Looking to hire a welder but not sure how much it will cost you? We’ve got the information you need. In this article, we will break down the average cost of welding per hour, so you can budget accordingly for your upcoming welding project. Welding costs can vary depending on various factors, including the complexity of the job, the materials being welded, and the skill level of the welder. By understanding these factors, you will be able to make an informed decision and avoid any surprises when it comes time to pay.
Whether you are looking to repair metal structures, create customized metal pieces, or tackle a DIY welding project, knowing the average cost of welding per hour will help you plan your budget effectively. So, before you start reaching out to welding professionals in your area, take a few minutes to read this article and get a better understanding of what you can expect to pay.
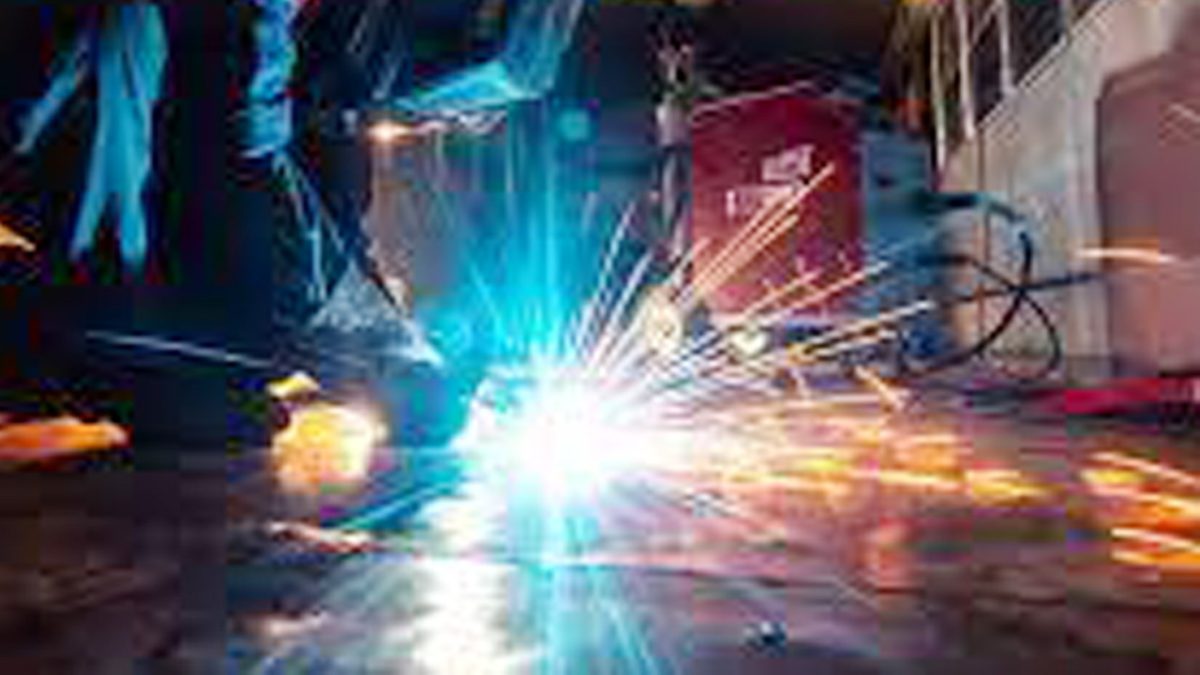
Factors that affect welding costs
Welding is a complex process that requires skill, experience, and specialized equipment. The cost of welding can vary depending on several factors.
Firstly, the complexity of the job will play a significant role in determining the cost. Simple welding tasks, such as joining two metal pieces together, will generally cost less than more intricate projects that require intricate welding techniques or the use of specialized equipment.
Secondly, the type of material being welded will also impact the cost. Different metals require different welding techniques, and some metals are more challenging to weld than others. For example, welding stainless steel or aluminum will typically cost more than welding mild steel due to the higher skill level required and the specialized equipment needed.
Lastly, the skill level and experience of the welder will affect the cost. Highly skilled and experienced welders may charge higher rates due to their expertise and reputation. However, it’s important to note that hiring a skilled welder can save you money in the long run by ensuring the job is done correctly and reducing the risk of future repairs.
Considering these factors will allow you to get a better understanding of what to expect when it comes to welding costs. However, keep in mind that the rates can vary significantly depending on your location, so it’s always a good idea to get multiple quotes before making a decision.
Average hourly rates for welding services
The average hourly rates for welding services can vary depending on several factors, including the location, the specific type of welding required, and the experience of the welder. In general, the national average hourly rate for welding services in the United States ranges from $40 to $100 per hour. However, keep in mind that these rates can be higher or lower depending on your location and the factors mentioned earlier.
In metropolitan areas or regions with a high cost of living, you can expect to pay towards the higher end of the range. On the other hand, in rural areas or regions with a lower cost of living, you may find welders who charge towards the lower end of the range. It’s important to note that these rates are just averages, and the actual cost may vary depending on the factors discussed earlier. Additionally, some welders may charge a flat fee for specific projects rather than an hourly rate.
When hiring a welder, it’s essential to inquire about their pricing structure and get a detailed breakdown of the costs involved. This will help you compare quotes and ensure you’re getting a fair price for the services you require.
Different types of welding and their associated costs
There are several different types of welding, each with its own associated costs. The type of welding required for your project will impact the overall cost.
Shielded Metal Arc Welding (SMAW)
Shielded Metal Arc Welding (SMAW) also known as stick welding, is a versatile and widely used welding method. It involves using a consumable electrode coated in flux to create an arc between the electrode and the workpiece. SMAW is commonly used for construction, maintenance, and repair work. The cost of SMAW welding is generally lower compared to other methods, with hourly rates ranging from $40 to $60.
Gas Metal Arc Welding (GMAW)
Gas Metal Arc Welding (GMAW) also known as MIG welding, is a popular method for automotive, manufacturing, and fabrication projects. It involves using a wire electrode and a shielding gas to create an arc between the electrode and the workpiece. GMAW offers high productivity and produces clean welds. The average hourly rates for GMAW welding range from $50 to $80.
Gas Tungsten Arc Welding (GTAW)
Gas Tungsten Arc Welding (GTAW) also known as TIG welding, is a precise and high-quality welding method commonly used for stainless steel, aluminum, and exotic metals. It involves using a non-consumable tungsten electrode and a shielding gas to create an arc between the electrode and the workpiece. GTAW offers excellent control and produces clean and precise welds. The hourly rates for GTAW welding can range from $60 to $100.
Flux-Cored Arc Welding (FCAW)
Flux-Cored Arc Welding (FCAW) is a versatile and efficient welding method that uses a tubular wire electrode with flux inside. FCAW can be used for both thick and thin materials and is commonly used in construction and fabrication. The average hourly rates for FCAW welding range from $50 to $80.
The choice of welding method will depend on the specific requirements of your project, the type of material being welded, and the desired quality of the weld. It’s essential to consult with a professional welder to determine the most suitable welding method and associated cost for your needs.
Additional costs to consider in welding projects
When budgeting for a welding project, it’s important to consider additional costs that may arise. These costs can vary depending on the nature of the project and the specific requirements. Here are some common additional costs to keep in mind:
Materials
The cost of materials is a significant factor in welding projects. Depending on the type and quantity of metal required, the cost of materials can vary significantly. It’s important to factor in the cost of materials when estimating the overall cost of the project.
Consumables
Welding consumables, such as electrodes, shielding gas, and flux, may need to be purchased separately. These consumables can add to the overall cost of the project, particularly for larger or more complex projects.
Preparation and cleanup
Depending on the condition of the workpiece and the specific requirements of the project, additional preparation work may be needed. This can include cleaning, grinding, and removing any existing welds. Additionally, cleanup after the welding process may be required, especially if there is slag or spatter to remove.
Travel and accommodation
If you require a welder to travel to your location, you may need to factor in travel expenses, such as fuel costs or accommodation if the project requires an extended stay.
Welding certifications
For certain projects or industries, welders may need to hold specific certifications to ensure compliance with safety and quality standards. The cost of obtaining these certifications may be passed on to the client.
It’s important to discuss these additional costs with your welder and factor them into your budget to avoid any surprises or unexpected expenses.
Tips for reducing welding costs
While welding costs can add up, there are several ways you can reduce the overall cost of your welding project. Here are a few tips to help you save money:
Plan ahead
Proper planning can help save time and money on a welding project. By having a clear understanding of your project requirements and specifications, you can minimize any unnecessary welding or rework.
Optimize material usage
Minimize waste by accurately estimating the amount of material required for your project. This can help reduce material costs and improve overall efficiency.
Consider alternative methods
Depending on your project requirements, there may be alternative fabrication methods that can achieve similar results at a lower cost. It’s worth exploring different options and discussing them with your welder.
Get multiple quotes
Don’t settle for the first quote you receive. It’s always a good idea to get multiple quotes from different welders to compare prices and ensure you’re getting a fair deal.
Invest in preventive maintenance
Regular maintenance and inspections can help identify and address issues early on, preventing costly repairs down the line. By investing in preventive maintenance, you can extend the lifespan of your welded structures and reduce long-term costs.
By implementing these tips, you can optimize your welding project and save money without compromising on quality or safety.
Comparing welding costs with other fabrication methods
When considering a welding project, it’s essential to compare the costs with alternative fabrication methods to determine the most cost-effective solution. While welding is a versatile and widely used fabrication method, it may not always be the most suitable or affordable option.
For example, if you require a large quantity of identical metal pieces, processes like laser cutting or waterjet cutting may offer a more cost-effective solution compared to welding individual pieces together. These methods can provide precise and clean cuts, eliminating the need for welding and reducing overall costs.
Similarly, if you require complex shapes or designs, processes like CNC machining or 3D printing may offer more efficient and cost-effective options compared to welding multiple pieces together.
It’s important to consult with a professional fabricator or engineer to evaluate the specific requirements of your project and determine the most suitable fabrication method in terms of cost, quality, and timeframe.
Hiring a professional welder vs. DIY welding
When it comes to welding projects, you have the option of hiring a professional welder or tackling the project yourself. While DIY welding may seem like a cost-effective solution, there are several factors to consider before deciding which route to take.
Skill and expertise
Welding is a skilled trade that requires training, experience, and knowledge of safety practices. Professional welders undergo extensive training and have the expertise to handle various welding projects. If you’re not confident in your welding skills, hiring a professional welder is the safer option to ensure the job is done correctly.
Equipment and setup
Welding requires specialized equipment, including welding machines, protective gear, and various tools. Purchasing or renting this equipment can add to the overall cost of a DIY welding project. Professional welders have access to high-quality equipment and can provide the necessary tools and materials for the job.
Time and efficiency
Welding projects can be time-consuming, especially if you’re new to welding. Hiring a professional welder can save you time and ensure the project is completed efficiently. Professionals have the experience to handle welding tasks quickly and effectively, minimizing the risk of errors or delays.
Safety and liability
Welding can be hazardous if not done correctly, posing risks to both the welder and the surrounding environment. Professional welders are trained in safety protocols and adhere to industry standards to ensure a safe working environment. By hiring a professional welder, you can mitigate the risks associated with welding and avoid potential liabilities.
While DIY welding may be suitable for small, straightforward projects, it’s important to consider the complexity of the task, your welding skills, and the overall safety implications before deciding to tackle a welding project yourself.
Examples of welding projects and their cost breakdowns
To give you a better idea of how welding costs can vary, here are a few examples of common welding projects and their cost breakdowns:
Repairing a metal fence
Suppose you have a metal fence that requires welding repairs due to rust or damage. The complexity of the repairs will depend on the extent of the damage and the number of welds required. On average, repairing a metal fence can cost between $200 and $500, including materials and labor.
Creating custom metal gates
If you’re looking to have custom metal gates fabricated for your property, the cost will depend on the size, design, and complexity of the gates. On average, custom metal gates can cost between $1,000 and $5,000, including materials, labor, and any additional finishes or coatings.
Building a metal handrail
For a metal handrail installation, the cost will depend on the length, design, and materials used. On average, building a metal handrail can cost between $500 and $2,000, including materials and labor.
It’s important to note that these are just examples, and the actual cost of your welding project may vary depending on your specific requirements, location, and the factors discussed earlier. To get an accurate cost estimate, it’s recommended to consult with a professional welder and provide them with detailed project specifications.
Conclusion
Understanding and budgeting for welding costs is essential when planning any welding project. By considering factors such as the complexity of the job, the materials being welded, and the skill level of the welder, you can make an informed decision and avoid any surprises when it comes time to pay.
Remember to get multiple quotes from different welders and consider the additional costs that may arise, such as materials, consumables, and travel expenses. By following the tips for reducing welding costs and comparing welding costs with other fabrication methods, you can optimize your project and save money without compromising on quality.
Lastly, when deciding between hiring a professional welder or DIY welding, consider factors such as skill, expertise, equipment, time, and safety. Hiring a professional welder may be the safer and more efficient option for complex or large-scale projects. Now that you have a better understanding of how much welding costs per hour and the factors that can contribute to the final price tag of your project, you can confidently plan and budget for your upcoming welding project.