Plastic welding is a process that involves joining two plastic materials using heat, pressure, or a combination of both. But does plastic welding work? Can it create strong, durable bonds between different plastic materials? In this article, we will explore the effectiveness of plastic welding and delve into the process and techniques involved.
Plastic welding has become a popular method for joining plastic materials due to its versatility, reliability, and cost-effectiveness. It is a highly effective way of joining plastics, creating strong and lasting bonds that can withstand tough environments and conditions.
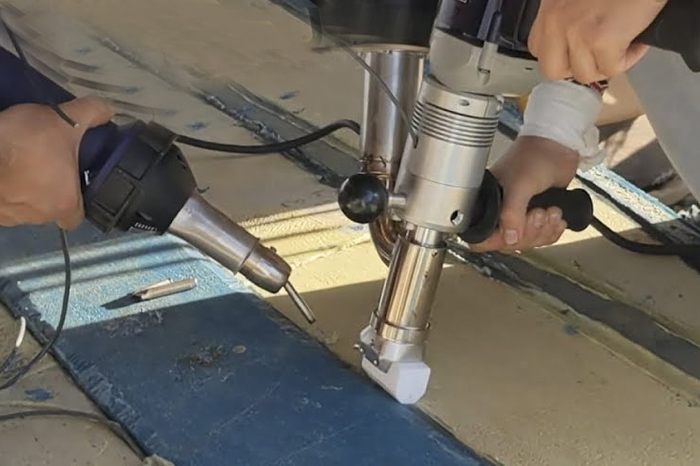
Photos by Precious_Plastic
The plastic welding process involves melting the ends of the two plastic materials to be joined, then pressing them together to create a bond. There are several techniques that can be used in plastic welding, including hot gas welding, extrusion welding, and ultrasonic welding. Each technique has its unique advantages and disadvantages, depending on the type of plastic material and the specific application.
Understanding the Plastic Welding Process
Plastic welding is an increasingly popular technique used to join plastic materials. It involves using heat, pressure, and sometimes filler material to create a bond between the plastic components. The process is versatile, cost-effective, and environmentally friendly, making it a preferred method for a wide range of applications.
Plastic Welding Applications
Plastic welding has numerous applications across different industries, including the automotive, construction, and medical sectors. Some common applications of plastic welding include:
- Repairing plastic products, such as car bumpers, water tanks, and toys.
- Manufacturing plastic products, such as pipes, packaging materials, and automotive parts.
- Joining plastic materials with other materials, such as metal or glass.
Plastic welding is an excellent alternative to traditional joining methods, such as gluing or mechanical fastening. It provides a strong, durable bond that can withstand harsh environments and extreme temperatures, making it suitable for a range of applications.
Types of Plastic Welding
There are several types of plastic welding methods, each with its own benefits and applications. Some common types of plastic welding techniques include:
Method | Description | Applications |
---|---|---|
Hot plate welding | Uses a heated platen to melt and join two plastic parts. | Large parts, such as automotive parts and electrical housings. |
Ultrasonic welding | Uses high-frequency vibrations to generate heat and join two plastic parts. | Small parts, such as electronics and medical devices. |
Hot gas welding | In Hot gas welding, uses a heated gas to melt and join two plastic parts. | Pipes, tanks, and other plastic components. |
Choosing the right plastic welding technique depends on the materials being joined, the size of the components, and the required strength of the bond. A skilled plastic welder can determine the best method for each application, ensuring a strong, durable bond.
The Benefits and Advantages of Plastic Welding
Plastic welding has numerous benefits and advantages over traditional methods of joining plastic materials. It has become a popular choice in industries such as automotive, construction, and medical due to its many strengths.
Durable and Strong Joints
One of the main benefits of plastic welding is that it creates durable and strong joints. The welding process fuses the plastic materials together, creating a bond that is often even stronger than the original material. This is particularly important in industries where strength and durability are essential.
Clean and Aesthetic Appearance
Plastic welding also provides a clean and aesthetic appearance. Unlike other methods of joining plastics, such as mechanical fastening or adhesive bonding, plastic welding does not leave visible marks or joints. This is important for industries where appearance is a top priority, such as automotive or consumer goods.
Cost-Effective
Another advantage of plastic welding is its cost-effectiveness. It can be a more affordable option than other joining methods, especially when considering the long-term durability and strength of the joint. Additionally, it requires minimal materials and produces less waste than other methods, making it an environmentally friendly choice.
Versatility
Plastic welding is also highly versatile. It can be used to join a wide variety of plastic materials, including PVC, ABS, and HDPE, among others. This makes it an ideal choice for industries that work with multiple types of plastic materials.
Time-Saving
Finally, plastic welding is a time-saving method of joining plastic materials. The welding process requires minimal preparation and can be completed quickly, reducing production time and costs.
The Process and Equipment in Plastic Welding
Plastic welding is a process used to join plastic materials together to create a strong, durable bond. The process involves melting the surfaces of the plastics to be joined and fusing them together to form a solid bond. There are several different plastic welding methods, each requiring specific equipment and techniques.
Types of Plastic Welding Methods
There are several plastic welding methods, each with its unique set of advantages and disadvantages. The most commonly used methods include:
- Ultrasonic welding: This method uses high-frequency sound waves to heat and melt the plastic materials, creating a strong bond.
- Hot gas welding: Hot gas welding is often used to join thermoplastics. It involves heating the plastic material with a gas flame and then pressing the heated ends together to create a bond.
- Hot plate welding: Hot plate welding uses a heated plate to melt the plastic material, creating a bond when the melted ends are pressed together.
- Spin welding: Spin welding involves spinning one plastic part against a stationary part while applying pressure to create heat. The heat generated melts the plastic, creating a bond.
The Necessary Equipment
The equipment required for plastic welding varies depending on the type of plastic welding method used. However, some of the most commonly used equipment include:
Equipment | Description |
---|---|
Welding gun | Used in hot gas and hot plate welding, the welding gun produces the heat required to melt the plastic materials. |
Welding table | A sturdy work surface used to hold the plastic materials during welding. |
Ultrasonic equipment | Used in ultrasonic welding, this equipment produces high-frequency sound waves that melt the plastic materials together. |
Welding fixtures | Used to hold the plastic materials in place during welding. |
“Using the right equipment for a particular plastic welding method is crucial in achieving a strong and durable bond.”
When selecting equipment for plastic welding, it is important to consider factors such as the type of plastic material to be welded, the size and shape of the materials, and the required strength of the bond.
With the right plastic welding method and equipment, it is possible to achieve a strong and durable bond between plastic materials, making plastic welding an ideal solution for a wide range of applications.
Conclusion and How Does It Plastic Welding Work?
Plastic welding is a highly effective method for joining plastic materials. The process involves heating and melting the plastic surfaces to be joined and then pressing them together until they cool and solidify. This creates a strong and durable bond that is resistant to impact and weathering.
Plastic welding has a wide range of applications, from automotive and aerospace industries to medical and consumer goods. Its advantages include its ability to join different types of plastic materials, its cost-effectiveness, and its speed and efficiency.
The process of plastic welding requires specialized equipment and tools, such as a hot air gun, a welding rod, and a welding nozzle. There are various types of plastic welding methods, including hot gas welding, hot plate welding, and ultrasonic welding.
Overall, plastic welding is a reliable and efficient method for joining plastic materials, and it is becoming increasingly popular in various industries for its numerous benefits. With the right equipment and technique, plastic welding can create strong and long-lasting bonds that can withstand even the most demanding applications.
FAQ
Does plastic welding work? How does it work?
Plastic welding is a highly effective method for joining plastic materials. It works by using heat to melt the surfaces of the plastics being joined, and then pressing them together to create a strong bond.
What are the different types of plastic welding?
There are several types of plastic welding techniques, including butt welding, ultrasonic welding, hot gas welding, and friction welding. Each method has its own advantages and is suitable for different applications.
What are the benefits of plastic welding?
Plastic welding offers numerous benefits, such as producing strong and durable joints, being a cost-effective method, enabling the joining of different types of plastics, and providing a seamless finish without the need for additional materials.
What equipment is used in plastic welding?
The equipment used in plastic welding varies depending on the method being used. Common equipment includes a welding gun, hot air blowers, ultrasonic welders, or a heated platen for hot plate welding. These tools are designed to create the necessary heat and pressure for the welding process.