Are you considering a career in non-destructive testing (NDT) but finding it difficult to choose between ultrasonic testing (UT) and radiography? Don’t worry, because in this article, we will explore the key differences between UT and radiography to help you make an informed decision.
UT and radiography are two widely used methods in NDT that are used to detect flaws and anomalies in various materials and structures. While both methods are effective in providing accurate results, they differ in terms of principle, equipment, advantages, and limitations.
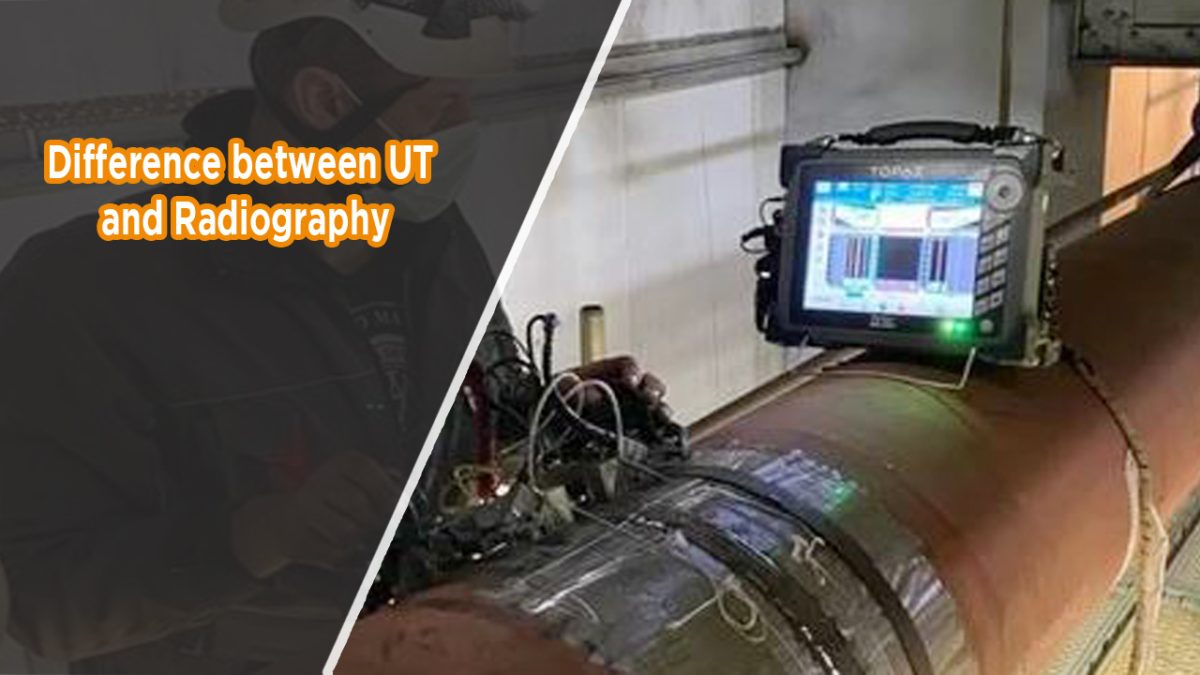
Basics of UT and Radiography
Ultrasonic testing relies on high-frequency sound waves that are transmitted through the material being tested. These sound waves reflect back when they encounter a flaw, producing a detailed image of the internal structure. On the other hand, radiography uses X-rays or gamma rays to penetrate the material, creating a radiographic image that can reveal internal defects.
Principles and techniques of UT
Ultrasonic testing works on the principle of sound waves. A transducer is used to introduce high-frequency sound waves into the material being tested. These sound waves travel through the material and are reflected back when they encounter a flaw or boundary between different materials. By analyzing the time it takes for the sound waves to return and the amplitude of the reflected waves, an inspector can determine the location, size, and type of defect present in the material.
There are several techniques used in UT, including pulse-echo, time-of-flight diffraction (TOFD), phased array, and immersion testing. Each technique has its advantages and is suitable for different applications. For example, pulse-echo is commonly used for flaw detection, while TOFD is ideal for measuring the size and position of defects.
Principles and techniques of Radiography
Radiography, on the other hand, relies on X-rays or gamma rays to penetrate the material being tested. These rays are absorbed differently by different materials and structures, creating a radiographic image that can reveal internal defects such as cracks, voids, or inclusions. The image produced by radiography is similar to an X-ray image used in medical diagnostics.
There are two main types of radiography: film radiography and digital radiography. Film radiography uses X-ray film to capture the image, which then needs to be developed. Digital radiography, on the other hand, captures the image directly in a digital format, allowing for immediate analysis and manipulation.
Applications of UT in various industries
UT is widely used in various industries for flaw detection, thickness measurement, and material characterization. In the aerospace industry, UT is used to inspect aircraft components such as wings, fuselage, and engine parts for hidden defects that could compromise the safety and performance of the aircraft. In the oil and gas industry, UT is used to inspect pipelines, storage tanks, and pressure vessels for corrosion, erosion, and cracks. UT is also used in the automotive, manufacturing, and construction industries for quality control and structural integrity assessment.
Applications of Radiography in various industries
Radiography is also extensively used in various industries for flaw detection, weld inspection, and material analysis. In the automotive industry, radiography is used to inspect welds in car bodies and engine components. In the petrochemical industry, radiography is used to inspect welds in pipelines and storage tanks to ensure their integrity. Radiography is also commonly used in the medical field for diagnostic imaging.
Advantages and limitations of UT
UT offers several advantages over radiography. Firstly, it is a non-hazardous testing method as it does not involve the use of ionizing radiation. This makes it safer for both the inspector and the environment. UT also provides real-time imaging, allowing for immediate analysis and decision-making. It is also highly portable and can be performed on-site, making it suitable for inspections in remote locations. UT has limitations in terms of the type of materials it can inspect. It is most effective in detecting flaws in materials with good acoustic properties, such as metals and composites. It may not be suitable for materials with poor acoustic properties, such as concrete or wood.
Advantages and limitations of Radiography
Radiography also has its advantages and limitations. One of the main advantages of radiography is its ability to penetrate dense materials and provide a detailed image of internal defects. It is effective in inspecting a wide range of materials, including metals, composites, and ceramics. Radiography also allows for permanent record keeping through film or digital images. Radiography involves the use of ionizing radiation, which can be hazardous if proper safety measures are not followed. It also requires a controlled environment and specialized equipment, which may not be feasible in certain situations.
Choosing between UT and Radiography: Factors to consider
When choosing between UT and radiography, there are several factors to consider. Firstly, the type of material being tested plays a crucial role. If the material has good acoustic properties and the inspection needs to be conducted on-site, UT may be the preferred method. On the other hand, if the material is dense and the inspection can be performed in a controlled environment, radiography may be more suitable.
The size and complexity of the structure being tested, as well as the required level of detail in defect detection, should also be taken into account. Cost, safety considerations, and regulatory requirements should also be considered when making a decision.
Final Thoughts
UT and radiography are both valuable methods in non-destructive testing. While UT relies on sound waves to detect flaws, radiography uses X-rays or gamma rays to penetrate the material and reveal internal defects. Both methods have their advantages and limitations, and the choice between them depends on various factors such as the type of material being tested, the inspection environment, and the required level of detail in defect detection.
By understanding the principles, applications, advantages, and limitations of both UT and radiography, you can make an informed decision and choose the right method for your specific NDT application.