Calculating welding costs can be a challenging task, especially when it comes to determining the cost per inch. Welding is a crucial process in many industries, and having an accurate understanding of the costs involved is essential for budgeting and project planning.
In this ultimate guide, we will walk you through the step-by-step process of calculating welding costs per inch. Whether you are a professional welder or a business owner looking to estimate project expenses, this comprehensive guide will provide you with the knowledge and tools you need to make accurate and informed calculations. So, if you’ve ever wondered, “How much does welding cost per inch?” – keep reading!
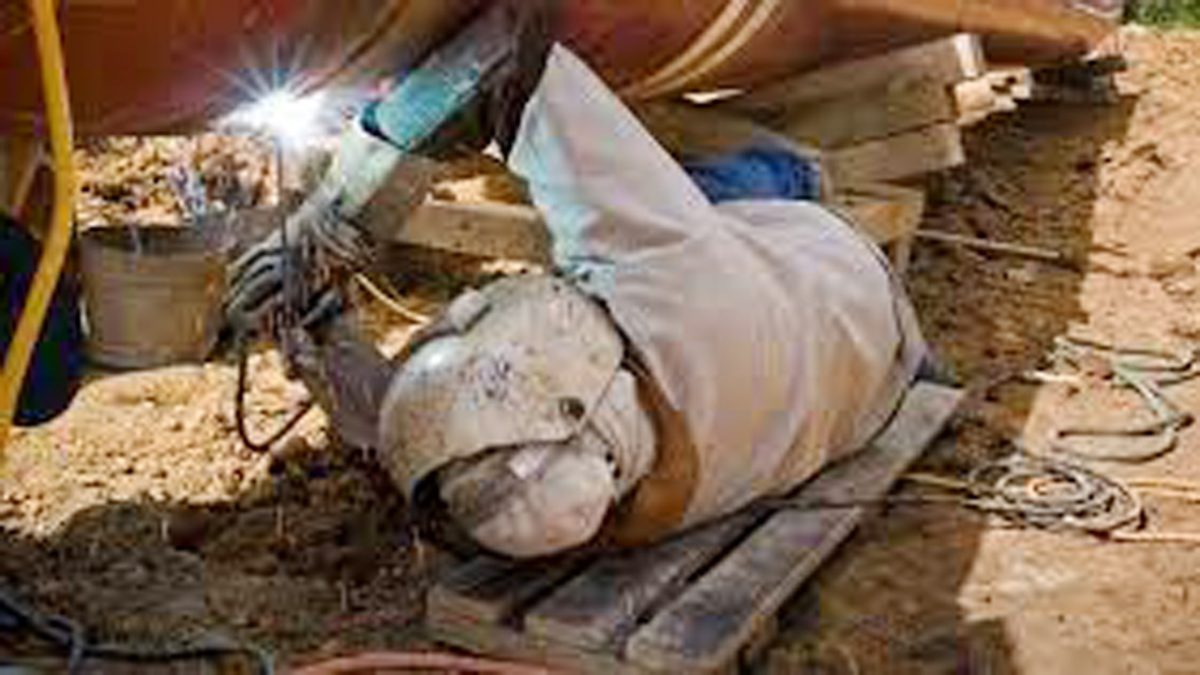
Importance of calculating welding costs per inch
Understanding the costs associated with welding is crucial in various industries. By calculating the welding costs per inch, businesses and professionals can accurately estimate project expenses, allocate resources efficiently, and make informed decisions regarding pricing and budgeting.
Calculating the welding costs per inch allows for better cost control and helps prevent unexpected expenses that could impact profitability. It also enables companies to determine the competitiveness of their pricing in the market, ensuring that they remain profitable while providing quality services.
Additionally, by knowing the welding costs per inch, businesses can accurately bid on projects, ensuring they cover expenses while remaining competitive. This knowledge can give them an edge in securing contracts and maintaining a healthy bottom line.
Factors that affect welding costs
To accurately calculate welding costs per inch, it’s crucial to have a deep understanding of the factors that contribute to these costs. By knowing and considering these factors, businesses can make informed decisions to optimize their welding processes and manage expenses effectively.
One of the primary factors that affect welding costs is the type of material being welded. Different materials have varying welding requirements, such as preheating, specific welding procedures, and post-welding treatments, which can significantly impact the overall cost.
The welding method used is another crucial factor. Different welding processes, such as MIG, TIG, or stick welding, have varying equipment and consumable requirements, which directly influence costs. Moreover, the experience and skill level of the welder also play a role in determining the cost per inch.
Other factors that can affect welding costs include the complexity and size of the project, the number of welds required, and the accessibility of the welding area. Each of these factors needs to be carefully analyzed and accounted for when calculating the welding costs per inch.
Steps to accurately calculate welding costs per inch
Now that we have a clear understanding of the factors that contribute to welding costs, let’s delve into the steps you can take to accurately calculate your welding costs per inch. By following these steps, you can gain valuable insights into your welding expenses and make informed decisions to optimize your processes.
Step 1: Gather relevant information
Start by gathering all the necessary information, such as the type of material being welded, the welding method used, the experience level of the welder, the complexity and size of the project, the number of welds required, and the accessibility of the welding area. This information will form the basis for your calculations.
Step 2: Determine material costs
Consider the cost of the welding material required for the project. Different materials have varying prices, so it is important to accurately estimate the amount of material needed and calculate the associated costs.
Step 3: Calculate equipment and consumable expenses
Take into account the equipment and consumables required for the welding process. This includes the cost of welding machines, electrodes, gas, filler metal, and any other necessary tools and supplies.
Step 4: Factor in labor costs
Consider the labor costs associated with the project. This includes wages, benefits, and any additional costs related to the welder’s experience level and skill set.
Step 5: Account for overhead expenses
Include any overhead expenses that are directly or indirectly related to the welding process. This may include rent, utilities, insurance, and maintenance costs for the welding equipment.
Step 6: Determine the total welding cost per inch
By adding up all the costs determined in the previous steps, you can calculate the total welding cost per inch. Divide the total cost by the length of the weld to get an accurate cost per inch figure.
By following these steps, you will have a comprehensive understanding of your welding costs per inch. This knowledge will empower you to optimize your processes, identify areas for cost-saving, and ultimately, enhance your bottom line.
Tips for reducing welding costs
Now that you have a firm grasp on how to calculate your welding costs per inch, it’s time to explore some practical tips and strategies to help you reduce these costs without compromising the quality of your work. By implementing these tips, you can maximize efficiency and profitability in your welding operations.
1. Plan and optimize your welding process: Before starting any welding project, take the time to carefully plan and optimize your process. This includes selecting the most appropriate welding method, considering joint design and fit-up, and using the right equipment and consumables for the job. By streamlining your process, you can minimize waste and maximize productivity.
2. Invest in training and skills development: Proper training and skill development for your welders can go a long way in reducing welding costs. A well-trained welder can work more efficiently, produce higher quality welds, and minimize the chances of rework or scrap. Consider investing in training programs or partnering with welding experts to enhance the skills of your workforce.
3. Conduct regular maintenance on equipment: Regular maintenance and inspection of your welding equipment is crucial for preventing breakdowns and costly repairs. By keeping your equipment in top shape, you can reduce downtime and ensure optimal performance.
4. Explore automation and technology: Embracing automation and technology in your welding processes can lead to significant cost savings. Robotic welding systems, for example, can increase productivity, reduce labor costs, and enhance the consistency and quality of welds. Additionally, software and data analysis tools can help you track and optimize your welding operations.
5. Evaluate and negotiate supplier contracts: Take the time to evaluate and negotiate your supplier contracts for welding materials and consumables. Consider partnering with reliable suppliers who offer competitive pricing and quality products. By securing favorable deals, you can reduce material costs and improve your bottom line.
By following these tips, you can make significant strides in reducing your welding costs per inch. Remember, optimizing your processes and investing in efficiency will not only save you money but also improve the overall quality of your work.
Common mistakes to avoid when calculating welding costs
Calculating welding costs per inch is not without its challenges, and it’s important to be aware of common mistakes that can lead to inaccurate calculations. By avoiding these mistakes, you can ensure that your cost calculations are reliable and that you have a clear understanding of the financial implications of your welding projects.
One common mistake is neglecting to account for all the variables involved in the welding process. It’s essential to consider factors such as the type and size of the welding material, the type and size of the weld joint, the welding method, and any additional costs such as labor or overhead. Failing to factor in these variables can result in significant discrepancies in your cost calculations.
Another mistake to be mindful of is relying solely on estimates or assumptions when determining the cost of materials and consumables. It’s best to obtain accurate pricing information from reputable suppliers and consider any discounts or bulk purchasing options that may be available to you.
Additionally, overlooking the costs associated with pre- and post-welding activities can lead to inaccurate cost calculations. This includes activities such as material preparation, cleaning, and finishing. Failure to include these costs can give you an incomplete picture of the overall expenses associated with your welding projects.
Lastly, not accounting for the potential for rework or scrap can result in underestimating the true costs of a welding project. It’s crucial to factor in the possibility of setbacks or errors that may require rework or result in scrapped materials. By considering these potential costs, you can have a more accurate assessment of your overall welding expenses.
Avoiding these common mistakes will help you achieve more accurate and reliable welding cost calculations. By having a clear understanding of the true costs involved, you can make informed decisions, optimize your processes, and ultimately increase your profitability.
Conclusion
Calculating welding costs per inch is a complex process that requires careful consideration of various variables and potential pitfalls. By avoiding common mistakes such as neglecting important variables, relying on estimates, overlooking pre- and post-welding activities, and not accounting for rework or scrap, you can ensure more accurate cost calculations.
To refine your welding cost calculations, it is essential to obtain accurate pricing information from reputable suppliers, consider any discounts or bulk purchasing options, and include all relevant costs associated with the project. This includes material preparation, cleaning, finishing, and potential setbacks or errors that may require rework or result in scrapped materials.
By following these strategies and techniques, you can make informed decisions, optimize your processes, and ultimately increase your profitability. Calculating welding costs per inch may be challenging, but with diligence and attention to detail, you can master this crucial aspect of your welding projects.