Welding is a process of joining two or more materials together by applying heat, pressure, or both. It is widely used across various industries, including construction, manufacturing, and automotive. Welding is not a simple process, and there are several factors that can affect the quality and durability of the weld. In this article, I will explore the factors that affect welding and how they can impact the final outcome.
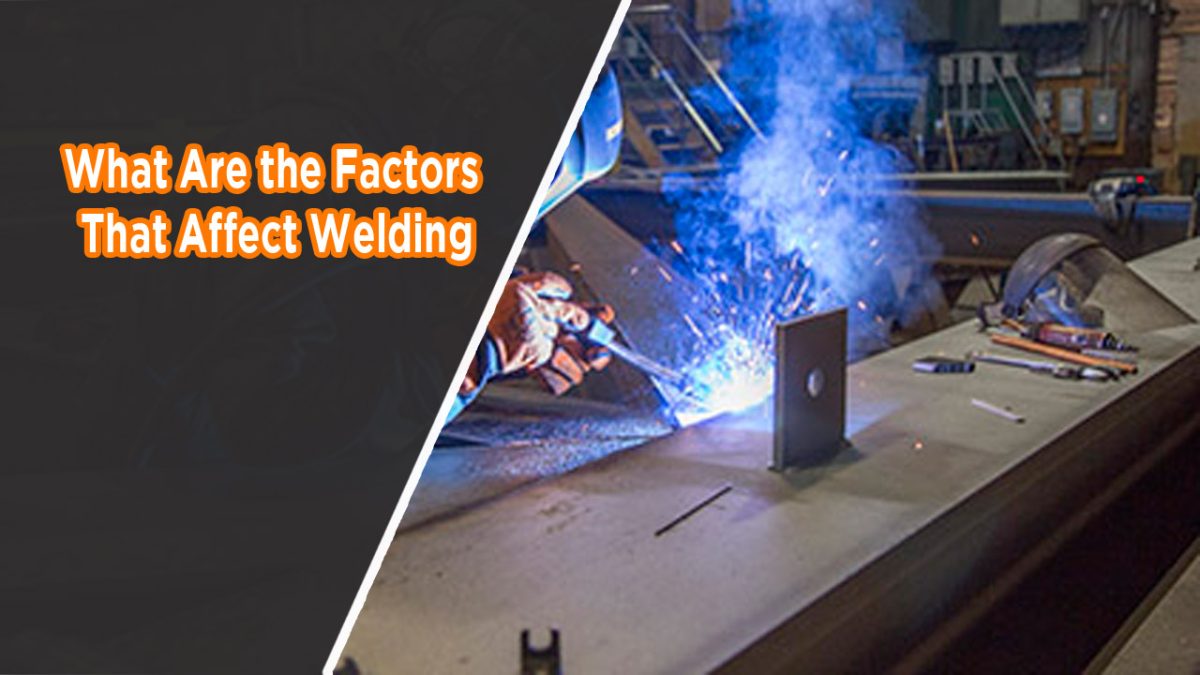
Image by hobartbrothers
One of the most critical factors that affect welding is the welding process itself. There are several welding processes, including MIG, TIG, Stick, and Flux-Cored, and each has its unique characteristics. The choice of the welding process depends on various factors, such as the type of material being welded, the thickness of the material, and the desired outcome. Each welding process has its advantages and disadvantages, and it’s essential to choose the right process for the job to achieve the desired results.
Another critical factor that affects welding is the welding technique. Welding technique refers to the way the welder manipulates the welding equipment, including the angle of the torch, the speed of the weld, and the distance between the torch and the material being welded. The welding technique can significantly impact the quality of the weld, and it’s essential to use the right technique for the job. A skilled welder can adjust the welding technique to compensate for other factors that may affect the weld, such as the type of material being welded and the welding process being used.
Material Properties
As the name suggests, material properties refer to the characteristics of the base metals that are being welded. These properties play a significant role in determining the quality of the weld and the overall success of the welding process. There are several material properties that can affect welding, including the type of base metals, metal thickness, and metal surface conditions.
Type of Base Metals
The type of base metal being used in welding can have a significant impact on the weldability of the material. Some metals, such as aluminum and copper, have high thermal conductivity, which means they require more heat to melt and can be more challenging to weld. On the other hand, materials like steel and titanium have lower thermal conductivity and are easier to weld. It is essential to understand the properties of the base metal being used to determine the appropriate welding technique and equipment required for a successful weld.
Metal Thickness
The thickness of the metal being welded is another critical factor that can affect the welding process. Thicker metals require more heat and energy to melt, which can result in longer welding times and more significant heat input. This can increase the risk of distortion, warping, and cracking. It is important to select the appropriate welding technique and equipment for the thickness of the material being welded to ensure proper penetration and a successful weld.
Metal Surface Conditions
The surface condition of the metal being welded can also impact the welding process. Materials with rust, oil, or other contaminants on the surface can result in poor weld quality and porosity. It is crucial to prepare the metal surface properly by removing any contaminants and ensuring a clean, smooth surface for welding. This can be achieved through various methods such as grinding, sandblasting, or chemical cleaning.
Material properties play a critical role in determining the success of the welding process. Understanding the type of base metals, metal thickness, and metal surface conditions is essential in selecting the appropriate welding technique and equipment for a successful weld.
Welding Processes
When it comes to welding, there are several processes that can be used to join two or more materials together. Each process has its own advantages and disadvantages, and the choice of process will depend on the specific application. In this section, I will discuss some of the most common welding processes.
Gas Metal Arc Welding (GMAW)
Gas Metal Arc Welding, also known as GMAW or MIG welding, is a process that uses a wire electrode and a shielding gas to join two metals together. The wire electrode is fed through a welding gun and melts as it comes into contact with the base metal. The shielding gas, usually a mixture of argon and carbon dioxide, is used to protect the weld from contamination.
GMAW is a versatile process that can be used on a variety of metals, including aluminum, stainless steel, and mild steel. It is also a relatively fast process, making it ideal for high-volume production environments.
Shielded Metal Arc Welding (SMAW)
Shielded Metal Arc Welding, also known as SMAW or stick welding, is a process that uses a consumable electrode coated in flux to join two metals together. The flux creates a shield around the weld, protecting it from contamination.
SMAW is a popular welding process because it is relatively easy to learn and can be used on a wide variety of metals. It is also a portable process, making it ideal for fieldwork.
Tungsten Inert Gas Welding (TIG)
Tungsten Inert Gas Welding, also known as TIG welding, is a process that uses a non-consumable tungsten electrode and a shielding gas to join two metals together. The weld area is protected from contamination by the shielding gas, which is usually argon or helium.
TIG welding is a precise process that can be used on a variety of metals, including stainless steel, aluminum, and copper alloys. It is also a slow process, making it ideal for applications that require a high level of precision.
Submerged Arc Welding (SAW)
Submerged Arc Welding, also known as SAW, is a process that uses a consumable electrode and a granular flux to join two metals together. The flux creates a protective shield around the weld, protecting it from contamination.
SAW is a fast process that can be used on thick sections of metal. It is also a highly efficient process, making it ideal for high-volume production environments.
Overall, each welding process has its own advantages and disadvantages, and the choice of process will depend on the specific application. By understanding the different welding processes available, you can choose the right process for your needs.
Welding Parameters
Welding parameters are the settings that determine the quality and strength of a weld. These parameters include current and voltage settings, welding speed, and heat input. By adjusting these parameters, a welder can control the size, shape, and penetration of the weld.
Current and Voltage Settings
Current and voltage settings are crucial in welding because they determine the amount of heat that is applied to the metal. According to MillerWelds, the current amperage generally dictates the size and penetration of a weld bead when you’re moving your torch at the right speed. Voltage, on the other hand, affects the arc length and the quality of the weld.
Welding Speed
Welding speed is another important parameter that affects the quality of the weld. If the welding speed is too slow, the heat input will be too high, resulting in a wide bead with poor penetration. On the other hand, if the welding speed is too fast, the heat input will be too low, resulting in a narrow bead with insufficient penetration. According to WeldingClarity, the welding speed should be adjusted based on the thickness of the metal being welded.
Heat Input
Heat input is the amount of heat that is applied to the metal during welding. According to Welding Heaven, heat input is determined by the welding current, voltage, and welding speed. If the heat input is too high, the metal will become overheated, resulting in distortion and warping. If the heat input is too low, the weld will be weak and lack penetration.
In conclusion, welding parameters are essential in achieving a high-quality weld. By adjusting the current and voltage settings, welding speed, and heat input, a welder can control the size, shape, and penetration of the weld.
Welder Skill and Technique
Welding requires a high level of skill and technique to produce high-quality welds. The skills of the welder can have a significant impact on the quality of the finished weld. The following subsections provide more details about the importance of welder skill and technique in welding.
Welder Certification
Welder certification is a process that verifies a welder’s skills and knowledge in a specific welding process. Welder certification is typically required by industry standards and regulations. Welder certification is important because it ensures that the welder has the necessary skills and knowledge to perform the welding task correctly.
Welder Experience
Welder experience is another important factor that affects the quality of the weld. Experienced welders have a better understanding of the welding process, which allows them to produce high-quality welds consistently. Experienced welders also have a better understanding of the materials being welded, which allows them to select the correct welding parameters and techniques.
Consistency and Control
Consistency and control are critical factors that affect the quality of the weld. Consistency refers to the ability of the welder to produce welds that meet the same quality standards repeatedly. Control refers to the ability of the welder to control the welding process to produce welds that meet the desired quality standards. Welders must have a high level of consistency and control to produce high-quality welds consistently.
Welder skill and technique are critical factors that affect the quality of the weld. Welder certification, experience, consistency, and control are all important factors that contribute to the quality of the finished weld. Welders must have a high level of skill and technique to produce high-quality welds consistently.
Equipment and Technology
As a welder, I know that the equipment and technology used in welding have a significant impact on the quality and efficiency of the welding process. In this section, I will discuss the three main elements of equipment and technology that affect welding: welding machines, welding consumables, and automation and control systems.
Welding Machines
Welding machines are an essential component of the welding process. The type and condition of the welding machine can significantly impact the quality and efficiency of the weld. Welding machines come in various types, including Stick, MIG, TIG, and Flux-cored welding machines. Each type of welding machine has its advantages and disadvantages, and the choice of the machine depends on the welding process and the material being welded.
The condition of the welding machine also plays a vital role in the welding process. Proper maintenance of the welding machine is essential to ensure that it operates at optimal performance. Regular cleaning, inspection, and calibration of the welding machine can prevent issues that may affect the quality and efficiency of the weld.
Welding Consumables
Welding consumables, such as electrodes, wires, and shielding gases, are essential components of the welding process. The type and quality of welding consumables used can significantly impact the quality and efficiency of the weld. Using the wrong welding consumables can lead to poor quality welds, while using high-quality consumables can result in a strong and efficient weld.
The choice of welding consumables depends on the welding process, the material being welded, and the desired weld quality. It is essential to use the right welding consumables for the job to ensure that the weld is of the required quality and strength.
Automation and Control Systems
Automation and control systems are becoming increasingly popular in the welding industry. These systems use robots and other automated equipment to perform welding tasks, resulting in increased efficiency and precision. Automation and control systems also reduce the risk of human error, leading to better weld quality.
The use of automation and control systems requires specialized training and expertise. Welders need to be familiar with the equipment and technology used in these systems to operate them effectively. Additionally, regular maintenance and calibration of the automation and control systems are essential to ensure that they operate at optimal performance.
The equipment and technology used in welding have a significant impact on the quality and efficiency of the welding process. Welding machines, welding consumables, and automation and control systems are essential components of the welding process that require proper maintenance, calibration, and expertise to ensure optimal performance.
Environmental Conditions
Welding is a process that can be affected by various environmental conditions. In this section, I will discuss the impact of ambient temperature, humidity, wind speed, and drafts on welding.
Ambient Temperature
Ambient temperature can have a significant impact on welding. When the temperature is too low, it can cause the metal to become brittle, making it more difficult to weld. On the other hand, when the temperature is too high, it can cause the metal to warp, making it difficult to maintain the correct shape.
To ensure that the metal is at the right temperature, it is essential to monitor the ambient temperature carefully. Welding should be done in an area where the temperature is stable and within the recommended range for the type of metal being welded.
Humidity
Humidity is another factor that can affect welding. High humidity can cause moisture to form on the metal surface, making it difficult to weld. It can also cause porosity in the weld, reducing its strength.
To prevent these issues, it is important to keep the welding area dry. This can be achieved by using a dehumidifier or by welding in an area with low humidity.
Wind Speed and Drafts
Wind speed and drafts can also have a significant impact on welding. Strong winds can blow away shielding gas, causing porosity in the weld. Drafts can also cause the shielding gas to be blown away, making it difficult to maintain a stable arc.
To prevent these issues, it is important to weld in an area with minimal wind and drafts. If it is not possible to avoid windy conditions, a windbreak can be used to protect the welding area.
In conclusion, environmental conditions can have a significant impact on welding. By monitoring and controlling the ambient temperature, humidity, wind speed, and drafts, it is possible to ensure a successful weld.
Joint Design and Fit-Up
When it comes to welding, joint design and fit-up are critical factors that affect the quality and strength of the final weld. Proper joint design and fit-up ensure that the weld has the necessary strength and integrity to withstand the stresses and loads that it will be subjected to. Here are some of the key factors to consider when designing and fitting up weld joints:
Joint Type
The type of joint used depends on the application and the type of parts being joined. Some common types of joints include butt joints, lap joints, T-joints, and corner joints. Each type of joint requires a specific welding technique and preparation to ensure a strong and durable weld.
Joint Preparation
Preparing the joint properly is crucial for achieving a strong and durable weld. The preparation process typically involves cleaning the surfaces to be welded, removing any rust, dirt, or other contaminants that could weaken the weld. The edges of the joint must also be properly prepared, with any burrs or sharp edges removed to ensure proper penetration of the weld.
Alignment and Tack Welds
Proper alignment of the parts being welded is essential for achieving a strong and durable weld. Misaligned parts can result in weak or incomplete welds that are prone to failure. Tack welds can be used to hold the parts in place while the final weld is completed. Tack welds are small, temporary welds that are used to hold the parts in place until the final weld is completed. Care must be taken to ensure that the tack welds do not interfere with the final weld and that they are properly removed once the final weld is completed.
Joint design and fit-up are critical factors that affect the quality and strength of the final weld. Proper preparation, alignment, and tack welding are essential for achieving a strong and durable weld. By taking the time to properly design and fit-up the joint, welders can ensure that their welds are strong, durable, and able to withstand the stresses and loads that they will be subjected to.
Welding Codes and Standards
As a welder, I know that welding codes and standards play a crucial role in ensuring the quality of a weld. These codes and standards are developed by organizations such as the American Welding Society (AWS), the American Society of Mechanical Engineers (ASME), and the International Organization for Standardization (ISO).
The purpose of these codes and standards is to provide guidelines for the design, fabrication, and inspection of welded structures. They cover a wide range of topics such as welding procedures, welding qualifications, materials, and safety.
One of the most commonly used welding codes is the AWS D1.1 Structural Welding Code – Steel. This code provides guidelines for the welding of structural steel and is used extensively in the construction industry. It covers topics such as welding procedures, welder qualifications, and inspection requirements.
Another important code is the ASME Boiler and Pressure Vessel Code. This code provides guidelines for the design, fabrication, and inspection of boilers, pressure vessels, and other pressure-containing equipment. It covers topics such as material selection, welding procedures, and non-destructive testing.
It is important for welders to be familiar with these codes and standards and to follow them closely when performing welding operations. Failure to do so can result in substandard welds that may compromise the safety and integrity of the structure being welded.
Conclusion
The factors that affect welding include the welding process itself, the welding technique, and the material properties. The choice of welding process depends on factors such as the type and thickness of the material. The welding technique, including torch angle and speed, plays a crucial role in achieving the desired weld quality. Material properties, such as the type of base metal, thickness, and surface conditions, also impact the welding process. Understanding these factors is essential for selecting the appropriate welding technique and equipment for a successful weld.