Destructive testing is a critical process used in various industries to evaluate the strength, durability, and performance of materials and structures. From aerospace and automotive to construction and manufacturing, this testing method provides valuable insights that help ensure product safety and reliability.
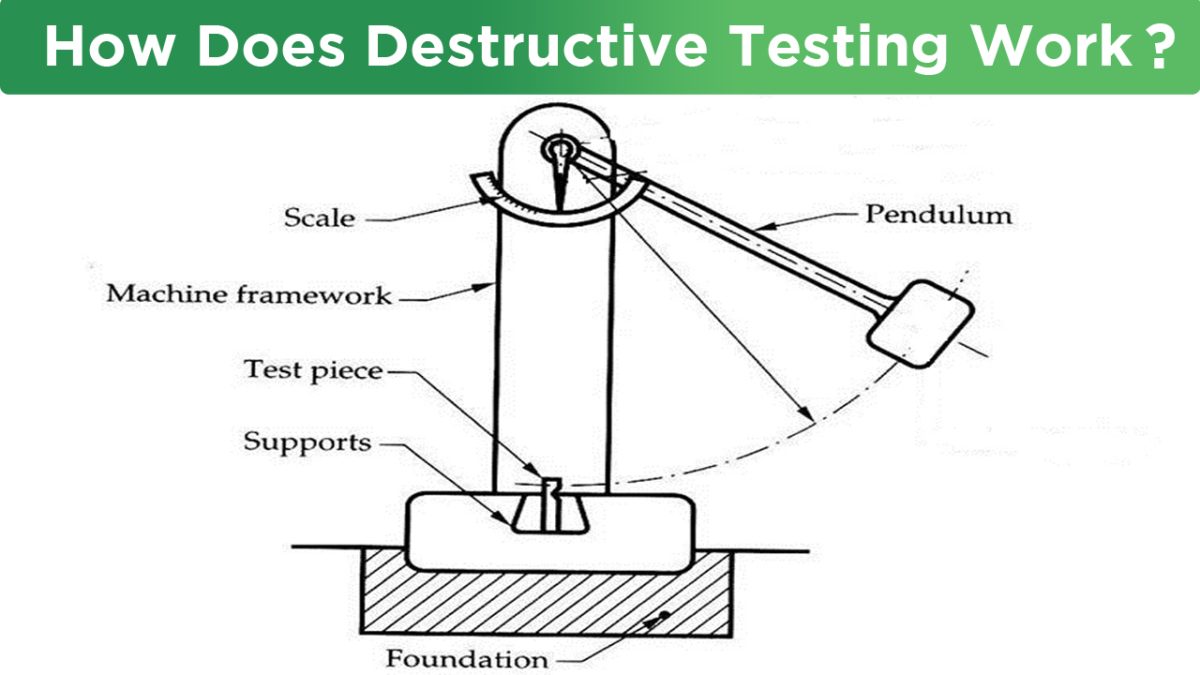
Image by inspection-for-industry
Purpose and importance of destructive testing
Destructive testing serves a crucial purpose in the development and manufacturing of products. Its primary goal is to push materials and structures to their limits, intentionally causing failure, in order to understand their capabilities and weaknesses. By subjecting samples or components to extreme conditions or forces that exceed their intended use, engineers and manufacturers gain a comprehensive understanding of the limits and breaking points of the tested item.
The importance of destructive testing lies in its ability to provide crucial information that cannot be obtained through non-destructive testing methods. It allows engineers to identify potential design flaws, evaluate the suitability of materials for specific applications, and determine the structural integrity and overall quality of a product. Through destructive testing, manufacturers can make informed decisions, refine designs, improve manufacturing processes, and ultimately deliver products that meet the highest standards of quality and reliability.
Common methods of destructive testing
There are several common methods used in destructive testing, each designed to simulate different types of stress and evaluate specific properties of materials and structures. These methods include tension, compression, shear, impact, fatigue, and torsion testing.
Tension testing involves subjecting a sample to a stretching force until it breaks, allowing engineers to measure the maximum load it can withstand. Compression testing, on the other hand, involves applying a compressive force to a sample to determine its resistance to crushing. Shear testing evaluates a material’s resistance to forces that cause it to slide against each other, while impact testing assesses a material’s ability to withstand sudden shocks or blows.
Fatigue testing involves subjecting a sample to repeated loading and unloading cycles to simulate the effects of long-term stress. This type of testing is particularly important in industries such as aerospace and automotive, where materials are exposed to constant vibrations and cyclic loading. Torsion testing, on the other hand, applies a twisting force to a sample to evaluate its resistance to torsional stress.
Step-by-step process of destructive testing
The process of destructive testing typically involves several steps to ensure accurate and reliable results. The first step is to determine the specific objectives of the testing, including the properties to be evaluated and the conditions to be simulated. This step helps engineers define the appropriate testing method and select the most suitable samples or components for testing.
Once the objectives are established, the next step is to prepare the samples or components for testing. This may involve machining, cutting, or shaping the materials to the desired dimensions. It is crucial to ensure that the samples are representative of the actual product or structure being tested.
After preparation, the samples are subjected to the specified testing conditions. This may involve applying loads, subjecting them to extreme temperatures, or exposing them to harsh environments, depending on the objectives of the testing. Throughout the testing process, engineers carefully monitor and record the behavior of the samples, including any deformations, cracks, or failures.
Once the testing is complete, engineers analyze the data to draw meaningful conclusions. This analysis may involve evaluating the load-displacement curves, measuring the ultimate strength or failure point of the samples, or performing statistical analysis to determine the material properties. The results of the destructive testing help engineers make informed decisions, refine designs, and improve the overall quality and performance of the tested materials or structures.
Advantages and limitations of destructive testing
Destructive testing offers several advantages over non-destructive testing methods. Firstly, it provides a comprehensive understanding of the behavior and limits of materials and structures under extreme conditions. This information is crucial for ensuring product safety and reliability. Secondly, destructive testing allows engineers to identify design flaws and weaknesses that may not be apparent through non-destructive testing methods. By intentionally causing failure, engineers can uncover hidden defects and improve the overall quality of the product.
However, destructive testing also has its limitations. One of the main limitations is the cost associated with the testing process. Since destructive testing involves intentionally destroying samples or components, it can be expensive to produce additional samples for testing purposes. Additionally, destructive testing may not be suitable for all materials or structures. Some materials, such as ceramics or composites, may be difficult to test destructively due to their brittle nature or complex internal structure. In such cases, non-destructive testing methods may be preferred.
Applications of destructive testing in different industries
Destructive testing finds applications in various industries where product safety and reliability are of utmost importance. In the aerospace industry, for example, destructive testing is used to evaluate the strength and durability of aircraft components, such as wings, fuselages, and landing gears. By subjecting these components to extreme conditions, engineers can ensure that they can withstand the demanding conditions of flight.
In the automotive industry, destructive testing is used to assess the crashworthiness of vehicles. By simulating high-speed collisions, engineers can evaluate the structural integrity of the vehicle and determine the effectiveness of safety features, such as airbags and seat belts. Destructive testing is also used in the construction industry to evaluate the strength of building materials, such as concrete and steel, and ensure compliance with safety regulations.
Safety precautions and regulations for conducting destructive testing
Destructive testing involves working with extreme forces and potentially hazardous materials. Therefore, it is essential to follow strict safety precautions and adhere to regulations to ensure the safety of personnel and the environment. This includes providing appropriate personal protective equipment, such as safety goggles, gloves, and protective clothing, and conducting testing in controlled environments to minimize risks.
Furthermore, there are industry-specific regulations and standards that govern the conduct of destructive testing. For example, the aerospace industry follows standards set by organizations such as the Federal Aviation Administration (FAA) and the European Aviation Safety Agency (EASA). These standards outline the testing procedures, safety requirements, and documentation necessary for conducting destructive testing.
Case studies and examples of destructive testing in action
To better understand the practical applications of destructive testing, let’s look at a few case studies and examples from different industries.
In the aerospace industry, destructive testing played a crucial role in the development of the Boeing 787 Dreamliner. During the testing phase, engineers subjected various components, including the wings and fuselage, to extreme conditions to evaluate their strength and durability. Through destructive testing, they were able to identify potential design flaws and make necessary improvements, ensuring the safety and reliability of the aircraft.
In the automotive industry, destructive testing is commonly used to evaluate the crashworthiness of vehicles. An example is the Insurance Institute for Highway Safety (IIHS) crash tests, where vehicles are subjected to controlled collisions to assess their structural integrity and safety features. These tests provide valuable data for improving vehicle designs and enhancing occupant protection.
In the construction industry, destructive testing is used to evaluate the strength of building materials. For example, concrete cylinders are subjected to compression testing to determine their compressive strength. This information helps engineers ensure that the concrete used in construction projects meets the required standards for structural stability and safety.
Training and certification for destructive testing technicians
Conducting destructive testing requires specialized knowledge and skills. Technicians involved in destructive testing must undergo proper training and certification to ensure the accuracy and reliability of the testing process.
Many organizations and institutions offer training programs and certifications in destructive testing. These programs cover various aspects of the testing process, including test method selection, sample preparation, testing equipment operation, data analysis, and safety procedures. By completing these programs and obtaining certifications, technicians demonstrate their competence and ability to perform destructive testing according to industry standards.
The future of destructive testing and its impact on product development
Destructive testing will continue to play a crucial role in ensuring product safety and reliability across various industries. As technology advances, new testing methods and equipment will emerge, allowing engineers to push the boundaries even further and gain deeper insights into material behavior.
The future of destructive testing lies in its integration with other testing methods, such as non-destructive testing and computer simulations. By combining these methods, engineers can obtain a more comprehensive understanding of material properties and behavior, leading to improved product designs and manufacturing processes.
In conclusion, destructive testing is not only a necessary and reliable method for evaluating the strength and durability of materials and structures, but it is also essential for ensuring the safety and reliability of products in various industries. By pushing the limits and uncovering weaknesses, engineers and manufacturers can deliver products that meet the highest standards of quality and performance.