Fiber laser welding is revolutionizing the manufacturing industry with its precise and efficient capabilities. As a cutting-edge technology, it offers a more advanced and effective approach to the traditional welding process. But how does fiber laser welding work exactly? Well, it all starts with a high-intensity laser beam that is focused and concentrated through an optical fiber. This beam is then directed towards the material to be welded, creating a concentrated heat source that quickly melts and joins the metal together. The accuracy and control provided by fiber laser welding result in stronger and higher-quality welds.
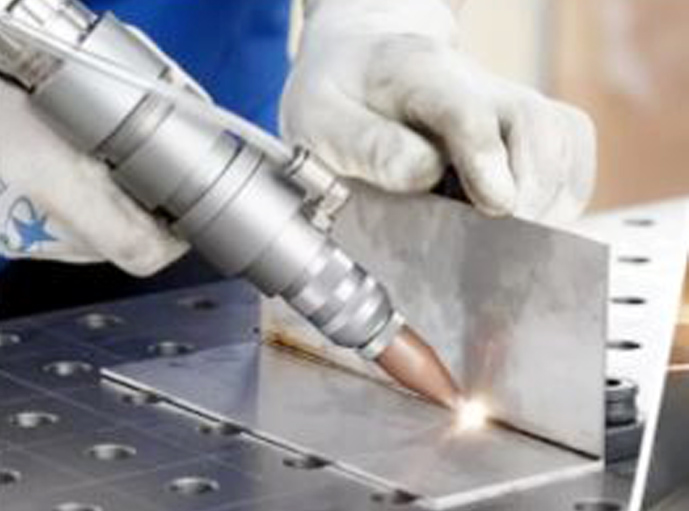
Image: weldingpros.net
How Does Fiber Laser Welding Work?
Fiber laser welding works by utilizing a high-intensity laser beam that is generated by a fiber laser source. The laser beam is then focused and concentrated through an optical fiber, which acts as a conduit for the laser energy. This allows the laser beam to be directed precisely towards the material to be welded.
When the laser beam reaches the material, it creates a concentrated heat source that rapidly melts and fuses the metal together. The high energy density of the laser beam ensures that the heat is localized, minimizing the heat-affected zone and reducing the risk of distortion or damage to the surrounding material.
The process of fiber laser welding can be controlled and automated using computer numerical control (CNC) systems, which allow for precise positioning and movement of the laser beam. This ensures consistent and accurate welds, even in complex geometries.
Fiber laser welding is particularly effective for welding thin materials, as the focused laser beam provides a narrow heat-affected zone, reducing the risk of burn-through and distortion. It also offers high welding speeds, making it a fast and efficient process for industrial applications.
Advantages of Fiber Laser Welding
Fiber laser welding offers several advantages over traditional welding techniques. One of the main advantages is its ability to weld a wide range of materials, including metals with different melting points. This makes it a versatile option for various industries, including automotive, aerospace, and electronics.
Another advantage of fiber laser welding is its high precision and accuracy. The focused laser beam allows for fine control over the welding process, resulting in stronger and higher-quality welds. This is particularly important for applications that require high structural integrity, such as in the aerospace industry.
Fiber laser welding also offers excellent repeatability, as the process can be easily automated and controlled using CNC systems. This ensures consistent weld quality and reduces the risk of human error. Additionally, fiber welding is a non-contact process, which eliminates the need for physical contact with the material and reduces the risk of contamination or damage.
Furthermore, fiber laser welding is an energy-efficient process, as the laser beam can be easily directed and focused on the desired area. This reduces the amount of heat generated and minimizes energy wastage, making it a more environmentally friendly option compared to traditional welding methods.
However, it is important to note that fiber laser welding does have some disadvantages that need to be considered.
Disadvantages of Fiber Laser Welding
One of the main disadvantages of fiber laser welding is the initial high cost of equipment. Fiber lasers are expensive to purchase and maintain, making it a significant investment for companies. It is worth noting that the long-term cost savings in terms of increased productivity and reduced rework can offset the initial investment.
Another disadvantage of fiber laser welding is the need for skilled operators who can optimize the settings for each welding task. The process requires expertise in laser technology, material science, and welding techniques. This means that companies need to invest in training and education to ensure that their operators are proficient in fiber laser welding.
Additionally, fiber welding may not be suitable for all applications. It is primarily used for thin materials, and it may not be suitable for thicker or highly reflective materials. In such cases, alternative welding methods may be more appropriate.
Despite these disadvantages, fiber laser welding remains a highly effective and efficient welding technique that offers numerous benefits for various industries.
Techniques Used in Fiber Laser Welding
Fiber laser welding can be performed using different techniques, depending on the specific requirements of the application. Some common techniques include:
- Conduction mode welding: This technique is used for welding thin materials. The laser beam is focused on the surface of the material, creating a shallow weld pool. Heat is conducted through the material, melting the edges and joining them together.
- Deep penetration welding: This technique is used for welding thicker materials. The laser beam is focused on the surface of the material, creating a deep weld pool. The high energy density of the laser beam vaporizes the material, creating a keyhole effect. The keyhole is then filled with molten metal, resulting in a strong and deep penetration weld.
- Laser cladding: This technique is used for surface modification and repair. A layer of metal powder or wire is deposited on the surface of the material, and the laser beam is used to melt and fuse the deposited material with the base material. This can be used to enhance the surface properties of the material or repair damaged parts.
The choice of technique depends on factors such as material thickness, joint design, and desired weld characteristics.
Applications of different Industries
Fiber laser welding is widely used in various industries due to its versatility and efficiency. Some common applications include:
- Automotive industry: Fiber laser welding is used for welding car body components, exhaust systems, and fuel tanks. It provides high-quality welds with minimal distortion and excellent corrosion resistance.
- Aerospace industry: Fiber laser welding is used for joining critical components in aircraft structures, such as fuel tanks, engine parts, and landing gear. The high precision and strength of fiber laser welds make them ideal for aerospace applications.
- Electronics industry: Fiber welding is used for joining electronic components, such as connectors, sensors, and batteries. The non-contact nature of the process ensures minimal heat input and reduces the risk of damage to sensitive electronic parts.
- Medical industry: Fiber laser welding is used for joining medical devices and implants, such as pacemakers, stents, and surgical instruments. The precise control and minimal heat input of fiber laser welding ensure biocompatibility and high-quality welds.
These are just a few examples of the wide range of applications where fiber laser welding is utilized. As the technology continues to advance, new applications are constantly being discovered.
Comparison of Fiber Laser with Other Welding Techniques
Fiber laser welding offers several advantages over traditional welding techniques, such as arc welding and resistance welding. Here are some key points of comparison:
- Speed: Fiber laser welding is significantly faster than traditional welding techniques. The high power density of the laser beam allows for rapid heating and cooling, resulting in shorter cycle times.
- Precision: Fiber laser welding provides higher precision and accuracy compared to traditional welding techniques. The focused laser beam allows for fine control over the welding process, resulting in stronger and higher-quality welds.
- Heat input: Fiber laser welding generates less heat compared to traditional welding techniques. This reduces the risk of distortion and damage to the surrounding material, making it suitable for thin and heat-sensitive materials.
- Versatility: Fiber laser welding can weld a wide range of materials, including metals with different melting points. This makes it a versatile option for various industries.
- Automation: Fiber welding can be easily controlled and automated using CNC systems. This ensures consistent weld quality and reduces the risk of human error.
It is important to consider the specific requirements of the application when choosing between fiber laser welding and other welding techniques.
Factors to Consider When Choosing Welding Equipment
When choosing fiber welding equipment, several factors need to be considered. These include:
- Power and energy: The power and energy output of the fiber laser source determine the welding speed and penetration depth. Higher power lasers are suitable for thicker materials or applications that require deep penetration.
- Beam quality: The beam quality affects the focus ability and stability of the laser beam. A high-quality beam ensures precise and consistent welding.
- Beam delivery system: The beam delivery system consists of optical fibers, beam switches, and focusing optics. It should be designed to minimize energy losses and provide reliable and efficient laser beam delivery.
- Control system: The control system should allow for precise control over laser power, pulse duration, and other welding parameters. It should also provide real-time monitoring and feedback to ensure consistent weld quality.
- Maintenance and support: Consider the availability of technical support, spare parts, and maintenance services when choosing a fiber laser welding system. It is important to work with a reputable supplier that can provide timely assistance and minimize downtime.
By considering these factors, companies can select the most suitable fiber laser welding equipment for their specific needs.
Conclusion
Fiber laser welding is a highly advanced and efficient welding technique that is revolutionizing the manufacturing industry. Its precise control, versatility, and high-quality welds make it a preferred choice for various applications in industries such as automotive, aerospace, electronics, and medical.
While fiber welding offers numerous advantages, it also has some disadvantages, such as the initial high cost of equipment and the need for skilled operators. However, the long-term benefits and cost savings often outweigh these challenges.
By understanding the principles, techniques, advantages, and disadvantages of fiber laser welding, companies can make informed decisions about adopting this cutting-edge technology. With proper training, certification, and the right equipment, they can harness the full potential of fiber welding and stay ahead in the competitive manufacturing landscape.