Gas welding uses a flame produced by burning a fuel gas with oxygen to join metals. It is versatile and widely used in various industries.
Gas welding is a fundamental technique in metalworking. It involves using a flame generated by burning a fuel gas, such as acetylene, with oxygen to heat and join metals. This method is valued for its versatility and ability to weld different types of metals, including steel, aluminum, and copper.
Gas welding equipment is relatively affordable and portable, making it accessible for both hobbyists and professionals. Mastery of gas welding requires understanding the correct gas mixtures, flame settings, and welding techniques to ensure strong, clean welds. This welding method is crucial in automotive repair, construction, and metal fabrication industries.
Introduction To Gas Welding
Gas welding is a popular and versatile welding technique. It is widely used in various industries for its efficiency and cost-effectiveness. This method involves using a flame produced by burning a fuel gas, commonly acetylene, with oxygen. The high-temperature flame melts the metal pieces, allowing them to fuse together upon cooling.
What Is Gas Welding?
Gas welding, also known as oxy-fuel welding, uses a flame to join metals. The flame is produced by mixing oxygen with a fuel gas. Acetylene is the most common fuel gas used in gas welding. This process allows precise control over the heat input, making it suitable for welding thin materials.
Gas welding equipment includes:
- Welding torch
- Fuel gas and oxygen cylinders
- Pressure regulators
- Hoses
- Protective gear
Important benefits of gas welding include:
- Portability
- Versatility
- Cost-effectiveness
History And Evolution
The history of gas welding dates back to the early 1900s. It started with the discovery of acetylene gas and its properties. French chemist Edmond Fouché and engineer Charles Picard introduced oxy-acetylene welding in 1903. This method quickly gained popularity due to its efficiency and ease of use.
The evolution of gas welding saw many improvements:
- Development of safer equipment
- Introduction of new fuel gases
- Advancements in flame control techniques
Today, gas welding remains an essential skill in various industries. Its ability to produce strong and clean welds makes it a preferred choice for many applications.
Types Of Gas Welding
Gas welding is a popular method for joining metals. It uses fuel gases to produce a flame. This flame melts the metal, creating a strong bond. There are several types of gas welding. Each type has unique characteristics and applications.
Oxy-acetylene Welding
Oxy-Acetylene Welding is the most common type of gas welding. It uses a mixture of oxygen and acetylene gases. This combination produces a very hot flame. The flame can reach temperatures up to 3,500 degrees Celsius.
This method is highly versatile. It can weld, cut, and heat metals. Oxy-Acetylene Welding is ideal for general repair work and fabrication. It is also used in metal art and sculpture.
Pros | Cons |
---|---|
Highly versatile | Requires proper safety measures |
Can weld, cut, and heat metals | Risk of gas leaks |
Ideal for general repair | Expensive gas and equipment |
Oxy-hydrogen Welding
Oxy-Hydrogen Welding uses oxygen and hydrogen gases. The flame produced is less hot than Oxy-Acetylene. It reaches temperatures of about 2,800 degrees Celsius.
This type of welding is safer. It has a lower risk of explosion. Oxy-Hydrogen Welding is suitable for delicate tasks. It is often used in jewelry making and scientific applications.
- Pros:
- Safer than Oxy-Acetylene
- Lower risk of explosion
- Suitable for delicate tasks
- Cons:
- Less versatile
- Lower flame temperature
Essential Equipment
Gas welding is a versatile technique. It requires specific tools to ensure safety and efficiency. Understanding the essential equipment is crucial for every welder. Let’s dive into the key components needed for gas welding.
Welding Torches
Welding torches are the heart of gas welding. They mix fuel gas and oxygen for a controlled flame. Torches come in different types:
- Blowpipe torches: Ideal for precision work.
- Cutting torches: Used for cutting metals.
- Heating torches: Designed for heating tasks.
It’s important to choose the right torch for the job. Ensure it has good quality and durability. Proper maintenance extends the lifespan of your torch.
Gas Cylinders
Gas cylinders store the gases needed for welding. Typically, they include oxygen and acetylene. Here’s a brief overview:
Gas | Use | Color Code |
---|---|---|
Oxygen | Supports combustion | Green |
Acetylene | Fuel gas | Red |
Always secure gas cylinders properly. Check for leaks before use. Store them in a cool, dry place. Regular inspections ensure safety and efficiency.
Understanding and maintaining your equipment enhances your welding experience. Safe practices prevent accidents and ensure high-quality results.
Safety Measures
Gas welding is a powerful technique but involves risks. Safety measures are crucial to prevent accidents and injuries. This section discusses protective gear and handling gas cylinders.
Protective Gear
Wearing the right protective gear is essential for safety in gas welding. Here is what you need:
- Welding Helmet: Protects your eyes and face from sparks and bright light.
- Gloves: Use flame-resistant gloves to protect your hands from burns.
- Apron: A flame-resistant apron safeguards your body from sparks and hot metal.
- Safety Glasses: Wear these under your helmet for added eye protection.
- Boots: Use steel-toed boots to protect your feet from falling objects.
Handling Gas Cylinders
Proper handling of gas cylinders is vital to prevent leaks and explosions. Follow these guidelines:
- Storage: Store cylinders in a well-ventilated area, away from heat sources.
- Transportation: Secure cylinders upright during transport to prevent tipping.
- Usage: Open cylinder valves slowly to avoid pressure surges.
- Inspection: Regularly check for leaks using soapy water around the valve.
- Labeling: Ensure cylinders are clearly labeled with their contents.
Preparing For Welding
Welding requires proper preparation for safety and precision. Let’s explore the key steps in preparing for gas welding.
Cleaning The Metal Surface
Cleaning the metal surface ensures a strong weld. Any dirt, rust, or oil can weaken the weld. Follow these steps for a clean surface:
- Use a wire brush to remove rust and dirt.
- Wipe the surface with a clean cloth.
- Use a degreaser to remove oil and grease.
A clean surface leads to better weld quality.
Setting Up The Work Area
A well-organized work area enhances safety and efficiency. Ensure the following:
- Keep the work area clean and free of clutter.
- Ensure proper ventilation to avoid inhaling fumes.
- Have a fire extinguisher nearby for emergencies.
Organize your tools and equipment for easy access. Use a welding table to keep your workspace stable.
By preparing properly, you set the stage for successful welding.
Basic Welding Techniques
Gas welding is an essential skill for metal workers. Knowing the basic welding techniques ensures strong and clean welds. Let’s dive into the fundamentals of gas welding.
Striking The Flame
Striking the flame is the first step in gas welding. Follow these steps for a successful ignition:
- Open the gas valves on your torch slightly.
- Use a spark lighter to ignite the gas.
- Adjust the flame until you get a neutral flame.
A neutral flame has a clear, blue inner cone. This type of flame is ideal for most welding tasks.
Controlling The Heat
Controlling the heat is crucial for quality welds. Here are some tips:
- Adjust the oxygen and acetylene mix to control the flame temperature.
- Move the torch closer or farther from the workpiece to manage heat.
- Practice maintaining a steady hand and pace.
Too much heat can burn through the metal. Too little heat can result in weak welds. Always aim for the right balance.
Understanding these basic techniques will help you achieve better results in your welding projects.
Common Welding Joints
Understanding common welding joints is crucial for beginners in gas welding. Each joint type serves a different purpose. They ensure structural integrity and durability in welded structures. In this section, we will explore two primary types: Butt Joints and Lap Joints.
Butt Joints
Butt joints are the most common type of welding joint. They involve welding two pieces of metal end-to-end. This creates a straight seam. Butt joints are simple to create and provide strong bonds.
Here are some key points about butt joints:
- Alignment: Ensure the metal pieces are aligned perfectly.
- Gap: Maintain a small gap between the pieces for better penetration.
- Weld Type: Use a single or double V-groove weld for thicker metals.
- Strength: Butt joints provide excellent strength if welded correctly.
Butt joints are commonly used in pipe welding and frame construction. They are essential for creating long, straight welds.
Lap Joints
Lap joints involve overlapping two pieces of metal. Weld along the edges of the overlap. These joints are ideal for joining thin sheets of metal.
Key characteristics of lap joints include:
- Overlap: Ensure a sufficient overlap for a strong bond.
- Edge Preparation: Clean edges to remove any contaminants.
- Weld Type: Use a fillet weld along the overlapping edges.
- Application: Ideal for sheet metal and thin materials.
Lap joints are commonly used in automotive and sheet metal work. They provide a strong bond and are easy to create.
Joint Type | Best For | Key Feature |
---|---|---|
Butt Joints | Pipes, Frames | Strong, Straight Seams |
Lap Joints | Sheet Metal | Overlap for Thin Materials |

Credit: www.sciencedirect.com
Troubleshooting Tips
Gas welding is a skill that requires precision. Even experienced welders face issues. Here are troubleshooting tips to help you improve your welds. These tips can save you time and ensure better results.
Addressing Porosity
Porosity in welds can weaken the joint. It looks like tiny holes or bubbles in the weld. Here are some steps to tackle porosity:
- Clean the material: Ensure the welding surface is free of rust, oil, and dirt.
- Check gas flow: Ensure the correct gas flow rate. Too much or too little gas can cause porosity.
- Inspect equipment: Check hoses and connections for leaks. Replace any damaged parts.
- Control torch angle: Maintain a consistent torch angle. This ensures even gas coverage.
Preventing Cracks
Cracks can compromise weld strength. They often occur due to rapid cooling. Follow these tips to prevent cracks:
- Preheat the metal: Warm the material before welding. This reduces temperature differences.
- Use the right filler rod: Match the filler rod to the base material.
- Control cooling rate: Let the weld cool slowly. Use blankets or other methods to insulate the weld.
- Avoid excessive heat: Use the right flame size. Too much heat can cause cracking.
By following these tips, you can address common gas welding issues. This will lead to stronger, cleaner welds.
Advanced Practices
Gas welding is a versatile method used in various industries. As you progress, advanced practices become essential. These techniques ensure strong and precise welds. Let’s explore some advanced gas welding practices.
Welding Different Metals
Different metals require specific considerations during welding. Here are some tips:
- Steel: Use a neutral flame. This prevents oxidation.
- Aluminum: Employ a slightly carburizing flame. It reduces oxidation.
- Copper: Use a neutral flame. This maintains metal integrity.
Check the table below for flame types and their uses:
Metal | Flame Type | Reason |
---|---|---|
Steel | Neutral | Prevents oxidation |
Aluminum | Carburizing | Reduces oxidation |
Copper | Neutral | Maintains integrity |
Multi-pass Welding
Multi-pass welding involves multiple layers for strong joints. Follow these steps:
- Prepare the base metal. Clean it thoroughly.
- Apply the root pass. Ensure full penetration.
- Allow cooling between passes. This prevents warping.
- Repeat the process. Add multiple layers as needed.
- Inspect each pass. Ensure no defects.
Key Points for multi-pass welding:
- Use consistent technique.
- Maintain proper temperature control.
- Ensure thorough inspection.
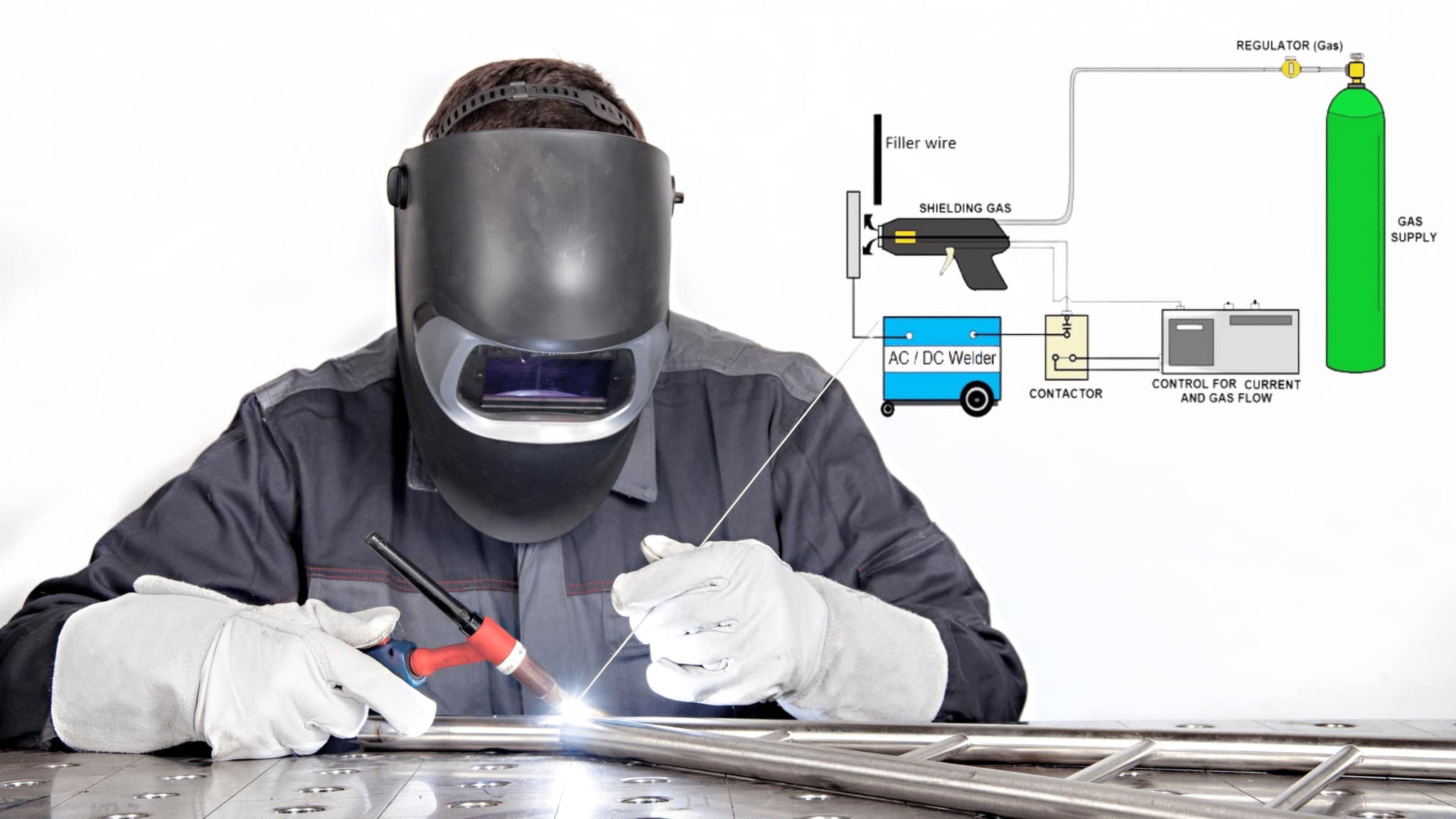
Credit: www.arccaptain.com
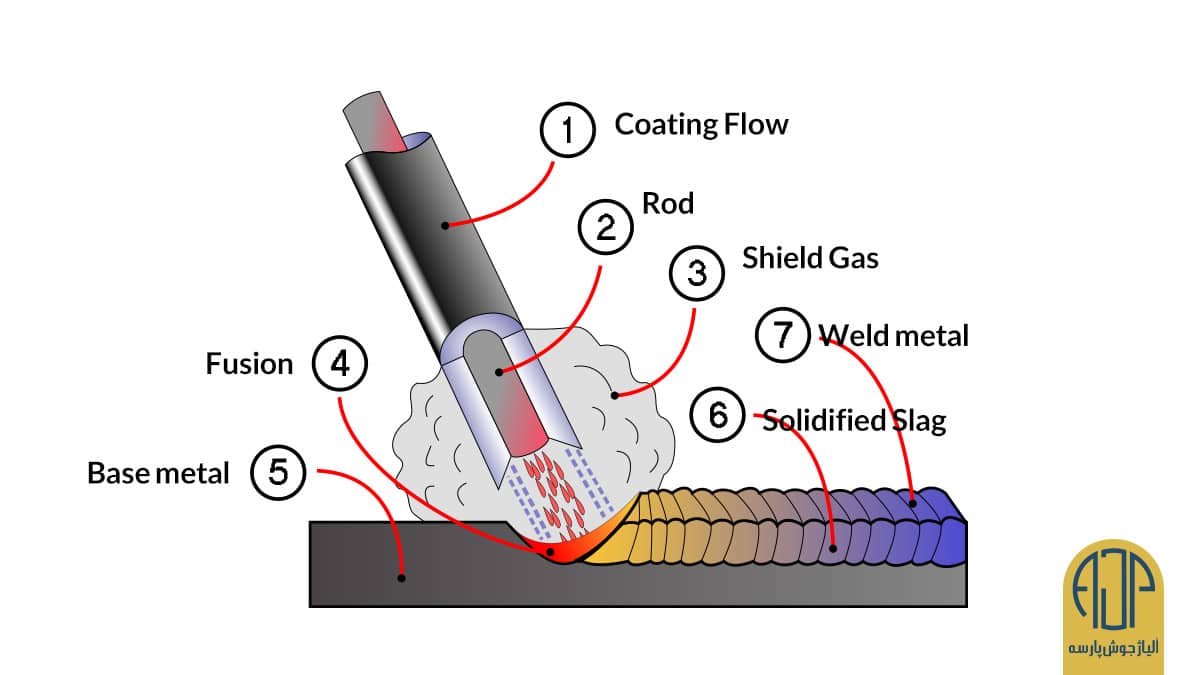
Credit: ajpwelding.com
Frequently Asked Questions
What Is Gas Welding?
Gas welding is a process that uses a flame from burning gas to melt and join metals. It typically involves oxygen and a fuel gas, like acetylene.
How Does Gas Welding Work?
Gas welding works by heating metals with a flame until they melt. Then, a filler material is added to join the metals.
What Equipment Is Needed For Gas Welding?
You need a gas welding torch, oxygen and fuel gas cylinders, regulators, hoses, and protective gear. These tools are essential for safe and effective welding.
Is Gas Welding Safe?
Gas welding is safe when proper precautions are taken. Always use protective gear, maintain equipment, and follow safety guidelines to prevent accidents.
Conclusion
Mastering gas welding basics ensures strong, durable joints. Practice safety and precision for the best results. Embrace the learning process and build your skills gradually. Remember, proper technique and knowledge are key. Happy welding!