You are probably already aware that welding aluminum is a little bit different than welding other steel materials, you may not have considered just how different it can be. This is especially true when it comes to welding aluminum without gas. Let’s take a look at some of the ways that welding aluminum without gas can make your job more challenging and less reliable. Keep reading to find out why this topic is so important, as well as how you can avoid these issues.
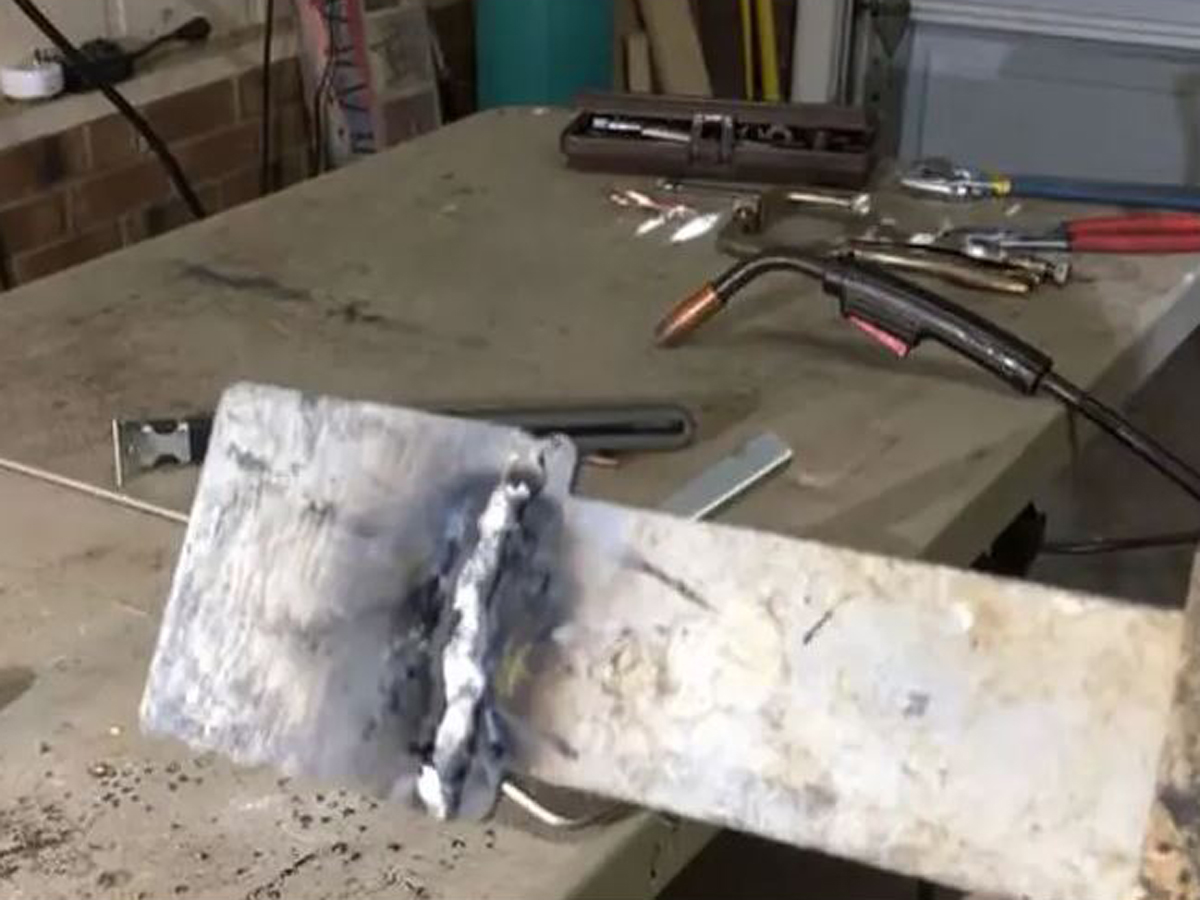
Photo by StairwayToVideo
What You Need to Know About Welding Aluminum Without Gas?
Aluminum is an extremely strong material that is also lightweight. This makes it an excellent choice for a lot of applications, such as aircraft, cars, boats, and even sports equipment. Aluminum is an extremely versatile material. Welding it requires a different approach when compared to welding steel. As such, welding aluminum without gas can actually be quite difficult. While you can do it, it does require a few precautions so that you don’t end up with poor welds or an unsafe job. The first thing you need to know about welding aluminum without gas is that it’s not a good idea. Aluminum is a strong material, and it’s also fairly stable at high temperatures.
Welding aluminum at high temperatures can cause it to change properties. For example, it can become weaker and more susceptible to fracture. This is something that you don’t want to happen. When welding aluminum without gas, you are also working at much higher temperatures. High temperatures can cause aluminum to expand and contract rapidly, which can cause it to crack and break apart. When welding aluminum, you don’t want either of these things to happen because they can lead to an unsafe job and serious issues for the equipment.
You Need a Few Key Things Tackled Prior to Welding
Now that you know the basics about welding aluminum without gas, it’s time to take a look at some of the things that you need to tackle prior to welding aluminum. When welding aluminum, you are going to work at higher temperatures than welding steel. This means that you need to make sure that your equipment can handle this increased wear and tear. Aluminum welders need to have thicker shafts, larger wheels, and more durability than their steel counterparts.
In addition to the necessary welding power, you need a welding torch that can handle the high temperature requirements of welding aluminum without gas. Carbon dioxide and argon torches are great for welding aluminum. You will also need to make sure that your torch doesn’t overheat when welding. This can happen if the torch isn’t capable of handling the high temperatures of welding aluminum.
How to Safely Weld Aluminum Without Gas
Aluminum welding requires a very different approach than welding steel. This is especially true when you are welding aluminum without any kind of gas or shielding gas. To avoid issues, you will want to follow these guidelines when welding aluminum. Welding Aluminum Without Gas Is a Challenge When it comes to welding aluminum, you will find that the challenges are similar to those that welding other non-ferrous materials presents. However, there are a few key differences that make welding aluminum even more challenging.
- Aluminum has a much higher melting point than steel, which can make it much more difficult to reach welding parameters. The added difficulty that welding aluminum without gas presents also means that you need to make sure that your equipment is suited for the job. Aluminum has a very high melting point, which means that you are going to have to work at much higher temperatures. It’s best to work in a well-ventilated area and with a shield or smoke machine that helps keep the area relatively clean.
- Aluminum is less dense than steel. As such, it can expand and contract more rapidly when you weld. You’ll want to make sure that your equipment is made to handle these changes, and it’s also a good idea to make sure that you work at slower speeds. With less dense materials, you need to work at slower speeds to make sure that you avoid material expansion or contraction.
Tubing Welding Without Gas
Tubing welding is one of the most common aluminum welding projects. This is especially true for projects where you need to weld a straight line of aluminum tubing in a consistent fashion. As such, you will want to make sure that you have a few things ready prior to welding tubing in aluminum. Make sure that your materials are ready for the job. When welding aluminum, you will want to work at much higher temperatures than you would when welding steel. You need a welding torch for handle these high temperatures, as well as a wheel that can survive the wear and tear of these temperatures.
Consistent, straight welds are a difficult task to manage, which means that you will want to make sure that you have prepared your materials well. You can do this by making sure that you have the aluminum tubing sized properly, as well as the weld joints clean and ready for welding.
MIG Welding Without Gas
MIG welding aluminum is one of the most common types of welding for aluminum projects. In fact, it’s often the only welding that you need to do. MIG welding aluminum is a great way to work with aluminum because it allows you to weld in a narrow range of feed rates and welding parameters. Welding aluminum with MIG is one of the most common aluminum welding projects. It’s common because it’s a very versatile welding technique that works with a wide range of welding parameters and welding materials.
If you are planning to weld aluminum in the future, you need to be sure that you know how to weld aluminum with an MIG welder. MIG welding aluminum is also an excellent way to test and troubleshoot your equipment prior to welding. You can use an MIG welder for practice runs and for testing equipment before actually welding.
Tig Welding Without Gas
If you want a welding method that is completely different than welding with an MIG or gas, you can consider tungsten electrode welding. With an electrode welder, you are welding with a tungsten rod instead of an arc. This is different than gas welding. You can weld with a tungsten electrode welder when you need to weld a wide range of materials, including aluminum. However, you can also use a tig welder to weld aluminum if you don’t have access to gas welding. There are a few things that you need to keep in mind when welding aluminum with a tungsten electrode.
- You can only use a flux-cored tungsten electrode with aluminum.
- You need to make sure that the electrode is properly balanced.
- You also need to make sure that you have the right tip on your tungsten electrode welder.
Stick Welding Without Gas
For projects where you don’t need to weld a straight line of aluminum tubing or weld a consistent or standard size of tubing, you can consider stick welding. When stick welding, you are welding with a stick-style welding stick instead of a Lincoln or MIG welder. You can also use stick welding for a wide range of welding projects, including welding aluminum. Stick welding aluminum is a very difficult welding project. The welding process for stick welding is different than most other types of welding.
In order to weld aluminum, you need to use a different technique. You can weld aluminum with a stick welder if you don’t have access to a welding machine with a Lincoln or MIG function.
Should You Ever Weld Aluminum Without Gas?
For projects where you only need to weld a small amount of aluminum, you can consider welding it without any kind of gas. Aluminum is an excellent choice for this type of small welding project. It’s lightweight, strong, and easy to weld. Aluminum also has a high melting point, which means that you can weld it with a stick welder. For projects where welding aluminum without gas is the only welding that you need to do, it’s a good idea to consider this type of welding. For projects where the aluminum is only a small portion of the overall project, welding it without gas can be a good option.
Final Thoughts
Welding aluminum without gas can be a cost-effective and efficient method for small-scale projects. It requires a certain level of skill and experience to master this technique. It is important to choose the right type of welding machine, filler rod, and welding technique to ensure a strong and clean weld. While gasless aluminum welding may not be suitable for larger projects or industrial applications, it can be a viable option for DIY enthusiasts or small business owners looking to save money on welding expenses. With proper preparation, practice, and safety precautions, welding aluminum without gas can produce high quality and reliable results.