Ever wondered about the perils faced by those who brave the depths to weld underwater? The underwater welding profession, known for its lucrative pay and high risks, is shrouded in curiosity. In this article, we delve into the question that lingers in the minds of many: “How do underwater welders die?” With a unique blend of technical expertise, courage, and the ability to navigate the challenges beneath the waves, the lives of underwater welders are both intriguing and perilous.

Photos: weldtube
From the dangers of high voltage electricity to the hazards of working in confined spaces underwater, this article uncovers the grave risks inherent to this extraordinary occupation, shedding light on the mysterious circumstances surrounding fatalities in this field.
As we unravel the factors that contribute to the mortality rate of underwater welders, prepare to gain a deeper understanding of the dangers they face and the safety measures crucial to their survival. Delve into this insightful exploration to discover the untold truths behind the enigmatic world of underwater welding.
Risks and Hazards of Underwater Welding
Underwater welding, a critical component of marine construction and maintenance, involves inherent risks that make it one of the most dangerous occupations in the world. The combination of electrical equipment, water pressure, and confined spaces creates a challenging and hazardous environment for welders. The primary risks associated with underwater welding include the potential for electric shock, drowning, and exposure to hazardous materials. The physical demands of working in water, such as extreme temperatures and visibility issues, further contribute to the perilous nature of this profession.
The underwater environment presents unique challenges, including the corrosive nature of saltwater, which can accelerate metal deterioration and compromise the structural integrity of underwater structures. The risks of entanglement, collision with marine life, and the unpredictability of underwater currents add layers of complexity to the already hazardous conditions. Despite the advancements in technology and safety protocols, the unforgiving nature of the underwater world continues to pose significant threats to the safety and well-being of underwater welders.
To comprehend the gravity of the risks involved, one must acknowledge the complex interplay of factors that make underwater welding a high-stakes endeavor. The need for meticulous planning, rigorous training, and adherence to stringent safety standards is paramount in mitigating the potential dangers inherent to this specialized form of welding.
Common Causes of Fatalities in Underwater Welding
The unfortunate reality of underwater welding is the presence of common causes of fatalities that underscore the extreme hazards associated with this occupation. Electric shock ranks among the leading causes of fatalities, as the use of high voltage welding equipment in a conductive medium like water poses a significant risk to the safety of underwater welders. The potential for electrical faults, inadequate insulation, or improper grounding amplifies the danger of electric shock, often with fatal consequences.
In addition to electric shock, drowning remains a pervasive risk, as the underwater environment introduces a multitude of factors that can lead to asphyxiation and loss of life. The complexities of working in confined spaces, combined with the challenges of maintaining a reliable air supply and managing decompression sickness, further elevate the threat of drowning as a fatal outcome of underwater welding incidents.
The exposure to toxic fumes and contaminants, coupled with the risks of physical trauma from equipment malfunctions or underwater hazards, contribute to the grim statistics of fatalities within the underwater welding industry. The cumulative effect of these hazards underscores the critical importance of implementing robust safety measures and comprehensive training to safeguard the lives of underwater welders.
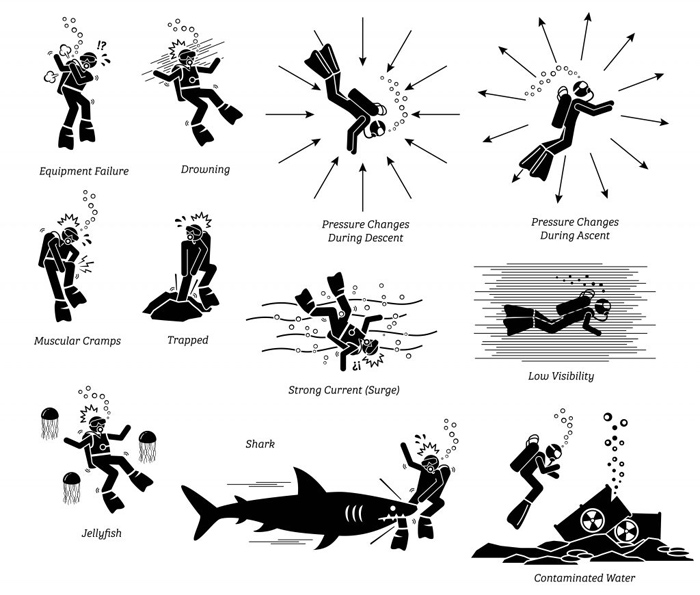
Photos by weldingpros.net
Safety Measures and Precautions for Underwater Welders
In light of the inherent dangers associated with underwater welding, the implementation of rigorous safety measures and precautions is imperative to mitigate the risks and ensure the well-being of welders operating in this challenging environment. Comprehensive risk assessments, thorough pre-dive inspections, and adherence to strict safety protocols form the cornerstone of a safety-centric approach to underwater welding operations.
The utilization of advanced welding techniques, such as dry welding methods that minimize the exposure to water, and the integration of cutting-edge equipment designed for underwater applications, contribute to enhancing the safety and efficiency of welding operations beneath the waves. The establishment of emergency response plans, meticulous monitoring of environmental conditions, and the provision of comprehensive diver training programs are essential components of a proactive safety framework tailored to the unique demands of underwater welding.
The significance of maintaining a robust safety culture within the underwater welding industry cannot be overstated. The collective commitment to prioritizing safety, continuous training and skill development, and the ongoing refinement of safety protocols are pivotal in safeguarding the lives of underwater welders and minimizing the occurrence of fatal incidents. By fostering a safety-conscious mindset and embracing a holistic approach to risk management, the industry can strive to create a safer and more secure environment for those engaged in underwater welding activities.
Case Studies of Fatal Underwater Welding Incidents
The examination of real-world case studies of fatal underwater welding incidents provides invaluable insights into the circumstances, contributing factors, and lessons learned from tragic events within the industry. By analyzing these case studies, the underlying causes of fatalities, including lapses in safety protocols, equipment failures, and human errors, can be identified and addressed to prevent the recurrence of similar incidents in the future.
The comprehensive review of fatal underwater welding incidents underscores the critical importance of proactive risk management, continuous improvement of safety practices, and the imperative of fostering a culture of accountability and diligence in upholding safety standards. Through a thorough analysis of case studies, the industry can glean actionable takeaways that inform the development of more robust safety measures and protocols aimed at safeguarding the lives of underwater welders.
The Importance of Proper Equipment and Maintenance
The reliance on specialized equipment tailored for underwater welding operations is pivotal in ensuring the safety, efficiency, and effectiveness of welders working in this challenging environment. The meticulous maintenance, inspection, and calibration of welding apparatus, diving gear, and associated equipment are essential in mitigating the risks of equipment malfunctions and minimizing potential hazards during underwater welding activities.
The utilization of state-of-the-art equipment designed to withstand the rigors of underwater conditions, coupled with stringent maintenance procedures and quality assurance protocols, plays a pivotal role in enhancing the safety and reliability of welding operations beneath the surface. Moreover, the adherence to industry-specific standards for equipment utilization and maintenance fosters a culture of safety and excellence, emphasizing the paramount significance of reliability and performance in mitigating the risks inherent to underwater welding.
By prioritizing the procurement of high-quality equipment, the implementation of robust maintenance practices, and the adherence to stringent quality assurance standards, the industry can fortify the safety infrastructure and resilience of underwater welding operations, ultimately safeguarding the lives of welders and preserving the integrity of underwater structures.
Legal and Regulatory Aspects of Underwater Welding Safety
The legal and regulatory framework governing underwater welding safety encompasses a comprehensive array of standards, guidelines, and regulations aimed at safeguarding the well-being of individuals engaged in underwater welding activities. Organizations such as the Occupational Safety and Health Administration (OSHA) in the United States, the Health and Safety Executive (HSE) in the United Kingdom, and the International Marine Contractors Association (IMCA) play pivotal roles in establishing and enforcing stringent safety standards and regulatory requirements tailored to the unique challenges of underwater welding.
The adherence to legal and regulatory mandates, coupled with the proactive implementation of industry best practices, reinforces the commitment to upholding the highest standards of safety, professionalism, and ethical conduct within the underwater welding industry. By aligning with legal and regulatory requirements, organizations and individuals demonstrate their dedication to ensuring the welfare and safety of underwater welders, while also contributing to the preservation of environmental integrity and the sustainability of marine structures.
Resources for Further Information on Underwater Welding Safety
For those seeking to deepen their understanding of underwater welding safety and explore additional resources, a myriad of reputable organizations, publications, and industry associations provide valuable insights, guidance, and educational materials on the subject. The American Welding Society (AWS), the International Marine Contractors Association (IMCA), and the Diver Certification Board of Canada (DCBC) offer comprehensive resources, training materials, and industry-specific publications that serve as invaluable references for individuals and organizations seeking to enhance their knowledge and proficiency in underwater welding safety.
In addition to organizational resources, industry publications, such as “Underwater Welding and Cutting” by the American Welding Society and “IMCA Diving Division Guidance” by the International Marine Contractors Association, offer in-depth analyses, best practices, and practical recommendations for optimizing safety and performance in underwater welding operations. By leveraging these resources, stakeholders can access a wealth of knowledge and expertise that empowers them to navigate the complexities of underwater welding safety with confidence and competence.
Final Thoughts
The enigmatic world of underwater welding is characterized by a unique blend of technical prowess, formidable challenges, and inherent risks that demand unwavering vigilance and commitment to safety. The grave dangers posed by high voltage electricity, confined spaces, and the complexities of working in an underwater environment underscore the critical imperative of prioritizing safety measures and rigorous adherence to industry best practices.
By embracing a safety-centric mindset, investing in advanced training and certification, and upholding the highest standards of equipment reliability and maintenance, the industry can strive to mitigate the risks and preserve the lives of underwater welders.
As we unravel the complexities surrounding the question of how underwater welders die, it becomes apparent that a holistic approach to safety, propelled by continuous improvement, industry collaboration, and the dissemination of knowledge, is fundamental to the safeguarding of lives and the sustainability of underwater welding operations. Through the collective commitment to excellence, safety, and professionalism, the industry can navigate the perils of underwater welding with resilience, fortitude, and an unwavering dedication to the preservation of life and the integrity of underwater structures.