Sanitary welding stainless steel ensures hygienic and corrosion-resistant joints, crucial for food, pharmaceutical, and dairy industries. This process prevents contamination and maintains high cleanliness standards.
Sanitary welding stainless steel is a specialized technique designed to create clean, smooth, and durable welds. The method is essential for industries where cleanliness and hygiene are paramount, such as food processing, pharmaceuticals, and dairy. By ensuring welds are free from crevices and contaminants, this type of welding helps prevent bacterial growth and product contamination.
Proper sanitary welding requires skilled professionals and adherence to stringent standards to achieve the desired quality and safety. Investing in high-quality sanitary welding practices can enhance product safety, extend equipment lifespan, and comply with industry regulations.

Credit: m.youtube.com
Introduction To Sanitary Welding
Sanitary welding is crucial in industries where cleanliness is paramount. This technique ensures the integrity and hygiene of welded joints. Sanitary welding of stainless steel is common due to its corrosion resistance and durability. Here, we dive into the importance of hygiene and the various applications in different industries.
Importance Of Hygiene
Hygiene is vital in industries like food processing and pharmaceuticals. Contaminants can lead to severe health issues. Sanitary welding helps maintain sterile conditions. This process ensures that joints are smooth and free of crevices. Crevices can harbor bacteria and other harmful microorganisms. The use of stainless steel further enhances hygiene due to its non-porous nature.
- Prevents contamination
- Ensures smooth welds
- Minimizes bacterial growth
Sanitary welding is essential for maintaining health standards. It plays a crucial role in preventing contamination and ensuring product safety.
Applications In Various Industries
Sanitary welding is used in many industries. Each industry has unique requirements for cleanliness and durability. Here are some key applications:
Industry | Application |
---|---|
Food and Beverage | Piping systems, storage tanks, processing equipment |
Pharmaceutical | Bioreactors, cleanrooms, pharmaceutical equipment |
Biotechnology | Fermentation equipment, filtration systems, containment vessels |
Healthcare | Medical devices, surgical instruments, hospital equipment |
Each application demands precision and strict hygiene standards. Sanitary welding ensures that products meet these demands. This method is vital for industries focused on health and safety.
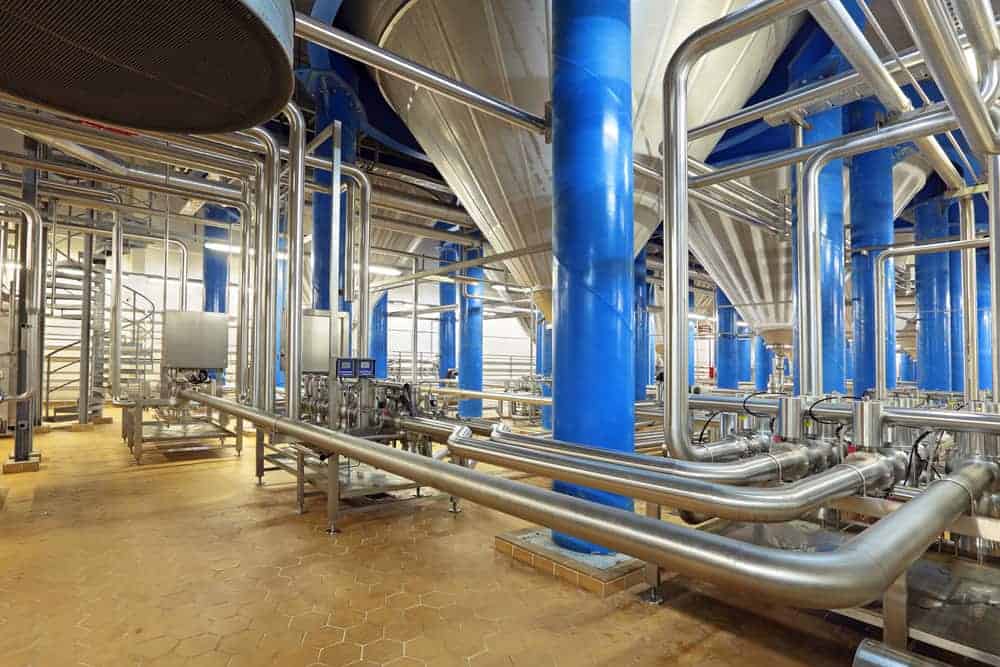
Credit: resources.arcmachines.com
Stainless Steel In Sanitary Welding
Stainless steel is essential in sanitary welding. It ensures cleanliness and durability. This material is widely used in industries like food and healthcare. Its unique properties make it a top choice. Let’s explore the benefits and types of stainless steel used in sanitary welding.
Benefits Of Stainless Steel
- Corrosion Resistance: Stainless steel resists rust and corrosion. This ensures longevity and safety.
- Easy to Clean: Its smooth surface makes cleaning easy. This prevents bacterial growth.
- High Strength: Stainless steel is strong and durable. It can withstand high pressure and temperature.
- Non-reactive: It does not react with food or chemicals. This keeps the product safe and pure.
- Aesthetic Appeal: Stainless steel has a shiny, modern look. It adds a professional touch to equipment.
Types Of Stainless Steel Used
Different types of stainless steel are used in sanitary welding. Each type has unique properties.
Type | Properties | Applications |
---|---|---|
304 Stainless Steel | High corrosion resistance, easy to form | Food processing equipment, kitchen sinks |
316 Stainless Steel | Better resistance to chemicals, heat resistant | Pharmaceutical equipment, marine applications |
430 Stainless Steel | Cost-effective, good corrosion resistance | Automotive trim, appliances |
Each type serves specific needs in sanitary welding. Choosing the right one ensures the best results.
Preparation For Welding
Preparation is key to successful sanitary welding of stainless steel. This process ensures strong, clean, and safe welds. Proper preparation can prevent contamination and ensure high-quality welds.
Surface Cleaning
Surface cleaning is the first step in preparing for welding. Clean surfaces ensure a strong weld and prevent contamination. Use a stainless steel wire brush to clean the surfaces.
Follow these steps for surface cleaning:
- Remove any visible dirt and grease.
- Use a clean cloth to wipe the surface.
- Brush the surface with a stainless steel wire brush.
- Wipe again to remove any remaining particles.
Material Selection
Choosing the right material is crucial. Different grades of stainless steel have different properties. Select the grade based on the welding project requirements.
Grade | Properties | Application |
---|---|---|
304 | Corrosion resistance, weldability | Food processing, kitchen equipment |
316 | Higher corrosion resistance | Medical devices, marine environments |
430 | Heat resistance | Automotive trim, appliances |
Ensure to match the filler material with the base material. This ensures a strong and uniform weld.
Welding Techniques
Sanitary welding of stainless steel requires precision and expertise. Different techniques ensure clean and durable welds. The two most prominent methods are TIG welding and orbital welding.
Tig Welding
TIG welding stands for Tungsten Inert Gas welding. It is also known as GTAW (Gas Tungsten Arc Welding). This method uses a non-consumable tungsten electrode. The electrode produces the weld.
The process involves using an inert gas like argon to protect the weld area. This gas shields the weld from contaminants in the air. TIG welding is ideal for thin sections of stainless steel. It produces clean and precise welds.
Orbital Welding
Orbital welding is a specialized form of welding. It involves a mechanized system. The welding head rotates around the workpiece in a precise orbit.
This technique ensures consistent and repeatable welds. It is perfect for sanitary welding applications. The process is highly automated. It reduces human error.
Orbital welding is widely used in industries where hygiene is crucial. Examples include the food and beverage industry and pharmaceutical manufacturing.
Ensuring Cleanliness
Ensuring cleanliness in sanitary welding of stainless steel is critical. This ensures the safety and hygiene of the final product. Cleanliness prevents contamination and ensures the longevity of the steel.
Post-weld Cleaning
Post-weld cleaning is the first step to ensure cleanliness. This process removes any contaminants that may have been introduced during welding. Using the right cleaning methods is vital.
Method | Description |
---|---|
Mechanical Cleaning | Uses brushes or grinding tools to remove contaminants. |
Chemical Cleaning | Involves using acid solutions to clean the welds. |
Passivation Processes
Passivation is essential for stainless steel. It forms a protective layer on the steel’s surface. This layer resists corrosion and increases the durability of the steel.
The passivation process involves treating the steel with acid solutions. This removes free iron from the surface. It also helps to build a chromium oxide layer.
- Enhances corrosion resistance
- Improves product longevity
- Ensures hygienic surfaces
Inspection And Testing
The quality of sanitary welding stainless steel is crucial. Inspection and testing ensure the strength and cleanliness of welds. They prevent contamination and ensure safety in food, pharmaceutical, and other industries.
Visual Inspection
Visual inspection is the first step in assessing weld quality. Experts look for defects such as cracks, porosity, and undercuts. They use magnifying glasses and portable microscopes to check the welds.
- Check for uniform bead shape.
- Ensure there are no visible cracks or porosity.
- Inspect for weld bead smoothness.
Non-destructive Testing
Non-destructive testing (NDT) methods are essential for evaluating weld quality without damaging the material. These methods include:
- Ultrasonic Testing (UT): Uses high-frequency sound waves to detect internal flaws.
- Radiographic Testing (RT): Uses X-rays or gamma rays to create images of the weld’s interior.
- Dye Penetrant Testing (DPT): Applies a dye to the surface to reveal cracks and pores.
- Magnetic Particle Testing (MPT): Uses magnetic fields to detect surface and near-surface flaws.
Below is a table summarizing NDT methods:
Method | Technique | Applications |
---|---|---|
Ultrasonic Testing | Sound waves | Detects internal flaws |
Radiographic Testing | X-rays/Gamma rays | Creates internal images |
Dye Penetrant Testing | Surface dye | Reveals cracks and pores |
Magnetic Particle Testing | Magnetic fields | Detects surface flaws |
Common Challenges
Sanitary welding of stainless steel comes with unique challenges. These obstacles can affect the quality and longevity of the weld. Let’s explore some common challenges welders face.
Contamination Risks
Contamination is a significant risk in sanitary welding. Even tiny particles can compromise the weld.
- Dust and dirt can stick to the weld area.
- Grease and oil from tools can transfer to the metal.
- Fingerprints can introduce unwanted elements.
To avoid contamination, welders must follow strict cleanliness protocols. Use clean gloves and tools. Wipe the metal surface before welding.
Heat-affected Zones
Heat-affected zones (HAZ) are areas near the weld that change due to heat. These zones can become weak spots if not handled correctly.
The main issues in HAZ include:
- Cracking: Intense heat can cause the metal to crack.
- Oxidation: Heat can lead to unwanted oxidation, changing the metal’s properties.
- Distortion: The metal can warp due to uneven heating.
To manage HAZ, control the heat input during welding. Use proper techniques to ensure even heat distribution.
Issue | Cause | Solution |
---|---|---|
Cracking | Excessive heat | Control heat input |
Oxidation | High temperatures | Use inert gas shielding |
Distortion | Uneven heating | Use proper welding techniques |
Pay close attention to these common challenges in sanitary welding. This will help ensure high-quality and long-lasting welds.
Advancements In Sanitary Welding
Sanitary welding stainless steel has seen significant advancements. These changes ensure cleaner, safer, and more efficient welds. The latest technologies have revolutionized the industry.
Automation In Welding
Automation has transformed sanitary welding. Robots now perform precision welds. This ensures consistent quality and reduces human error.
- Robots can work 24/7.
- They produce uniform welds.
- Automation reduces labor costs.
Using automated systems, companies can achieve high production rates. This technology boosts efficiency and ensures product safety.
Innovative Cleaning Techniques
New cleaning techniques have emerged in sanitary welding. These methods ensure that welds remain free from contaminants. Clean welds are crucial for industries like food and pharmaceuticals.
- Electropolishing: This method smoothens and cleans weld surfaces.
- Ultrasonic Cleaning: Uses sound waves to remove residues.
- Passivation: Enhances the corrosion resistance of stainless steel.
These techniques help maintain the integrity and hygiene of welded joints. They ensure that products meet stringent industry standards.
Future Trends
The world of sanitary welding stainless steel is evolving rapidly. Emerging technologies and practices promise exciting advancements. Let’s explore the future trends in this dynamic field.
Sustainability In Welding
Sustainability is becoming a core focus in welding practices. Welders aim to reduce waste and energy consumption. Adopting eco-friendly materials and methods is on the rise.
Here are some sustainable welding practices:
- Using recyclable materials
- Implementing energy-efficient welding processes
- Reducing emissions through advanced techniques
Energy-efficient welding methods are gaining popularity. They help in minimizing the carbon footprint. Welders and manufacturers are adopting these methods globally.
Enhanced Material Performance
Material performance is critical in sanitary welding. New materials are being developed. These materials offer superior durability and hygiene.
Here are some advancements in material performance:
Material | Advancements |
---|---|
Stainless Steel | Higher resistance to corrosion |
Composite Materials | Improved strength and flexibility |
Using advanced materials ensures longer-lasting welds. This reduces the need for frequent repairs. It also enhances the overall efficiency of the welding process.

Credit: www.fourmilewelding.com
Frequently Asked Questions
What Is Sanitary Welding?
Sanitary welding ensures clean, contaminant-free joints in stainless steel. It is crucial for industries like food, dairy, and pharmaceuticals.
Why Use Stainless Steel In Sanitary Welding?
Stainless steel is corrosion-resistant and easy to clean. It maintains hygiene standards, making it ideal for sanitary welding.
How To Achieve Sanitary Welding?
Use proper techniques and equipment. Ensure welds are smooth, free of cracks, and thoroughly cleaned to prevent contamination.
What Industries Need Sanitary Welding?
Industries like food processing, pharmaceuticals, and dairy rely on sanitary welding. It ensures equipment remains clean and safe.
Conclusion
Sanitary welding stainless steel ensures durability and hygiene in critical industries. Proper techniques and materials prevent contamination. High-quality welds enhance safety and longevity. Investing in skilled welders and quality stainless steel is essential. Achieve reliable, sanitary results with attention to detail and professional expertise.
Prioritize sanitary welding for a cleaner, safer environment.