Laser welding aluminum has emerged as a game-changing technology in the manufacturing industry, offering a highly precise and efficient method for joining aluminum components. This advanced technique has reshaped the way aluminum is utilized across various sectors, delivering unparalleled benefits such as high welding speeds, minimal heat-affected zones, and exceptional weld quality. As the demand for lightweight and durable materials continues to rise, laser welding aluminum has positioned itself as an indispensable solution for achieving robust and reliable aluminum joints.
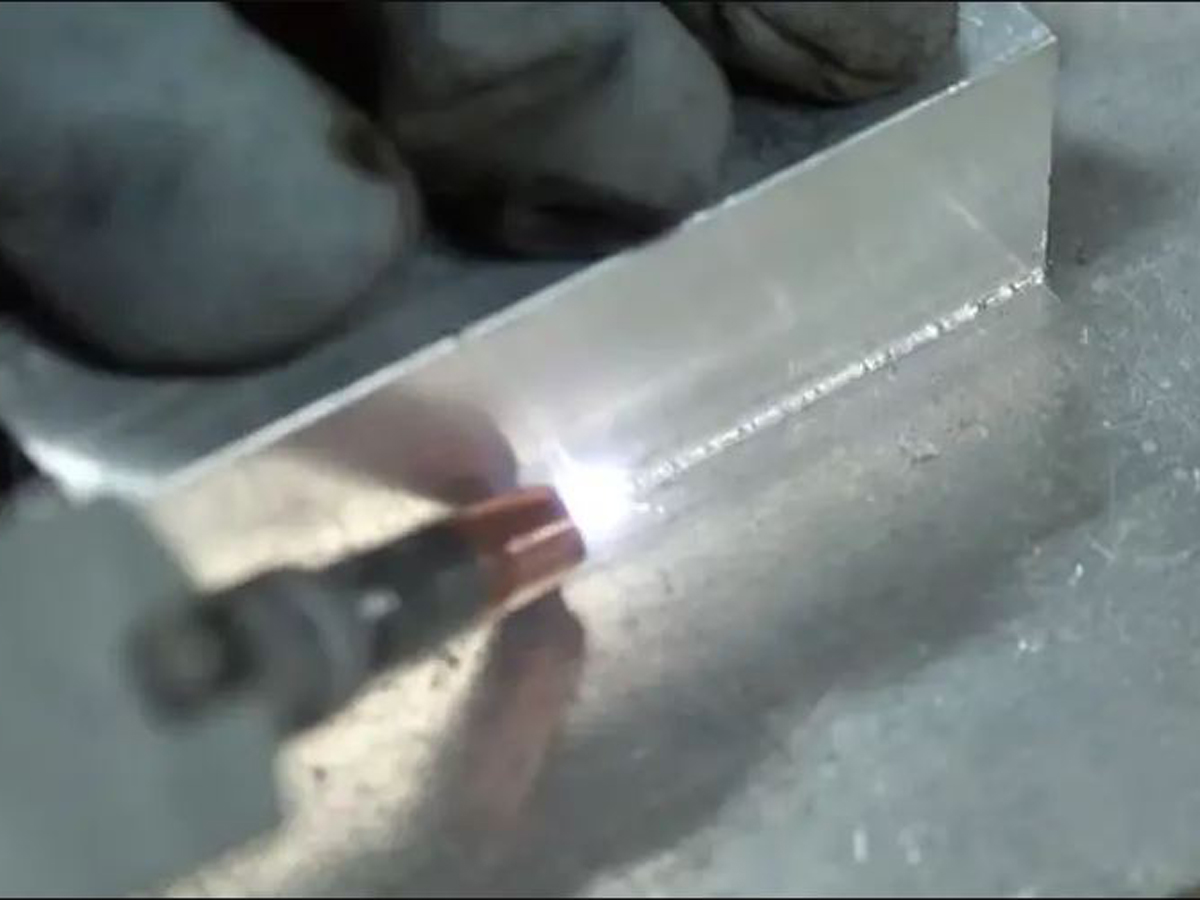
Photo by diodelaphotonics5578 on YT
Understanding Laser Welding and Its Applications
Laser welding is a process that utilizes a concentrated beam of light energy to create a fusion weld. When applied to aluminum, this method enables the joining of intricate designs and complex configurations with remarkable precision. The versatility of laser welding makes it well-suited for a wide range of applications, particularly in industries that demand high precision and efficiency, such as automotive, aerospace, and electronics. The ability to weld aluminum with intricate geometries and thin materials has opened up new design possibilities and manufacturing efficiencies, making laser welding an invaluable tool in modern production processes.
The use of high-power lasers and advanced optics in laser welding aluminum allows for the creation of joints that exhibit superior strength and integrity. With the capability to achieve weld penetration depths far exceeding traditional welding methods, laser welding offers manufacturers the flexibility to explore innovative designs and complex assemblies that were previously unattainable.
Advantages of Laser Welding Aluminum
One of the primary advantages of laser welding aluminum is the high welding speeds it offers. The concentrated heat source and precise control of the laser beam result in rapid welding processes, leading to increased productivity and reduced manufacturing cycle times. Laser welding produces minimal heat-affected zones, which helps to preserve the integrity of the base material and minimize distortion, leading to higher quality welds.
Another significant advantage lies in the ability of laser welding to create strong, reliable joints in aluminum components. The high energy density of the laser beam allows for deep penetration and effective fusion, resulting in welds that exhibit exceptional strength and durability. This is particularly crucial in industries such as aerospace and automotive, where the structural integrity of components is paramount to ensure safety and performance.
Laser welding aluminum offers excellent control over the welding process, enabling precise manipulation of parameters such as power, speed, and focus. This level of control contributes to the production of consistent, high-quality welds, reducing the need for post-welding rework and enhancing overall manufacturing efficiency.
Disadvantages of Laser Welding Aluminum
Longer welding time – Since aluminum doesn’t conduct heat well, you have to use a longer wavelength laser to create a weld that won’t break. This means that you have to position the parts much more precisely and have to focus your attention on the welding process.
Difficulty in joining irregular shapes – Welding aluminum is usually done on a flat surface. This means that you have to join irregular shapes, such as tubes or round holes, with different types of joints.
Greater cost than joining two sheets of steel – As mentioned above, aluminum welding usually costs more than joining two sheets of steel, since many of the components used in welding aluminum, such as the laser diode, are designed for aluminum.
More pollution than welding steel – The laser beam creates more pollution than the electric arc when welding steel.
Challenges and Considerations in Laser Welding Aluminum
While laser welding aluminum presents numerous advantages, it also comes with its own set of challenges and considerations. One of the primary challenges is the high reflectivity of aluminum, which can result in a significant portion of the laser energy being reflected instead of being absorbed for welding. To address this, specialized laser sources and optics are employed to optimize energy absorption and enhance the welding process.
The thermal conductivity of aluminum necessitates careful management of heat input during the welding process. Excessive heat can lead to distortion and metallurgical changes in the base material, affecting the mechanical properties of the welded joints. Therefore, precise control of laser parameters and optimized welding strategies are crucial to mitigate these challenges and ensure the production of high-quality aluminum welds.
Furthermore, the selection of suitable filler materials and shielding gases is essential to achieve optimal weld characteristics and minimize the formation of defects. Proper joint design and preparation also play a pivotal role in overcoming the challenges associated with laser welding aluminum, as they influence the overall weld quality and integrity.
Laser Welding Aluminum Processes and Techniques
Laser welding aluminum encompasses various processes and techniques, each tailored to specific applications and welding requirements. One of the common techniques is conduction mode welding, which utilizes lower laser power levels to produce shallow welds suitable for thin aluminum sheets and delicate components. This technique is characterized by its ability to minimize heat input and distortion, making it ideal for applications where precise control over the welding process is crucial.
On the other hand, keyhole mode welding involves higher laser power levels to create deep penetration welds in thicker aluminum materials. This technique is employed for applications that demand superior weld strength and robustness, such as structural components in aerospace and automotive assemblies. The keyhole mode welding process enables the formation of full-penetration welds with exceptional fusion and minimal heat-affected zones, ensuring the integrity of the welded joints.
Pulsed laser welding represents another technique used in aluminum welding, offering precise control over energy input and weld pool dynamics. This technique is advantageous for applications that require fine-tuned welding parameters and the ability to accommodate varying material thicknesses and joint configurations. By adjusting the pulse duration and frequency, manufacturers can achieve tailored weld characteristics that meet the specific requirements of their aluminum components.
Equipment and Technology for Laser Welding Aluminum
The successful implementation of laser welding aluminum hinges upon the utilization of advanced equipment and technology designed to optimize the welding process. High-power fiber lasers, equipped with cutting-edge beam delivery systems, are commonly employed to provide the concentrated energy required for efficient aluminum welding. These lasers offer exceptional beam quality and stability, ensuring precise control over the welding process and consistent weld quality.
In addition to laser sources, advanced optics and beam delivery systems play a crucial role in shaping and focusing the laser beam to achieve the desired weld characteristics. The integration of automated systems and robotics further enhances the efficiency and repeatability of laser welding processes, allowing for seamless integration into modern manufacturing environments.
The development of real-time monitoring and control systems has revolutionized the way laser welding aluminum is executed. These systems enable continuous assessment of key welding parameters, such as laser power, travel speed, and gas flow, providing valuable feedback to optimize the welding process and maintain the integrity of the welds. By leveraging these technological advancements, manufacturers can achieve unparalleled precision and consistency in their laser welding operations.
Quality Control in Laser Welding Aluminum
Ensuring the quality of laser-welded aluminum components is essential to meet stringent industry standards and performance requirements. Implementing comprehensive quality control measures throughout the welding process is crucial to validate the integrity and reliability of the welded joints. Non-destructive testing techniques, such as visual inspection, ultrasonic testing, and radiographic examination, are employed to detect any defects or discontinuities that may compromise the weld quality.
The use of advanced inspection technologies, such as laser profilometry and thermal imaging, provides valuable insights into the weld characteristics and integrity, allowing for real-time assessment and validation of the welding process. By leveraging these advanced quality control methods, manufacturers can ensure that their laser-welded aluminum components meet the highest standards of quality and performance, instilling confidence in the end-users and stakeholders.
Applications and Industries Using Laser Welding Aluminum
The versatility and precision of laser welding aluminum have positioned it as a critical technology in a diverse range of industries. In the automotive sector, laser-welded aluminum components are widely utilized in the production of lightweight structures, body panels, and chassis components, contributing to improved fuel efficiency and vehicle performance. The ability to achieve high-strength welds with minimal distortion makes laser welding an ideal solution for joining aluminum alloys in automotive applications.
In the aerospace industry, laser welding aluminum plays a pivotal role in the fabrication of aircraft components, ranging from structural elements to intricate assemblies. The exceptional weld quality and integrity offered by laser welding make it instrumental in ensuring the reliability and safety of aerospace structures, where the demand for lightweight materials and high-performance alloys is paramount.
Moreover, the electronics industry leverages laser welding aluminum for the assembly of intricate components and heat-sensitive materials, where traditional welding methods may pose challenges. The precise control and minimal heat input of laser welding enable the production of delicate electronic assemblies with minimal impact on the surrounding materials, meeting the stringent requirements of modern electronic devices.
The adoption of laser welding aluminum extends to industries such as marine engineering, renewable energy, and consumer electronics, where the demand for lightweight, durable, and high-performance materials continues to drive innovation and advancement. As the technology and capabilities of laser welding aluminum continue to evolve, its applications across various industries are expected to expand, further solidifying its position as a cornerstone of modern manufacturing.
Training and Certification in Laser Welding Aluminum
As the demand for laser-welded aluminum components grows, the need for skilled professionals proficient in laser welding techniques becomes increasingly pronounced. Training and certification programs tailored to laser welding aluminum equip individuals with the knowledge and expertise required to execute complex welding processes and ensure the production of high-quality aluminum welds.
Comprehensive training programs cover fundamental principles of laser welding, including laser safety, process optimization, and equipment operation. Hands-on practical training allows participants to gain proficiency in setting up welding parameters, troubleshooting common issues, and executing welds with precision and consistency. Additionally, specialized training in aluminum welding techniques, joint design, and material selection provides participants with the necessary skills to address the unique challenges associated with welding aluminum alloys.
Certification in laser welding aluminum serves as a testament to an individual’s proficiency and competence in executing aluminum welding processes to industry standards. Employers across various sectors place value on certified welders, recognizing their ability to deliver high-quality welds and uphold stringent quality requirements. Furthermore, ongoing professional development and continuous education ensure that certified welders remain abreast of the latest advancements and best practices in laser welding aluminum, further enhancing their expertise and marketability.
Choosing the Right Laser Welding Aluminum Service Provider
Selecting the right laser welding aluminum service provider is critical to the success of manufacturing operations that rely on high-quality aluminum welds. When evaluating potential service providers, it is essential to consider their expertise in laser welding technology, as well as their track record in delivering precision welds and meeting stringent quality requirements. An established provider with a proven history of executing complex welding projects and upholding industry standards instills confidence in the quality and reliability of the welded components.
Assessing the provider’s capabilities in terms of equipment, technology, and quality control measures is crucial to ensuring that the welding processes align with the specific requirements of the intended applications. The integration of advanced monitoring and inspection systems, coupled with a robust quality management system, demonstrates the provider’s commitment to delivering consistent and high-quality welds.
Additionally, the ability of the service provider to offer comprehensive support, from initial design and prototyping to full-scale production, is indicative of their capability to meet the evolving needs of manufacturers across diverse industries. Collaborating with a service provider that offers end-to-end solutions and technical expertise in laser welding aluminum fosters a strategic partnership that drives innovation and excellence in aluminum welding applications.
Final Thoughts
Laser welding aluminum has undoubtedly transformed the landscape of modern manufacturing, offering a precise, efficient, and versatile method for joining aluminum components. The remarkable advantages of laser welding, including high welding speeds, minimal heat-affected zones, and exceptional weld quality, have positioned it as an indispensable technology across industries such as automotive, aerospace, and electronics.
As the demand for lightweight and durable materials continues to shape the manufacturing landscape, laser welding aluminum stands at the forefront of innovation, enabling the creation of intricate designs and complex assemblies with unparalleled precision and reliability. The evolution of laser welding technology, coupled with ongoing advancements in equipment, processes, and quality control measures, reinforces the pivotal role of laser welding aluminum in driving efficiency, performance, and sustainability in modern manufacturing.
Embracing the potential of laser welding aluminum and leveraging the expertise of skilled professionals and reputable service providers are pivotal steps in harnessing the full capabilities of this transformative technology. As industries continue to push the boundaries of design and performance, laser welding aluminum will undoubtedly remain a cornerstone of innovation, driving the development of lightweight, high-performance aluminum components that shape the future of manufacturing.