Laser spot welding is a widely used method of joining metal components. It has many advantages and can be used with almost any type of material. This article will talk about some key points about why laser spot welding is the best way to weld. Laser spot weld offers many benefits compared to traditional manual spot welding processes. It’s faster, easier, and produces better results often in less time than it took for manual spot welders to do the same thing. Let’s take a look at six key benefits of laser spot welding and why you should adopt this process over manual or other types of spot welding.
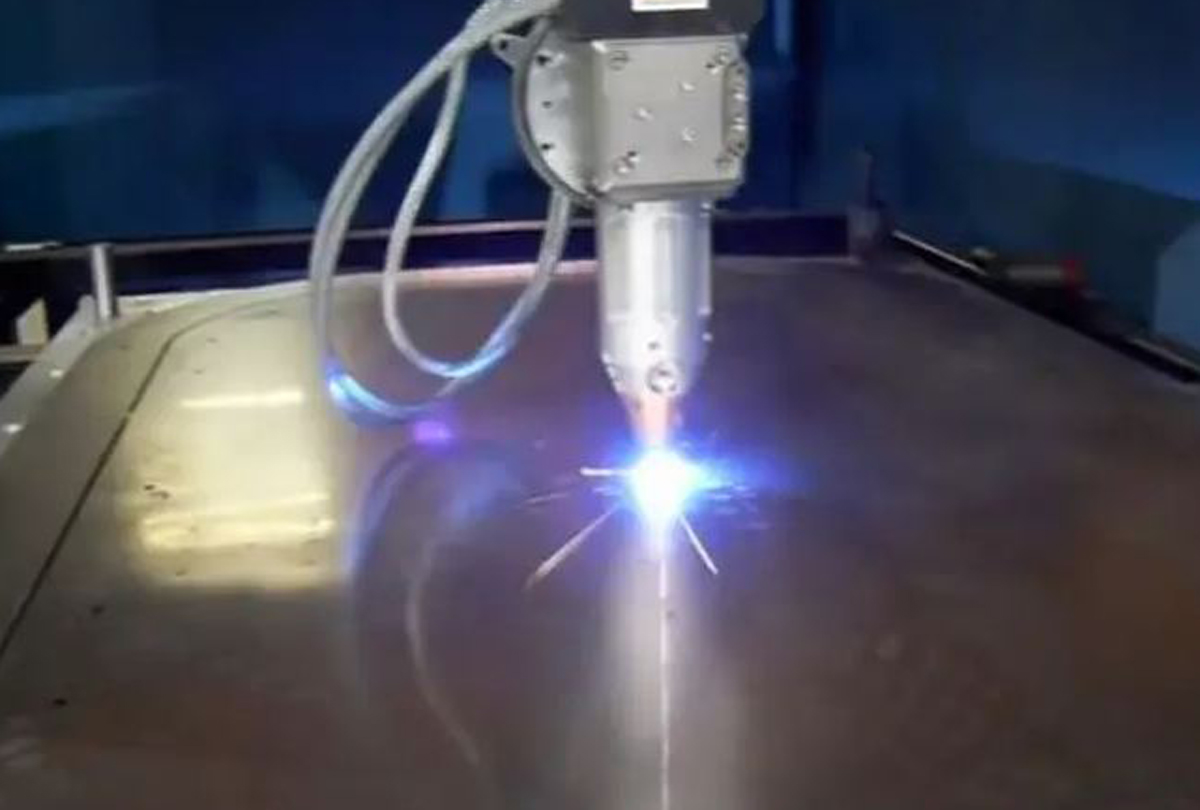
Photo by MDLInc
Faster Welding
Laser spot welding is extremely fast. In fact, it’s often claimed that you can weld cross-members together in a single day’s work, compared to the weeks or months that traditional spot welding would take. You could even weld the same components back to back without stopping, as you would need to do in manual spot welding. The two main reasons for the increased speed in laser spot welding are the high energy beam and the fact that the welding process occurs in a laser “beam line”. The laser beam heats up the workpiece, enabling it to be joined quickly with a high quality weld.
Easier And Robust Welding
Function specific welding is a growing trend, and one of the driving forces behind this design trend is the idea of welding “robust” components together. Welding “robust” components is the idea of welding parts that have been designed and manufactured to be strong and durable. In other words, you are looking to weld very heavy components together, like in a construction project, so the weld doesn’t have to withstand the weight of the components being welded together.
This can be done in laser spot welding with the use of a heavy laser beam and a robust welding electrode. With a laser beam that is powerful enough to melt a certain type of material, you can weld robust components together with ease.
Excellent Surface Finish
Another key benefit of laser spot welding is the excellent surface finish. Manual spot welding can leave a rough surface because it’s not done at a precise angle. The surface finish of the weld is dependent on the angle at which the weld is done. Laser spot weld does not have this problem because the beam is very precise. You can change the welding angle to get a smooth surface finish that is dependent on the angle at which the weld is done.
Unlike deformed welds made by traditional spot welding, the laser spot weld produces a perfectly flat surface weld that looks polished and is free from any scratches or gouges. This is because the beam is more precise and doesn’t produce a deformed weld.
No Edging Required
One of the main concerns of welders is the need to make a “good” weld and the need to mark out the weld area with a “bad” weld. This is true when welding by hand, but it’s something that you never have to think about when doing laser welding. Laser spot weld doesn’t produce a rough weld, but rather a smooth weld that leaves no edge. This is a huge advantage, especially when it comes to welding outside. You don’t need to make a “bad” weld inside the work area, then an “OK” weld outside the work area. You can make a perfect weld outside without an edge that you then have to edge.
No Splatter Or Fluid Markings
The final benefit of laser spot welding is its ability to produce no splatter or fluid markings. This is very important, especially when welding outdoors. The welds produced by conventional spot welding can leave a very messy look, with weld splatter and fluid markings on the surface. The welds made by laser welding do not have any of these problems. The welds are smooth and free from marks.
Final words about laser spot welding
Laser spot welding is a highly efficient and precise way to weld. It offers great flexibility and is ideal for welding robust components that would be difficult to weld manually. And it produces no splatter or fluid markings, perfect for welding outdoors. Let’s not forget the fact that it is also faster than manual spot welding. All of these benefits make this an excellent choice for welding when you need to weld components together quickly, reliably, and efficiently.
See Also
Welding on a Vehicle Frame: Tips and Tricks for Getting It Right