Electric resistance welding is a widely used technique in the manufacturing industry to join metal components together. It involves applying an electric current to the parts to be joined, creating heat that fuses them together. This method offers many advantages, including high productivity, cost-effectiveness, and the ability to join a wide range of materials.
However, mastering the art of electric resistance welding requires a thorough understanding of the key techniques involved. This blog post will explore these techniques in detail, providing valuable insights to help you achieve high-quality results in your welding projects.
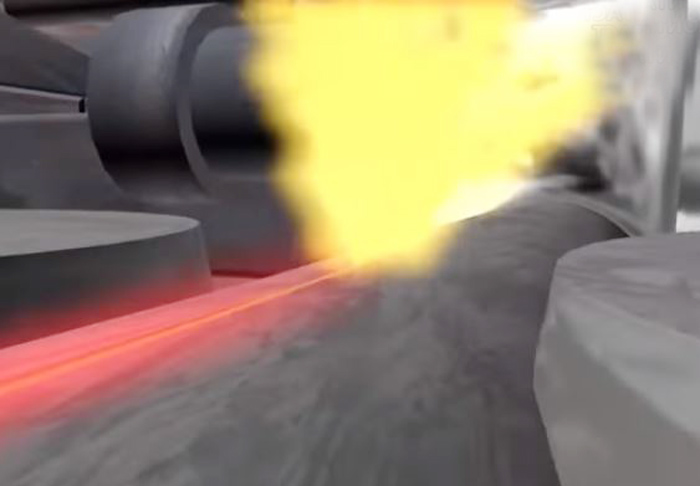
Photos by YT/tenaris
Benefits of ERW for various applications
Understanding the benefits of electric resistance welding (ERW) for various applications is crucial for achieving high-quality results in your welding projects. Electric resistance welding offers a range of advantages that make it a preferred choice across different industries.
One significant benefit of electric resistance welding is its high productivity. This welding technique allows for rapid joining of metal components, saving valuable time and increasing efficiency in manufacturing processes. Additionally, Electric resistance welding is highly cost-effective. The equipment required for electric resistance welding is relatively affordable compared to other welding methods, making it a cost-efficient option for many businesses.
Electric resistance welding is versatile and can be applied to a wide range of materials. Whether you are working with stainless steel, carbon steel, or aluminum, Electric resistance welding can effectively join different types of metals, providing strength and durability to your welded components.
In the next section, we will delve deeper into the specific benefits of electric resistance welding for various applications, exploring real-world examples and case studies that demonstrate its effectiveness. Stay tuned to learn more about how electric resistance welding can elevate your welding projects to new heights of quality and efficiency.
Techniques for achieving high-quality results in ERW
To achieve high-quality results in electric resistance welding (ERW), it is essential to master key techniques that optimize the welding process. These techniques not only ensure the strength and durability of the weld but also contribute to the overall efficiency of the project.
One crucial technique is proper joint preparation. Before beginning the welding process, it is crucial to clean and deburr the metal surfaces to be joined. This ensures that the weld area is free from contaminants and allows for better fusion between the two components.
Another important technique is controlling the heat input. Maintaining a consistent heat during the welding process is crucial to achieving a strong and uniform weld. Proper heat input controls prevent overheating or underheating, which can lead to weak and brittle welds.
Furthermore, choosing the appropriate welding parameters, such as current, voltage, and welding speed, is crucial. These parameters should be carefully selected based on the materials being welded and the desired outcome. Adjusting these parameters can help achieve the right balance between penetration, fusion, and minimal distortion.
In the upcoming section, we will discuss these techniques in detail, providing practical tips and guidelines for mastering each one. By implementing these techniques in your electric resistance welding projects, you can ensure high-quality results that meet industry standards and exceed customer expectations. Stay tuned for more valuable insights on achieving excellence in electric resistance welding.
Importance of proper equipment calibration and maintenance
Proper equipment calibration and maintenance play a significant role in achieving high-quality results in electric resistance welding (ERW). A well-calibrated and regularly maintained welding machine ensures accurate and consistent welding parameters, leading to improved weld quality.
Firstly, regular calibration of the welding equipment is essential to ensure that the current, voltage, and other settings are accurate and aligned with industry standards. Calibration ensures that the machine is delivering the intended heat input, resulting in reliable and strong welds.
In addition to calibration, routine maintenance is vital for the longevity and performance of the equipment. Regularly inspecting and cleaning the welding machine helps identify and troubleshoot potential issues before they affect the weld quality. It is crucial to pay attention to critical components such as electrode holders, contact tips, and cooling systems to maintain optimum performance.
By prioritizing proper equipment calibration and maintenance, you can minimize the risk of weld defects, reduce downtime, and increase overall productivity. In the next section, we will delve deeper into the processes and best practices for equipment calibration and maintenance in ERW. Stay tuned to discover how to maximize the lifespan and performance of your welding equipment for high-quality results.
Best practices for controlling variables in the welding process
Controlling variables in the welding process is crucial to achieving high-quality results in electric resistance welding (ERW). By understanding and implementing best practices, welders can ensure consistent weld quality and minimize the risk of defects.
One of the key variables to consider is the material being welded. Different materials have different electrical conductivity, resistance, and thermal properties, which can affect the welding parameters. It is essential to understand the material’s characteristics and adjust the welding settings accordingly to achieve optimal results.
Another important variable is the welding speed. Welding too fast can lead to insufficient heat input, resulting in weak and inadequate fusion. On the other hand, welding too slow can cause excessive heat input, leading to distortion and potential defects. Finding the right balance and maintaining a consistent welding speed is crucial for producing high-quality welds.
Electrode selection and maintenance also play a role in controlling variables. The choice of electrode material and size can impact the welding process and final weld quality. Additionally, regularly inspecting and replacing worn-out electrodes ensures consistent electrical contact and prevents potential issues.
Lastly, monitoring and controlling the environmental conditions can significantly affect the welding process. Factors like ambient temperature, humidity, and cleanliness can influence the weld’s integrity. Welding in a controlled environment, free from contamination, and maintaining stable atmospheric conditions can help achieve consistent results.
In the upcoming section, we will dive deeper into these variables and explore the best practices for controlling them in the welding process. Stay tuned to learn how to optimize your welding parameters and achieve high-quality results in ERW.
Advanced techniques for enhancing the strength and appearance of ERW welds
In the previous section, we discussed the key variables to consider in electric resistance welding (ERW) to achieve high-quality results. Now, let’s delve into advanced techniques that can further enhance the strength and appearance of your ERW welds.
One technique that can improve weld strength is preheating. Preheating the base metal before welding helps to reduce potential cracking and improve the overall integrity of the weld. The preheating temperature should be determined based on the material being welded and its thickness. It is crucial to follow industry guidelines and adhere to proper preheating practices to optimize the results.
Another technique for enhancing both strength and appearance is post-weld heat treatment. This process involves subjecting the welded part to controlled heating and cooling cycles. Post-weld heat treatment can relieve residual stresses, improve ductility, and enhance the mechanical properties of the weld. This technique is especially beneficial for welds that require high strength or are subjected to harsh operating conditions.
Using filler metals that complement the base material can significantly improve the strength and integrity of the weld. The selection of filler metal should take into consideration the compatibility with the base material, as well as the desired mechanical properties of the joint. Matching the filler metal composition to the base metal can help minimize potential weaknesses and improve the overall quality of the weld.
Lastly, proper welding techniques can enhance the appearance of ERW welds. This includes processes such as grinding, sanding, and polishing to remove any surface imperfections and create a smooth and aesthetically pleasing finish. By investing time and effort into proper weld finishing techniques, you can not only improve the appearance of the weld but also ensure that it meets the required standards for visual inspection.
By incorporating these advanced techniques into your ERW welding process, you can elevate the quality of your welds to new heights. In the next section, we will explore some common challenges faced in ERW welding and provide solutions to overcome them. Stay tuned to learn how to tackle common issues and achieve flawless results in your welding projects.
Training and certification opportunities for professionals in the field
In addition to mastering the key techniques for high-quality electric resistance welding (ERW) results, it is crucial for professionals in the field to seek training and certification opportunities. Training programs offer a comprehensive understanding of ERW principles, equipment operation, and safety protocols.
Certification validates your expertise and demonstrates your commitment to professionalism and continuous improvement. It also opens up new job opportunities and increases your earning potential. Several organizations and institutions offer ERW training and certification programs. These programs cover topics such as welding procedures, metallurgy, inspection methods, and industry standards. They provide hands-on training to develop practical skills and thorough knowledge of the ERW process.
Attending workshops, seminars, and conferences related to ERW welding is also beneficial for staying updated with the latest advancements and networking with industry experts. Investing in your professional development through training and certification is a wise career move. It not only enhances your skills but also establishes you as a trusted and competent ERW welder.
Case studies demonstrating the success of ERW in different industries
Electric resistance welding (ERW) has proven to be an effective and reliable welding technique in a variety of industries. Let’s take a closer look at some case studies that highlight its success.
In the oil and gas industry, ERW has been widely used for pipeline construction. This method ensures strong, leak-free joints, making it ideal for transporting natural gas and petroleum products over long distances. ERW pipes have also been crucial in the construction of water and sewage systems, providing a durable and cost-effective solution.
The automotive industry has also benefited from ERW technology. It has been instrumental in manufacturing exhaust systems, structural components, and fuel tanks. The precision and consistency achieved through ERW welding contribute to the overall safety and performance of vehicles.
Another industry that has embraced ERW is construction. From building structures to fabricating scaffolding, ERW welding offers high-quality and durable connections. Its efficiency and versatility make it a preferred choice for creating steel columns, beams, and trusses.
These case studies demonstrate the wide-ranging applications and benefits of ERW welding. As we delve deeper into this topic, we will explore the key techniques that contribute to achieving high-quality results in various industries. Stay tuned for valuable insights and expert tips to master the art of electric resistance welding.
Future of Electric Resistance Welding
As we conclude our exploration of electric resistance welding (ERW), it is evident that this welding technique has a promising future. Its versatility, efficiency, and ability to deliver high-quality results make it a preferred choice across various industries.
With advancements in technology, ERW is expected to continue evolving and improving. Manufacturers are continuously investing in research and development to enhance the precision and consistency of ERW welding. This will lead to even stronger and more durable connections, meeting the demanding requirements of modern applications.
As sustainability becomes a key focus in industries worldwide, ERW’s energy-efficient nature makes it a more environmentally friendly option compared to other welding methods. By minimizing heat input and material waste, ERW reduces environmental impact and contributes to a greener future.
Conclusion
Mastering the art of electric resistance welding is essential for professionals in industries such as oil and gas, automotive, and construction. By staying up-to-date with the latest techniques and advancements, welders can achieve high-quality results, ensuring the safety, durability, and efficiency of the final products. So, embrace the opportunities that ERW presents, and unlock your full potential in the world of welding.