Do you have a titanium exhaust that needs welding? You have come to the right place! In this article, we will guide you through the process of welding titanium exhausts, ensuring you have all the information you need to get the job done right. Welding titanium can be a tricky task, but with the right techniques and tools, you can achieve a strong and durable weld. Whether you’re a seasoned welder or a DIY enthusiast, our step-by-step instructions will help you successfully weld your titanium exhaust. From preparing the surface to selecting the appropriate welding method, we will cover it all.
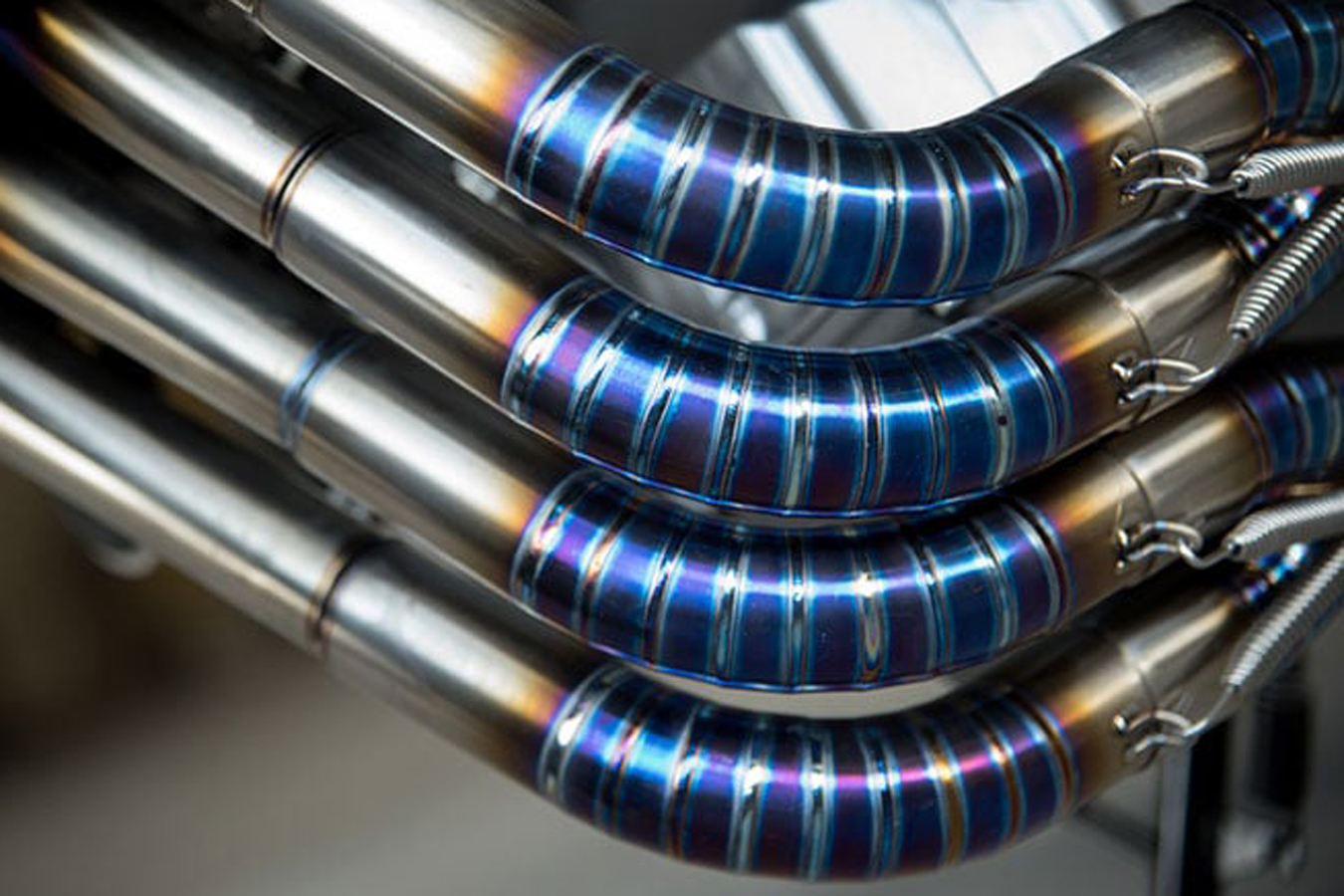
Understanding the Properties of Titanium
Before embarking on any welding project, it is crucial to have a good understanding of the material you’re working with. Titanium is a lightweight and strong metal that is commonly used in various industries, including automotive. It offers excellent corrosion resistance and can withstand high temperatures, making it an ideal choice for exhaust systems. However, titanium has unique properties that require special consideration when welding.
Firstly, titanium has a high melting point of around 3,000 degrees Fahrenheit, which means you need to use a welding technique suitable for this temperature range. Additionally, titanium has a low thermal conductivity, which makes it prone to warping and distortion during welding. To overcome these challenges, proper preparation, precise technique, and the right equipment are essential.
Safety Precautions for Welding Titanium
As with any welding project, safety should be your top priority when welding titanium exhausts. Titanium poses certain risks during welding, including exposure to harmful fumes and the risk of fire. To ensure your safety and the safety of those around you, follow these precautions:
- Work in a well-ventilated area or use a fume extraction system to remove welding fumes and prevent inhalation.
- Wear appropriate personal protective equipment (PPE), including a welding helmet, gloves, and a welding jacket.
- Keep a fire extinguisher within reach to quickly extinguish any sparks or fires.
- Ensure proper grounding for your welding equipment to prevent electrical hazards.
- Familiarize yourself with the Material Safety Data Sheet (MSDS) for the specific type of titanium you’re working with.
By taking these safety precautions, you can minimize the risks associated with welding titanium and create a safe working environment.
Tools and Equipment Needed for Welding Titanium Exhaust
To weld titanium exhausts, you’ll need the following tools and equipment:
- Tungsten Inert Gas (TIG) welding machine: TIG welding is the preferred method for welding titanium due to its precise control and low heat input.
- Argon gas: Argon is used as a shielding gas to protect the weld area from atmospheric contamination.
- Titanium filler rod: Use a filler rod specifically designed for titanium welding to ensure a compatible and strong weld.
- Welding helmet: Choose a helmet with a shade suitable for titanium welding to protect your eyes from harmful UV radiation.
- Welding gloves: Heat-resistant gloves are essential to protect your hands from burns and sparks.
- Welding clamps: Use clamps to hold the exhaust components in place during welding.
- Wire brush: Clean the titanium surface with a wire brush to remove any dirt, rust, or oxidation before welding.
Having the right tools and equipment will make the welding process smoother and help you achieve better results.
Choosing the Right Welding Method for Titanium Exhaust
When it comes to welding titanium exhausts, the TIG welding method is the most commonly used due to its precision and versatility. TIG welding involves creating an electric arc between a tungsten electrode and the workpiece, while simultaneously feeding the filler rod into the weld pool. This method provides excellent control over the welding process and allows for precise heat input, minimizing the risk of overheating and warping the titanium.
Another advantage of TIG welding is its ability to produce high-quality welds with minimal spatter. This is crucial when working with titanium, as any contaminants or imperfections can compromise the integrity of the weld. By using TIG welding, you can achieve clean and strong welds that will withstand the demanding conditions of an exhaust system.
Step-by-Step Guide to Welding Titanium Exhaust
Now that you have a good understanding of titanium properties, safety precautions, and the necessary tools, let’s dive into the step-by-step guide to welding titanium exhausts:
Step 1: Preparation – Clean the titanium surface using a wire brush to remove any dirt, rust, or oxidation. – Make sure the exhaust components fit together properly and use welding clamps to hold them in place during welding.
Step 2: Tungsten Electrode Selection – Choose a tungsten electrode suitable for titanium welding, such as pure tungsten or a tungsten alloy with a high percentage of tungsten. – Ensure the electrode is properly sharpened to create a focused and stable arc.
Step 3: Gas Shielding – Set up your TIG welding machine and connect the argon gas supply. – Adjust the flow rate to achieve adequate shielding of the weld area.
Step 4: Welding Technique – Position the TIG torch at a slight angle to the workpiece and establish an arc by making contact with the surface. – Maintain a consistent travel speed and create a small weld pool by adding the titanium filler rod as needed. – Move the torch along the joint, ensuring even heat distribution and complete fusion between the exhaust components.
Step 5: Post-Welding Inspection – Allow the weld to cool naturally and inspect it for any defects, such as cracks, porosity, or lack of fusion. – Use non-destructive testing methods, such as visual inspection or dye penetrant testing, to ensure the weld’s quality.
Tips for Achieving High-Quality Welds on Titanium Exhaust
While the step-by-step guide provides a solid foundation for welding titanium exhausts, here are some additional tips to help you achieve even better results:
- Practice on scrap titanium: Before welding your actual exhaust, practice on scrap pieces of titanium to get a feel for the material and perfect your technique.
- Control heat input: Titanium is sensitive to heat, so it’s crucial to maintain precise control over the heat input during welding. Avoid overheating the material, as it can lead to warping and distortion.
- Use back purging: If you’re welding a closed system, such as a titanium exhaust pipe, consider using back purging to prevent oxidation on the inside. This involves flowing argon gas through the pipe during welding.
- Maintain cleanliness: Titanium is highly reactive, so it’s essential to keep the weld area and filler rod clean throughout the welding process. Any contaminants can compromise the integrity of the weld.
By implementing these tips, you can enhance the quality of your welds and ensure the longevity of your titanium exhaust.
Troubleshooting Common Welding Issues with Titanium Exhaust
Even with proper technique and preparation, welding titanium exhausts can sometimes present challenges. Here are some common issues you may encounter and how to troubleshoot them:
- Porosity: Porosity refers to the presence of small holes or voids in the weld. It can be caused by contamination or inadequate gas shielding. Ensure the weld area is clean and increase the gas flow rate to improve shielding.
- Cracking: Cracks can occur due to excessive heat or rapid cooling. Control the heat input and allow the weld to cool naturally to minimize the risk of cracking.
- Lack of fusion: Lack of fusion happens when the base metal and filler metal do not properly bond. Ensure proper cleaning and use the right welding technique to achieve complete fusion.
- Warping: Titanium is prone to warping and distortion due to its low thermal conductivity. Use proper clamping techniques and control the heat input to minimize warping.
By identifying and addressing these issues promptly, you can troubleshoot and overcome common welding problems, ensuring the integrity of your titanium exhaust.
Post-Welding Care and Maintenance of Titanium Exhaust
Once you’ve successfully welded your titanium exhaust, it’s essential to take proper care and perform regular maintenance to prolong its lifespan. Here are some post-welding care tips for your titanium exhaust:
Allow the weld to cool naturally: Avoid rapid cooling or quenching, as it can increase the risk of cracking or warping.
Clean the weld area: Remove any residual flux or slag from the weld area using a wire brush or appropriate cleaning tools.
Inspect for defects: Regularly inspect your welds for any signs of cracks, porosity, or lack of fusion. Address any issues promptly to prevent further damage.
Perform regular maintenance: Depending on the exhaust system’s usage and environment, periodic maintenance may be required. This may include cleaning, lubrication, or inspection of other components.
By following these post-welding care and maintenance practices, you can ensure the longevity and optimal performance of your titanium exhaust.
Conclusion and Final Thoughts on Welding Titanium Exhaust
Welding titanium exhausts requires careful consideration of the material’s properties, precise technique, and proper equipment. By following the step-by-step guide and implementing the tips and precautions outlined in this article, you can confidently tackle your titanium exhaust welding project. Remember, safety should always be your top priority, so make sure to take the necessary precautions and work in a well-ventilated area. Additionally, practice on scrap pieces of titanium before welding your actual exhaust to perfect your technique and achieve high-quality welds.
With the right knowledge and skills, welding titanium exhausts can be a rewarding and successful endeavor. So, grab your welding helmet, gather your tools, and get ready to create strong and durable welds on your titanium exhaust.