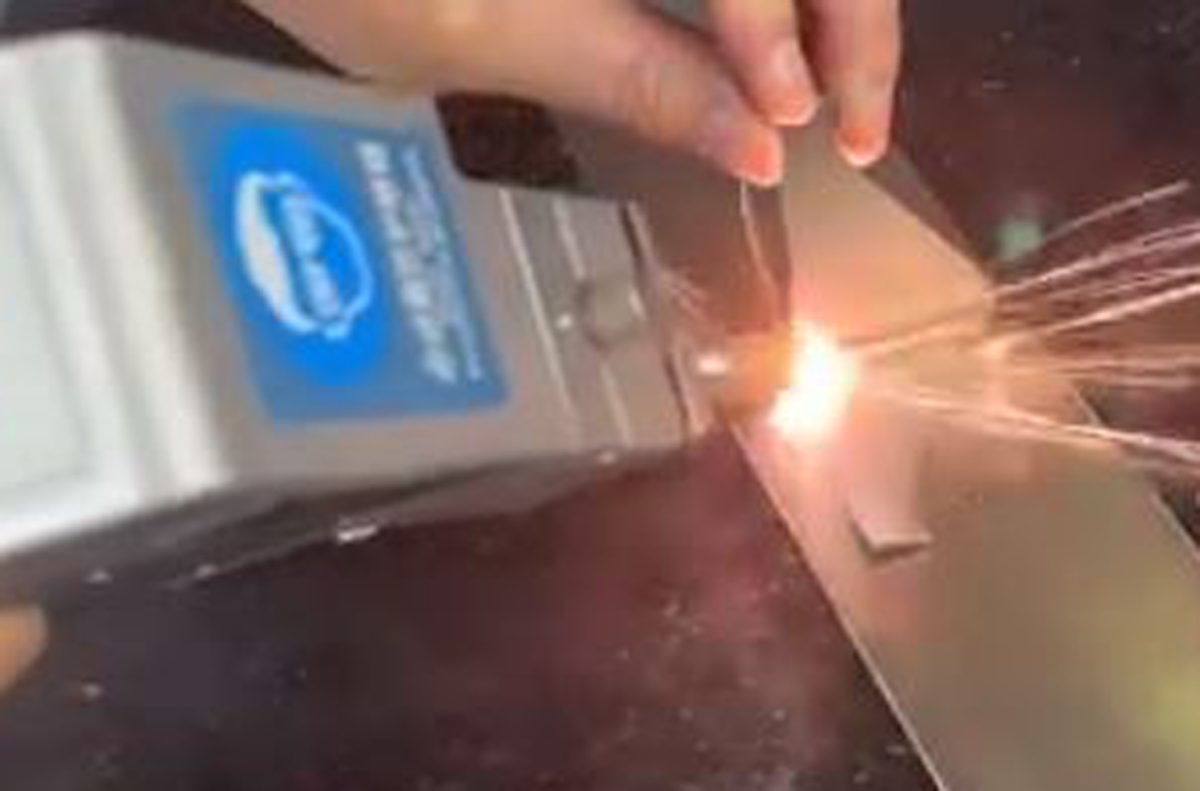
Photos by Triumphlaser on YT
Laser Welding Titanium and Its Application
Laser welding is a high-precision welding process that utilizes a concentrated beam of light to generate heat, enabling the fusion of metallic materials with exceptional accuracy. When applied to titanium, this advanced technique facilitates the creation of seamless, high-strength joints with minimal distortion and heat-affected zones. Unlike conventional welding methods, laser welding minimizes the risk of contamination and oxidation, preserving the material’s integrity and enhancing the overall quality of welded titanium components. The precise control and focused energy delivery of the laser beam enable intricate welding geometries and intricate designs, making it an ideal choice for complex titanium structures that demand uncompromising precision.
Advantages of Laser Welding Titanium
The adoption of laser welding for titanium fabrication offers a myriad of advantages that significantly elevate the production of titanium components. One of the primary benefits lies in the minimal heat input associated with laser welding, which effectively reduces the risk of thermal distortion and material degradation. This results in superior mechanical properties and structural integrity, positioning laser-welded titanium as a preferred choice for applications where precision and reliability are paramount.
The absence of filler materials in laser welding further enhances the corrosion resistance of titanium joints, making it an ideal solution for critical components exposed to harsh environments. The localized heat input and minimal thermal stress minimize the likelihood of microstructural changes, preserving the material’s properties and ensuring consistent performance across a wide range of operating conditions.
Challenges of Laser Welding Titanium
Despite its numerous advantages, laser welding titanium presents distinct challenges that require careful consideration and specialized expertise. Titanium’s high reactivity with oxygen and nitrogen necessitates stringent control of the welding environment to prevent the formation of undesirable intermetallic compounds and porosity. The reflective nature of titanium poses challenges in optimizing the absorption of laser energy, requiring precise tuning of laser parameters to achieve optimal weld penetration and quality.
The thermal conductivity of titanium demands meticulous attention to the management of heat input and dissipation, as excessive heat can lead to material embrittlement and diminished mechanical properties. Addressing these challenges mandates a deep understanding of titanium’s metallurgical behavior and the intricacies of laser welding, underscoring the importance of comprehensive training and expertise in this specialized welding discipline.
Laser Welding Titanium Process
The laser welding process for titanium involves a series of meticulously orchestrated steps to ensure the production of high-quality, defect-free welds. The selection of laser parameters, including power density, beam diameter, and pulse duration, is critical in achieving optimal energy absorption and penetration while mitigating the risk of thermal distortion. The use of shielding gases, such as argon or helium, serves to create a protective atmosphere that shields the molten weld pool from atmospheric contaminants, preserving the purity and integrity of the weld.
The precise alignment of the laser beam and the workpiece, coupled with advanced motion control systems, enables the creation of intricate weld geometries and precise joint configurations, further enhancing the versatility and applicability of laser-welded titanium components. The meticulous execution of the laser welding process, coupled with rigorous quality assurance measures, ensures the production of titanium welds that meet the most stringent performance and reliability standards.
Best Practices for Laser Welding Titanium
Achieving exceptional results in laser welding titanium hinges on the adherence to best practices that optimize process parameters, material preparation, and welding environment. Prior to welding, meticulous cleaning and surface preparation of titanium surfaces are essential to eliminate contaminants and ensure metallurgical purity. This preparatory step is crucial in preventing the formation of defects and preserving the integrity of the welded joints. Furthermore, the precise control of laser parameters, including focal position, beam quality, and pulse characteristics, is paramount in achieving consistent weld quality and minimizing the risk of imperfections.
The implementation of advanced monitoring and control systems allows for real-time assessment of welding parameters, enabling immediate adjustments to optimize weld quality and mitigate potential issues. By embracing best practices rooted in precision, thoroughness, and continuous improvement, manufacturers can unlock the full potential of laser welding for titanium applications, propelling the advancement of high-performance titanium components across diverse industries.
Quality Control and Inspection in Laser Welding Titanium
Ensuring the integrity and reliability of laser-welded titanium components demands a comprehensive approach to quality control and inspection. Advanced non-destructive testing techniques, such as ultrasonic testing and radiographic inspection, enable the detection of internal defects and discontinuities, safeguarding against the presence of flaws that could compromise the structural integrity of the welds. Additionally, meticulous visual inspection and dimensional measurements serve to verify the geometrical accuracy and surface finish of laser-welded titanium components, providing assurance of conformance to stringent industry standards.
The implementation of robust quality management systems and traceability protocols facilitates the documentation and tracking of welding parameters, material certifications, and inspection results, ensuring transparency and accountability throughout the manufacturing process. By prioritizing rigorous quality control and inspection practices, manufacturers can instill confidence in the performance and reliability of laser-welded titanium components, elevating their suitability for mission-critical applications across a spectrum of industries.
Applications of Laser Welding Titanium in Industries
The widespread adoption of laser-welded titanium has catalyzed transformative advancements across an array of industries, unlocking new possibilities and pushing the boundaries of performance and innovation. In the aerospace sector, laser welding titanium components have revolutionized the design and fabrication of lightweight, high-strength structures, enabling the realization of fuel-efficient aircraft and spacecraft with unparalleled resistance to corrosion and fatigue. The automotive industry has also witnessed the integration of laser-welded titanium for the production of exhaust systems, chassis components, and suspension elements, capitalizing on its exceptional durability and weight savings to enhance vehicle performance and fuel efficiency.
Moreover, the medical device manufacturing sector has leveraged laser-welded titanium to create implants, surgical instruments, and diagnostic equipment characterized by biocompatibility, corrosion resistance, and exceptional mechanical properties, underscoring its pivotal role in advancing the standard of care and patient outcomes. As laser welding titanium continues to redefine the possibilities in material science and engineering, its applications are poised to expand further, permeating new frontiers and stimulating innovation across diverse industrial domains.
Training and Certification in Laser Welding Titanium
The mastery of laser welding for titanium applications necessitates specialized training and certification to ensure proficiency and competence in this advanced welding discipline. Comprehensive training programs encompassing theoretical principles, practical techniques, and hands-on experience equip welding professionals with the knowledge and skills essential for the successful execution of laser welding processes. Additionally, certification programs validate the expertise and proficiency of welders, affirming their capability to uphold the exacting standards and specifications governing the laser welding of titanium.
Ongoing professional development and continuous education initiatives enable welding practitioners to stay abreast of technological advancements, emerging best practices, and evolving industry standards, empowering them to deliver exceptional results and maintain a competitive edge in the dynamic landscape of titanium fabrication. By investing in training and certification, organizations demonstrate their commitment to excellence and precision in laser welding, fostering a workforce equipped to drive innovation and excellence in the production of laser-welded titanium components.
Future Trends in Laser Welding Titanium
The future of laser welding titanium holds tremendous promise, with emerging trends and technological advancements poised to reshape the landscape of titanium fabrication and manufacturing. Continued research and development efforts are focused on enhancing laser welding processes through the integration of advanced monitoring and control systems, further refining the precision, reliability, and efficiency of titanium welding operations. The evolution of laser technology, including the advent of ultrafast lasers and beam shaping techniques, is set to expand the capabilities and versatility of laser welding, enabling the fabrication of intricate, multifaceted titanium components with unprecedented speed and precision.
The convergence of additive manufacturing and laser welding is anticipated to unlock new frontiers in the production of complex, hybrid structures, leveraging the complementary strengths of both technologies to realize next-generation titanium components with unparalleled performance and functionality. As these future-oriented trends unfold, the potential for laser-welded titanium to permeate new applications and industries is poised to catalyze transformative advancements, driving innovation, efficiency, and excellence across the entire spectrum of titanium fabrication.
Conclusion
The advent of laser welding has ushered in a new era of possibilities for titanium, empowering manufacturers to harness its exceptional properties with unparalleled precision and quality. The fusion of advanced laser technology with the inherent strengths of titanium has transcended the limitations of traditional welding methods, unlocking the potential for high-performance, mission-critical applications across aerospace, automotive, medical device manufacturing, and beyond. While the challenges of laser welding titanium are not to be underestimated, their thoughtful mitigation through best practices, rigorous quality control, and ongoing innovation promises to drive the continued advancement of laser-welded titanium components.
As the future unfolds, the transformative potential of laser welding titanium applications is poised to redefine the boundaries of material science and engineering, propelling the realization of groundbreaking innovations and elevating the standard of excellence across diverse industrial sectors. Embracing the precision and transformative capabilities of laser welding, the journey of titanium fabrication continues to unfold, opening new vistas of possibility and excellence in the relentless pursuit of innovation and performance.