Laser micro welding has become a pivotal technology in the manufacturing industry, offering unmatched precision and efficiency. This advanced welding technique employs high-powered lasers to join tiny components with immaculate accuracy. It has transformed the production of intricate and delicate assemblies, making it a game-changer for industries that demand the highest level of precision in their manufacturing processes. The ability to focus heat with pin-point precision minimizes the heat-affected zone, resulting in cleaner, stronger welds on materials that were previously challenging to join using traditional welding methods.
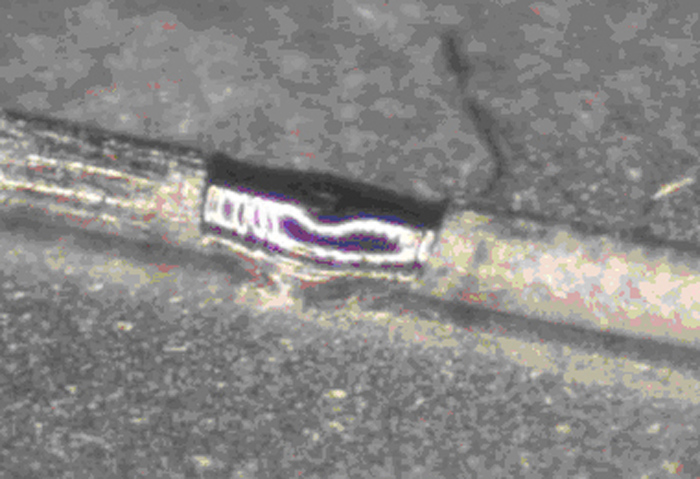
Image: laserstar.net
Understanding the Process
Laser micro welding is a specialized form of welding that utilizes a concentrated beam of light to create a high-temperature, localized weld joint. This process is particularly well-suited for joining small, delicate, or hard-to-reach components. The precision and control offered by laser micro welding make it an indispensable tool for industries that require intricate and high-quality welds.
The process involves directing the laser beam onto the workpiece, causing the material to melt and form a weld pool, which then solidifies to create a strong bond. Laser micro welding is highly versatile and can be used to join a wide range of materials, including metals, alloys, and even dissimilar materials. This capability makes it an attractive option for manufacturers across various industries.
Laser micro welding offers several advantages over traditional welding methods. One of the key benefits is its ability to produce minimal distortion in the welded components. This is particularly important for delicate or sensitive parts where heat distortion could compromise the integrity of the final product.
The precise control of the laser beam allows for exceptionally small weld sizes, making it ideal for applications requiring fine detail and accuracy. The minimal heat-affected zone also contributes to the overall quality of the weld, resulting in stronger and more reliable joints. Furthermore, the non-contact nature of the process reduces the risk of contamination, making it suitable for applications where cleanliness is paramount.
Advantages of Laser Micro Welding
The advantages of laser micro welding extend beyond the quality of the weld itself. The process is highly efficient, with rapid heating and cooling cycles that contribute to shorter production times. This efficiency translates to cost savings for manufacturers, as it reduces the overall energy consumption and labor required for welding operations.
Laser micro welding also offers environmental benefits, as the precise nature of the process minimizes material waste and reduces the need for post-welding finishing processes. Additionally, the ability to automate laser micro welding further enhances its efficiency, allowing for seamless integration into modern manufacturing systems.
Applications of Laser Micro Welding
The versatility of laser micro welding lends itself to a wide range of applications across various industries. In the electronics industry, this technology is used to create intricate connections in microelectronics, such as circuit boards and sensors. The medical device industry also benefits from laser micro welding, where it is employed to assemble tiny components for devices such as pacemakers, endoscopes, and surgical instruments. The automotive and aerospace sectors utilize laser micro welding for joining small, lightweight components, contributing to advancements in fuel efficiency and material optimization.
Furthermore, the jewelry and watchmaking industries rely on laser micro welding to create precise and intricate designs in precious metals. The applications of laser micro welding continue to expand as manufacturers discover new opportunities to leverage its capabilities for the production of high-precision components.
Types of Laser Micro Welding Techniques
Laser micro welding encompasses several techniques, each tailored to specific applications and material requirements. The most common techniques include conduction welding, keyhole welding, and pulsed laser welding. Conduction welding is well-suited for joining thin materials and offers excellent control over the welding process. Keyhole welding, on the other hand, is utilized for thicker materials and provides deeper penetration, making it suitable for applications requiring strong, robust welds.
Pulsed laser welding offers precise energy control, making it ideal for delicate materials and intricate designs. Each technique has its own set of advantages, allowing manufacturers to select the most suitable method based on their specific welding needs.
Factors to Consider When Choosing Welding System
Selecting the right laser micro welding system is crucial for achieving optimal results in precision manufacturing. Several factors must be considered when evaluating and choosing a system, including the power and wavelength of the laser, the control and automation capabilities, and the accessibility and flexibility of the system. The power and wavelength of the laser determine its suitability for different materials and welding depths, with higher power lasers being capable of welding thicker materials.
Control and automation features contribute to the overall precision and repeatability of the welding process, allowing for consistent results in high-volume production. Accessibility and flexibility considerations ensure that the system can accommodate a wide range of components and production setups, enhancing its versatility and usability.
Best Practices for Laser Micro Welding
Implementing best practices is essential for maximizing the benefits of laser micro welding. Proper preparation of the workpiece, including cleaning and positioning, is critical to ensure successful welds. Optimizing the laser parameters, such as power, pulse duration, and spot size, is crucial for achieving the desired weld characteristics. Maintaining a stable and controlled environment, including shielding gases and fixture stability, further enhances the quality and consistency of the welds.
It is also important to conduct thorough testing and validation of the welding process to identify and address any potential issues before full-scale production. Adhering to best practices not only ensures the quality of the welds but also contributes to the overall efficiency and reliability of the manufacturing process.
Common Challenges in Laser Micro Welding
While laser micro welding offers numerous benefits, it also presents certain challenges that manufacturers must address. One common challenge is the potential for porosity in the welds, especially when joining materials with high thermal conductivity. This can be mitigated through careful control of the welding parameters and the use of suitable filler materials. Another challenge is the potential for spattering and splashing of molten material, which can affect the integrity of the weld and lead to defects. Proper shielding and control of the welding environment can help minimize these issues.
Ensuring consistent joint fit-up and alignment is crucial for achieving precise and reliable welds, especially in applications with tight tolerances. Overcoming these challenges requires a thorough understanding of the welding process and the application of effective mitigation strategies.
Safety Considerations for Laser Micro Welding
Safety is paramount in any manufacturing process, and laser micro welding is no exception. The high-energy nature of the laser beam presents potential hazards, including exposure to intense light and heat. Proper training and adherence to safety protocols are essential for personnel working with laser micro welding systems. This includes the use of appropriate personal protective equipment, such as laser safety glasses, to protect against potential eye damage.
The establishment of controlled work areas with adequate ventilation and safety interlocks contributes to a safe working environment. Implementing thorough risk assessments and safety procedures ensures the well-being of personnel and the integrity of the manufacturing facility.
Future Trends in Laser Micro Welding
The future of laser micro welding holds exciting prospects for the manufacturing industry. Advancements in laser technology, including the development of more powerful and precise lasers, will further expand the capabilities of laser micro welding. This will enable the welding of a broader range of materials and the production of even smaller and more intricate components. Integration with digital manufacturing technologies, such as additive manufacturing and robotics, will enhance the automation and flexibility of laser micro welding systems, driving increased efficiency and productivity.
Ongoing research and development efforts are focused on optimizing laser process parameters and developing new welding techniques to address evolving industry requirements. The continued evolution of laser micro welding will undoubtedly shape the future of precision manufacturing, opening new frontiers for innovation and product development.
Conclusion
Laser micro welding represents a significant advancement in precision manufacturing, offering unparalleled accuracy, efficiency, and versatility. Its applications span across industries, from electronics and medical devices to automotive and aerospace, driving advancements in product miniaturization and quality. As manufacturers continue to seek innovative solutions for joining intricate and delicate components, laser micro welding has emerged as a critical process to meet these demands.
With ongoing technological advancements and a deepening understanding of its capabilities, laser micro welding is poised to play a pivotal role in shaping the future of manufacturing, enabling the production of increasingly complex and high-quality products.