Butt welding sheet metal is a fundamental welding technique that involves joining two metal sheets end-to-end. This process creates a strong and durable weld, making it an essential skill for fabricators and welders across various industries. Understanding the intricacies of butt welding is crucial for achieving seamless joints with minimal material distortion. Butt welding is widely used in industries such as automotive, aerospace, and manufacturing due to its ability to produce clean and precise joints. It is a preferred method for joining thin metal sheets, as it allows for a seamless appearance without the need for additional materials. Mastering the art of butt welding requires precision, control, and a deep understanding of the properties of the metals being joined.
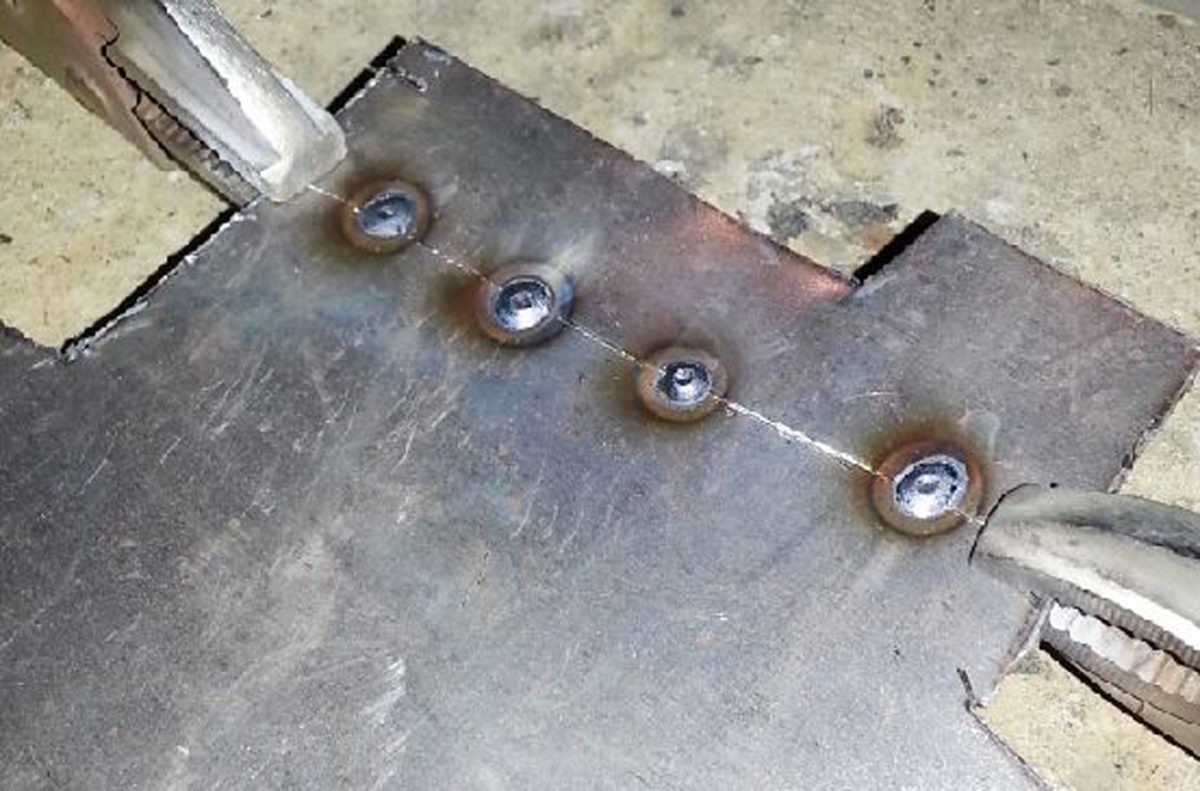
Photos by mig-welding.co.uk
The process of butt welding involves heating the adjoining surfaces of the metal sheets to the point of melting and then fusing them together. This results in a weld that is as strong as the base metal, providing a seamless and continuous joint. While it may seem straightforward, achieving a flawless butt weld requires careful preparation, the right equipment, and adherence to proper welding techniques.
Butt welding is an essential skill for anyone working with sheet metal, whether in a professional capacity or as a hobbyist. By understanding the advantages and disadvantages of this welding technique, individuals can make informed decisions about when and how to utilize butt welding in their projects. With the right knowledge and techniques, butt welding can be a valuable asset in creating high-quality, precise, and durable metal joints.
Advantages and Disadvantages of Butt Welding
Like any welding technique, butt welding sheet metal comes with its own set of advantages and disadvantages. Understanding these factors is essential for determining when butt welding is the most appropriate method for a particular project, as well as for ensuring the best possible results. One of the primary advantages of butt welding is the ability to create seamless joints with minimal material distortion. This makes it an ideal choice for applications where a clean and continuous appearance is desired, such as in the automotive and aerospace industries. Butt welding produces welds that are as strong as the base metal, ensuring the structural integrity of the joined components.
However, butt welding also has its limitations and challenges. It requires precise control and skill to achieve consistent and high-quality welds, particularly when working with thin metal sheets. Proper preparation of the metal surfaces is crucial, as any contaminants or imperfections can compromise the integrity of the weld. The heat-affected zone in butt welding can lead to distortion or warping of the metal, requiring careful consideration and planning during the welding process.
Despite these challenges, the advantages of butt welding often outweigh the disadvantages, making it a preferred method for joining sheet metal in many industrial and DIY projects. By understanding the strengths and limitations of butt welding, welders and fabricators can effectively leverage this technique to achieve superior results.
Types of Butt Welding Techniques
Several techniques can be used for butt welding sheet metal, each suited to different applications and requirements. Understanding the various types of butt welding techniques is essential for selecting the most appropriate method for a specific project and achieving the desired outcome.
One of the most common butt welding techniques is the fusion welding method, which involves melting and fusing the adjoining metal surfaces without the use of additional filler material. This technique is preferred for creating seamless joints and is often used in applications where aesthetics and strength are crucial, such as in architectural metalwork and automotive body panels.
Another technique is resistance butt welding, which utilizes electrical resistance to generate heat and join the metal sheets. This method is particularly efficient for high-volume production and is commonly used in the manufacturing industry for joining metal components with precision and speed. Friction stir welding is a solid-state welding process that involves rotating a non-consumable tool to generate frictional heat, allowing the metal sheets to be joined without melting. This technique is ideal for joining dissimilar metals and producing high-strength welds without the need for filler material.
Each butt welding technique offers unique advantages and considerations, and selecting the most suitable method depends on factors such as the type of metal being welded, the desired appearance and strength of the joint, and the specific requirements of the project. By understanding the options available, welders can make informed decisions about which butt welding technique will yield the best results for their applications.
Equipment and Tools Required for Butt Welding Sheet Metal
Executing a successful butt welding process requires the use of specific equipment and tools tailored to the characteristics of the metal being welded. From welding machines to protective gear, having the right resources at hand is essential for achieving precise and high-quality welds.
One of the primary pieces of equipment needed for butt welding is a welding machine capable of generating the necessary heat and power to fuse the metal sheets. TIG (tungsten inert gas) and MIG (metal inert gas) welding machines are commonly used for butt welding sheet metal, offering precise control and versatility in handling various types of metals and thicknesses. The selection of welding electrodes or filler rods is crucial for achieving strong and durable welds, as these materials contribute to the integrity of the joint.
In addition to welding machines and consumables, protective gear such as welding helmets, gloves, and safety glasses are essential for ensuring the welding safety of the welder during the butt welding process. Proper ventilation and fume extraction systems should also be in place to mitigate the risks associated with welding fumes and gases. Clamps, jigs, and other fixtures are often used to secure the metal sheets in the correct position and alignment, facilitating precise and consistent welds.
Understanding the specific requirements of the project and the properties of the metal being welded is crucial for selecting the appropriate equipment and tools. By having the right resources at hand, welders can execute butt welding with confidence, precision, and safety, ultimately resulting in exceptional weld quality and integrity.
Preparing Sheet Metal for Butt Welding
Effective preparation of the sheet metal surfaces is a critical step in ensuring the success of the butt welding process. Properly preparing the metal not only contributes to the quality and strength of the weld but also minimizes the risk of defects and imperfections in the joint.
The first step in preparing sheet metal for butt welding is to thoroughly clean the surfaces to be joined, removing any contaminants, oxides, or coatings that could interfere with the welding process. This can be achieved using solvent-based cleaners, wire brushes, or abrasive pads to ensure that the metal surfaces are free of any impurities that could compromise the integrity of the weld. The edges of the metal sheets should be carefully deburred to remove any sharp or uneven edges that could affect the fit-up and welding process.
After cleaning, it is essential to properly fit and align the metal sheets to ensure a tight and precise joint. This may involve using clamps, jigs, or fixtures to hold the sheets in position, as well as verifying that the edges are straight and even. Proper fit-up is crucial for achieving consistent and high-quality welds, as any misalignment or gaps between the metal sheets can lead to weak or flawed joints.
Once the metal surfaces are cleaned and properly fit-up, it is important to consider the welding process’s heat input and distortion control. Minimizing the heat-affected zone and reducing the risk of metal distortion during welding can be achieved through proper welding techniques, such as controlling the welding speed, current, and heat input. Additionally, using backing bars or supports can help manage distortion and ensure the flatness of the welded joint.
By meticulously preparing sheet metal for butt welding, fabricators and welders set the stage for achieving precise, strong, and flawless welds. Attention to detail in cleaning, fit-up, and distortion control is essential for ensuring the integrity and quality of the welded joint, ultimately leading to superior results in various industrial and DIY applications.
Butt Welding Process Step by Step
Executing a successful butt welding process requires a systematic approach that encompasses meticulous preparation, precise execution, and careful inspection. Following a step-by-step procedure ensures that each stage of the welding process is executed with precision, ultimately yielding strong and durable welds.
The first step in the butt welding process is to set up the welding equipment and prepare the work area. This includes ensuring that the welding machine is properly configured for the type and thickness of metal being welded, as well as establishing a safe and well-ventilated workspace. The metal sheets should be thoroughly cleaned, fit-up, and secured in the correct position using clamps or fixtures.
Once the preparation is complete, the welding process begins with the careful selection of welding parameters, such as current, voltage, and welding speed, based on the characteristics of the metal being welded. For TIG welding, this may involve setting the appropriate tungsten electrode type and gas flow rate, while MIG welding requires the selection of suitable welding wire and shielding gas. The precise adjustment of welding parameters is critical for achieving consistent and high-quality welds.
As the welding process commences, the welder must maintain control and precision in directing the heat and filler material to the joint, ensuring thorough fusion and proper penetration. This may involve employing techniques such as weaving or oscillating the welding torch to distribute heat evenly across the joint, as well as maintaining a steady travel speed to avoid overheating or under-penetration.
Following the completion of the weld, the joint should be allowed to cool gradually to reduce the risk of stress and distortion. Once the weld has cooled, it is essential to inspect the joint for any defects, such as cracks, porosity, or incomplete fusion. This may involve conducting non-destructive testing methods, such as visual inspection, dye penetrant testing, or ultrasonic testing, to verify the integrity and quality of the weld.
By following a systematic and meticulous approach to the butt welding process, welders can achieve precise, strong, and flawless joints that meet the highest quality standards. Each step of the process, from preparation to inspection, plays a crucial role in ensuring the integrity and durability of the welded joint, ultimately contributing to the success of various industrial and DIY projects.
Common Mistakes to Avoid in Butt Welding Sheet Metal
While butt welding sheet metal is a valuable and versatile technique, it is not without its challenges and potential pitfalls. Understanding and avoiding common mistakes in the butt welding process is essential for achieving superior weld quality, structural integrity, and overall project success.
One of the most common mistakes in butt welding is inadequate preparation of the metal surfaces. Failing to thoroughly clean and fit-up the metal sheets can result in the inclusion of contaminants, poor joint alignment, and increased risk of defects in the weld. Additionally, improper cleaning and fit-up can lead to weak or flawed joints that compromise the integrity of the welded components.
Another critical mistake to avoid is inadequate control and precision during the welding process. Inconsistent welding parameters, such as excessive heat input, improper travel speed, or insufficient fusion, can lead to defects, distortion, and reduced weld strength. Maintaining precise control and adherence to proper welding techniques are essential for achieving high-quality and durable butt welds.
Furthermore, neglecting post-weld inspection and quality assurance is a common oversight that can result in undetected defects and compromised weld integrity. Thoroughly inspecting the welded joint for any signs of defects, such as cracks, porosity, or incomplete fusion, is crucial for ensuring the reliability and safety of the weld. Employing non-destructive testing methods, such as visual inspection and ultrasonic testing, can help identify and rectify any issues before they compromise the project.
By understanding and proactively avoiding these common mistakes, welders can enhance the quality, strength, and durability of butt welded joints, ultimately contributing to the success of various industrial and DIY projects. Addressing these challenges with precision, skill, and attention to detail ensures that butt welding remains a valuable asset in creating high-quality and reliable metal joints.
Finishing and Inspecting Butt Welding Sheet Metal
Completing the butt welding process is not the final step in achieving a high-quality and reliable metal joint. Proper finishing and thorough inspection are essential for ensuring the integrity, strength, and aesthetic appearance of the welding sheet metal, ultimately contributing to the success of the project.
After the welding process is complete, any excess weld material or spatter should be carefully removed from the joint using appropriate finishing tools, such as grinders or sanders. This ensures that the weld surface is smooth, uniform, and free of any irregularities that could compromise the appearance or functionality of the joint. Additionally, any sharp edges or burrs should be carefully deburred to create a safe and visually appealing welded joint.
Following the finishing process, the welded joint should undergo thorough inspection to verify its integrity and quality. Visual inspection is the first step, involving a careful examination of the weld for any signs of defects, such as cracks, porosity, or incomplete fusion. Additionally, non-destructive testing methods, such as dye penetrant testing or ultrasonic testing, can be employed to further assess the internal integrity of the weld.
Once the joint has been inspected and any necessary corrections or repairs have been made, it is essential to consider any additional treatments or coatings that may be required to protect the welded metal from corrosion, oxidation, or other environmental factors. This may involve applying protective coatings, such as paint or sealants, to ensure the long-term durability and functionality of the welded joint.
Applications and Industries Utilizing Butt Welding Sheet Metal
Butt welded sheet metal finds widespread applications across various industries, where its strength, durability, and seamless appearance make it a preferred method for joining metal components. Understanding the diverse range of applications and industries that utilize butt welded sheet metal highlights the importance of mastering this essential welding technique.
In the automotive industry, butt welding is commonly used for joining body panels, exhaust systems, and structural components. The seamless and strong joints produced by butt welding contribute to the structural integrity, safety, and aesthetic appeal of automotive vehicles. Additionally, the aerospace industry relies on butt welded sheet metal for creating lightweight and durable components, such as aircraft fuselage panels, wings, and structural supports.
Final Thoughts
Butt welding sheet metal is an essential skill for anyone who wants to tackle DIY projects. Butt welding allows for strong, reliable welds that can last a long time when done correctly. While mastering this technique isn’t necessarily easy, taking the time to learn and practice proper techniques will pay off with stronger and better-looking welds. If you are considering tackling a sheet metal project, especially one that needs to be butt welded, do your research, practice on scrap material before attempting it on your sheet metal project, and wear the right safety equipment at all times. And if you ever need help or advice along the way, don’t hesitate to reach out to us! We’re here to help – ready and willing – so please get in touch and we look forward to helping out with your project.