Automotive plastic welding joins plastic components in vehicles using heat, pressure, or vibration. It ensures strong, durable bonds for various applications.
Automotive plastic welding is crucial in modern car manufacturing. It combines plastic parts like bumpers, dashboards, and fuel tanks, ensuring they remain securely attached under various conditions. This process utilizes different techniques like hot plate welding, ultrasonic welding, and vibration welding, each suited for specific materials and applications.
The choice of method depends on the type of plastic, the part’s design, and the required strength of the bond. Automotive plastic welding helps improve vehicle durability, reduce weight, and enhance aesthetic appeal. By ensuring precision and reliability, this technique plays a vital role in the production of high-quality, safe vehicles.
Introduction To Automotive Plastic Welding
Automotive plastic welding is a critical process in the manufacturing of vehicles. It involves the joining of plastic components using heat, pressure, and various welding techniques. This method ensures that plastic parts are securely bonded, enhancing the vehicle’s durability and performance. Understanding its history and significance can provide insights into its importance in modern manufacturing.
History And Evolution
The history of automotive plastic welding dates back to the mid-20th century. Initially, plastic welding was primitive and used mainly in small applications. Over the decades, technological advancements have revolutionized this process. Early methods relied on simple tools and manual labor. Modern techniques now employ sophisticated machinery and automation.
In the 1980s, the automotive industry began to see the potential of plastic welding. This was due to the increasing use of plastic parts in vehicle manufacturing. The need for lightweight, durable, and cost-effective materials drove innovation. Today, automotive plastic welding is a highly specialized field, with numerous techniques tailored to specific applications.
Significance In Modern Manufacturing
Plastic welding is pivotal in today’s automotive manufacturing landscape. It plays a crucial role in ensuring the structural integrity and safety of vehicles. The use of plastic components has grown significantly, making welding essential for assembly.
One of the primary benefits of automotive plastic welding is weight reduction. Lighter vehicles are more fuel-efficient and environmentally friendly. Plastic welding also allows for more intricate and complex designs. This flexibility enables manufacturers to innovate and create more advanced vehicle models.
Below is a table highlighting the key advantages of plastic welding in automotive manufacturing:
Advantages | Description |
---|---|
Weight Reduction | Contributes to fuel efficiency and lower emissions. |
Cost-Effective | Reduces production costs through efficient processes. |
Design Flexibility | Allows for complex and innovative vehicle designs. |
Durability | Ensures strong and long-lasting components. |
Automotive plastic welding is vital for the production of modern vehicles. Its significance cannot be overstated in the context of manufacturing efficiency and product quality.
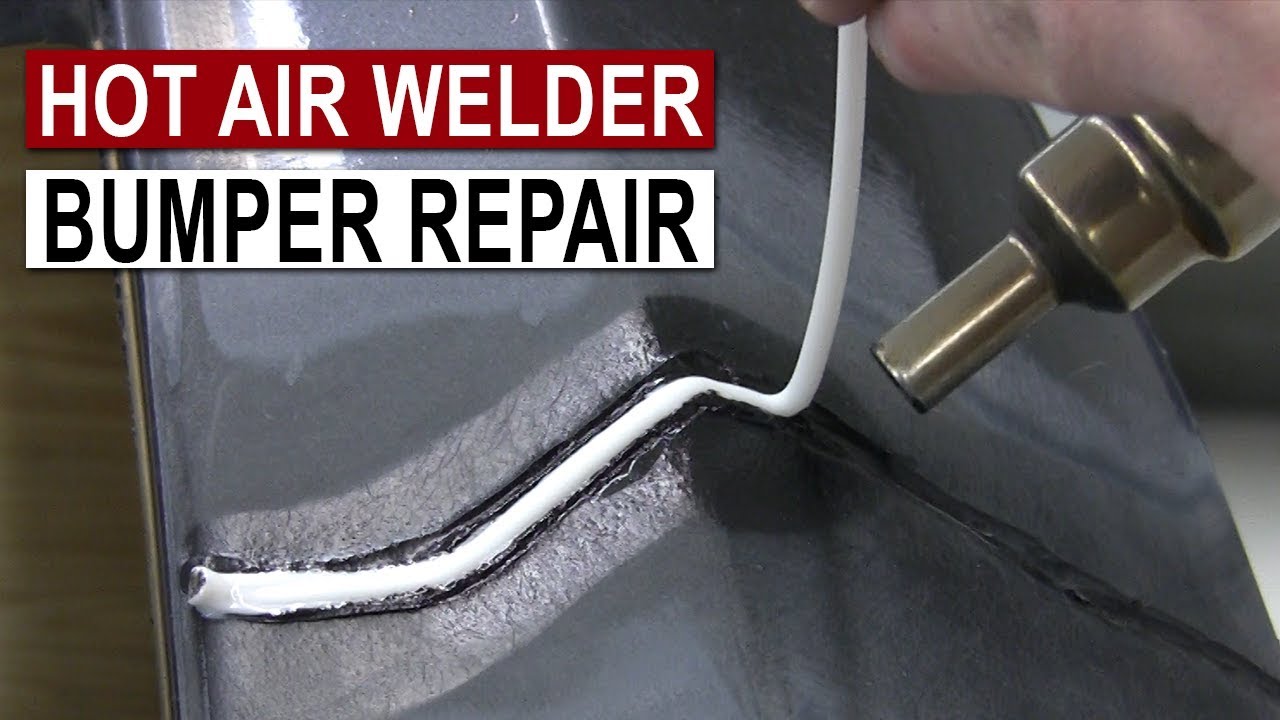
Credit: m.youtube.com
Types Of Plastic Welding Techniques
Automotive plastic welding is crucial in manufacturing. Different techniques ensure strong and durable bonds. Here, we explore various types of plastic welding methods.
Ultrasonic Welding
Ultrasonic welding uses high-frequency sound waves. This method joins plastic components quickly.
A horn transfers ultrasonic energy to the parts. The parts vibrate and generate heat. This heat melts the plastic, creating a bond.
This method is fast and efficient. It is ideal for high-volume production.
Hot Plate Welding
Hot plate welding involves a heated plate. The plate melts the surfaces of the parts to be joined.
The parts are pressed against the plate. Then, they are pressed together to form a bond. This method works for large or complex parts.
Advantages | Disadvantages |
---|---|
Strong bond | Slow cycle time |
Handles large parts | Risk of plate contamination |
Laser Welding
Laser welding uses a laser beam. The beam precisely melts the plastic at the joint.
This method is very accurate. It allows for clean and strong bonds.
- Minimal part deformation
- Suitable for intricate designs
- High initial setup cost
Materials Used In Plastic Welding
Plastic welding has revolutionized the automotive industry. It is essential to understand the materials used. This knowledge ensures strong and durable bonds. Different plastics and specialty polymers are used in this process.
Common Plastics
Automotive plastic welding often uses common plastics. These plastics are easy to weld and widely available. Here are some examples:
- Polypropylene (PP) – Known for its toughness and flexibility.
- Polyethylene (PE) – Commonly used for fuel tanks and containers.
- Polyvinyl Chloride (PVC) – Used in interior trim and cables.
- Acrylonitrile Butadiene Styrene (ABS) – Ideal for dashboards and panels.
Specialty Polymers
Some applications need specialty polymers. These materials offer unique properties. They are used in high-performance parts:
- Polyether Ether Ketone (PEEK) – Resistant to chemicals and heat.
- Polyphenylene Sulfide (PPS) – Known for its strength and stability.
- Polycarbonate (PC) – Provides impact resistance and clarity.
- Polyamide (PA) – Commonly known as Nylon, used for gears and bearings.
Understanding these materials is crucial. It ensures proper welding techniques. This leads to durable and reliable automotive parts. The right material makes all the difference.
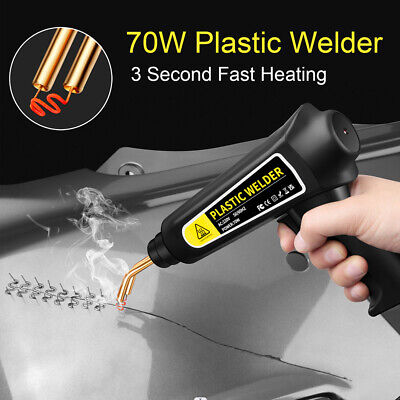
Credit: www.ebay.com
Advantages Of Plastic Welding In Automotive Industry
Automotive plastic welding has transformed vehicle manufacturing. It offers numerous benefits. This blog post highlights the key advantages of plastic welding in the automotive industry.
Cost-effectiveness
Plastic welding is a cost-effective solution. It reduces the need for metal parts. This leads to significant cost savings. Lightweight plastic parts lower production costs.
Additionally, plastic welding cuts down on material waste. This results in more efficient use of resources. The process is quick and requires minimal labor. This reduces overall production costs.
Enhanced Durability
Plastic welding ensures enhanced durability of components. Welded plastic parts exhibit high strength. They can withstand extreme conditions. This includes heat, pressure, and vibrations.
Moreover, plastic welding creates a seamless bond. This bond is resistant to leaks and cracks. It ensures long-lasting performance. Vehicles enjoy a longer lifespan.
Advantages | Description |
---|---|
Cost-Effectiveness | Reduces material waste and labor costs |
Enhanced Durability | Creates strong, leak-resistant bonds |
Challenges And Solutions
Automotive plastic welding is essential in modern vehicle manufacturing. This process ensures strong, lightweight, and durable plastic components. Despite its benefits, it poses several challenges. Below are the common challenges and solutions in automotive plastic welding.
Technical Difficulties
One primary challenge is achieving consistent weld quality. Uneven heat distribution can weaken joints. Using precise temperature controls and advanced welding equipment solves this issue.
Another problem is material compatibility. Different plastics have varying melting points. Selecting compatible materials or using specialized adhesives can help.
Complex geometries also create hurdles. Intricate designs need precise welding techniques. Robotic welders and 3D printing technology can address these challenges.
Environmental Concerns
Plastic welding can produce harmful fumes. These emissions are dangerous to workers and the environment. Installing proper ventilation systems and using eco-friendly materials can mitigate this risk.
Another concern is plastic waste. Disposing of scrap materials is challenging. Implementing recycling programs and using biodegradable plastics can reduce waste.
Energy consumption is also significant. Welding processes can be energy-intensive. Adopting energy-efficient machines and renewable energy sources can lower the environmental footprint.
Below is a summary table of the challenges and solutions:
Challenge | Solution |
---|---|
Inconsistent weld quality | Precise temperature controls, advanced equipment |
Material compatibility | Select compatible materials, use specialized adhesives |
Complex geometries | Robotic welders, 3D printing technology |
Harmful fumes | Proper ventilation, eco-friendly materials |
Plastic waste | Recycling programs, biodegradable plastics |
Energy consumption | Energy-efficient machines, renewable energy sources |

Credit: www.amazon.com
Applications In Car Manufacturing
Automotive plastic welding has revolutionized car manufacturing. It ensures strong, lightweight, and durable components. This technology is used to join various plastic parts seamlessly. Let’s explore its applications in car manufacturing.
Interior Components
Plastic welding in car interiors enhances both aesthetics and functionality. It is used for:
- Dashboard assemblies: Ensures a smooth, seamless look.
- Instrument panels: Provides durable and precise fitment.
- Door panels: Offers a perfect blend of design and strength.
- Console components: Guarantees integration of multiple parts.
Plastic welding secures these parts firmly. It eliminates the need for screws or adhesives. This results in a cleaner and more polished finish.
Exterior Parts
The exterior of a car benefits greatly from plastic welding. Key applications include:
- Bumpers: Ensures impact resistance and seamless design.
- Grilles: Provides structural integrity and aesthetic appeal.
- Fenders: Offers lightweight and durable protection.
- Mirror housings: Ensures precision and durability.
Using plastic welding, manufacturers create durable and aerodynamic parts. This process helps reduce vehicle weight. Lightweight cars are more fuel-efficient and perform better.
Component | Benefit |
---|---|
Dashboard | Seamless appearance |
Bumper | Impact resistance |
Fender | Durability |
Mirror Housing | Precision |
Plastic welding is essential in modern car manufacturing. It ensures strong, lightweight, and durable components. This technology continues to advance, offering even more applications in the automotive industry.
Innovations And Future Trends
Automotive plastic welding has seen rapid advancements in recent years. Innovations and future trends are shaping the industry. These developments enhance efficiency, sustainability, and precision. Let’s explore the latest trends in this exciting field.
Advanced Techniques
Advanced techniques in plastic welding are transforming automotive manufacturing. These methods provide stronger and more reliable welds. Here are some notable techniques:
- Laser Welding: This technique offers high precision and speed. It creates clean and strong welds.
- Ultrasonic Welding: This method uses high-frequency sound waves. It is ideal for small, intricate parts.
- Hot Plate Welding: This technique is perfect for larger parts. It ensures uniform welding across surfaces.
Sustainability Initiatives
Sustainability is a key focus in automotive plastic welding. Manufacturers are adopting eco-friendly practices to reduce waste and energy consumption. Some initiatives include:
- Recycled Plastics: Using recycled materials in welding processes. This reduces the demand for new plastic.
- Energy-Efficient Equipment: Modern machines consume less energy. They are designed to be more efficient.
- Waste Reduction: Implementing strategies to minimize waste during welding. This includes better material management and recycling.
Technique | Benefit |
---|---|
Laser Welding | High precision, speed, clean welds |
Ultrasonic Welding | Ideal for small parts, high-frequency sound waves |
Hot Plate Welding | Uniform welding, suitable for larger parts |
These innovations and trends are driving the automotive plastic welding industry forward. They promise a future of efficient and sustainable manufacturing practices.
Case Studies
Automotive plastic welding has revolutionized manufacturing processes. Case studies provide insights into real-world applications. Let’s explore how leading automotive manufacturers have implemented these techniques successfully.
Leading Automotive Manufacturers
Many leading automotive manufacturers have adopted plastic welding. Here’s a look at a few:
- BMW: Known for precision and quality, BMW uses plastic welding in their assembly lines. Their use of ultrasonic welding ensures strong bonds in lightweight parts.
- Toyota: Toyota integrates plastic welding for fuel efficiency. Laser welding helps in reducing vehicle weight.
- Ford: Ford employs vibration welding in their production. This helps in achieving durable and reliable parts.
Successful Implementations
Successful implementations of plastic welding have led to significant advancements. Here are a few examples:
Manufacturer | Technique | Outcome |
---|---|---|
General Motors | Hot Plate Welding | Improved fuel tank integrity |
Honda | Spin Welding | Enhanced air intake systems |
Mercedes-Benz | Infrared Welding | Superior headlamp assemblies |
These implementations showcase the versatility and effectiveness of plastic welding. Automotive manufacturers continue to innovate, ensuring safer and more efficient vehicles.
Frequently Asked Questions
What Is Automotive Plastic Welding?
Automotive plastic welding is a process that joins plastic parts in vehicles. It ensures strong, durable connections. Various techniques like ultrasonic, hot plate, and vibration welding are used.
Why Is Plastic Welding Important In Cars?
Plastic welding is crucial for vehicle manufacturing. It provides strong, lightweight, and durable components. This enhances vehicle performance and fuel efficiency.
What Are The Types Of Plastic Welding?
There are several types of plastic welding. Common methods include ultrasonic, hot plate, and vibration welding. Each method has unique applications.
How Does Ultrasonic Plastic Welding Work?
Ultrasonic welding uses high-frequency sound waves. These waves create friction, generating heat to bond plastic parts. It’s fast, efficient, and precise.
Conclusion
Automotive plastic welding offers a cost-effective, durable solution for modern vehicle manufacturing. It enhances strength and reduces weight, leading to better performance. Embracing this technology ensures efficient production and superior quality. Stay ahead in the automotive industry by adopting advanced plastic welding techniques.