Types of pipe welding include TIG, MIG, Stick, and Flux-Cored Arc Welding. Each method has unique advantages for specific applications.
Pipe welding is essential in various industries, including construction, oil and gas, and manufacturing. Different techniques offer unique benefits depending on the project’s requirements and materials used. TIG welding, known for precision, is ideal for thin materials. MIG welding, efficient and fast, suits thicker materials and extensive projects.
Stick welding is versatile and effective in outdoor conditions. Flux-Cored Arc Welding combines the benefits of MIG and Stick, excelling in high-speed and structural applications. Understanding these methods helps in selecting the right technique for your welding needs, ensuring strong, reliable, and durable pipe joints.
Introduction To Pipe Welding
Pipe welding is a crucial skill in many industries. It involves joining pipes to create a continuous system. These systems are essential for transporting liquids, gases, and other materials. Pipe welding ensures the integrity and safety of these systems.
Importance Of Pipe Welding
Pipe welding is vital for infrastructure development. It is used in construction, manufacturing, and energy sectors. Proper pipe welding prevents leaks and maintains system efficiency. It supports the safety of workers and the environment.
In the oil and gas industry, pipe welding is indispensable. It ensures pipelines are strong and durable. In the construction industry, it supports the creation of robust plumbing and heating systems.
Basic Concepts
Understanding the basic concepts of pipe welding is essential. The process involves various techniques and equipment. Here are some key concepts:
- Welding Types: Different methods are used, such as MIG, TIG, and Stick welding.
- Materials: Pipes are made from metals like steel, aluminum, and copper.
- Safety: Proper safety measures are crucial to prevent accidents.
- Equipment: Welders use torches, electrodes, and protective gear.
Welding Type | Best For | Advantages |
---|---|---|
MIG Welding | Thin metals | Easy to learn |
TIG Welding | Precision work | High-quality welds |
Stick Welding | Thicker metals | Versatile and durable |
Shielded Metal Arc Welding (smaw)
Shielded Metal Arc Welding (SMAW), also known as stick welding, is a popular method for pipe welding. This process uses a consumable electrode coated in flux to create the weld. It is a versatile and straightforward technique, suitable for various applications.
Process Overview
SMAW involves striking an arc between the electrode and the metal workpiece. The heat melts the electrode, creating a molten weld pool. The flux coating produces a gas shield, protecting the weld from contamination. As the weld cools, the flux forms a slag layer, which must be chipped away.
- Striking an arc to generate heat.
- Melting the electrode and workpiece.
- Creating a molten weld pool.
- Flux coating produces a protective gas shield.
- Formation of slag layer on cooling.
Advantages And Disadvantages
Advantages | Disadvantages |
---|---|
|
|
Gas Tungsten Arc Welding (gtaw)
Gas Tungsten Arc Welding (GTAW), also known as TIG welding, is a precise welding process. It uses a non-consumable tungsten electrode to produce the weld. The process is known for creating high-quality welds on a variety of metals.
Process Overview
The GTAW process involves several key steps. First, a welder starts the arc between the tungsten electrode and the workpiece. The arc is very stable and creates a weld pool. The welder then feeds a filler material into the pool manually. This method allows for precise control over the weld.
A shielding gas, usually argon or helium, protects the weld area from contamination. The welder must maintain a clean and stable arc. This ensures high-quality welds with minimal defects.
Applications In Industry
GTAW is widely used across various industries. It is particularly favored in the aerospace industry. This is due to its ability to produce high-strength, defect-free welds.
In the automotive industry, GTAW is used for welding critical components. This includes exhaust systems and chassis parts. The process is also popular in the construction of chemical plants and pipelines. This is because it can handle a wide range of materials, including stainless steel and aluminum.
Industry | Common Applications |
---|---|
Aerospace | High-strength structures, engine components |
Automotive | Exhaust systems, chassis parts |
Chemical Plants | Pipe welding, tank construction |
Benefits of GTAW include:
- High-quality welds
- Precise control
- Works with various metals
Challenges include:
- Requires skilled welders
- Slower process compared to other methods
Gas Metal Arc Welding (gmaw)
Gas Metal Arc Welding (GMAW) is a popular welding method used in various industries. It is also known as MIG (Metal Inert Gas) welding. This technique uses a continuous wire feed as an electrode. It creates a strong weld by melting the metal pieces together.
Key Features
GMAW has several key features that make it a preferred choice:
- High Welding Speed: GMAW offers fast welding speeds, increasing productivity.
- Ease of Use: It is easier to learn compared to other welding methods.
- Versatility: Suitable for welding various metals like steel, aluminum, and copper.
- Clean Process: Produces less spatter, resulting in cleaner welds.
- Continuous Welding: The continuous wire feed allows for long, uninterrupted welds.
Common Uses
GMAW is widely used across many industries due to its versatility:
Industry | Application |
---|---|
Automotive | Manufacturing car bodies and frames |
Construction | Building structures and frameworks |
Aerospace | Fabricating aircraft components |
Shipbuilding | Constructing ship hulls and decks |
Home Repairs | Fixing and creating metal objects |
GMAW’s high welding speed and ease of use make it ideal for mass production. It’s also great for repair work due to its versatility and clean process.
Flux-cored Arc Welding (fcaw)
Flux-Cored Arc Welding (FCAW) is a popular method in pipe welding. It uses a special tubular wire filled with flux. This technique combines the benefits of stick welding and MIG welding.
How It Works
FCAW uses a continuously fed consumable electrode. The electrode contains a flux core. This flux core generates shielding gas and slag. The shielding gas protects the weld pool from contaminants. The slag covers and protects the cooling weld. FCAW can be used with or without additional shielding gas.
Benefits And Drawbacks
Benefits:
- High deposition rate: FCAW allows for fast welding.
- Versatility: Suitable for various positions and materials.
- Reduced pre-cleaning: Handles dirty or rusty materials well.
- Portability: Excellent for fieldwork due to self-shielding option.
Drawbacks:
- Slag removal: Requires additional time to remove slag.
- Smoke and fumes: Produces more smoke compared to other methods.
- Equipment cost: FCAW equipment can be expensive.
- Learning curve: Requires skill to handle and control.
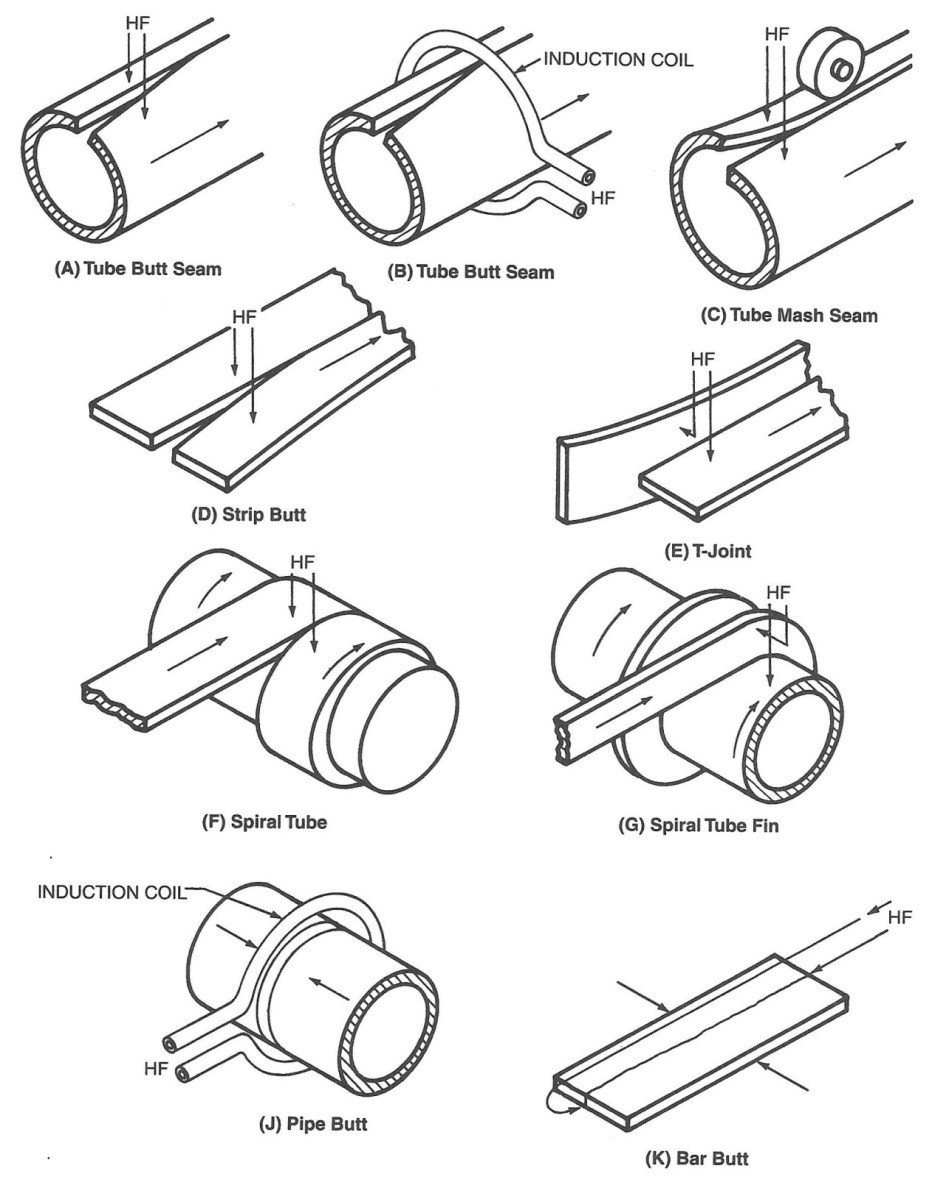
Credit: ahssinsights.org
Submerged Arc Welding (saw)
Submerged Arc Welding (SAW) is a widely used welding process known for its high efficiency. This automatic or semi-automatic welding technique involves the use of a continuously fed consumable electrode and a blanket of granular fusible flux. The flux completely covers the molten weld and the arc zone, preventing spatter and sparks, and ensuring high-quality welds.
Detailed Process
During the Submerged Arc Welding (SAW) process, the electrode is continuously fed through the welding gun. The granular flux creates a blanket over the arc and the weld pool. This blanket shields the arc from atmospheric contamination.
The flux also helps to stabilize the arc and improve weld quality. It melts to form a slag that covers the weld, protecting it from oxidation and other atmospheric contaminants. The slag is removed once the weld cools, leaving a clean, smooth weld bead.
Here is a step-by-step breakdown of the SAW process:
- Prepare the welding area and clean the materials.
- Set up the welding machine and load the electrode.
- Apply the granular flux over the weld area.
- Start the welding process, feeding the electrode continuously.
- The flux melts and forms a protective slag over the weld.
- Allow the weld to cool and remove the slag.
Industrial Applications
Submerged Arc Welding (SAW) is commonly used in industries requiring high-quality, high-strength welds. It is ideal for welding thick materials and is often used in the following applications:
- Shipbuilding – For constructing large ships and vessels.
- Pressure Vessels – For fabricating large storage tanks and boilers.
- Pipelines – For welding long sections of pipelines efficiently.
- Structural Steel – For constructing bridges and large steel structures.
The efficiency and quality of SAW make it a preferred choice in these industries. Its ability to produce deep penetration welds ensures strong, durable joints.
Below is a table summarizing the key advantages of SAW:
Advantage | Description |
---|---|
High Efficiency | Continuous feed and high deposition rates. |
High Quality | Minimal spatter and clean welds. |
Deep Penetration | Strong and durable welds. |
Safety | Reduced exposure to UV radiation and fumes. |
SAW is a reliable welding method with numerous industrial applications. Its benefits make it an essential process in modern manufacturing and construction.
Oxy-acetylene Welding
Oxy-Acetylene Welding, also known as gas welding, is a versatile welding technique. This method uses a mix of oxygen and acetylene gases to produce a flame hot enough to melt metals. It’s widely used for welding thin sheets of metal, repairing metal parts, and cutting metal.
Equipment Needed
For Oxy-Acetylene Welding, specific equipment is necessary:
- Oxygen and Acetylene Cylinders: Store the gases under high pressure.
- Regulators: Control the gas flow from the cylinders.
- Hoses: Transport gases to the torch.
- Welding Torch: Mixes gases and produces the flame.
- Nozzles: Various sizes for different flame types.
- Welding Rods: Fill the weld joint.
Safety Precautions
Safety is crucial in Oxy-Acetylene Welding. Follow these safety tips:
- Wear Safety Gear: Use gloves, goggles, and flame-resistant clothing.
- Check Equipment: Inspect hoses, regulators, and cylinders regularly.
- Work in Ventilated Areas: Ensure proper ventilation to avoid gas buildup.
- Store Cylinders Properly: Keep oxygen and acetylene cylinders upright and secure.
- Avoid Flames: Keep flammable materials away from the welding area.
Following these precautions helps ensure a safe welding experience.
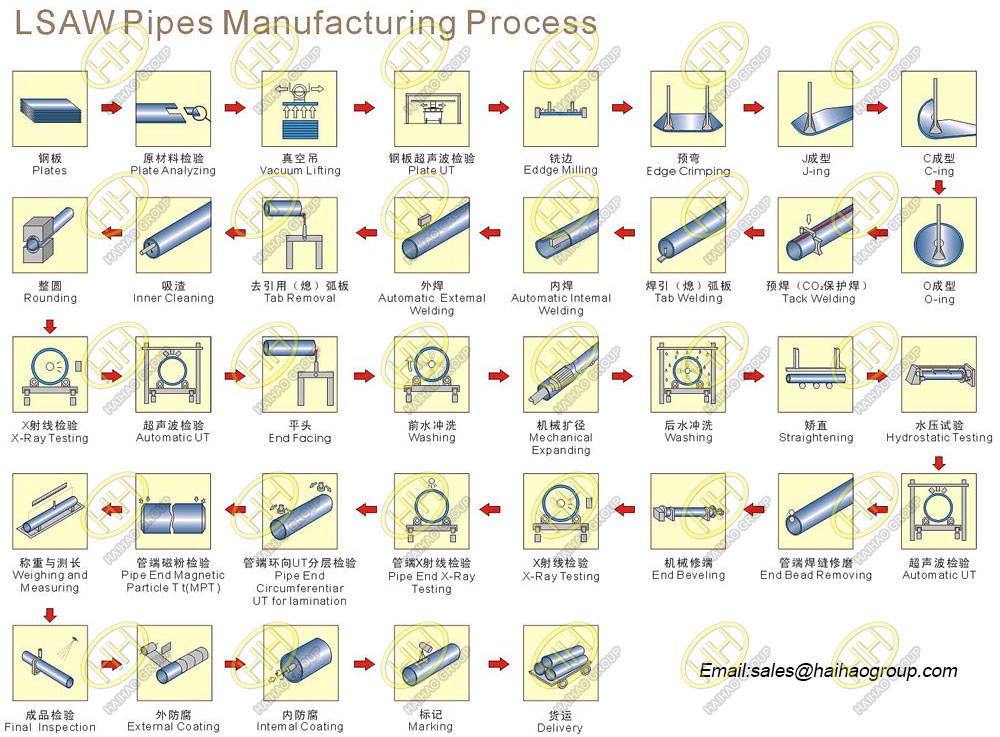
Credit: www.haihaopiping.com
Choosing The Right Welding Technique
Choosing the right welding technique is essential for the success of any pipe welding project. Various techniques are available, each with its own benefits and challenges. Understanding these techniques helps in making informed decisions for specific projects.
Factors To Consider
Several factors influence the choice of welding technique:
- Material Type: Different materials require different welding methods.
- Thickness: The thickness of the pipe affects the welding process.
- Position: The position of the pipe can impact the technique used.
- Environment: Environmental conditions may limit some welding techniques.
Matching Technique To Project
Matching the welding technique to the project needs careful consideration.
Technique | Best For | Challenges |
---|---|---|
MIG Welding | Thin materials, indoor projects | Not suitable for outdoor use |
TIG Welding | High precision, non-ferrous metals | Slower process, requires skill |
Stick Welding | Outdoor projects, thicker materials | More splatter, less precision |
Each technique offers unique benefits. Choose the right one based on your project needs.
Tips For Mastering Pipe Welding
Mastering pipe welding requires a combination of technical skills, practice, and attention to detail. Whether you are a beginner or an experienced welder, there are always areas to improve. In this section, you will find valuable tips to enhance your pipe welding proficiency. Focus on improving your skills and avoiding common mistakes to achieve better results.
Improving Skills
Improving your pipe welding skills is essential for quality work. Here are a few tips to help you:
- Practice regularly: Consistent practice helps refine your techniques.
- Understand the materials: Different materials require different approaches.
- Use the right equipment: Ensure your tools are in good condition.
- Study welding positions: Learn and practice different welding positions.
- Seek feedback: Get advice from experienced welders.
Welding Position | Description |
---|---|
1G | Flat position welding |
2G | Horizontal position welding |
5G | Vertical position welding |
6G | Inclined position welding |
Common Mistakes To Avoid
Avoiding common mistakes can significantly improve your welding outcomes. Here are some pitfalls to watch out for:
- Poor preparation: Always clean and prepare the pipes before welding.
- Incorrect settings: Adjust your welding machine settings properly.
- Wrong electrode angle: Maintain the correct electrode angle for uniform welds.
- Inadequate ventilation: Ensure proper ventilation to avoid harmful fumes.
- Skipping safety gear: Always wear appropriate safety gear during welding.
Mastering pipe welding involves continuous learning and practicing. By focusing on improving your skills and avoiding common mistakes, you can achieve high-quality welds. Remember, the key to success in welding is dedication and attention to detail.
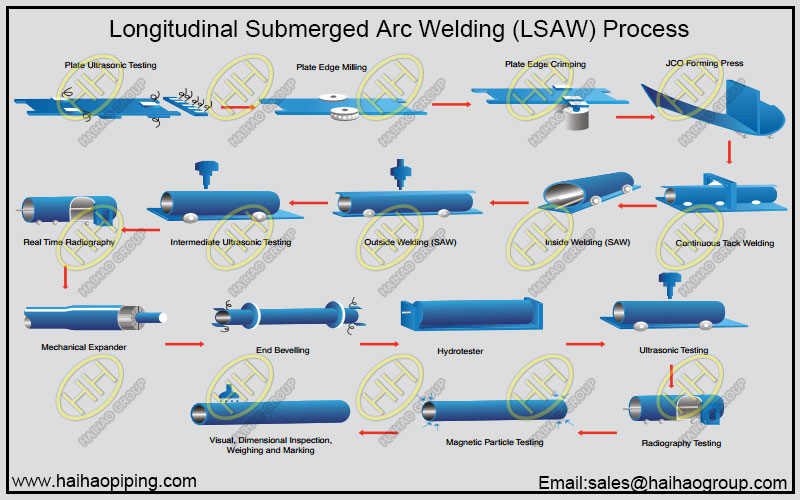
Credit: www.haihaopiping.com
Frequently Asked Questions
What Are The Main Types Of Pipe Welding?
The main types of pipe welding are MIG, TIG, Stick, and Flux-Cored. Each method has unique advantages. MIG welding is versatile, TIG welding offers precision, Stick welding is good for outdoor work, and Flux-Cored is efficient for thick materials.
Which Pipe Welding Method Is Best For Beginners?
MIG welding is best for beginners. It is easy to learn and versatile. The process is straightforward, making it ideal for those new to welding. MIG welding also works on various materials, providing a good starting point for novices.
What Is The Difference Between Mig And Tig Welding?
MIG welding uses a continuous wire feed for welding. TIG welding uses a non-consumable tungsten electrode. MIG is faster and easier for beginners, while TIG offers more precision and control. Each method suits different types of projects and materials.
Is Stick Welding Suitable For All Environments?
Yes, Stick welding is suitable for all environments. It is highly versatile and works well outdoors. It can handle adverse conditions like wind and rain, making it ideal for construction sites and repairs. Stick welding is robust and reliable.
Conclusion
Mastering different types of pipe welding can enhance your skills and career opportunities. Each method has unique benefits and applications. Understanding these techniques is essential for safe and efficient welding. Stay updated with industry trends to remain competitive. Invest in quality tools and training for the best results.