Are you new to welding and feeling overwhelmed by all the different types of welding processes available? Two popular options that you’ve probably heard about are arc welding and stick welding. But what’s the difference between these two techniques? In this article, we’ll break it down for you and help you understand the pros and cons of each method.
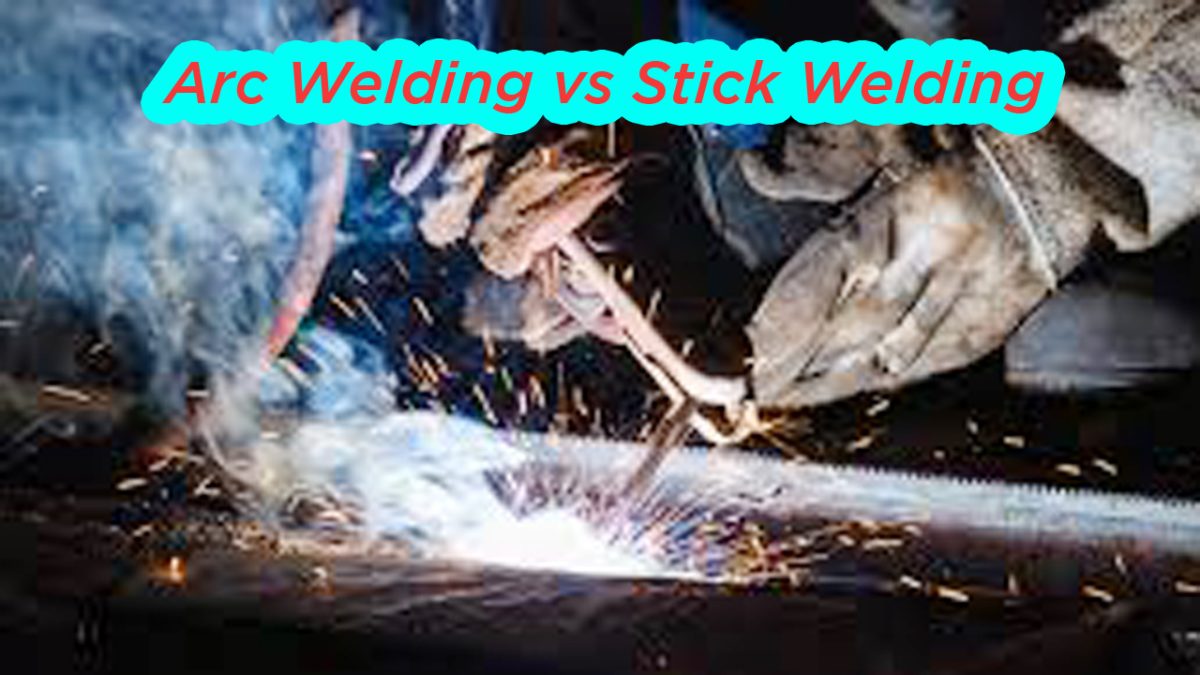
Image by tws.edu
Understanding the Arc Welding
Arc welding, also known as shielded metal arc welding (SMAW), involves using an electric arc to melt and fuse metals together. It requires an electrode and a power source to generate the necessary heat. The electrode, typically made of metal, acts as both the heat source and the filler material. As the electrode melts, it forms a weld puddle that fuses the metal pieces together.
Arc welding is a versatile welding process that can be used on a variety of metals, including steel, stainless steel, cast iron, and aluminum. It is commonly used in industries such as construction, automotive, and manufacturing. One of the main advantages of arc welding is its portability. The equipment required for arc welding is relatively small and lightweight, making it easy to transport to different job sites.
Another advantage of arc welding is its ability to produce high-quality welds. The electric arc generated during the process provides excellent control over the heat input, resulting in strong and precise welds. Additionally, arc welding is suitable for both indoor and outdoor applications, as it is not affected by wind or drafts.
However, arc welding does have some drawbacks. It requires a certain level of skill and experience to achieve optimal results. The welder needs to maintain a constant arc length and control the welding speed to avoid defects such as porosity, cracks, or incomplete fusion. Additionally, arc welding produces a significant amount of heat and sparks, which can be a safety hazard if proper precautions are not taken.
Understanding the Stick Welding
Stick welding is a specific type of arc welding that utilizes a consumable electrode covered in flux. This flux coating shields the weld puddle from atmospheric contamination, resulting in a more stable and high-quality weld. Stick welding is also commonly referred to as shielded metal arc welding (SMAW), manual metal arc welding (MMAW), or simply “stick” welding.
Stick welding is widely used in industries such as construction, shipbuilding, pipeline construction, and repair work. It is particularly suitable for welding thick materials and performing repairs in the field. The equipment for stick welding is relatively simple and affordable, making it accessible to a wide range of welders.
One of the main advantages of stick welding is its versatility. It can be used on various metals, including carbon steel, stainless steel, cast iron, and even non-ferrous metals like copper and nickel. Stick welding is also known for its ability to handle dirty or rusty surfaces, as the flux coating helps to remove contaminants and produce a clean weld.
Stick welding also offers excellent penetration, making it ideal for welding thick materials or joining dissimilar metals. The process can be performed in all positions, including flat, horizontal, vertical, and overhead. This flexibility makes stick welding a popular choice for welding in challenging or hard-to-reach areas.
However, stick welding does have its limitations. It is generally slower compared to other welding processes, as the welder needs to frequently stop and change electrodes. This can result in lower productivity, especially when working on large projects. Stick welding also tends to produce more spatter and slag, which require additional cleaning and post-welding work.
Differences between Arc Welding vs Stick Welding
Now that we have a basic understanding of arc welding vs stick welding, let’s explore the differences between these two techniques. While both methods fall under the umbrella of arc welding, they vary in several aspects, including the welding equipment used, the welding process itself, and the types of materials they can handle.
The main difference lies in the type of electrode used. In arc welding, the electrode can be either consumable or non-consumable, depending on the specific process. On the other hand, stick welding exclusively uses a consumable electrode, which is consumed during the welding process. The flux coating on the stick electrode acts as a shielding gas, protecting the weld from atmospheric contamination.
Another difference is the level of skill and experience required. Arc welding, particularly with non-consumable electrodes, demands a higher level of skill and precision. The welder needs to control the arc length, welding speed, and manipulation techniques to produce high-quality welds. Stick welding, while still requiring skill, is often considered more forgiving and easier to learn, making it a popular choice for beginners.
Additionally, arc welding is generally faster compared to stick welding, as it allows for continuous welding without the need for frequent electrode changes. Stick welding, on the other hand, requires the welder to periodically stop and replace the consumable electrode, resulting in slower overall welding speed.
Pros and Cons of Arc Welding
Arc welding offers several advantages that make it a preferred choice for many welders. One of the main benefits is its versatility. Arc welding can be used on a wide range of metals, including steel, stainless steel, cast iron, and aluminum. This versatility makes it suitable for various applications, from small repairs to large-scale construction projects.
Another advantage of arc welding is its portability. The equipment required for arc welding is relatively small and lightweight, making it easy to transport to different job sites. This portability allows welders to work in remote locations or areas with limited access.
Arc welding also offers excellent control over the heat input, resulting in high-quality welds. The electric arc provides precise control over the melting and fusion of metals, ensuring strong and durable welds. Additionally, arc welding is not affected by wind or drafts, making it suitable for both indoor and outdoor applications.
Arc welding does have some drawbacks. It requires a certain level of skill and experience to achieve optimal results. The welder needs to maintain a constant arc length and control the welding speed to avoid defects such as porosity, cracks, or incomplete fusion. Arc welding produces a significant amount of heat and sparks, which can be a safety hazard if proper precautions are not taken.
Pros and Cons of Stick Welding
Stick welding offers its own set of advantages and disadvantages. One of the main benefits of stick welding is its versatility. It can be used on various metals, including carbon steel, stainless steel, cast iron, and even non-ferrous metals like copper and nickel. Stick welding is also known for its ability to handle dirty or rusty surfaces, as the flux coating helps to remove contaminants and produce a clean weld.
Stick welding also offers excellent penetration, making it ideal for welding thick materials or joining dissimilar metals. The process can be performed in all positions, including flat, horizontal, vertical, and overhead. This flexibility makes stick welding a popular choice for welding in challenging or hard-to-reach areas.
However, stick welding does have its limitations. It is generally slower compared to other welding processes, as the welder needs to frequently stop and change electrodes. This can result in lower productivity, especially when working on large projects. Stick welding also tends to produce more spatter and slag, which require additional cleaning and post-welding work.
Choosing Between Arc Welding vs Stick Welding
When it comes to choosing between arc welding and stick welding, several factors need to be considered. The type of project, the materials being welded, and the welder’s skill level all play a role in determining the most suitable welding process.
Arc welding is generally preferred for applications that require high-quality welds, such as structural welding, pipe welding, or precision work. It is also suitable for welding thinner materials or materials that require precise control over the heat input. Arc welding may not be the best choice for beginners or for projects that require high productivity.
Stick welding, on the other hand, is often chosen for its versatility and ease of use. It is suitable for a wide range of applications, from small repairs to heavy-duty welding. Stick welding is particularly advantageous for welding thick materials, performing repairs in the field, or working in challenging environments. It is also a good option for beginners who are just starting to learn welding.
Ultimately, the choice between arc welding vs stick welding depends on the specific requirements of the project and the welder’s skills and preferences. It is always recommended to consult with a professional or experienced welder to determine the best welding process for your needs.
Best Practices for Arc Welding
To achieve optimal results with arc welding, it is important to follow some best practices. Here are a few tips to help you get started:
Safety first: Always wear the appropriate safety gear, including a welding helmet, gloves, and protective clothing. Ensure that you are working in a well-ventilated area to avoid inhaling harmful fumes.
Prepare the materials: Clean the surfaces to be welded, removing rust, paint, or dirt. Proper cleaning ensures better weld quality and reduces the risk of defects.
Choose the right electrode: Select the appropriate electrode based on the type of metal being welded and the welding process. Different electrodes have different properties and are designed for specific applications.
Set the correct welding parameters: Adjust the welding current, voltage, and travel speed according to the type and thickness of the material. Proper parameters ensure good penetration and fusion.
Maintain a steady arc length: Keep a consistent distance between the electrode and the workpiece. This helps to control the heat input and prevent defects such as porosity or incomplete fusion.
Practice proper welding techniques: Master the various welding techniques, such as weaving, circular motion, or straight line, depending on the joint configuration and position. Practice is key to improving your welding skills.
Best Practices for Stick Welding
Stick welding, being a specific type of arc welding, also has its own set of best practices. Here are some tips to help you achieve better results with stick welding:
Safety first: Always wear the appropriate safety gear, including a welding helmet, gloves, and protective clothing. Ensure that you are working in a well-ventilated area to avoid inhaling harmful fumes.
Prepare the materials: Clean the surfaces to be welded, removing any rust, paint, or dirt. Proper cleaning ensures better weld quality and reduces the risk of defects.
Choose the right electrode: Select the appropriate stick electrode based on the type of metal being welded and the welding process. Different electrodes have different properties and are designed for specific applications.
Set the correct welding parameters: Adjust the welding current, voltage, and travel speed according to the type and thickness of the material. Proper parameters ensure good penetration and fusion.
Maintain a steady arc length: Keep a consistent distance between the electrode and the workpiece. This helps to control the heat input and prevent defects such as porosity or incomplete fusion.
Manage the slag: Remove the slag from the weld bead after each pass using a chipping hammer or wire brush. This helps to ensure a clean weld and reduces the risk of slag inclusions.
Develop a rhythm: Stick welding requires a rhythmical motion to achieve consistent welds. Practice maintaining a steady travel speed and electrode angle to improve your welding technique.
Conclusion
Arc welding and stick welding are two popular techniques used in various industries to join metal pieces together. While both methods fall under the umbrella of arc welding, they differ in terms of the welding equipment used, the welding process itself, and the types of materials they can handle.
Arc welding, also known as shielded metal arc welding (SMAW), utilizes an electric arc to melt and fuse metals together. It offers versatility, portability, and precise control over the heat input. Stick welding, on the other hand, is a specific type of arc welding that uses a consumable electrode covered in flux. It offers versatility, excellent penetration, and the ability to handle dirty or rusty surfaces.
When choosing between arc welding and stick welding, factors such as project requirements, material types, and skill level should be considered. It is always recommended to consult with a professional or experienced welder to determine the best welding process for your needs.
By following best practices and mastering the necessary techniques, you can achieve high-quality welds using either arc welding or stick welding. So, whether you’re a beginner or an experienced welder, embrace the world of welding and explore the possibilities of arc welding vs stick welding.