When investing in a welding machine, it’s essential to know how long it will last before you have to replace it. The longevity of a welding machine depends on several factors, including its quality, usage, and maintenance. A well-made and properly maintained welding machine can last for many years, providing you with reliable performance throughout its lifespan.
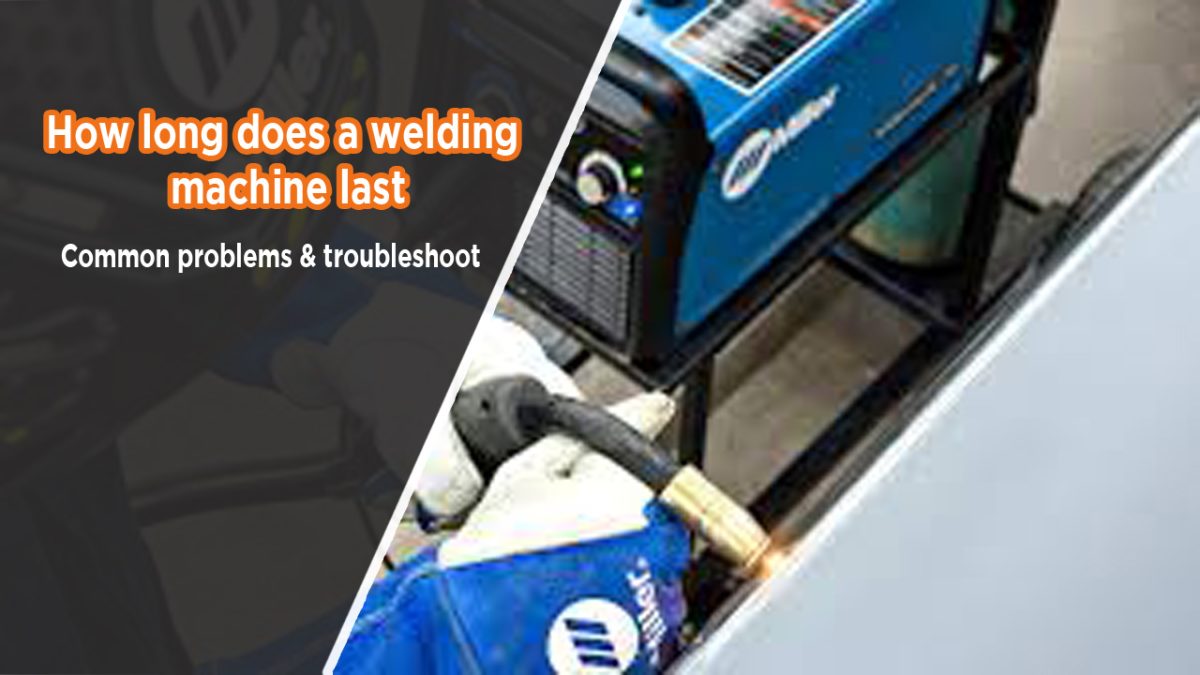
Image by motortrend
Factors that affect the lifespan of a welding machine
The lifespan of a welding machine can be influenced by various factors. Understanding these factors can help you make an informed decision when purchasing a welding machine and ensure its longevity. Here are some key factors that can affect the lifespan of a welding machine:
Quality of the welding machine
High-quality welding machines from reputable brands are usually designed with durability in mind. These machines are built to withstand the demands of heavy-duty welding projects and are manufactured using robust materials. Investing in a high-quality machine can significantly extend its lifespan.
Usage intensity
The frequency and duration of usage play a vital role in determining how long a welding machine will last. A welding machine used for occasional projects may last longer compared to one that is constantly used for large-scale commercial welding. It’s important to consider your specific usage requirements before selecting a welding machine.
Maintenance and care
Proper maintenance and care are crucial for maximizing the lifespan of a welding machine. Regular cleaning, lubricating, and replacing worn-out parts can prevent premature wear and tear. Following the manufacturer’s guidelines for maintenance can help ensure that your welding machine remains in optimal condition for an extended period.
Average lifespan of different types of welding machines
The average lifespan of a welding machine can vary based on its type. Different welding processes and technologies can impact the durability and longevity of the machine. Here’s a breakdown of the average lifespan for some common types of welding machines:
Stick welding machines
Stick welding machines, also known as shielded metal arc welding (SMAW) machines, are known for their durability and longevity. When properly maintained, these machines can last for 10 to 20 years. The simplicity of their design contributes to their longevity, making them a popular choice among welders.
MIG welding machines
MIG welding machines, which use a wire electrode to create an arc for welding, have an average lifespan of 5 to 15 years. The lifespan can vary depending on the quality of the machine, frequency of usage, and maintenance practices. Regularly cleaning the wire feed mechanism and replacing consumables can help extend the lifespan of a MIG welding machine.
TIG welding machines
TIG welding machines, also known as gas tungsten arc welding (GTAW) machines, are known for their precision and versatility. These machines can last for 7 to 15 years with proper maintenance. TIG welding machines require regular cleaning and inspection of the torch and gas supply system for optimal performance and longevity.
Signs that indicate a welding machine needs to be replaced
Even with regular maintenance, there may come a time when a welding machine needs to be replaced. Recognizing the signs of a failing or outdated welding machine is crucial for ensuring safety and efficiency. Here are some common signs that indicate it’s time to replace a welding machine:
Decreased performance
If you notice a decline in the welding machine’s performance, such as inconsistent arc stability, poor weld quality, or difficulty striking an arc, it may be a sign of internal issues. In such cases, it’s often more cost-effective to invest in a new machine rather than attempting extensive repairs.
Frequent breakdowns
If your welding machine requires frequent repairs or experiences repeated breakdowns, it may be a sign of underlying issues. Constantly repairing an old or unreliable machine can be time-consuming and costly. Investing in a new machine can provide you with better reliability and reduce downtime.
Outdated technology
Welding technology is constantly evolving, with new features and advancements being introduced regularly. If your welding machine lacks essential features or is outdated, it may be time to consider upgrading to a newer model. Newer machines often offer improved efficiency, ease of use, and safety features.
Tips for extending the lifespan of a welding machine
Proper maintenance and care are key to extending the lifespan of a welding machine. By following these tips, you can ensure that your welding machine remains in optimal condition for as long as possible:
Clean the machine regularly
Regularly clean the welding machine to remove dust, debris, and welding residue. Use compressed air or a brush to clean hard-to-reach areas. Accumulated dirt can affect the machine’s performance and lead to premature wear.
Lubricate moving parts
Lubricate the moving parts of the welding machine as recommended by the manufacturer. This includes the wire feed mechanism, drive rollers, and any other components that require lubrication. Lubrication reduces friction and helps prevent premature wear and tear.
Replace consumables as needed
Consumables such as contact tips, nozzles, and electrodes should be replaced regularly to maintain optimal performance. Worn-out consumables can lead to poor weld quality and increased stress on the welding machine.
Store the machine properly
When not in use, store the welding machine in a clean and dry environment. Protect the machine from extreme temperatures, moisture, and dust. Storing the machine properly can prevent corrosion and other damage.
Follow maintenance guidelines
Always follow the manufacturer’s guidelines for maintenance and servicing. This includes recommended maintenance intervals, inspections, and any specific instructions for your welding machine model. Adhering to these guidelines ensures that your machine remains in good working condition.
Maintenance and care for welding machines
Proper maintenance and care are essential for ensuring the longevity and performance of a welding machine. Here are some maintenance and care practices you should follow:
Cleaning
Regularly clean the welding machine, including the exterior surfaces, wire feed mechanism, torch, and gas supply system. Use appropriate cleaning agents and tools to remove dirt, debris, and welding residue. Cleaning prevents clogs and ensures optimal performance.
Lubrication
Lubricate the moving parts of the welding machine as recommended by the manufacturer. Apply lubricants to areas such as the wire feed mechanism, drive rollers, and any other components that require lubrication. Proper lubrication reduces friction and extends the lifespan of the machine.
Inspection
Periodically inspect the welding machine for any signs of wear, damage, or loose connections. Check the cables, connectors, and grounding components for any issues. Promptly address any problems to prevent further damage and maintain safety.
Replacement of consumables
Replace consumables such as contact tips, nozzles, electrodes, and shielding gas as needed. Worn-out consumables can hinder the welding process and lead to poor weld quality. Regularly inspect and replace consumables to ensure optimal performance.
Calibration and adjustments
Calibrate and adjust the welding machine as recommended by the manufacturer. This includes checking and adjusting settings such as voltage, amperage, wire speed, and gas flow. Proper calibration ensures accurate and consistent welding results.
Common welding machine problems and how to troubleshoot them
Even with proper maintenance, welding machines can experience common issues. Understanding these problems and knowing how to troubleshoot them can save you time and money. Here are some common welding machine problems and their possible solutions:
Poor weld quality
If you’re experiencing inconsistent weld quality, check for issues such as incorrect settings, improper grounding, or worn-out consumables. Ensure that the machine is properly calibrated and adjust the settings as needed. Replace any worn-out consumables that may be affecting the weld quality.
Overheating
Overheating is a common issue in welding machines, especially during prolonged usage. Ensure that the machine has proper ventilation and is not operating in an excessively hot environment. If the machine overheats, give it time to cool down before resuming operation.
Wire feeding problems
If the wire feeding mechanism is not working properly, check for issues such as wire jams, tension problems, or worn-out drive rolls. Clean the wire feed mechanism, ensure proper tension, and replace any worn-out parts. Properly align the wire feeding system to prevent feeding problems.
Electrical issues
If the welding machine is not receiving power or experiencing electrical issues, check the power source, cables, and connectors. Ensure that the power source is functioning correctly and that all connections are secure. If necessary, consult a qualified electrician to address any electrical issues.
Factors to consider when purchasing a new welding machine
When purchasing a new welding machine, several factors should be taken into consideration to ensure you select the right machine for your needs. Here are some key factors to consider:
Welding process
Determine the specific welding process you will be using, such as stick welding, MIG welding, or TIG welding. Different processes require different types of welding machines, so choose one that is compatible with your preferred welding process.
Power requirements
Consider the power requirements of the welding machine. Ensure that your power source can provide sufficient voltage and amperage for the machine’s operation. It’s important to have the right power supply to avoid issues such as insufficient power or electrical overload.
Duty cycle
The duty cycle refers to the amount of time a welding machine can operate continuously before it needs to cool down. Consider your typical welding projects and choose a machine with a duty cycle that can handle your workload without excessive downtime.
Quality and reliability
Invest in a welding machine from a reputable brand known for producing high-quality and reliable equipment. Read reviews and seek recommendations from experienced welders to ensure you choose a machine that will last and perform well.
Budget
Determine your budget for purchasing a welding machine. Consider both the initial cost of the machine and any additional accessories or consumables you may need. While it’s important to stay within your budget, also prioritize the quality and features that are essential for your welding projects.
Cost comparison: Repairing vs. replacing a welding machine
When faced with a malfunctioning or aging welding machine, you may be unsure whether to repair or replace it. Assessing the cost factors can help you make an informed decision. Here’s a cost comparison between repairing and replacing a welding machine:
Repairing
Repairing a welding machine can be a cost-effective option if the issue is minor and the machine is relatively new. However, extensive repairs or replacing major components can quickly add up in terms of labor and replacement parts. Consider the overall cost of repairs and the potential for future issues before opting for repairs.
Replacing
If the welding machine is old, outdated, or requires costly repairs, replacing it may be the better option. Investing in a new machine ensures reliability, updated technology, and improved performance. Consider the long-term benefits and potential savings of a new machine compared to ongoing repairs.
Conclusion and Making the most of your welding machine’s lifespan
The lifespan of a welding machine primarily depends on its quality, usage, and maintenance. By investing in a high-quality machine, considering your usage intensity, and following proper maintenance practices, you can ensure that your welding machine will last for many years, providing you with reliable and efficient performance.
Regular cleaning, lubrication, and replacement of consumables are essential for maintaining optimal performance and extending the lifespan of a welding machine. Recognizing the signs that indicate a welding machine needs to be replaced can help you avoid safety hazards and unnecessary downtime.
When purchasing a new welding machine, consider factors such as welding process compatibility, power requirements, duty cycle, and overall quality and reliability. Additionally, assess the cost factors when deciding between repairing and replacing a welding machine.
By taking these factors into account and implementing proper maintenance and care practices, you can maximize the lifespan of your welding machine and get the most out of your investment. A well-maintained welding machine will continue to provide you with consistent and reliable performance throughout its lifespan. So, choose wisely, maintain diligently, and enjoy the benefits of a long-lasting welding machine.