When it comes to precision cutting, two popular methods often come to mind: laser cutting and plasma cutting. These techniques are widely used in various industries, from manufacturing to automotive, for their ability to produce precise and clean cuts. But what sets them apart? In this article, we will compare laser cutting and plasma cutting to help you understand their differences and determine which method suits your specific needs.
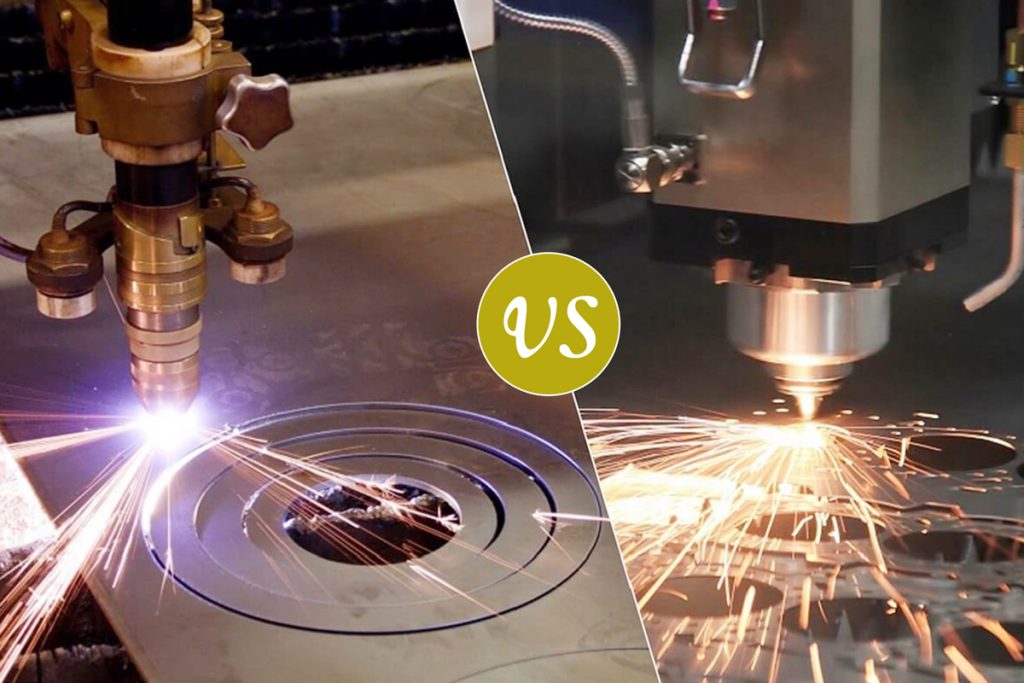
Differences between laser cutting vs plasma cutting
Laser cutting utilizes a high-powered laser beam to cut through a variety of materials, including metal, plastic, and wood. The laser beam is focused and directed onto the workpiece, melting or vaporizing the material in its path, resulting in a precise cut with a narrow kerf.
Plasma cutting, on the other hand, uses a high-velocity jet of ionized gas to melt and cut through conductive materials. The plasma arc is created by passing an electrical current through gas, which generates a high-energy plasma capable of piercing through various thicknesses.
Both laser cutting vs plasma cutting have their unique characteristics and advantages. Understanding these differences will help you make an informed decision for your cutting needs.
Advantages of laser cutting
Laser cutting offers several advantages that make it an attractive choice for many applications. Firstly, laser cutting provides high precision and accuracy, allowing for intricate and complex designs. The focused laser beam ensures a narrow kerf width, resulting in minimal material waste.
Another advantage of laser cutting is its versatility. Laser cutters can work with a wide range of materials, including metals, plastics, wood, and even fabrics. This flexibility makes laser cutting a popular choice for industries such as signage, jewelry, and automotive, where different materials need to be cut with precision.
Laser cutting is a non-contact process, meaning there is no physical force applied to the workpiece. This reduces the risk of material deformation or damage, especially for delicate materials. Laser cutting also produces clean and smooth cuts, eliminating the need for additional finishing processes.
Advantages of plasma cutting
While laser cutting excels in precision and versatility, plasma cutting offers its own set of advantages. One major advantage is the ability to cut through thick materials. Plasma cutting can easily pierce through materials with thicknesses of up to several inches, making it suitable for heavy-duty applications like shipbuilding and construction.
Plasma cutting is also a faster process compared to laser cutting, especially when dealing with thicker materials. The high-velocity plasma jet allows for rapid cutting speeds, resulting in increased productivity and efficiency. This makes plasma cutting an ideal choice for large-scale production environments.
Plasma cutting is relatively more cost-effective, especially for materials that are not highly reflective. Laser cutting can be more expensive due to the high cost of laser machines and maintenance. Plasma cutting systems, on the other hand, are generally more affordable and require less upkeep.
Limitations of laser cutting
Despite its numerous advantages, laser cutting does have a few limitations. One limitation is the inability to cut through highly reflective materials, such as copper and aluminum. The reflective properties of these materials cause the laser beam to bounce back, resulting in inefficient cutting or potential damage to the laser machine.
Laser cutting is not suitable for cutting materials that emit hazardous fumes when heated. Certain plastics and metals, such as PVC and galvanized steel, can release toxic gases when exposed to the high temperatures generated by the laser. Proper ventilation and safety measures are required when working with these materials.
Another limitation of laser cutting is the initial investment cost. Laser machines can be expensive, especially for small businesses or those with limited budgets. Maintenance and servicing costs should also be taken into consideration, as lasers require regular calibration and replacement of consumables.
Limitations of plasma cutting
While plasma cutting has its advantages, it also has a few limitations. One limitation is the wider kerf width compared to laser cutting. The plasma arc produces a wider cut, resulting in more material waste, especially when precision is crucial.
Plasma cutting is also not suitable for cutting non-conductive materials such as plastics and wood. Since plasma cutting relies on ionized gas and electrical conductivity, it cannot effectively cut through these materials. Laser cutting remains the better choice for working with non-conductive materials.
Plasma cutting can produce rougher edges compared to laser cutting. The high-velocity plasma jet can cause molten metal to splatter, resulting in uneven and jagged edges. This may require additional finishing processes to achieve the desired smoothness.
Factors to consider when choosing between laser cutting vs plasma cutting
When deciding between laser cutting vs plasma cutting, several factors should be considered. Firstly, the material type and thickness play a crucial role. Laser cutting is more suitable for thin and reflective materials, while plasma cutting excels in cutting thick and non-reflective materials. The desired level of precision is another important factor. Laser cutting offers higher precision and accuracy, making it ideal for intricate and detailed designs. Plasma cutting, on the other hand, may be more suitable for applications where precision is not the primary concern.
Budget and cost-effectiveness should also be taken into account. Laser cutting machines are generally more expensive upfront and require regular maintenance. Plasma cutting systems are more affordable and have lower maintenance costs, making them a cost-effective option for certain applications.
The intended application and production requirements should be considered. Laser cutting is often preferred for industries that require high precision and versatility, such as jewelry and automotive. Plasma cutting is favored in heavy-duty industries like shipbuilding and construction, where speed and thickness capabilities are crucial.
Applications of laser cutting
Laser cutting finds applications in a wide range of industries. In the automotive industry, laser cutting is used for precision cutting of metal components, such as body panels and exhaust systems. The jewelry industry utilizes laser cutting for intricate designs and precise gemstone settings. Signage companies rely on laser cutting for creating customized and detailed signs. Laser cutting is used in the medical field for fabricating surgical instruments and medical devices with high precision.
Applications of plasma cutting
Plasma cutting is commonly used in industries that require cutting through thick materials. Shipbuilding companies utilize plasma cutting for cutting steel plates and constructing ship hulls. Construction companies rely on plasma cutting for cutting metal beams and structural components. The HVAC industry utilizes plasma cutting for fabricating ductwork and ventilation systems. Furthermore, plasma cutting is used in the agricultural sector for manufacturing equipment such as plows and trailers.
Which cutting method is right for you?
Both laser cutting vs plasma cutting have their own advantages and limitations. Laser cutting offers high precision, versatility, and clean cuts, making it suitable for intricate designs and a wide range of materials. Plasma cutting excels in cutting thick materials, cost-effectiveness, and high cutting speeds, making it ideal for heavy-duty applications.
When choosing between laser cutting vs plasma cutting, consider factors such as material type and thickness, precision requirements, budget, and intended application. Assessing these factors will help you make an informed decision and select the cutting method that best suits your specific needs.