When it comes to repairing a car, getting in isn’t always easy. Whether you break a headlight on a rusty classic or your battery got damaged, getting access to Ecu or any part of the vehicle is no longer just about removing panels. With the right equipment and knowledge, though, it’s easier than ever before. And when we mean easier, we mean MUCH easier.
To get that old rusty metal working again and to keep the costs down wherever possible, the DIY repair enthusiast will often find themselves asking… Is there a better alternative than replacing that rusty sheet metal with new? Are there some parts of vehicles where welding isn’t such an ideal solution? The answer to these questions is an unequivocal yes. If you have an eye for detail and have patience as well as manual dexterity, then becoming a skilled sheet metal welder can be your calling.
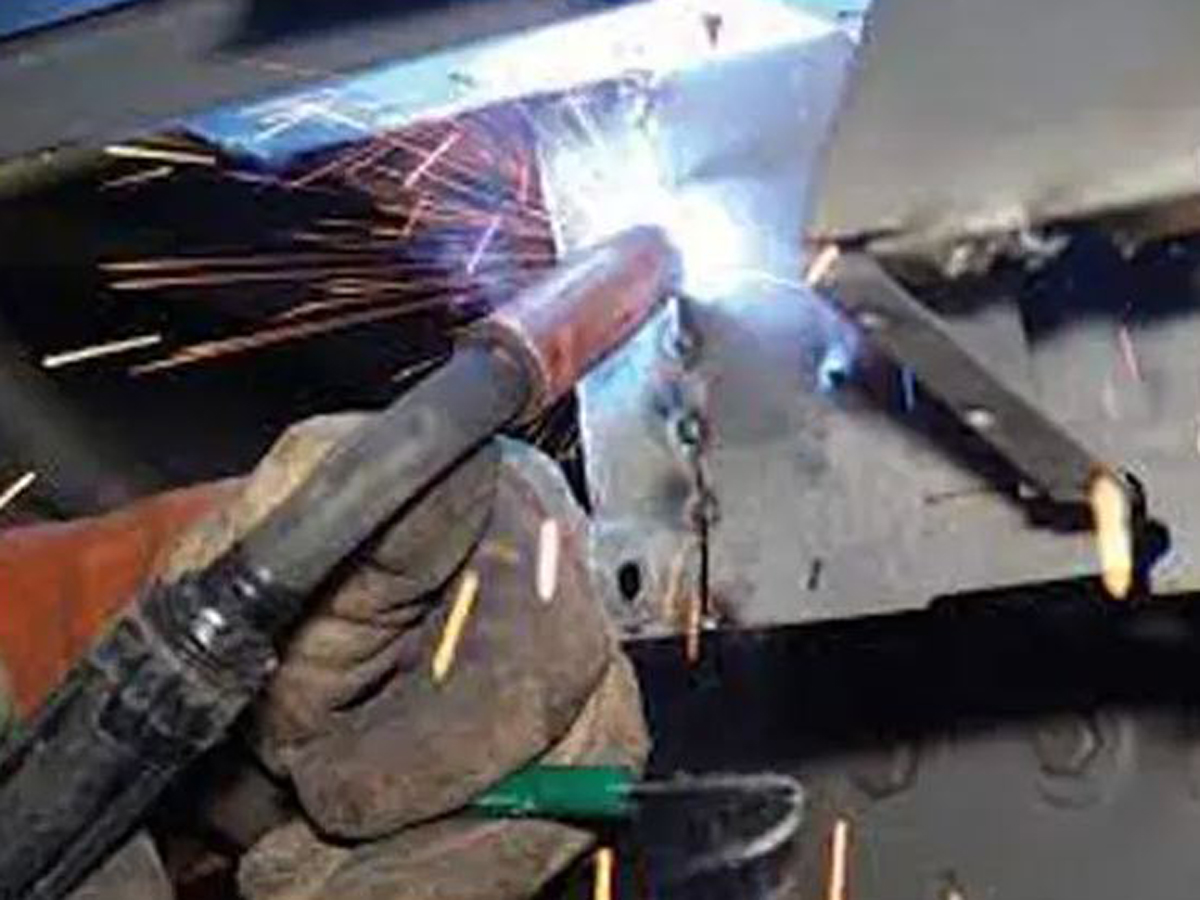
What is the Welder For Automotive Sheet Metal?
Welding is the process of joining two or more pieces of metal together by melting their outer surface, fusing it into a solid, and then drawing the metal back together. This is achieved by applying heat to the metal pieces, then applying a special welding rod that has a rod coat that contains the filler material. When the welding rod coat melts, it combines with the other metals, causing them to fuse together. Usually, the welding rod coat is made of a special alloy that contains nickel, copper, and chromium, which are the main components of stainless steel. When the rod coat melts, it combines with the other metals to create a weld between the pieces.
Why Welding Is Important For Automotive Repairs
Welding has come a long way since the days of blacksmiths. Today, it’s used in almost every industry and field, from shipbuilding to construction, auto repair and manufacturing, and more. Welding is an essential skill for almost every industry, and if you are doing automotive repair or maintenance, welding is one of the most important skills to master. Welding repairs are often the best option for a variety of reasons. It’s a quick, efficient way to join two pieces of metal.
When welding, you are actually joining two pieces of metal together, not just heating the surface and melting it. This is important because welding creates a bond between the pieces of metal, so if there’s any damage to the metal, welding will cover it up. Welding is also stronger than simple drilling and bolting because the weld itself holds the pieces of metal together.
Welder Classes and Skill Levels
Welders can be broken down into two classes, depending on their skill level, and the amount of experience they have: Class I and Class II. Class I welding is generally done by experienced welders who work on all types of metal, while Class II welding is generally reserved for work on ferrous metals and is done by less-experienced welders. In general, Class I welders are good for welding almost any type of metal. They are generally skilled welders with a high level of experience. Class I welders are also called general or specialty welders. Class II welders are only allowed to perform spot welding repairs on ferrous metals. They must also have a Class I license and experience with Class II welding.
Which Welder Is Right For You?
A welder’s skill level can be an important factor when choosing which model and welder to purchase. If you are looking to replace rusted sheet metal or damaged parts, a high-quality model with a good reputation will perform well and last a long time. If you are looking to weld smaller joints, such as attaching a fender to a hub, you may want a lower-cost model that’s easier to maneuver. For repairs that require welding longer joints, or welding on larger or thicker pieces of metal, you will want a higher-quality model with a large enough tank to last the entire repair. If you are looking for a portable welder for smaller project, a small portable welder may be best for you.
Metalworking Basics for Welding
Before you can weld, you need to know a few basic metalworking skills. Metalworking is the process of shaping and cutting metal, drilling holes in it, forming it into parts, and joining it together. It includes every step from design and blueprinting to manufacturing and assembly. To weld, you need a welder, welding rod, and welding wire. The welding rod is the main component of the welding system; it’s the source of heat and the part that melts the metal. It’s made up of an electrode and a flux. The flux is a substance that’s mixed into the electrode and creates a chemical reaction that helps the electrode reach higher temperatures, making the weld stronger and more lasting.
Finding the Right Parts for Welding Repair
The first step in finding the right parts for welding repair is to measure the damaged area. Once you have that, note the dimensions of the damaged area and the area you want to weld. Once you know the dimensions of the damaged area and the area you want to weld, you can search online for sheet metal parts that are similar to the one you’re welding. Some parts can be hard to find. If you can’t find the part you need, you may want to consider designing your own part in CAD software.
Avoid Using Spot welders for Sheet Metal Repair
A lot of repair shops will spot weld a joint, but you should always weld a joint. Spot welding is when you weld with a spot welder on a small joint, making it weaker than it would be if welded in a continuous weld. Using spot welders on large parts with large thicknesses negatively affects the welded joint. For example, spot welding a 1/2-in. plate with a 1/4-in. spot weld results in a joint that’s only half as strong as it would be if welded in a continuous weld. In addition, welding a joint on a spot welded part weakens the welded joint on a continuous welded part. If you want to repair a car but need to weld, you’re better off replacing the part.
How to Choose a Best Welder For Automotive Sheet Metal Repair?
There are a few things to look for when choosing a best welder for automotive sheet metal repairs.
What kind of welding am I doing?
For example, if you are repairing a flat tire, you are going to be welding different types of metal than if you are replacing a headlight, bumper, or other more complicated part.
Is the welder easy to use and maneuver?
A good welder should be easy to use and maneuver around the repair site. This will make it easier to weld large parts or joints.
What type of protection is included with the welder?
A good welder will have a large enough tank to weld the entire repair.
What type of welding wire is included with the welder?
A good welder will include a variety of welding wires, including a solid wire and a gas shielding wire to address any welding needs.
How to Pick a Good welder for Automotive Sheet Metal Repair?
A good welder will have great customer service, a good warranty, and a variety of welding equipment, including a variety of welding rods, wire, shielding gas, and shielding sticks. A good welder is also easy to use and maneuver. A good welder will have all of the features you need and will perform well. A good welder will be easy to use and will have an easy-to-read control panel. A good welder should have a large enough tank to weld the whole repair. A good welder should also be easy to use and maneuver.
Final Words
Welding is one of the most important and useful skills you can learn. It’s a great way to repair or replace a broken part and saves money when compared to other methods of mechanical repair or replacement such as drilling, bolting, or grinding. When welding, you’re joining two pieces of metal together, not just heating the surface and melting it. This is important because welding creates a bond between the pieces of metal,