Gas welding is a widely used method for joining metals, and stainless steel is no exception. In this article, we will explore the essential techniques for successful gas welding stainless steel. Whether you are a beginner or an experienced welder, understanding the properties of stainless steel and following the correct procedures are crucial for achieving high-quality welds.
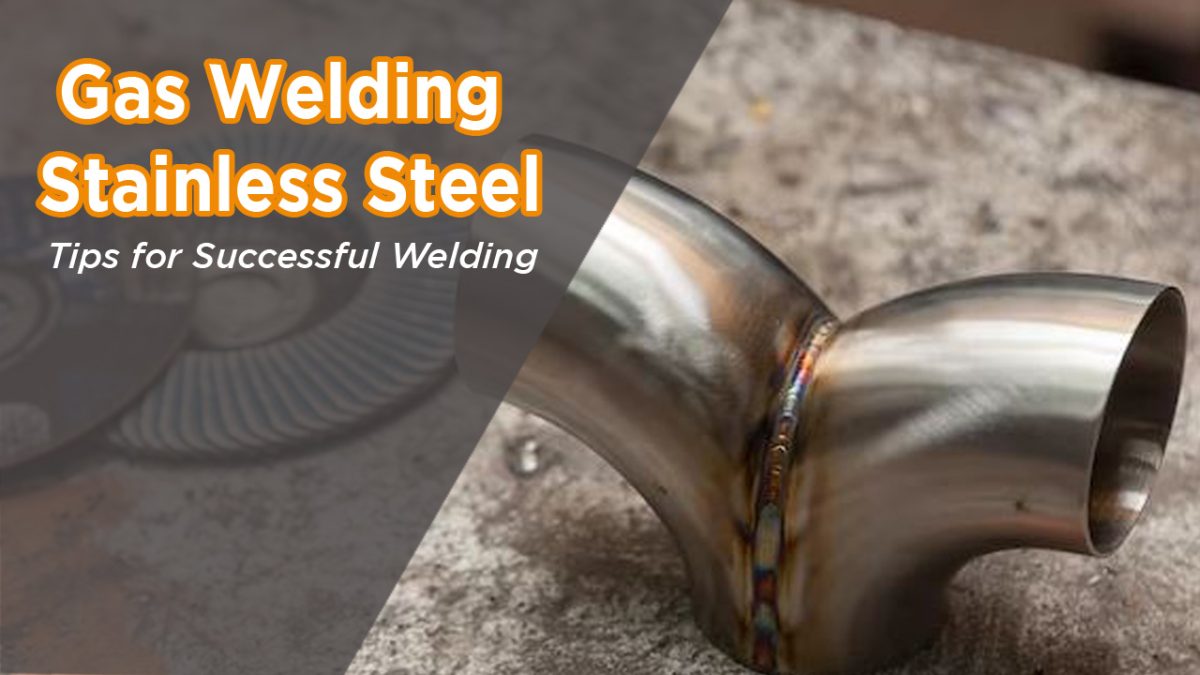
Properties of Stainless Steel for Gas Welding
Before diving into the techniques of gas welding stainless steel, it is important to have a good understanding of the properties of this unique metal. Stainless steel is known for its corrosion resistance and high strength, making it suitable for a wide range of applications. However, it also has some characteristics that can pose challenges during the welding process.
One important property to consider is the low thermal conductivity of stainless steel. This means that it can quickly build up heat during welding, leading to distortion or warping of the metal. Another factor to be aware of is the presence of chromium in stainless steel, which can form chromium carbides during welding if not properly controlled. These carbides can reduce the corrosion resistance of the weld, compromising its integrity.
Safety Precautions for Gas Welding Stainless Steel
Safety should always be a top priority when working with any form of welding, and gas welding stainless steel is no exception. Here are some important safety precautions to follow:
Personal Protective Equipment (PPE)
Wear appropriate PPE, including flame-resistant clothing, gloves, safety glasses, and a welding helmet with the correct shade of lens.
Ventilation: Ensure good ventilation in the welding area to prevent the accumulation of harmful fumes and gases. Consider using local exhaust ventilation systems or working in open spaces.
Fire Prevention
Keep a fire extinguisher nearby and be aware of potential fire hazards. Remove any flammable materials from the welding area and make sure the workpiece is properly secured.
Training and Certification
Obtain proper training and certification in gas welding techniques. This will ensure that you have the necessary skills and knowledge to work safely with stainless steel.
By following these safety precautions, you can minimize the risks associated with gas welding stainless steel and create a safe working environment.
Equipment and Tools Required for Gas Welding Stainless Steel
To successfully weld stainless steel using a gas welding process, you will need the following equipment and tools:
Welding Machine: Choose a gas welding machine that is suitable for stainless steel welding. Select the appropriate heat settings and gas flow rates according to the thickness of the stainless steel.
Gas Cylinders: Use a suitable shielding gas, such as argon or a mixture of argon and helium, to protect the weld pool from atmospheric contamination.
Welding Torch: Select a welding torch that is compatible with the gas welding machine and provides a stable and controlled flame.
Filler Rods: Stainless steel filler rods are necessary to add material to the weld pool and create a strong bond between the base metal and the filler metal.
Cleaning Tools: Stainless steel surfaces must be properly cleaned and prepared before welding. Use stainless steel brushes, abrasive pads, or chemical cleaners to remove any dirt, grease, or oxide layers.
Having the right equipment and tools is essential for achieving high-quality welds and ensuring the longevity of the stainless steel joints.
Preparing the Stainless Steel Surface for Gas Welding
Proper surface preparation is crucial for successful gas welding of stainless steel. Follow these steps to prepare the stainless steel surface:
Cleaning: Thoroughly clean the stainless steel surface using stainless steel brushes, abrasive pads, or chemical cleaners. Remove any dirt, grease, or oxide layers that may hinder the welding process.
Tacking: Use clamps or tack welds to hold the stainless steel pieces in position. This will ensure proper alignment during the welding process.
Beveling: In some cases, beveling the edges of the stainless steel pieces can improve the quality of the weld. This allows for better penetration of the filler metal and reduces the risk of incomplete fusion.
Fit-up: Ensure that the joint clearances and fit-up are appropriate for gas welding. Proper fit-up will help maintain the correct heat input during the welding process.
By following these preparation steps, you will create a clean and properly aligned surface for gas welding stainless steel, which will result in stronger and more durable welds.
Gas Welding Techniques for Stainless Steel
Gas welding stainless steel requires specific techniques to ensure the quality and integrity of the welds. Here are some key techniques to keep in mind:
Torch Angle: Maintain a torch angle of around 75 to 80 degrees from the workpiece. This angle provides good access to the joint and allows for proper heat distribution.
Travel Speed: Control the travel speed to achieve the desired penetration and fusion. Moving too quickly can result in insufficient heat input, while moving too slowly can cause overheating and distortion.
Tack Welding: Use tack welds to secure the stainless steel pieces before making the final weld. Tack welds help maintain proper alignment and prevent distortion during the welding process.
Filler Metal Selection: Choose the appropriate filler metal for gas welding stainless steel. The filler metal should have similar compositions to the base metal to ensure compatibility and maintain the desired mechanical properties.
Welding Technique: Employ a weaving or oscillating technique to distribute the heat evenly and avoid excessive build-up in one area. This technique helps control the size and shape of the weld bead.
By mastering these gas welding techniques, you will be able to create strong and aesthetically pleasing welds on stainless steel.
Common Challenges and Troubleshooting in Gas Welding Stainless Steel
Gas welding stainless steel can present some challenges that may affect the quality of the welds. Here are some common issues and their possible solutions:
Distortion: Stainless steel has low thermal conductivity, which can lead to distortion or warping during welding. To minimize this, use tack welds to hold the pieces in position and control the heat input by adjusting the travel speed.
Chromium Carbide Formation: When the temperature of stainless steel exceeds a certain range, chromium carbides can form, reducing the corrosion resistance of the weld. To prevent this, use proper heat control and select filler metals with low carbon content.
Porosity: Porosity, or the presence of gas pockets in the weld, can weaken the joint. Ensure that the stainless steel surface is properly cleaned and free from contaminants before welding. Also, adjust the gas flow rate and torch angle to minimize the risk of porosity.
Incomplete Fusion: Incomplete fusion occurs when the filler metal does not fully bond with the base metal, resulting in weak welds. To avoid this, ensure proper fit-up and penetration by adjusting the torch angle and travel speed.
By troubleshooting these common challenges and implementing the appropriate solutions, you can overcome the obstacles in gas welding stainless steel and produce high-quality welds.
Post-Welding Processes and Finishing Touches
After completing the gas welding process, there are several post-welding processes and finishing touches that can improve the overall quality of the welds:
Cleaning: Clean the welded area using stainless steel brushes or abrasive pads to remove any residual flux, slag, or oxides. This will improve the appearance of the weld and enhance its corrosion resistance.
Grinding and Polishing: If a smooth and aesthetically pleasing finish is desired, consider grinding and polishing the welds. This will remove any rough edges or surface imperfections and create a seamless appearance.
Heat Treatment: In some cases, heat treatment may be necessary to relieve residual stresses in the welds. Consult the welding specifications or guidelines for the specific stainless steel grade to determine if heat treatment is required.
By performing these post-welding processes and finishing touches, you can ensure that the gas-welded stainless steel joints meet the desired standards in terms of appearance, strength, and corrosion resistance.
Best Practices for Successful Gas Welding of Stainless Steel
To achieve successful gas welding of stainless steel, it is important to follow some best practices:
Plan and Prepare: Properly plan the welding project and prepare the stainless steel surfaces before welding. This includes cleaning, beveling (if necessary), and ensuring proper fit-up.
Control Heat Input: Stainless steel is sensitive to heat, so it is essential to control the heat input during welding. Adjust the torch angle, travel speed, and heat settings to maintain the correct temperature range.
Use Appropriate Filler Metal: Select filler metals with compositions similar to the base metal to ensure compatibility and maintain the desired mechanical properties.
Practice Welding Techniques: Master the gas welding techniques specific to stainless steel, including torch angle, travel speed, and weaving technique. Practice on scrap material before working on critical projects.
Inspect and Test: After welding, thoroughly inspect the welds for any defects or imperfections. Perform non-destructive testing, such as visual inspection or dye penetrant testing, to ensure the integrity of the welds.
By following these best practices, you can consistently achieve high-quality gas welds on stainless steel and meet the required standards for your welding projects.
Conclusion and Final Thoughts
Gas welding stainless steel requires a combination of knowledge, skill, and attention to detail. By understanding the properties of stainless steel, following the correct safety precautions, using the right equipment and tools, and mastering the welding techniques, you can produce strong, aesthetically pleasing, and durable welds.
Remember to always prioritize safety and follow the recommended procedures to minimize the risks associated with gas welding. Continuously improve your skills through practice and stay updated with the latest advancements in gas welding technology.
With the essential techniques outlined in this article, you are now equipped to take on gas welding of stainless steel projects with confidence. Embrace the challenges, strive for excellence, and enjoy the rewarding experience of creating high-quality welds on stainless steel.