Looking to join the welding world but confused about which method to choose? Flux core welding and MIG (Metal Inert Gas) are two popular options, each with their own advantages and applications. In this article, we will compare and contrast the two, helping you make an informed decision based on your needs and preferences.
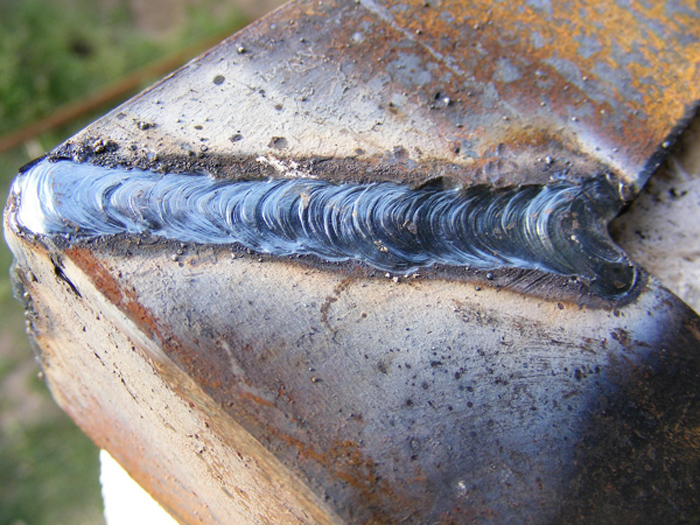
Photo by pixabay
What is Flux Core Welding?
Flux core welding, also known as FCAW (Flux-Cored Arc Welding), utilizes a continuous feed of tubular electrode filled with flux. This process generates a shielding gas that protects the weld from impurities and contaminants, making it ideal for outdoor applications and windy conditions.
One of the main advantages of flux core welding is its ability to penetrate through thick materials. The flux in the electrode creates a slag that covers the weld, allowing it to cool slowly and providing additional protection against oxidation. This results in stronger and more durable welds, especially in heavy-duty applications such as structural steel fabrication and shipbuilding.
Another benefit of flux core welding is its versatility. It can be used with a wide range of materials, including carbon steel, stainless steel, and even some non-ferrous metals. This makes it a popular choice for various industries, from construction and automotive to oil and gas.
Flux core welding does have its drawbacks. The process produces more smoke and fumes compared to MIG welding, which may require additional ventilation and safety precautions. The flux core wire tends to be more expensive than solid wire used in MIG welding, increasing the overall cost of the process.
Overall, flux core welding is a reliable and efficient method that excels in heavy-duty applications and outdoor environments.
What is MIG Welding?
MIG welding, also known as Gas Metal Arc Welding (GMAW), uses a solid wire electrode and an inert gas like argon or helium to create a protective atmosphere around the weld. This method is commonly used for thinner materials, precision work, and in clean environments.
One of the main advantages of MIG welding is its ease of use. The process is relatively simple and straightforward, making it suitable for beginners and hobbyists. With a stable arc and minimal spatter, MIG welding produces clean and aesthetically pleasing welds. MIG welding also offers excellent control over the heat input, allowing for precise welds on thin materials. This makes it a popular choice in industries such as automotive, aerospace, and electronics, where precision and aesthetics are crucial.
Another advantage of MIG welding is its efficiency. The continuous wire feeding system allows for uninterrupted welding, increasing productivity and reducing downtime. Additionally, the absence of flux eliminates the need for post-weld cleaning, saving time and effort. MIG welding is not without its limitations. It is not suitable for outdoor applications or windy conditions, as the shielding gas can easily be disrupted. Thicker materials may also require multiple passes, increasing the welding time and complexity.
In summary, MIG welding is a versatile and efficient method that is ideal for thin materials, precision work, and clean environments.
Pros and Cons of Flux Core Welding
Pros of Flux Core Welding: Excellent penetration and strength in thick materials – Versatile, suitable for a wide range of materials – Ideal for outdoor applications and windy conditions
Cons of Flux Core Welding: Produces more smoke and fumes compared to MIG welding – Flux core wire can be more expensive than solid wire used in MIG welding
Flux core welding is a reliable and efficient method that excels in heavy-duty applications and outdoor environments. Its excellent penetration and strength make it a popular choice for industries such as construction, shipbuilding, and oil and gas. The process does produce more smoke and fumes, requiring additional ventilation and safety precautions. The cost of flux core wire is also higher than solid wire used in MIG welding, which should be taken into consideration when selecting the welding method.
Pros and Cons of MIG Welding
Pros of MIG Welding: Easy to use, suitable for beginners and hobbyists – Produces clean and aesthetically pleasing welds – Excellent control over heat input, ideal for thin materials
Cons of MIG Welding: Not suitable for outdoor applications or windy conditions – Thicker materials may require multiple passes
MIG welding is a versatile and efficient method that is ideal for thin materials, precision work, and clean environments. Its ease of use and ability to produce clean and aesthetically pleasing welds make it popular in industries such as automotive, aerospace, and electronics. It is not suitable for outdoor applications or windy conditions, as the shielding gas can easily be disrupted. Thicker materials may also require multiple passes, increasing the welding time and complexity.
Cost Comparison
When comparing the cost of flux core welding and MIG welding, several factors need to be taken into consideration. The cost of equipment, consumables, and overall productivity can vary depending on the specific requirements of the project.
Flux core welding generally requires more specialized equipment compared to MIG welding. The flux core welding machine itself may be more expensive, and additional accessories such as flux core wire and gas cylinders may also add to the cost. The higher cost of equipment can be offset by the lower cost of consumables, as flux core wire is generally cheaper than solid wire used in MIG welding.
In terms of productivity, MIG welding has the advantage of continuous wire feeding, allowing for uninterrupted welding and increased efficiency. Flux core welding, on the other hand, may require more frequent stops to replace the flux core wire, resulting in longer welding times and reduced productivity.
Ultimately, the cost comparison between flux core welding and MIG welding will depend on the specific project requirements and budget constraints. It is advisable to consult with welding professionals or suppliers to get accurate cost estimates based on your specific needs.
Skill Level Requirement
When it comes to skill level requirement, both flux core welding and MIG welding have their own learning curves.
Flux core welding requires a certain level of expertise to achieve optimal results. The nature of the process, with its flux-filled electrode and shielding gas, requires the welder to have a good understanding of welding techniques, settings, and parameters. The higher level of smoke and fumes produced during flux core welding may require the welder to be more knowledgeable about safety precautions and ventilation.
MIG welding, on the other hand, is considered to be more beginner-friendly. The process is relatively simple and straightforward, making it easier for beginners to learn and master. With a stable arc and minimal spatter, MIG welding is forgiving and allows for easier control over the weld.
It is important to note that while MIG welding may be easier to learn, achieving high-quality welds still requires practice and experience. Proper technique, positioning, and understanding of welding parameters are essential for producing strong and reliable welds.
Both flux core welding and MIG welding require a certain level of skill and knowledge. While MIG welding is generally considered to be more beginner-friendly, both processes require practice and experience to achieve optimal results.
Applications and Versatility
Flux core welding vs MIG welding have different applications and levels of versatility, making them suitable for different types of projects.
Flux core welding is known for its strength and penetration, making it ideal for heavy-duty applications. It is commonly used in industries such as construction, shipbuilding, and oil and gas, where thick materials and structural integrity are paramount. The ability to weld a wide range of materials, including carbon steel, stainless steel, and some non-ferrous metals, adds to its versatility.
MIG welding, on the other hand, is often used in industries that require precision and aesthetics. Its ability to produce clean and aesthetically pleasing welds makes it popular in automotive, aerospace, and electronics industries. MIG welding is also suitable for thin materials, as it offers excellent control over the heat input.
Both flux core welding and MIG welding have their limitations. Flux core welding is not suitable for thin materials and precision work, as it tends to produce a rougher surface finish. MIG welding, on the other hand, is not recommended for outdoor applications or windy conditions, as the shielding gas can easily be disrupted.
The choice between flux core welding vs MIG welding will depend on the specific requirements of the project. Flux core welding is ideal for heavy-duty applications and outdoor environments, while MIG welding excels in precision work and clean environments.
Weld Quality and Strength
When comparing the weld quality and strength of flux core welding and MIG welding, several factors need to be taken into consideration.
Flux core welding is known for its excellent penetration and strength, especially in thick materials. The flux in the electrode creates a slag that covers the weld, allowing it to cool slowly and providing additional protection against oxidation. This results in stronger and more durable welds, making flux core welding suitable for heavy-duty applications.
MIG welding, on the other hand, produces clean and aesthetically pleasing welds. The absence of flux eliminates the need for post-weld cleaning, resulting in a smoother surface finish. While MIG welding may not have the same level of penetration as flux core welding, it can still produce strong and reliable welds, especially on thin materials.
It is important to note that the quality and strength of the welds depend not only on the welding method but also on the skill and technique of the welder. Proper preparation, positioning, and understanding of welding parameters are essential for producing high-quality welds.
Both flux core welding and MIG welding can produce strong and reliable welds. Flux core welding excels in heavy-duty applications, while MIG welding offers clean and aesthetically pleasing welds. The choice between the two will depend on the specific requirements of the project and the skill level of the welder.
Choosing the Right Welding Method
Both flux core welding and MIG welding have their own advantages and applications. Flux core welding is ideal for heavy-duty applications and outdoor environments, offering excellent penetration and strength. MIG welding, on the other hand, is suitable for thin materials, precision work, and clean environments, producing clean and aesthetically pleasing welds.
When choosing the right welding method, it is important to consider factors such as project requirements, budget constraints, skill level, and the specific materials to be welded. Consulting with welding professionals or suppliers can provide valuable insights and help you make an informed decision.
The choice between flux core welding vs MIG welding will depend on your needs and preferences. By understanding the differences between the two methods, you will be able to select the technique that suits your specific requirements and embark on your welding journey with confidence.