Laser welding technology, a cutting-edge advancement in manufacturing processes, has revolutionized the way industries approach welding. Unlike traditional welding methods that rely on heat conduction, laser welding utilizes a concentrated beam of light to join materials together. The precision and accuracy achieved through laser welding are unparalleled, making it an indispensable tool in modern manufacturing. This technology operates on the principles of photonics, where a high-powered laser beam is directed at the joint to create a fusion.
The result is a seamless bond between the materials with minimal distortion, heat-affected zones, and superior weld quality. Laser welding has emerged as a game-changer, offering unmatched efficiency, speed, and versatility in joining a wide range of materials. Its impact extends across diverse industries, from automotive and aerospace to electronics and medical devices, where precision and reliability are paramount.
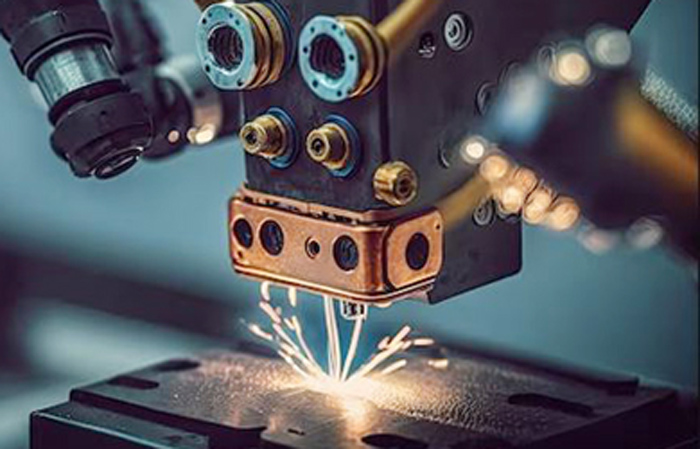
Image: shutterstock
The process of laser welding involves the generation of intense heat at the point of contact between the materials to be joined. This localized heat causes the materials to melt and fuse together, creating a strong and durable bond. The laser beam’s high energy density allows for rapid heating and cooling, resulting in minimal distortion of the surrounding area. As a non-contact process, laser welding eliminates the need for physical pressure on the materials, reducing the risk of deformation and ensuring precise control over the welding parameters.
The ability to achieve deep penetration and narrow weld seams further distinguishes laser welding as a superior joining method. By harnessing the power of focused light energy, laser welding offers a level of precision and consistency that traditional welding techniques struggle to match.
The versatility of laser welding extends beyond its ability to join different materials, including metals, plastics, and composites. Its capability to weld dissimilar materials with varying thicknesses and thermal properties makes it an attractive choice for complex manufacturing requirements. Whether it’s aluminum to steel, titanium to carbon fiber, or even dissimilar plastics, laser welding accommodates diverse material combinations with exceptional seam quality. This flexibility positions laser welding as a preferred solution for industries seeking to optimize production processes, minimize material waste, and elevate the overall quality of welded components.
Advantages of Laser Welding Technology
The adoption of laser welding technology offers a multitude of advantages that significantly impact manufacturing efficiency, product quality, and cost-effectiveness. One of the primary benefits of laser welding is its ability to achieve high welding speeds while maintaining precision and control. The concentrated energy of the laser beam allows for rapid heating and cooling cycles, resulting in faster production rates compared to conventional welding methods. This accelerated process not only increases throughput but also reduces the overall manufacturing lead times, contributing to enhanced productivity and time-to-market for finished products.
The precise control and focus of the laser beam enable the creation of narrow and deep weld seams, ensuring minimal heat-affected zones and distortion in the surrounding material. This precision contributes to the production of high-quality welds with exceptional mechanical properties, such as improved strength, fatigue resistance, and corrosion resistance. The remarkable weld quality achieved through laser welding translates to superior product performance and longevity, making it an attractive choice for industries that demand flawless weld integrity.
In addition to speed and quality, laser welding offers a cost-effective solution by minimizing material waste and secondary processing requirements. The focused nature of the laser beam allows for precise material utilization, reducing the need for excessive filler materials or post-weld machining. This optimization of material usage not only contributes to cost savings but also supports sustainable manufacturing practices by minimizing material waste. Moreover, the ability to weld dissimilar materials with varying thicknesses eliminates the need for additional joining techniques, simplifying the manufacturing process and reducing overall production costs.
The non-contact nature of laser welding further enhances its advantages by eliminating the risk of physical distortion or contamination from welding electrodes or filler materials. This clean and precise welding process reduces the need for extensive post-weld cleaning and finishing, streamlining production processes and minimizing labor-intensive tasks. The overall reduction in secondary operations translates to cost savings and shorter production cycles, making laser welding a compelling choice for industries seeking to optimize their manufacturing operations.
Laser Welding Applications in Different Industries
The versatility and precision of laser welding technology have led to its widespread adoption across diverse industries, where the demand for high-quality, high-strength welded components is paramount. In the automotive industry, laser welding plays a pivotal role in the production of vehicle components, including body panels, exhaust systems, and structural elements. The ability to join dissimilar materials such as aluminum and steel with exceptional seam quality makes laser welding indispensable in lightweight vehicle construction, contributing to fuel efficiency and overall vehicle performance.
The aerospace industry also leverages laser welding for its ability to produce complex and lightweight components with uncompromising structural integrity. From aircraft fuselage assemblies to engine components, laser welding ensures the precision and reliability required for critical aerospace applications. The medical device industry benefits from laser welding’s capability to join biocompatible materials, such as titanium and stainless steel, with precision and cleanliness, meeting the stringent quality standards for implantable medical devices.
In the electronics industry, the demand for miniaturization and precision components has propelled the adoption of laser welding for joining delicate electronic assemblies. The ability to create intricate and reliable welds in microelectronics and semiconductor devices positions laser welding as an essential manufacturing technology for electronic components. Additionally, laser welding finds applications in the production of consumer electronics, where seamless and durable welds are crucial for device performance and longevity.
The burgeoning field of additive manufacturing, commonly known as 3D printing, also benefits from laser welding technology for joining metal parts created through additive processes. Laser welding enables the precise fusion of 3D-printed metal components, contributing to the production of complex and functional prototypes, tooling, and end-use parts. The versatility of laser welding extends to the jewelry and watchmaking industries, where intricate designs and precise joins are achieved with minimal heat impact, preserving the aesthetic and structural integrity of precious metals.
Types of Laser Welding
Laser welding encompasses various processes that cater to specific manufacturing requirements, each offering unique advantages in terms of speed, precision, and material compatibility. The two primary types of laser welding are conduction welding and keyhole welding, each suited for distinct applications and material thicknesses. Conduction welding, also known as heat conduction welding, operates at lower power levels and is suitable for thin materials and shallow weld penetration. This process relies on the gradual conduction of heat through the material thickness, resulting in a wider but shallower weld seam.
In contrast, keyhole welding, also referred to as deep penetration welding, utilizes higher power levels to create a focused laser beam that vaporizes and melts the material, forming a narrow and deep weld seam. Keyhole welding is particularly effective for thicker materials and complex joint configurations, offering deep penetration and exceptional weld strength. The choice between conduction welding and keyhole welding depends on the specific material properties, joint designs, and desired weld characteristics, allowing manufacturers to tailor the laser welding process to their precise requirements.
Another notable laser welding process is pulsed laser welding, which modulates the laser beam’s intensity to create controlled pulses of energy. This pulsing capability allows for precise control over the welding parameters, including heat input, cooling rates, and weld seam morphology. Pulsed laser welding is favored for applications that demand fine-tuned control over the welding process, such as micro-welding, thin material welding, and heat-sensitive material joining. The ability to adjust pulse parameters makes pulsed laser welding a versatile choice for achieving welds with minimal thermal distortion and exceptional precision.
Laser welding processes also encompass hybrid approaches that combine laser welding technology with other welding methods, such as arc welding or electron beam welding. These hybrid processes leverage the strengths of each welding technique to achieve synergistic effects, allowing for increased welding speeds, enhanced material compatibility, and improved joint quality. By integrating laser welding with complementary welding methods, manufacturers can address a wider range of production requirements while maintaining the precision and efficiency synonymous with laser welding technology.
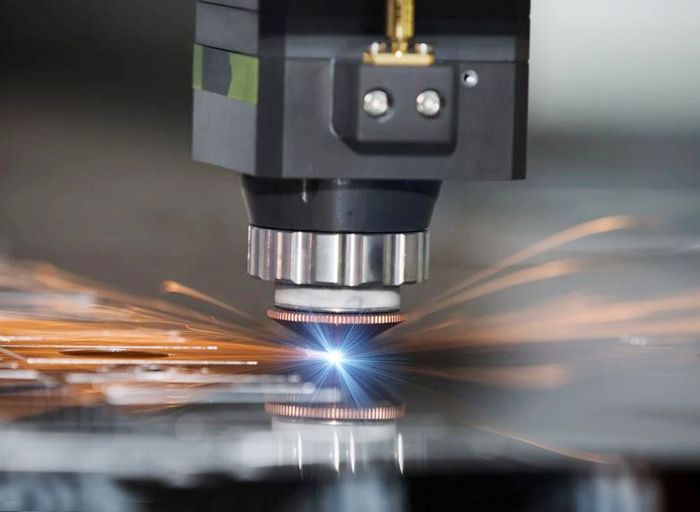
Photos: medicaldevice-network
Factors to Consider in Laser Welding
The successful implementation of laser welding technology relies on a comprehensive understanding of the factors that influence the welding process, ensuring optimal results and consistent weld quality. Material compatibility is a critical consideration in laser welding, as different materials exhibit varying responses to laser energy, absorption, and thermal conductivity. Understanding the material properties, such as reflectivity, absorption coefficient, and melting characteristics, is essential for selecting the appropriate laser parameters and optimizing the welding process for specific material combinations.
The joint design and fit-up play a crucial role in laser welding, influencing the accessibility of the laser beam to the joint and the overall weld quality. Proper joint preparation, including edge quality, fit-up tolerances, and clamping arrangements, is imperative for ensuring seamless laser welding without compromising joint integrity. Additionally, the orientation of the laser beam relative to the joint geometry and material thickness affects the weld penetration, heat distribution, and overall weld quality, necessitating meticulous consideration of joint configurations during process planning.
Laser welding parameters, including power density, pulse duration, beam focus, and travel speed, require precise calibration to achieve the desired weld characteristics and seam quality. The selection of laser parameters is contingent on the material thickness, joint configuration, and production requirements, demanding thorough process development and optimization to achieve consistent and reliable welds. Furthermore, the control of shielding gases and atmosphere during laser welding is essential for minimizing oxidation, porosity, and contamination in the weld zone, preserving the integrity of the welded joint and the material properties.
The integration of monitoring and control systems is instrumental in ensuring the reliability and repeatability of laser welding processes. Real-time monitoring of key welding parameters, such as temperature, seam quality, and weld bead morphology, enables immediate adjustments to optimize the welding process and mitigate potential defects. The implementation of closed-loop control systems further enhances the precision and consistency of laser welding, providing adaptive feedback and correction to maintain optimal weld quality throughout the production cycle.
Choosing the Right Laser Welding Equipment
The selection of laser welding equipment is a pivotal decision that directly impacts the quality, efficiency, and versatility of the welding processes. The choice between fiber lasers, disk lasers, and CO2 lasers depends on the specific application requirements, material compatibility, and production scale. Fiber lasers, characterized by their high beam quality, compact footprint, and energy efficiency, are well-suited for precision welding, micro-welding, and high-speed production environments. Their ability to deliver concentrated energy with exceptional control makes fiber lasers an ideal choice for a wide range of material thicknesses and joint configurations.
Disk lasers, renowned for their high power output and robustness, excel in applications that demand deep penetration welding, thick material welding, and high-speed production. The superior beam quality and energy stability of disk lasers make them a preferred solution for automotive, aerospace, and heavy industries where stringent weld quality and productivity requirements are paramount. CO2 lasers, known for their versatility, long wavelength, and capability to weld non-metallic materials, find applications in industries that require precision cutting, engraving, and welding of organic materials, such as plastics, ceramics, and composites.
The integration of robotic systems and automation solutions enhances the efficiency and repeatability of laser welding processes, allowing for precise positioning of the laser beam and workpieces. Robotic laser welding systems offer flexibility in handling complex joint geometries, multi-axis welding paths, and seamless integration with manufacturing workflows. By leveraging robotic automation, manufacturers can achieve consistent and high-throughput laser welding operations, optimizing production efficiency and minimizing manual intervention.
The availability of advanced software for process simulation, programming, and control further elevates the capabilities of laser welding equipment, enabling predictive modeling of welding outcomes, optimization of laser parameters, and real-time monitoring of welding processes. The seamless integration of software solutions with laser welding systems empowers manufacturers to anticipate and address potential welding challenges, ensuring the achievement of superior weld quality and production efficiency.
Safety Measures in Laser Welding
Ensuring the safety of personnel and the integrity of the work environment is paramount in laser welding operations, given the high-energy nature of laser beams and the potential hazards associated with laser radiation. Implementing comprehensive safety measures and protocols is essential for mitigating risks and maintaining a secure working environment. Personal protective equipment (PPE), including laser safety glasses, face shields, and protective clothing, is mandatory for personnel involved in laser welding activities, providing essential protection against direct or reflected laser radiation.
The establishment of restricted access zones and safety interlocks around laser welding equipment prevents unauthorized personnel from exposure to laser radiation, minimizing the risk of accidental eye injuries or skin burns. Clear signage, warning lights, and audible alarms further contribute to the visibility and awareness of laser welding areas, ensuring that all individuals within the vicinity are cognizant of the potential laser hazards. The implementation of administrative controls, such as standardized operating procedures, safety training, and hazard assessments, fosters a culture of safety awareness and compliance among personnel engaged in laser welding activities.
The proper maintenance and calibration of laser welding equipment, including beam delivery systems, shielding gas supply, and safety interlocks, are instrumental in ensuring the consistent and safe operation of the equipment. Regular inspections, maintenance schedules, and adherence to manufacturer’s recommendations contribute to the longevity and reliability of laser welding systems, minimizing the risk of equipment malfunctions or safety breaches. Emergency protocols and response plans, including first-aid procedures, evacuation routes, and emergency shutdown protocols, provide a structured approach to addressing unforeseen incidents and safeguarding personnel in the event of a laser-related emergency.
Occupational exposure limits (OELs) for laser radiation, as defined by regulatory agencies, serve as guidelines for establishing safe exposure levels and implementing control measures to protect personnel from excessive laser radiation. Compliance with OELs necessitates the implementation of engineering controls, such as laser beam enclosures, interlocked workstations, and exhaust ventilation, to minimize the potential for laser exposure and ensure a safe working environment. Periodic monitoring of ambient laser radiation levels and the implementation of control measures based on exposure assessments contribute to the ongoing safety and compliance of laser welding operations.
Training and Certifications in Laser Welding
The proficiency and expertise required for successful laser welding operations are acquired through comprehensive training programs and certifications that equip personnel with the knowledge, skills, and safety awareness essential for performing laser welding tasks. Basic training in laser safety, including the principles of laser radiation, hazard awareness, and personal protective measures, forms the foundational knowledge for individuals entering the field of laser welding.
Understanding the potential risks associated with laser radiation and the importance of adhering to safety protocols is paramount for ensuring the well-being of personnel engaged in laser welding activities.
Final Thoughts
Overall, laser welding technology has become increasingly popular due to its source of precision and numerous benefits. Its use goes beyond repair or the medical field but can be used in many different industries such as the automotive space. Laser welding continues to be a game-changer thanks to its accuracy and affordability. As this form of manufacturing technology strengthens its dominion in the marketplace, it is easy to see that this method of welds will remain an essential scientific technology tool for years to come. If you’re interested in learning more about laser welding or getting some insight into implementing welding within your own organization, reach out today — we did love nothing more than to help!