In the fast-evolving landscape of medical device manufacturing, the integration of advanced technologies has become paramount in meeting the increasingly complex demands for precision, durability, and safety. Among these technologies, laser welding has emerged as a game-changing method, revolutionizing the fabrication process of medical devices. With its unparalleled accuracy, minimal heat impact, and ability to fuse intricate components with utmost precision, laser welding has redefined the standards of quality and reliability in medical device assembly.
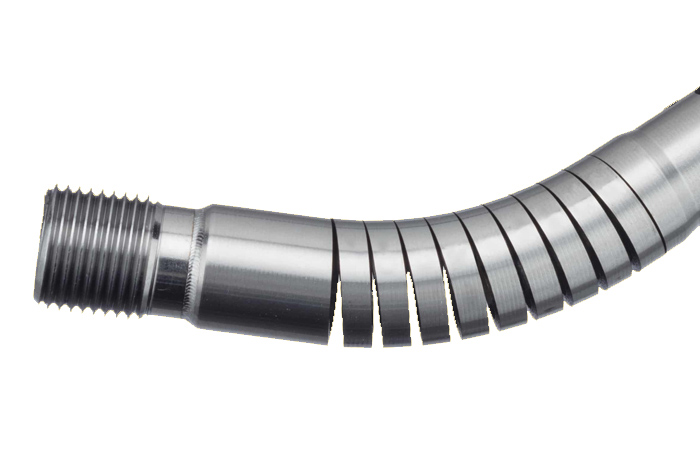
Image: okayind.com
Advantages of Laser Welding Medical Devices
Laser welding offers a multitude of advantages that make it indispensable in the production of medical devices. Unlike traditional welding methods, laser welding generates minimal thermal distortion, making it ideal for joining small, delicate components without compromising their integrity. The non-contact nature of laser welding minimizes the risk of contamination, ensuring the sterility of medical devices, a critical factor in the healthcare industry. The precision and narrow heat-affected zone of laser welding result in minimal impact on surrounding tissues or materials, making it especially suitable for fabricating devices intended for medical implantation or direct patient contact.
Laser welding enables the creation of seamless, high-strength joints with exceptional aesthetic appeal, a crucial factor in medical device manufacturing where precision and visual appeal are equally important. By producing consistent, reliable welds, laser welding enhances the overall performance and longevity of medical devices, meeting the stringent quality standards of the healthcare industry and instilling confidence in both manufacturers and end-users.
The adaptability of laser welding to a wide range of materials, including stainless steel, titanium, and various alloys commonly used in medical device fabrication, makes it a versatile and cost-effective method for producing diverse devices, from surgical instruments to implantable components.
Types of Laser Welding Medical Devices
The application of laser welding medical devices industry spans across a diverse range of products, showcasing its versatility and efficacy in fabricating various instruments and components critical to modern healthcare. Surgical instruments, such as forceps, scissors, and needle holders, benefit from the precision and cleanliness of laser welding, ensuring their functionality and longevity in surgical settings. In addition, laser welding plays a vital role in the production of implantable medical devices, such as orthopedic implants, dental implants, and vascular stents, where the integrity of the welds directly impacts patient safety and device performance.
Laser welding is widely utilized in assembling diagnostic devices, including endoscopes, ultrasound probes, and blood glucose monitors, where the fusion of intricate components demands utmost precision and reliability. The inherent ability of laser welding to join dissimilar materials further expands its application to devices comprising multiple materials, such as catheters, where the compatibility of materials and the integrity of welds are paramount to the device’s functionality and safety.
Laser Welding Process for Medical Devices
The laser welding process for medical devices involves a series of meticulously controlled steps to ensure the precise fusion of components while upholding the highest standards of quality and safety. The process begins with the selection of an appropriate laser source, such as a fiber laser or a pulsed laser, based on the specific material and design requirements of the medical device being fabricated. The laser parameters, including power, pulse duration, and frequency, are carefully calibrated to achieve optimal weld strength and aesthetic finish, minimizing any potential impact on the surrounding material.
Subsequently, the components to be welded are meticulously aligned and fixtured to ensure precise positioning and stable fit-up during the welding process. The laser beam is then focused on the joint area, generating a localized heat source that rapidly melts the material and forms a strong, seamless bond between the components. Advanced monitoring and control systems, including real-time temperature sensors and automated feedback mechanisms, are employed to maintain the integrity and consistency of the weld throughout the process.
Post-welding, the assembled components undergo thorough inspection and testing to verify the quality and integrity of the welds, ensuring that they meet the stringent regulatory standards and performance requirements of medical devices. This comprehensive approach to the laser welding process not only ensures the precision and reliability of the fabricated medical devices but also underscores the commitment to delivering safe, high-quality products to the healthcare industry and, ultimately, to the patients.
Quality Control and Regulations in Medical Device Laser Welding
Quality control and adherence to regulatory standards are paramount in the fabrication of medical devices laser welding, given the critical nature of these instruments in healthcare settings. Stringent quality control measures are implemented throughout the entire manufacturing process, from material selection and component fabrication to the final assembly through laser welding. This includes comprehensive material testing, weld qualification, and non-destructive testing techniques, such as X-ray inspection and ultrasonic testing, to ensure the integrity and reliability of the welds.
Laser welding medical devices is subject to rigorous regulatory oversight, with stringent standards set forth by regulatory bodies such as the U.S. Food and Drug Administration (FDA) and the International Organization for Standardization (ISO). Manufacturers are required to adhere to specific guidelines and standards, such as ISO 13485 for quality management systems and ISO 14971 for risk management in medical devices, to ensure the safety, efficacy, and traceability of laser-welded medical devices.
Compliance with these regulations not only underscores the commitment to delivering safe and reliable medical devices but also instills confidence in healthcare professionals and patients, assuring them of the quality and performance of the laser-welded devices they rely on for patient care.
Case Studies of Successful Laser Welding Medical Devices
The transformative impact of laser welding medical devices fabrication is exemplified through numerous case studies showcasing the successful application of this technology in producing critical healthcare instruments and components. One such example is the fabrication of vascular stents, where the precision and consistency of laser welding play a pivotal role in ensuring the structural integrity and biocompatibility of the stent, essential for its effectiveness in treating vascular diseases.
Another compelling case study lies in the production of orthopedic implants, where laser welding facilitates the assembly of intricate components with unmatched precision, contributing to the longevity and functionality of the implants in orthopedic surgeries. Additionally, the assembly of diagnostic devices, such as ultrasound probes, benefits from the cleanliness and accuracy of laser welding, ensuring the reliability and performance of these essential diagnostic tools in clinical settings.
These case studies underscore the indispensable role of laser welding in the fabrication of a wide array of medical devices, from life-saving implantable devices to diagnostic instruments, and serve as a testament to the technology’s capacity to meet the exacting standards of the healthcare industry while advancing patient care and treatment outcomes.
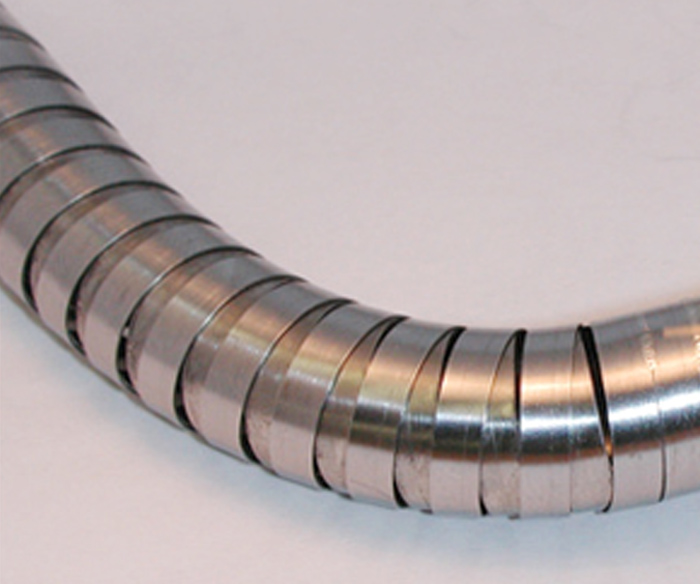
Image: laserstar.net
Future Trends in Laser Welding Medical Devices
As technology continues to evolve, the future of laser welding in medical device fabrication holds promising advancements and innovations that are poised to further enhance the precision, efficiency, and versatility of this critical manufacturing process. One such trend is the continued refinement of laser sources and beam delivery systems, leading to increased power, speed, and control, enabling the fabrication of even more intricate and complex medical devices with unprecedented precision and speed.
The integration of advanced robotics and automation in laser welding processes is expected to streamline production, reduce cycle times, and enhance repeatability, ensuring consistent quality and performance in the fabrication of medical devices. The development of novel laser welding techniques, such as hybrid laser welding and additive manufacturing with laser deposition, presents opportunities to expand the application of laser welding to new materials and device designs, further broadening its impact on the medical device industry.
The integration of digitalization and data analytics in laser welding processes will enable real-time monitoring, predictive maintenance, and quality assurance, optimizing the efficiency and reliability of medical device fabrication. These future trends in laser welding medical devices not only signify the ongoing evolution of this technology but also underscore its pivotal role in shaping the future of medical device manufacturing, driving innovation, and ensuring the delivery of safe, high-quality devices to patients in need.
Training and Certification for Laser Welding Medical Devices
The proficiency and expertise required for laser welding medical devices industry necessitate comprehensive training and certification programs to ensure the competence and compliance of personnel involved in the fabrication and assembly of medical devices. Training programs encompass a broad spectrum of topics, including laser safety, welding techniques, material compatibility, quality control, and regulatory requirements specific to the medical device industry.
Certification for laser welding in the medical device industry serves as a testament to the individual’s proficiency and adherence to industry standards, providing manufacturers, regulatory bodies, and end-users with the assurance of the welder’s capability to produce high-quality, reliable welds conforming to the stringent requirements of the healthcare industry.
Additionally, ongoing education and training initiatives are essential to keep abreast of the latest advancements in laser welding technology, regulatory updates, and best practices, ensuring the continued competence and compliance of personnel involved in the fabrication of medical devices.
Choosing the Right Laser Welding Equipment for Medical Device Manufacturing
The selection of appropriate laser welding equipment is a critical consideration in the fabrication of medical devices, as it directly impacts the quality, precision, and efficiency of the welding process. Factors such as laser type, power output, beam quality, pulse duration, and beam delivery systems play a pivotal role in determining the suitability of the equipment for specific medical device applications. Manufacturers must carefully evaluate their production requirements, material compatibility, and regulatory standards to select the most suitable laser welding equipment that aligns with their fabrication needs and quality objectives.
The integration of advanced features, such as real-time monitoring, automated control systems, and user-friendly interfaces, enhances the reliability and repeatability of the welding process, contributing to the consistent production of high-quality medical devices.
Considerations for equipment maintenance, service support, and long-term reliability are imperative in ensuring uninterrupted production and adherence to regulatory requirements, underscoring the significance of choosing the right laser welding equipment for medical device manufacturing.
Conclusion and the Future of Laser Welding in Medical Device Production
The transformative impact of laser welding medical devices fabrication is undeniable, revolutionizing the standards of precision, reliability, and safety in the healthcare industry. As technology continues to advance, the future of laser welding holds promising advancements and innovations that are poised to further elevate the capabilities and impact of this critical manufacturing process. With its unparalleled accuracy, minimal heat impact, and ability to meet the stringent regulatory standards governing the medical industry, laser welding stands as a testament to the unwavering commitment to delivering safe, high-quality medical devices to patients in need.
As the landscape of medical device manufacturing continues to evolve, the integration of advanced technologies, comprehensive training and certification programs, and the careful selection of laser welding equipment are imperative in ensuring the continued excellence and innovation in the fabrication of medical devices. By embracing the transformative potential of laser welding and staying at the forefront of advancements in this critical technology, manufacturers can uphold the highest standards of quality, reliability, and safety, ultimately advancing patient care and treatment outcomes in the healthcare industry.
In conclusion, the future of laser welding medical devices production is characterized by ongoing innovation, refinement, and a steadfast commitment to excellence, driving the continual advancement of medical device fabrication and the delivery of life-saving instruments to patients worldwide.