Gas welding is a versatile and widely-used welding technique that offers unique advantages and disadvantages for various applications. In this article, we will explore the basics of gas welding, its advantages, disadvantages, and applications.
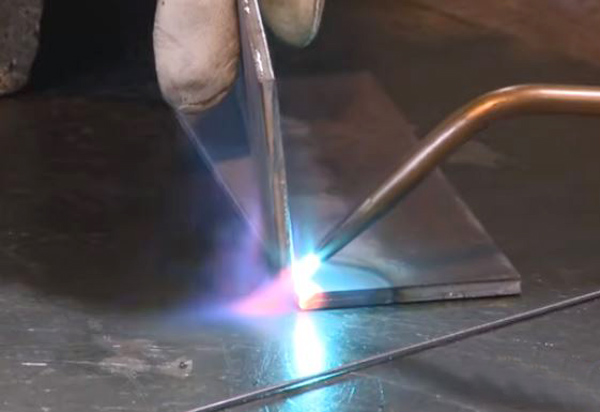
Image Weld.com
What is gas welding?
Gas welding, also known as oxy-fuel welding, utilizes a combination of oxygen and fuel gases, such as acetylene or propane, to generate a flame that melts the metal surfaces to be joined. This method is often preferred for its simplicity, portability, and low equipment costs, making it accessible to both professionals and hobbyists.
Advantages of gas welding
One of the main advantages of gas welding is its versatility. It can be used to weld a wide range of materials, including carbon steel, stainless steel, cast iron, and non-ferrous metals. Gas welding also allows for greater control over heat input, resulting in less distortion and warping. The flame produced by gas welding is highly concentrated, enabling precise and intricate welds.
Another advantage of gas welding is its ability to work in various positions, including vertical and overhead. This makes it suitable for welding in tight spaces or on complex shapes. Gas welding also produces a clean weld with minimal spatter, reducing the need for post-weld cleanup.
Gas welding equipment is portable and can be easily transported to job sites. The low cost of equipment and consumables makes gas welding an economical choice for small-scale projects or occasional welding needs. It is also a preferred method for outdoor welding, as it does not require an electrical power source.
Disadvantages of gas welding
Gas welding also has its limitations. It is slower compared to other welding methods, such as arc welding, and may not be suitable for high-speed production. The speed of gas welding largely depends on the skill and experience of the welder, as well as the size and complexity of the joint.
Gas welding also requires careful monitoring of gas flow rates, flame temperature, and joint cleanliness to achieve proper fusion. Improper control of these variables can result in weak or defective welds. Additionally, gas welding is not suitable for welding certain metals, such as aluminum, as it can cause excessive heat input and distortion.
Gas welding equipment and materials
To perform gas welding, you will need a welding torch, gas cylinders, regulator, hoses, and a welding rod or filler metal. The most commonly used fuel gas for gas welding is acetylene, known for its high flame temperature and versatility. Propane and propylene are also used as fuel gases, offering lower flame temperatures but greater stability and safety.
The welding torch consists of a handle, mixing chamber, and various tips or nozzles to control the flame size and shape. The size of the welding tip depends on the thickness of the metal being welded. The gas cylinders contain compressed oxygen and fuel gases, which are connected to the welding torch through hoses and regulated by flow meters.
The filler metal used in gas welding can be in the form of a welding rod or wire. It is chosen based on the type of metal being welded and the desired strength and properties of the weld. The filler metal is melted by the flame and added to the joint to create the weld pool.
Gas welding Basics- techniques and safety precautions
Gas welding requires proper technique and safety precautions to ensure successful and safe welds. The following are some key techniques and precautions to consider:
Joint preparation
Before welding, the metal surfaces to be joined must be clean and free of contaminants. Use a wire brush or grinder to remove rust, paint, and other impurities. Proper joint preparation ensures better fusion and stronger welds.
Flame adjustment
Adjust the flame size and shape according to the welding requirements. A neutral flame, with a balanced mixture of oxygen and fuel gas, is commonly used for most welding applications. The flame should be directed towards the joint, allowing the heat to melt the metal.
Welding technique
Move the welding torch steadily along the joint, maintaining a consistent speed and distance from the workpiece. The torch should be angled slightly towards the direction of travel, ensuring proper heat penetration and fusion. Practice and experience are key to achieving smooth and uniform welds.
Safety precautions
Gas welding involves the use of flammable gases and high temperatures, so it is important to follow safety guidelines to prevent accidents. Wear appropriate protective gear, including gloves, goggles, and flame-resistant clothing. Ensure proper ventilation in the welding area and have a fire extinguisher nearby. Regularly inspect and maintain the gas welding equipment to prevent leaks or malfunctions.
Applications of gas welding in various industries
Regardless of its disadvantages, gas welding finds applications in various industries, including automotive, construction, and manufacturing. It is commonly used for repairs, fabrication, and maintenance work. Some specific applications of gas welding include:
Automotive repairs
Gas welding is used to repair or fabricate exhaust systems, fuel tanks, and body panels. It can also be used for welding suspension components, brackets, and other metal parts.
Construction and infrastructure
Gas welding is commonly used in construction for welding structural steel, pipes, and reinforcing bars. It is also used for repairs and maintenance of metal structures, such as bridges and buildings.
Manufacturing and fabrication
Gas welding is employed in various manufacturing processes, including the production of furniture, appliances, and metal components. It is used to join different metal parts together or repair defective welds.
Artistic and decorative work
Gas welding allows for precise control and intricate welds, making it suitable for artistic and decorative metalwork. It is often used in sculptures, ornamental gates, and custom metal furniture.
Gas welding vs other welding methods
Gas welding is just one of many welding methods available today. Each method has its own advantages and limitations, making it suitable for specific applications. Here are some comparisons between gas welding and other common welding methods:
Arc welding
Arc welding, such as shielded metal arc welding (SMAW) or gas metal arc welding (GMAW), offers higher welding speeds and is suitable for high-volume production. Gas welding provides better control over heat input and is more versatile in terms of materials.
Tungsten inert gas (TIG) welding
TIG welding offers precise control and produces high-quality welds, especially on thin materials. Gas welding, on the other hand, is more cost-effective and can be performed without the need for electricity.
Resistance welding
Resistance welding, such as spot welding or seam welding, is commonly used for joining sheet metal or wire. Gas welding is preferred for thicker materials or when a stronger weld is required.
Gas welding certifications and training programs
To become a skilled gas welder, it is important to undergo proper training and obtain certifications. Various organizations and institutes offer gas welding training programs, covering the basics of gas welding, safety procedures, and hands-on practice. Some certifications recognized in the industry include:
American Welding Society (AWS)
AWS offers certifications for gas welders, including the Certified Welder (CW) and Certified Welding Inspector (CWI) programs. These certifications validate the skills and knowledge of gas welders and are highly regarded by employers.
Technical and vocational schools
Many technical and vocational schools offer gas welding courses as part of their welding programs. These courses provide comprehensive training in gas welding techniques, equipment operation, and safety precautions.
Apprenticeship programs
Some employers offer apprenticeship programs, allowing aspiring welders to gain hands-on experience under the guidance of experienced professionals. These programs typically combine on-the-job training with classroom instruction.
Common mistakes to avoid in gas welding
Gas welding, like any other welding method, requires practice and attention to detail. To ensure successful welds and avoid common mistakes, consider the following:
Improper joint preparation
Neglecting proper joint cleaning and preparation can lead to poor fusion and weak welds. Take the time to clean the metal surfaces thoroughly before welding.
Inadequate flame adjustment
A poorly adjusted flame can result in incomplete fusion or excessive heat input. Regularly check and adjust the flame to maintain a proper balance of oxygen and fuel gas.
Incorrect travel speed
Welding too slowly or too quickly can affect the quality of the weld. Practice maintaining a consistent travel speed to achieve uniform and strong welds.
Insufficient gas flow
Insufficient gas flow can lead to a weak flame and inadequate heat for proper fusion. Ensure that the gas cylinders are properly connected and the flow rates are adjusted according to the welding requirements.
Conclusion
Gas welding offers unique advantages and disadvantages for various applications. Its versatility, control over heat input, and portability make it a preferred choice for many welders. However, it is important to consider its limitations, such as slower welding speed and the need for careful monitoring of variables. Gas welding finds applications in automotive, construction, manufacturing, and artistic industries, among others.
By following proper techniques, safety precautions, and avoiding common mistakes, gas welders can achieve successful and strong welds. Invest in proper training and certifications to enhance your skills and open up opportunities in the welding industry. So go ahead, explore the potential of gas welding basics and take your welding projects to the next level.